What is PCB Soldering?
PCB soldering is the process of joining electronic components to a printed circuit board using a melted metal alloy called solder. The solder creates an electrical and mechanical connection between the component leads and the copper pads on the PCB. This allows electrical current to flow through the circuit and enables the components to function as intended.
Types of Soldering
There are two main types of soldering used in PCB assembly:
-
Through-hole soldering: This method involves inserting component leads through holes drilled in the PCB and soldering them to pads on the opposite side of the board.
-
Surface-mount soldering: In this method, components are placed directly onto pads on the surface of the PCB and soldered in place. Surface-mount components are smaller and allow for denser circuit layouts compared to through-hole components.
Soldering Equipment and Materials
To get started with PCB soldering, you’ll need the following equipment and materials:
Soldering Iron
A soldering iron is the most essential tool for PCB soldering. It consists of a heated metal tip that melts the solder and allows it to flow onto the joint. When choosing a soldering iron, consider the following factors:
- Wattage: A higher wattage iron heats up faster and maintains its temperature better, but may be overkill for small components. A 30-50 watt iron is suitable for most PCB soldering tasks.
- Temperature control: Some soldering irons have adjustable temperature controls, which can be useful for working with different types of solder and components.
- Tip size and shape: Different tip sizes and shapes are available for various soldering tasks. A conical or chisel tip is suitable for most general-purpose soldering.
Solder
Solder is a metal alloy that melts at a relatively low temperature and is used to create the electrical and mechanical connection between components and the PCB. The most common types of solder used in electronics are:
- Lead-based solder: Traditionally, solder was made from a mixture of tin and lead. However, due to health and environmental concerns, lead-based solder is being phased out in favor of lead-free alternatives.
- Lead-free solder: Lead-free solder is typically made from a mixture of tin, silver, and copper. It has a slightly higher melting point than lead-based solder and may require different soldering techniques.
Solder is available in various diameters and forms, such as wire, paste, and preforms. For most hand soldering tasks, a solder wire with a diameter of 0.5-0.8mm is suitable.
Flux
Flux is a chemical compound that helps to remove oxides and impurities from the surfaces being soldered, promoting better solder flow and adhesion. There are two main types of flux:
- Rosin flux: This is the most common type of flux used in electronics soldering. It is available in various activity levels, from mild to activated. Rosin flux leaves a residue that may need to be cleaned after soldering.
- Water-soluble flux: This type of flux is easier to clean than rosin flux but may require more frequent cleaning during the soldering process to prevent corrosion.
Many solder wires come with a flux core, which eliminates the need for a separate flux application.
Other Tools and Accessories
In addition to the soldering iron, solder, and flux, you may find the following tools and accessories helpful for PCB soldering:
- Soldering iron stand: A stand provides a safe place to rest your hot soldering iron when not in use.
- Sponge or brass wool: Used for cleaning the soldering iron tip.
- Tweezers: Useful for holding small components in place during soldering.
- Solder wick: A braided copper wire used for removing excess solder from joints.
- Magnifying glass or microscope: Helps with inspecting small components and solder joints.
- Fume extractor: Removes harmful fumes produced during soldering.
PCB Soldering Techniques
Now that you have your equipment and materials, let’s discuss some basic PCB soldering techniques.
Tinning the Soldering Iron Tip
Before you start soldering, it’s essential to tin the tip of your soldering iron. Tinning helps to protect the tip from oxidation and promotes better heat transfer. To tin the tip:
- Heat up the soldering iron to the appropriate temperature for your solder.
- Clean the tip with a damp sponge or brass wool.
- Apply a small amount of solder to the tip and let it melt, coating the entire tip.
- Wipe off any excess solder on the sponge or brass wool.
Through-Hole Soldering
To solder a through-hole component:
- Insert the component leads through the appropriate holes in the PCB.
- Bend the leads slightly outward to hold the component in place.
- Heat the component lead and the pad simultaneously with the soldering iron.
- Apply solder to the joint, allowing it to melt and flow around the lead and pad.
- Remove the solder and then the iron, holding the component in place until the solder cools and hardens.
- Trim the excess component lead with wire cutters.
Surface-Mount Soldering
Surface-mount soldering can be more challenging than through-hole soldering due to the smaller size of the components and pads. There are two main methods for surface-mount soldering:
-
Solder paste and reflow: In this method, solder paste (a mixture of solder particles and flux) is applied to the pads using a stencil or syringe. The components are then placed onto the pads, and the entire assembly is heated in a reflow oven or with a hot air gun until the solder melts and forms a joint.
-
Hand soldering with an iron: For hand soldering surface-mount components, follow these steps:
a. Apply a small amount of solder to one of the component pads.
b. Position the component on the pads using tweezers, aligning it with the solder.
c. While holding the component in place, heat the solder joint with the iron until the solder melts and the component settles into place.
d. Solder the remaining leads by applying heat and solder as needed.
