Introduction to IPC PCB Standards
Printed Circuit Boards (PCBs) are the backbone of modern electronics. They are used in almost every electronic device we use today, from smartphones and laptops to medical equipment and aerospace systems. To ensure the reliability, quality, and consistency of these PCBs, the electronics industry relies on a set of standards known as IPC PCB standards.
IPC, formerly known as the Institute for Printed Circuits, is a global trade association that develops and publishes standards for the electronics industry. These standards cover various aspects of PCB design, fabrication, assembly, and testing. In this article, we will explore the importance of IPC PCB standards and why they are essential for the electronics industry.
The Need for IPC PCB Standards
Ensuring Consistency and Reliability
One of the primary reasons for the development of IPC PCB standards is to ensure consistency and reliability in PCB manufacturing. With the increasing complexity of electronic devices and the growing demand for high-quality PCBs, it is essential to have a set of guidelines that manufacturers can follow to produce consistent and reliable products.
IPC PCB standards provide a common language and a set of best practices for PCB designers, fabricators, and assemblers. By adhering to these standards, manufacturers can ensure that their PCBs meet the required specifications and perform as expected. This consistency and reliability are crucial for the proper functioning of electronic devices and systems.
Facilitating Communication and Collaboration
Another important aspect of IPC PCB standards is that they facilitate communication and collaboration among various stakeholders in the electronics industry. PCB designers, fabricators, assemblers, and end-users all have different requirements and expectations when it comes to PCBs. IPC standards provide a common framework that allows these stakeholders to communicate effectively and work together seamlessly.
For example, when a PCB designer creates a layout based on IPC standards, the fabricator can easily understand the design intent and manufacture the board accordingly. Similarly, when an assembler receives a PCB that adheres to IPC standards, they can be confident that the board will be compatible with their assembly processes. This streamlined communication and collaboration help to reduce errors, minimize delays, and improve the overall efficiency of the PCB manufacturing process.
Promoting Quality and Reliability
IPC PCB standards also play a crucial role in promoting quality and reliability in the electronics industry. These standards define a set of requirements and guidelines for various aspects of PCB manufacturing, such as material selection, design rules, fabrication processes, and testing methods. By following these standards, manufacturers can ensure that their PCBs meet the highest quality standards and are reliable enough to withstand the rigors of real-world applications.
For example, IPC-6012, the standard for the qualification and performance of rigid printed boards, specifies the requirements for board materials, conductor thickness, hole sizes, and other critical parameters. By adhering to these requirements, manufacturers can produce PCBs that are mechanically and electrically robust, with minimal defects and a long service life.
Enabling Interoperability and Compatibility
Interoperability and compatibility are essential in today’s interconnected world, where electronic devices and systems from different manufacturers need to work together seamlessly. IPC PCB standards help to ensure that PCBs from different sources can be integrated and used together without compatibility issues.
For instance, IPC-2221, the standard for the generic requirements for printed board design, defines a set of design rules and guidelines that ensure the compatibility of PCBs with various manufacturing processes and assembly techniques. By following these guidelines, PCB designers can create layouts that are compatible with a wide range of fabrication and assembly equipment, making it easier to source components and integrate PCBs from different manufacturers.
Reducing Costs and Improving Efficiency
Adhering to IPC PCB standards can also help to reduce costs and improve efficiency in the electronics industry. By providing a common set of guidelines and best practices, these standards help to minimize errors, rework, and scrap, which can be costly and time-consuming.
For example, IPC-A-600, the standard for the acceptability of printed boards, defines a set of visual and dimensional criteria for inspecting and accepting PCBs. By using these criteria, manufacturers can quickly and accurately identify defects and anomalies, reducing the need for expensive and time-consuming rework or scrap.
Moreover, by promoting consistency and reliability in PCB manufacturing, IPC standards help to reduce the overall cost of ownership for electronic devices and systems. When PCBs are manufactured to a high standard, they are less likely to fail or require maintenance, resulting in lower lifecycle costs for end-users.
