What is IoT in Electronics Manufacturing?
IoT in electronics manufacturing refers to the integration of connected devices, sensors, and software into production processes. This allows for real-time monitoring, data collection, analysis, and optimization of manufacturing operations. IoT systems can track assets, monitor equipment health, control processes, and enable predictive maintenance.
Key components of IoT in electronics manufacturing include:
- Connected devices and sensors
- Industrial IoT platforms
- Cloud computing and data analytics
- Automation and robotics
- Artificial intelligence and machine learning
By leveraging these technologies, manufacturers can create smart factories that are more agile, efficient, and responsive to changing market demands.
Benefits of IoT in Electronics Manufacturing
IoT offers numerous benefits for electronics manufacturers, including:
-
Improved efficiency and productivity – IoT enables real-time monitoring and optimization of processes, reducing waste, downtime, and costs. Automation and robotics can further enhance productivity.
-
Enhanced quality control – Connected sensors and AI-powered visual inspection systems can detect defects and quality issues in real-time, reducing scrap and rework.
-
Predictive maintenance – By monitoring equipment health and performance data, IoT systems can predict when maintenance is needed, preventing unplanned downtime and extending asset lifespans.
-
Increased flexibility and agility – IoT enables manufacturers to quickly reconfigure production lines and processes to accommodate new products or changes in demand.
-
Better decision making – Real-time data collection and analytics provide valuable insights for optimizing operations, identifying bottlenecks, and making data-driven decisions.
-
Enhanced supply chain visibility – IoT can track inventory, shipments, and supplier performance in real-time, improving supply chain efficiency and responsiveness.
The table below summarizes some key benefits of IoT in electronics manufacturing:
Benefit | Description |
---|---|
Efficiency | Optimize processes, reduce waste and downtime |
Quality | Real-time defect detection and prevention |
Maintenance | Predictive maintenance to avoid unplanned downtime |
Flexibility | Quickly adapt to changes in products or demand |
Decision Making | Data-driven insights for continuous improvement |
Supply Chain Visibility | Real-time tracking of inventory, shipments, and suppliers |
IoT Manufacturing Use Cases and Applications
IoT is being applied across various aspects of electronics manufacturing, from production to logistics. Some common use cases include:
Smart Factory Automation
IoT enables the automation of production processes through connected equipment, robots, and control systems. This allows for:
- Lights-out manufacturing with minimal human intervention
- Flexible, reconfigurable production lines
- Real-time production scheduling and optimization
- Integration with enterprise systems like ERP and MES
Predictive Maintenance
By analyzing sensor data from equipment, IoT systems can:
- Monitor equipment health and performance in real-time
- Detect anomalies and potential issues early
- Predict when maintenance will be needed
- Automatically trigger maintenance work orders
- Optimize maintenance schedules based on risk and criticality
This helps reduce unplanned downtime, extend equipment lifespans, and lower maintenance costs.
Quality Inspection
IoT and computer vision enable automated quality inspection at various stages of production:
- Vision systems with AI can detect surface defects and dimensional issues
- Connected in-line testers check electrical characteristics of components
- Analytics detect quality trends and correlate them to process parameters
- Real-time SPC identifies deviations and quality issues
By catching quality problems early, scrap and rework are minimized.
Inventory and Supply Chain Management
IoT can enhance inventory visibility and supply chain efficiency:
- RFID and other tracking technologies monitor inventory in real-time
- Connected containers and shipments provide end-to-end traceability
- Analytics predict demand and optimize inventory levels
- Supplier performance and risks are monitored
Some example applications in this area:
Application | Description |
---|---|
Smart shelves | Sensors track inventory and trigger replenishment |
Connected shipments | Real-time location, condition monitoring of goods |
Demand forecasting | Predictive analytics optimize inventory |
Supplier monitoring | IoT data tracks supplier quality and risks |
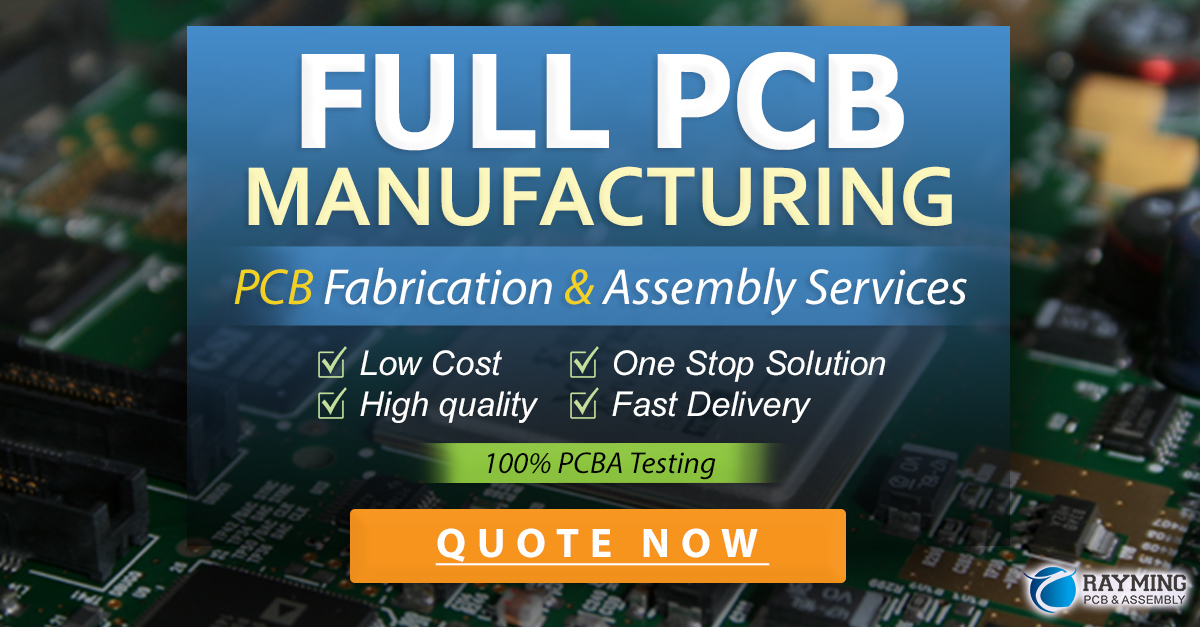