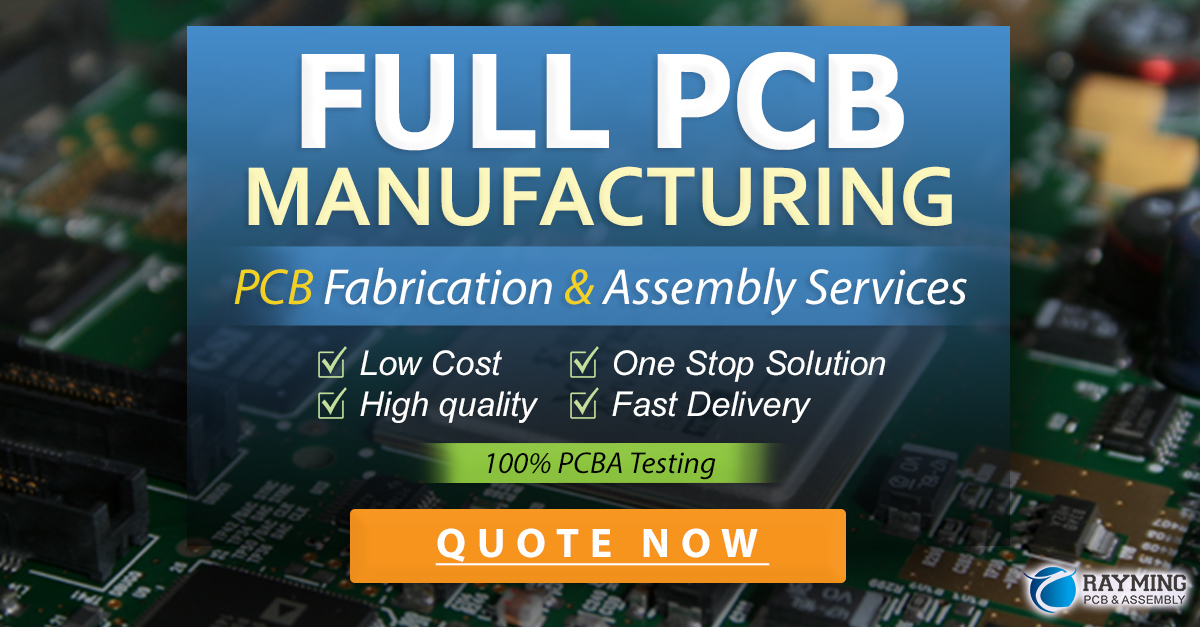
Soldering Tips and Best Practices
To achieve reliable and high-quality solder joints, follow these tips and best practices:
- Keep the soldering iron tip clean and well-tinned.
- Use the appropriate temperature for your solder and components.
- Apply heat to both the component lead and the pad simultaneously.
- Use just enough solder to create a strong joint, avoiding excess.
- Allow the solder to cool and harden before moving the component or PCB.
- Inspect your solder joints for quality and consistency.
- Practice proper safety precautions, such as using a fume extractor and avoiding touching hot surfaces.
Common Soldering Problems and Solutions
Even with proper technique, you may encounter some common soldering problems. Here are a few issues and their solutions:
Problem | Cause | Solution |
---|---|---|
Cold joint | Insufficient heat or poor surface preparation | Reheat the joint and apply fresh solder |
Bridging | Excess solder or insufficient space between pads | Remove excess solder with solder wick |
Solder not sticking | Dirty or oxidized surfaces | Clean surfaces with flux or solder wick |
Overheated joint | Excessive heat or prolonged contact | Use appropriate temperature and minimize contact time |
PCB Soldering Safety
Soldering involves high temperatures and potentially harmful fumes, so it’s essential to follow proper safety practices:
- Work in a well-ventilated area or use a fume extractor.
- Wear safety glasses to protect your eyes from solder splashes.
- Use a heat-resistant surface or soldering mat to protect your work area.
- Never touch the hot soldering iron tip or freshly soldered joints.
- Keep flammable materials away from your soldering station.
- Wash your hands after soldering, especially if using lead-based solder.
Advanced PCB Soldering Techniques
Once you’ve mastered the basics of PCB soldering, you may want to explore some advanced techniques:
- Drag soldering: A method for quickly soldering multiple surface-mount components by dragging the iron and solder across the pads.
- Hot air rework: Using a hot air gun to remove and replace surface-mount components without damaging the PCB.
- Solder paste stenciling: Applying solder paste to PCB pads using a laser-cut stencil for more precise and consistent surface-mount soldering.
Frequently Asked Questions (FAQ)
-
What is the best solder for PCB soldering?
The best solder for PCB soldering depends on your specific requirements and the components you are working with. For most applications, a lead-free solder with a composition of Sn96.5Ag3.0Cu0.5 (SAC305) is a good choice. It has a melting point of around 217°C and provides good wetting and joint strength. -
How do I choose the right soldering iron tip for my project?
When choosing a soldering iron tip, consider the size and type of components you’ll be soldering. For general-purpose PCB soldering, a conical or chisel tip with a diameter of 0.8-1.6mm is suitable. For smaller surface-mount components, a finer tip with a diameter of 0.4-0.8mm may be necessary. -
Can I use lead-based solder for PCB soldering?
While lead-based solder is still available and used in some applications, it is being phased out due to health and environmental concerns. It is recommended to use lead-free solder for PCB soldering whenever possible. If you must use lead-based solder, take appropriate safety precautions, such as using proper ventilation and washing your hands after handling. -
How do I clean my PCB after soldering?
Cleaning your PCB after soldering helps to remove flux residue and improve the appearance and reliability of the board. For rosin-based flux, use isopropyl alcohol and a soft brush to gently scrub the board, then rinse with clean isopropyl alcohol and allow it to dry. For water-soluble flux, use distilled water and a soft brush, then rinse with clean distilled water and dry the board. -
What should I do if I accidentally bridge two pads with solder?
If you accidentally create a solder bridge between two pads, you can remove the excess solder using solder wick. Place the solder wick over the bridge and apply heat with the soldering iron. The excess solder will be drawn up into the wick, removing the bridge. If necessary, apply a small amount of fresh solder to the individual pads to ensure proper connections.
Conclusion
PCB soldering is a critical skill for anyone working with electronics. By understanding the basics of soldering equipment, materials, and techniques, you can create reliable and high-quality solder joints for your projects. Remember to prioritize safety, practice proper technique, and continuously improve your skills through experience and learning. With the knowledge gained from this guide, you’ll be well-equipped to tackle a wide range of PCB soldering tasks.
Leave a Reply