Key IPC PCB Standards
There are numerous IPC PCB standards covering various aspects of PCB design, fabrication, assembly, and testing. Some of the most important standards include:
Standard | Description |
---|---|
IPC-2221 | Generic Standard on Printed Board Design |
IPC-2222 | Sectional Design Standard for Rigid Organic Printed Boards |
IPC-2223 | Sectional Design Standard for Flexible Printed Boards |
IPC-2226 | Sectional Design Standard for High Density Interconnect (HDI) Printed Boards |
IPC-6011 | Generic Performance Specification for Printed Boards |
IPC-6012 | Qualification and Performance Specification for Rigid Printed Boards |
IPC-6013 | Qualification and Performance Specification for Flexible Printed Boards |
IPC-6018 | Qualification and Performance Specification for High Frequency (Microwave) Printed Boards |
IPC-A-600 | Acceptability of Printed Boards |
IPC-A-610 | Acceptability of Electronic Assemblies |
IPC-J-STD-001 | Requirements for Soldered Electrical and Electronic Assemblies |
IPC-7711/7721 | Rework, Modification and Repair of Electronic Assemblies |
These standards cover a wide range of topics, from design rules and material requirements to acceptance criteria and rework procedures. By familiarizing themselves with these standards and incorporating them into their workflows, PCB designers, fabricators, and assemblers can ensure that their products meet the highest quality and reliability standards.
The Role of IPC in Developing and Maintaining Standards
IPC plays a crucial role in developing and maintaining PCB standards for the electronics industry. The organization brings together experts from various fields, including PCB design, fabrication, assembly, and testing, to collaborate on the development of new standards and the revision of existing ones.
The standards development process at IPC is a collaborative effort that involves the participation of industry professionals from around the world. Technical committees, consisting of volunteers from member companies, work together to draft, review, and approve new standards and revisions. This process ensures that the standards reflect the latest technological advancements and best practices in the industry.
IPC also provides training and certification programs to help industry professionals stay up-to-date with the latest standards and best practices. These programs cover various aspects of PCB manufacturing, from design and fabrication to assembly and testing. By participating in these programs, professionals can enhance their skills, knowledge, and credibility, and contribute to the overall quality and reliability of PCBs in the industry.
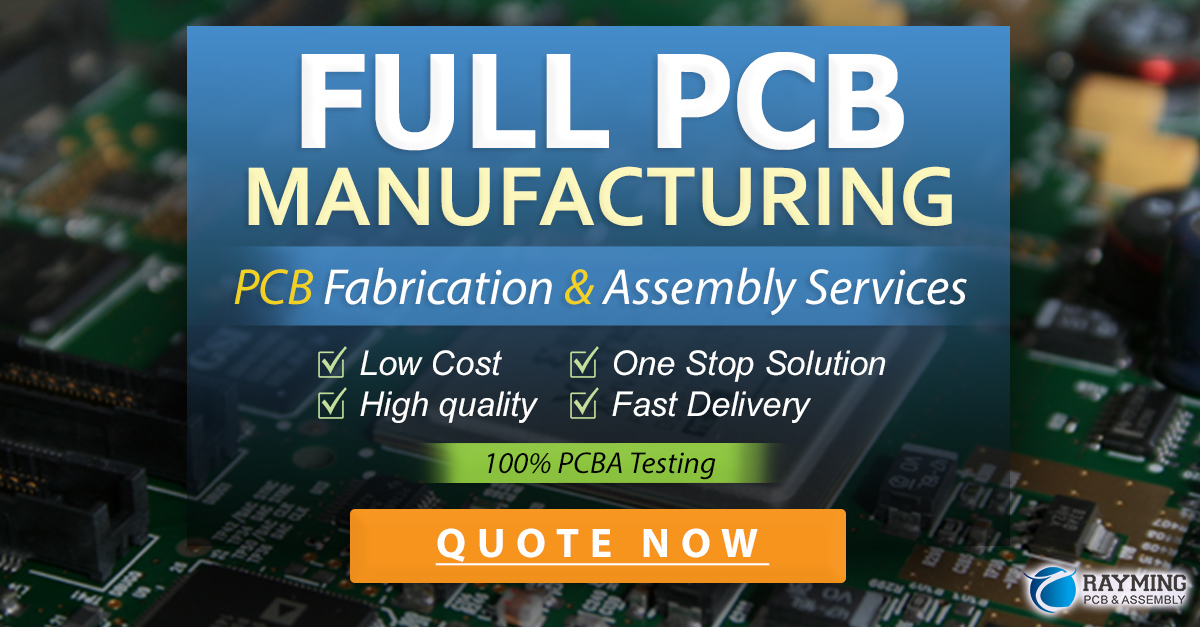
The Future of IPC PCB Standards
As technology continues to advance and the electronics industry evolves, IPC PCB standards will play an increasingly important role in ensuring the quality, reliability, and consistency of PCBs. The organization is continuously working on developing new standards and updating existing ones to keep pace with the latest technological advancements and industry trends.
