What is a Cable Harness?
A cable harness, also known as a wire harness, wiring harness, cable assembly, wiring assembly or wiring loom, is an organized set of electrical cables, wires and connectors that transmit signals or electrical power. The cables are bound together by straps, cable ties, cable lacing, sleeves, electrical tape, conduit, a weave of extruded string, or a combination thereof.
Cable harnesses provide several advantages over loose wires and cables. A properly designed cable harness increases the reliability of the interconnected wiring system compared to one made up of discrete wires. The installer has only one harness to install (as opposed to multiple wires), and each harness can be pre-formed to fit perfectly into its designated space. A cable harness reduces the risk of a short circuit and fire. This also decreases the chances of the connections coming undone or becoming damaged due to rubbing or vibration.
Components of a Cable Harness
A typical cable harness consists of several components:
-
Wires: These are the individual conductors that transmit electrical signals or power. They can be made of various materials such as copper, aluminum, or even optical fibers.
-
Connectors: These are the components that join the wires to other devices or to other harnesses. They come in various types such as plug connectors, socket connectors, terminal blocks, etc.
-
Terminals: These are the ends of the wires that are crimped or soldered to the connectors.
-
Sleeves: These are the protective coverings that go over the wires and the connectors. They can be made of various materials such as PVC, rubber, or heat-shrink tubing.
-
Cable ties: These are used to bundle the wires together and keep them organized.
Here’s a table summarizing these components:
Component | Description |
---|---|
Wires | Individual conductors that transmit electrical signals or power |
Connectors | Components that join the wires to other devices or harnesses |
Terminals | Ends of the wires that are crimped or soldered to the connectors |
Sleeves | Protective coverings that go over the wires and the connectors |
Cable ties | Used to bundle the wires together and keep them organized |
The Process of Cable Harness Assembly
The process of assembling a cable harness typically involves the following steps:
1. Design
The first step is to design the cable harness. This involves determining the number and type of wires needed, the length of each wire, the type of connectors to be used, and the overall layout of the harness. This is usually done using computer-aided design (CAD) software.
2. Cutting
Once the design is finalized, the next step is to cut the wires to the required lengths. This is usually done using automated wire cutting machines to ensure precision and consistency.
3. Stripping
After the wires are cut, the ends need to be stripped to expose the bare conductor. This is necessary for attaching the terminals or for soldering.
4. Crimping or Soldering
The exposed ends of the wires are then attached to the terminals of the connectors. This is done by either crimping or soldering. Crimping is a process where the terminal is mechanically deformed to grip the wire, while soldering involves melting a metal alloy to join the wire and the terminal.
5. Assembly
After the wires are attached to the connectors, the harness is assembled according to the design. This involves routing the wires, bundling them together with cable ties, and attaching any necessary sleeves or labels.
6. Testing
Once the harness is assembled, it needs to be tested to ensure that all the connections are secure and that the harness functions as intended. This usually involves electrical continuity tests and sometimes functional tests with the device the harness will be connected to.
