What is Through Hole PCB Assembly?
Through Hole (TH) PCB Assembly is a method of assembling electronic components onto a printed circuit board (PCB) by inserting the component leads through drilled holes in the board and soldering them onto the opposite side. This is one of the oldest and most reliable methods of PCB assembly, and it is still widely used today, especially for larger components or in applications where mechanical strength is crucial.
Advantages of Through Hole PCB Assembly
-
Mechanical Strength: TH components are physically mounted onto the PCB, providing a stronger mechanical bond compared to surface mount technology (SMT). This makes TH PCBA ideal for applications that require high durability or are subject to mechanical stress.
-
Ease of Repair: Since TH components are mounted through the board, they are easier to replace or repair manually compared to SMT components.
-
Compatibility with Larger Components: Some larger components, such as transformers, connectors, and high-power resistors, are only available in TH packages.
-
Lower Setup Costs: TH PCBA requires less sophisticated equipment compared to SMT, which can result in lower initial setup costs.
Disadvantages of Through Hole PCB Assembly
-
Lower Component Density: TH components occupy more space on the PCB compared to SMT components, limiting the potential for miniaturization.
-
Slower Assembly Process: Inserting and soldering TH components is a slower process compared to SMT, which can place components on both sides of the board simultaneously.
-
Higher Labor Costs: Due to the manual nature of TH PCBA, labor costs can be higher compared to automated SMT assembly.
-
Limited Design Flexibility: The need for drilled holes in the PCB can limit the routing options and overall design flexibility.
Through Hole PCB Assembly Process
The TH PCBA process involves several steps, which are outlined below:
1. PCB Design and Fabrication
The first step in the TH PCBA process is to design the PCB layout using electronic design automation (EDA) software. The design must include the appropriate hole sizes and locations for the TH components. Once the design is complete, the PCB is fabricated with the necessary holes and conductive traces.
2. Component Preparation
Before the assembly process begins, the TH components must be prepared. This involves forming the component leads, if necessary, to ensure they fit properly through the holes in the PCB. Some components may also require pre-soldering or tinning of the leads to facilitate the soldering process.
3. Component Insertion
The prepared TH components are manually inserted into the corresponding holes on the PCB. This process can be aided by using a component insertion machine for high-volume production. The component leads are pushed through the holes until the component body sits flush against the PCB surface.
4. Soldering
After all the components are inserted, the PCB is flipped over, and the protruding leads are soldered to the conductive traces on the opposite side of the board. This is typically done using a wave soldering machine, which applies molten solder to the board as it passes over a wave of solder. For smaller batches or prototypes, hand soldering may be used.
5. Inspection and Testing
Once the soldering process is complete, the assembled PCB undergoes visual inspection to ensure that all components are properly mounted and soldered. Automated optical inspection (AOI) systems may be used for high-volume production. The PCB is then tested for functionality using various methods, such as in-circuit testing (ICT) or functional testing.
6. Cleaning and Finishing
After inspection and testing, the assembled PCB is cleaned to remove any flux residue or contaminants from the soldering process. This can be done using various cleaning agents, such as deionized water, isopropyl alcohol, or specialized cleaning solutions. Finally, any necessary finishing touches, such as applying conformal coating or potting, are completed.
Techniques and Equipment Used in TH PCBA
Several techniques and pieces of equipment are used in the TH PCBA process to ensure high-quality and efficient assembly.
Component Forming
Component forming is the process of shaping the leads of TH components to ensure they fit properly through the holes in the PCB. This can be done manually using pliers or automatically using a component forming machine. Component forming ensures that the components sit flush against the PCB surface and helps prevent issues during the soldering process.
Wave Soldering
Wave soldering is the most common method for soldering TH components onto a PCB. In this process, the PCB is passed over a wave of molten solder, which flows up through the holes and around the component leads, creating a strong electrical and mechanical connection. Wave soldering machines can be configured with various settings, such as solder temperature, conveyor speed, and preheat temperature, to optimize the soldering process for different PCB designs and components.
Selective Soldering
Selective soldering is a more targeted approach to soldering TH components, where only specific areas of the PCB are exposed to molten solder. This method is useful for PCBs with a mix of TH and SMT components, or for components that are sensitive to high temperatures. Selective soldering can be performed using a variety of tools, such as soldering irons, solder fountains, or laser soldering systems.
Automated Optical Inspection (AOI)
AOI systems are used to quickly and accurately inspect assembled PCBs for defects, such as missing components, incorrect component placement, or poor solder joints. These systems use high-resolution cameras and advanced image processing algorithms to compare the assembled PCB to the original design files. AOI can significantly reduce the time and labor required for manual inspection, while improving the overall quality of the finished product.