One of the key areas of focus for IPC in the coming years is the development of standards for emerging technologies, such as 5G, the Internet of Things (IoT), and artificial intelligence (AI). These technologies require high-performance, high-density, and high-reliability PCBs that can operate in challenging environments. IPC is working closely with industry partners to develop standards that address the unique requirements of these technologies and ensure the successful deployment of next-generation electronic devices and systems.
Another area of focus for IPC is the promotion of sustainable and environmentally friendly practices in the electronics industry. The organization is developing standards and guidelines for the use of eco-friendly materials, the reduction of waste and emissions, and the responsible disposal of electronic waste. By adopting these standards, manufacturers can not only reduce their environmental footprint but also comply with increasingly stringent regulations and meet the growing demand for sustainable products.
Frequently Asked Questions (FAQ)
-
Q: What is the difference between IPC and other standards organizations?
A: IPC is a global trade association that focuses specifically on the electronics industry, while other standards organizations, such as ISO and ANSI, cover a wider range of industries. IPC standards are developed by industry experts and are tailored to the specific needs of the electronics industry. -
Q: Are IPC PCB standards mandatory?
A: While IPC PCB standards are not mandatory by law, they are widely adopted and recognized by the electronics industry worldwide. Many companies require their suppliers to adhere to IPC standards to ensure the quality and reliability of their products. -
Q: How often are IPC PCB standards updated?
A: IPC PCB standards are regularly reviewed and updated to keep pace with the latest technological advancements and industry trends. The frequency of updates varies depending on the standard and the pace of change in the industry, but most standards are reviewed and revised every few years. -
Q: How can I access IPC PCB standards?
A: IPC PCB standards are available for purchase on the IPC website (www.ipc.org). Some standards may also be available through other distributors or as part of a subscription service. IPC members have access to discounted prices and additional resources. -
Q: What are the benefits of getting IPC certified?
A: Getting IPC certified demonstrates your expertise and commitment to quality in the electronics industry. It can enhance your credibility, improve your job prospects, and help you stay up-to-date with the latest standards and best practices. IPC certification is recognized and valued by employers worldwide.
Conclusion
IPC PCB standards are essential for ensuring the quality, reliability, and consistency of printed circuit boards in the electronics industry. These standards provide a common language and a set of best practices for PCB designers, fabricators, and assemblers, facilitating communication and collaboration among various stakeholders. By adhering to IPC standards, manufacturers can reduce costs, improve efficiency, and promote the overall success of the electronics industry.
As technology continues to evolve, IPC will play an increasingly important role in developing and maintaining standards that address the unique requirements of emerging technologies and promote sustainable practices. By staying up-to-date with the latest IPC PCB standards and best practices, industry professionals can contribute to the advancement of the electronics industry and the development of innovative, high-quality products that meet the needs of a rapidly changing world.
Leave a Reply