Here’s a table outlining these steps:
Step | Description |
---|---|
Design | Determine the number, type, and length of wires, connectors, and layout |
Cutting | Cut the wires to the required lengths |
Stripping | Remove insulation from wire ends for terminal attachment or soldering |
Crimping/Soldering | Attach wire ends to connector terminals by crimping or soldering |
Assembly | Route wires, bundle with ties, attach sleeves or labels according to design |
Testing | Perform continuity and functional tests to ensure proper operation |
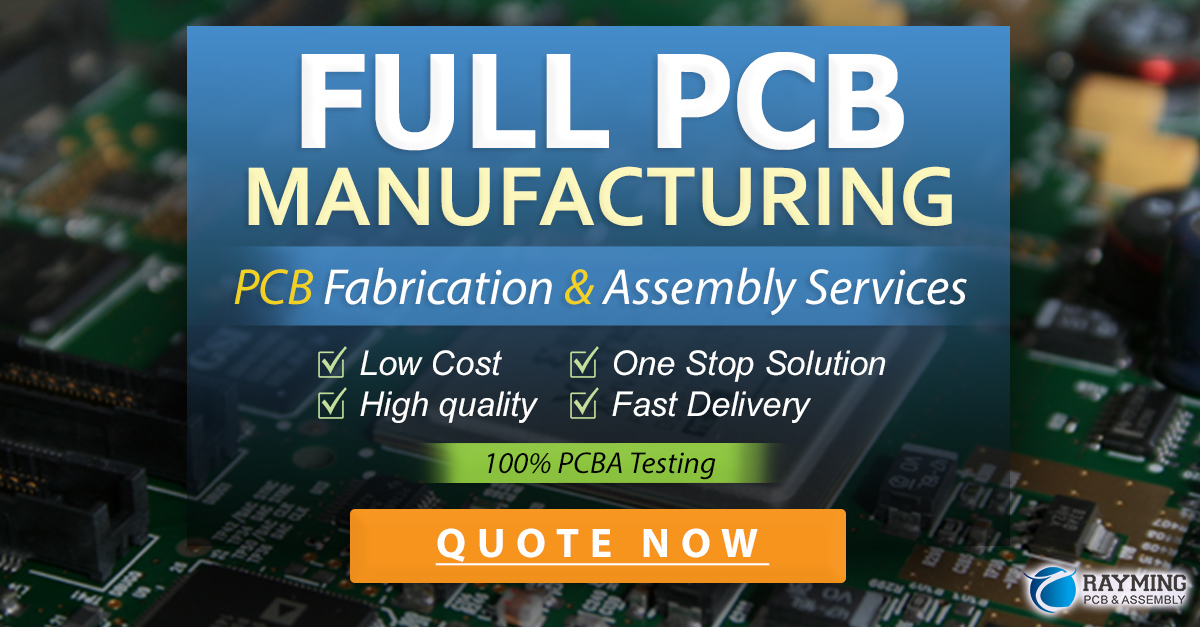
Types of Cable Harnesses
There are several types of cable harnesses, each designed for specific applications. Some common types include:
1. Electrical Wiring Harnesses
These are the most common type of harnesses. They are used to transmit electrical power and signals in various applications such as automobiles, appliances, and industrial machinery.
2. Electro-Mechanical Assemblies
These harnesses include both electrical and mechanical components. They often include items such as switches, sensors, and actuators in addition to the wires and connectors.
3. RF Cable Assemblies
These are designed to carry high-frequency radio frequency (RF) signals. They use specialized connectors and cables that are designed to minimize signal loss and interference.
4. Fiber Optic Harnesses
These use optical fibers instead of metallic wires to transmit data signals. They are used in telecommunications, computer networking, and other applications where high-speed data transmission is required.
5. Pneumatic and Hydraulic Hose Assemblies
While not strictly electrical, these assemblies are similar in concept to cable harnesses. They are used to transmit pressurized air or fluid in various industrial and automotive applications.
Advantages of Using Cable Harnesses
Using cable harnesses offers several advantages over loose wires and cables:
-
Simplicity: A single harness can replace dozens or even hundreds of individual wires. This makes installation and maintenance much simpler.
-
Reliability: Cable harnesses are pre-engineered and tested to ensure reliability. The connections are more secure and less likely to come loose due to vibration or movement.
-
Space Efficiency: Cable harnesses can be pre-formed to fit into tight spaces, making the most efficient use of the available space.
-
Cost Efficiency: While the initial design and setup costs for a cable harness can be higher, the overall installation and maintenance costs are often lower due to the simplicity and reliability.
-
Consistency: Cable harnesses ensure that every unit of a product is wired identically, reducing the risk of errors during installation.
Applications of Cable Harnesses
Cable harnesses are used in a wide variety of applications across many industries. Some common applications include:
1. Automotive
Nearly every vehicle on the road today contains multiple cable harnesses. They are used for everything from the engine control system to the entertainment system.