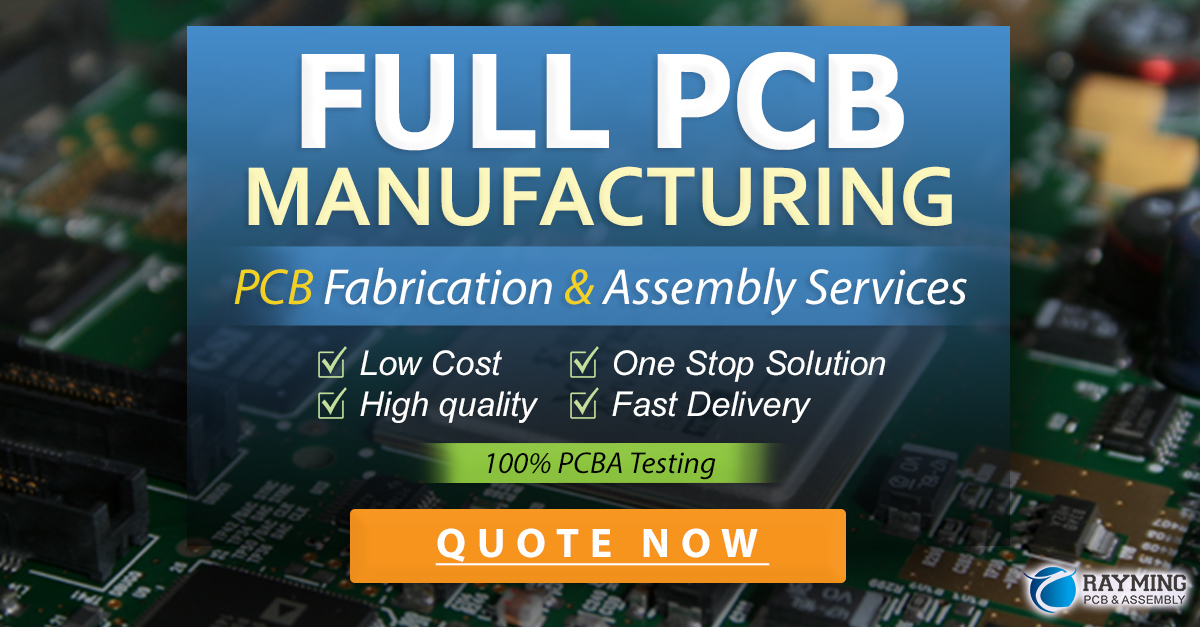
Best Practices for TH PCBA
To ensure high-quality and reliable TH PCB assemblies, several best practices should be followed:
-
Design for Manufacturability (DFM): When designing the PCB layout, consider the limitations and requirements of the TH PCBA process. This includes ensuring adequate hole sizes, proper component spacing, and accessible solder points.
-
Use Appropriate Components: Select TH components that are compatible with the PCB design and the intended application. Consider factors such as power rating, temperature tolerance, and lead pitch when choosing components.
-
Maintain Proper Process Control: Monitor and control the various parameters of the TH PCBA process, such as solder temperature, preheat temperature, and conveyor speed, to ensure consistent and high-quality results.
-
Implement Quality Assurance Measures: Utilize inspection and testing techniques, such as AOI and ICT, to identify and correct defects early in the assembly process. Establish quality control checkpoints throughout the process to maintain a high level of quality.
-
Provide Adequate Training: Ensure that all personnel involved in the TH PCBA process are properly trained on the equipment, techniques, and best practices used in the assembly process. Regular training and skill updates can help maintain a high level of quality and efficiency.
Frequently Asked Questions (FAQ)
1. What is the difference between Through Hole and Surface Mount PCB Assembly?
Through Hole (TH) PCB Assembly involves inserting component leads through drilled holes in the PCB and soldering them onto the opposite side, while Surface Mount (SMT) PCB Assembly involves placing components directly onto the surface of the PCB and soldering them in place. TH PCBA is generally stronger and easier to repair, while SMT PCBA allows for higher component density and faster assembly.
2. Can Through Hole and Surface Mount components be used on the same PCB?
Yes, it is possible to use both Through Hole and Surface Mount components on the same PCB. This is known as a mixed-technology or hybrid assembly. However, the assembly process becomes more complex, as it requires a combination of TH and SMT assembly techniques.
3. Are there any specific design considerations for Through Hole PCB Assembly?
When designing a PCB for Through Hole Assembly, it is important to consider factors such as hole sizes, component spacing, and lead pitch. Proper Design for Manufacturability (DFM) practices should be followed to ensure compatibility with the TH PCBA process and to facilitate efficient assembly.
4. What are some common defects encountered in Through Hole PCB Assembly?
Common defects in TH PCBA include poor solder joints (cold joints, insufficient solder, bridging), misaligned or missing components, and damaged components or PCBs. These defects can be caused by various factors, such as improper process control, inadequate cleaning, or human error.
5. How can the quality of Through Hole PCB assemblies be ensured?
To ensure the quality of TH PCB assemblies, several best practices should be followed, including:
- Implementing proper Design for Manufacturability (DFM) practices
- Using appropriate components and materials
- Maintaining proper process control and monitoring
- Utilizing inspection and testing techniques, such as Automated Optical Inspection (AOI) and In-Circuit Testing (ICT)
- Providing adequate training for all personnel involved in the assembly process
By adhering to these best practices and maintaining a focus on quality throughout the TH PCBA process, manufacturers can consistently produce high-quality and reliable PCB assemblies.
Conclusion
Through Hole PCB Assembly remains an essential method for producing reliable and robust electronic assemblies, despite the growing popularity of Surface Mount Technology. By understanding the advantages, disadvantages, and best practices associated with TH PCBA, manufacturers can make informed decisions about when and how to utilize this assembly method.
As the electronics industry continues to evolve, it is likely that Through Hole PCB Assembly will continue to play a significant role, particularly in applications that require strong mechanical connections or the use of larger components. By staying up-to-date with the latest techniques, equipment, and best practices, manufacturers can ensure that they are well-positioned to meet the changing demands of the industry and deliver high-quality TH PCB assemblies to their customers.
Leave a Reply