Challenges and Considerations for IoT in Electronics Manufacturing
While IoT offers significant benefits, there are also challenges manufacturers must address:
Security and Privacy
With more connected devices and data, cybersecurity risks increase. Manufacturers need robust strategies to:
- Secure devices, networks, and data
- Protect sensitive IP and customer information
- Ensure compliance with data privacy regulations
- Manage user access and authentication
- Detect and respond to security incidents
Integration and Interoperability
Integrating IoT into existing manufacturing systems can be complex. Key considerations include:
- Enabling communication between diverse devices and protocols
- Integrating IoT data with enterprise systems like ERP, MES, PLM
- Managing data storage, processing, and analytics
- Ensuring scalability and performance of IoT platforms
Skills and Talent
Implementing IoT requires new skills in areas like:
- IoT architecture and engineering
- Data science and analytics
- Cybersecurity
- Automation and robotics
Manufacturers need to reskill existing workers and attract new IoT talent.
ROI and Business Case
Justifying IoT investments requires a clear business case and ROI. Factors to consider:
- Upfront costs of sensors, networks, software
- Ongoing costs for data storage, processing, maintenance
- Expected benefits and efficiency gains
- Timeframes for realizing ROI
- Risks and uncertainties
Developing a phased approach and proof-of-concept can help manage costs and risks.
Future of IoT in Electronics Manufacturing
IoT will continue to transform electronics manufacturing in the coming years. Key trends to watch include:
-
Convergence with other technologies – IoT will increasingly integrate with AI, blockchain, edge computing, and 5G to enable new capabilities.
-
Growth of the Industrial IoT (IIoT) market – The IIoT market is projected to reach $263.4 billion by 2027, driven by the proliferation of connected devices and the need for industrial automation. (Source: Fortune Business Insights)
-
Emergence of new business models – IoT will enable servitization, where manufacturers offer products as services with predictive maintenance, performance-based contracts, and recurring revenue models.
-
Increased focus on sustainability – IoT will be used to monitor and optimize energy usage, reduce waste, and enable circular economy practices in manufacturing.
-
Evolution of IoT standards and platforms – Expect continued development of IoT standards and platforms to improve interoperability, security, and scalability.
As these trends unfold, electronics manufacturers who strategically adopt and scale IoT will be well-positioned for success in the Industry 4.0 era.
Frequently Asked Questions
What is the difference between IoT and IIoT?
IoT refers to the general concept of connected devices, while IIoT specifically focuses on industrial applications of IoT, such as in manufacturing, energy, and transportation. IIoT emphasizes ruggedness, reliability, and security for mission-critical operations.
How does IoT enable predictive maintenance?
IoT sensors can continually monitor the health and performance of manufacturing equipment, collecting data on vibration, temperature, runtime, and other parameters. Advanced analytics and AI models then predict when failures are likely to occur, allowing maintenance to be scheduled proactively to avoid unplanned downtime.
What are some key challenges in implementing IoT in electronics manufacturing?
Some of the main challenges include cybersecurity risks, complexity of integrating IoT with legacy systems, lack of standardization, and the need for new skills and talent. Manufacturers need to carefully plan their IoT strategies and investments to manage these challenges.
How can electronics manufacturers get started with IoT?
A phased approach is often recommended, starting with a specific use case and proof-of-concept. This allows manufacturers to validate the technology, refine their processes, and build internal capabilities before scaling up. Partnering with experienced IoT providers and learning from industry peers can also help accelerate adoption.
What is the future outlook for IoT in electronics manufacturing?
The future of IoT in electronics manufacturing is very promising. As the cost of sensors and connectivity continues to decrease, and as IoT platforms and analytics capabilities advance, more and more manufacturers will adopt IoT to drive innovation and competitiveness. IoT is poised to be a key enabler of the Industry 4.0 transformation in electronics manufacturing.
Leave a Reply