2. Aerospace
Aircraft and spacecraft use extensive cable harnesses to connect the various electrical and electronic systems. These harnesses must be designed to be lightweight and able to withstand the harsh conditions of flight.
3. Medical Equipment
Medical devices such as patient monitors, imaging machines, and surgical equipment rely on cable harnesses to connect the various components.
4. Industrial Machinery
Industrial machines such as CNC routers, injection molding machines, and packaging equipment use cable harnesses to connect the various sensors, actuators, and control systems.
5. Consumer Electronics
Appliances, computers, and entertainment systems all use cable harnesses to organize and simplify the internal wiring.
Cable Harness Testing
As mentioned earlier, testing is a crucial step in the cable harness assembly process. There are several types of tests that may be performed, depending on the application:
1. Continuity Test
This test checks that each wire in the harness is connected to the correct terminal and that there are no open circuits. It is typically performed with a multimeter or a dedicated continuity tester.
2. Insulation Resistance Test
This test checks the resistance of the insulation between the wires and the connectors. It helps to identify any potential short circuits or insulation damage.
3. High Potential (Hipot) Test
This test applies a high voltage between the wires and the connector shell or between different wire groups. It is used to verify the integrity of the insulation and to detect any potential leakage paths.
4. Functional Test
This test verifies that the harness functions as intended when connected to the device it is designed for. It may involve powering up the device and checking for proper operation.
Future Trends in Cable Harness Assembly
As technology advances, so does the field of cable harness assembly. Some trends to watch for include:
-
Automated Assembly: More and more of the assembly process is being automated to improve speed, consistency, and cost-efficiency.
-
Wireless Technology: While cable harnesses will always be necessary for power transmission, data transmission is increasingly going wireless. This may lead to a reduction in the complexity of some harnesses.
-
Miniaturization: As devices get smaller, so must the cable harnesses that connect them. This requires advances in materials and assembly techniques.
-
High-Speed Data: The demand for higher data speeds is driving the development of new cable and connector technologies, such as fiber optics and high-speed serial interfaces.
-
Environmental Sustainability: There is a growing focus on making cable harnesses more environmentally friendly, both in terms of the materials used and the manufacturing processes employed.
FAQ
1. What’s the difference between a cable harness and a wire harness?
There is no difference. The terms “cable harness” and “wire harness” are used interchangeably.
2. Can I make my own cable harness?
Yes, it is possible to make your own cable harness. However, it requires a significant investment in tools and materials, as well as a good understanding of electrical principles and assembly techniques. For most applications, it is more cost-effective to purchase pre-made harnesses or to have them custom-made by a professional assembly service.
3. How do I choose the right cable harness for my application?
Choosing the right cable harness involves considering factors such as the number and type of connections needed, the power and signal requirements, the physical environment the harness will be used in, and the applicable standards and regulations. It’s best to consult with a cable harness professional or manufacturer to determine the best solution for your specific application.
4. What standards apply to cable harnesses?
There are numerous standards that can apply to cable harnesses, depending on the application and industry. Some common ones include:
- IPC/WHMA-A-620, Requirements and Acceptance for Cable and Wire Harness Assemblies
- SAE J1128, Low Voltage Primary Cable
- MIL-STD-1553, Military Standard Aircraft Internal Time Division Command/Response Multiplex Data Bus
- NFPA 79, Electrical Standard for Industrial Machinery
It’s important to determine which standards apply to your specific application and to ensure that your cable harnesses are compliant.
5. How long does a cable harness last?
The lifespan of a cable harness depends on many factors, including the materials used, the assembly quality, the operating environment, and the level of use or stress. A well-designed and well-constructed harness can last for decades in a mild environment with infrequent use. However, a harness subjected to extreme temperatures, vibrations, or frequent motion may only last a few years or even less. Regular inspection and maintenance can help to extend the life of any cable harness.
Leave a Reply