Introduction to High Tg PCB Resins
Printed circuit boards (PCBs) are the backbone of modern electronics, providing the platform for mounting and interconnecting electronic components. The performance and reliability of PCBs depend heavily on the materials used in their construction, particularly the PCB resin. In recent years, advanced high glass transition temperature (Tg) PCB resins have gained popularity due to their superior thermal, mechanical, and electrical properties.
High Tg PCB resins are polymer materials that maintain their structural integrity and performance at elevated temperatures. The glass transition temperature (Tg) is the point at which the polymer transitions from a hard, glassy state to a soft, rubbery state. PCB resins with higher Tg values can withstand higher operating temperatures without deformation or degradation, making them ideal for applications that generate significant heat or are exposed to harsh environments.
Advantages of High Tg PCB Resins
- Enhanced thermal stability
- Improved mechanical strength
- Better dimensional stability
- Reduced thermal expansion
- Higher reliability and durability
Types of High Tg PCB Resins
Several types of high Tg PCB resins are available, each with its unique properties and advantages. The most common types include:
1. Epoxy Resins
Epoxy resins are the most widely used PCB resins due to their excellent electrical insulation, chemical resistance, and adhesion properties. High Tg epoxy resins, such as those based on multifunctional epoxy compounds, offer improved thermal stability and mechanical strength compared to standard epoxy resins.
Property | Standard Epoxy Resin | High Tg Epoxy Resin |
---|---|---|
Tg (°C) | 130-140 | 170-200 |
Thermal Expansion Coefficient (ppm/°C) | 60-80 | 30-50 |
Dielectric Constant (1 MHz) | 4.0-4.5 | 3.5-4.0 |
Dissipation Factor (1 MHz) | 0.02-0.03 | 0.01-0.02 |
2. Polyimide Resins
Polyimide resins are known for their exceptional thermal stability, with Tg values ranging from 250°C to 400°C. They also exhibit excellent chemical resistance, low dielectric constant, and low dissipation factor. However, polyimide resins are more expensive and challenging to process compared to epoxy resins.
Property | Polyimide Resin |
---|---|
Tg (°C) | 250-400 |
Thermal Expansion Coefficient (ppm/°C) | 20-40 |
Dielectric Constant (1 MHz) | 3.0-3.5 |
Dissipation Factor (1 MHz) | 0.002-0.008 |
3. Cyanate Ester Resins
Cyanate ester resins offer a balance between the properties of epoxy and polyimide resins. They have high Tg values (180°C to 250°C), low dielectric constant, and low dissipation factor. Cyanate ester resins also exhibit good processability and adhesion to copper.
Property | Cyanate Ester Resin |
---|---|
Tg (°C) | 180-250 |
Thermal Expansion Coefficient (ppm/°C) | 30-60 |
Dielectric Constant (1 MHz) | 3.0-3.5 |
Dissipation Factor (1 MHz) | 0.003-0.01 |
Applications of High Tg PCB Resins
High Tg PCB resins find applications in various industries where thermal stability, reliability, and high performance are critical. Some key applications include:
1. Automotive Electronics
The automotive industry has seen a significant increase in the use of electronic systems, such as advanced driver assistance systems (ADAS), infotainment systems, and powertrain control modules. These systems are often exposed to harsh environmental conditions, including high temperatures, vibrations, and moisture. High Tg PCB resins provide the necessary thermal stability and reliability to ensure the proper functioning of these critical components.
2. Aerospace and Defense
Aerospace and defense applications demand the highest level of performance and reliability from electronic systems. PCBs used in these applications must withstand extreme temperature fluctuations, high altitudes, and exposure to radiation. High Tg PCB resins, particularly polyimide and cyanate ester resins, are well-suited for these demanding environments.
3. High-Power Electronics
Power electronics, such as motor drives, power supplies, and inverters, generate significant heat during operation. PCBs used in these applications must have excellent thermal management capabilities to prevent overheating and ensure long-term reliability. High Tg PCB resins, with their improved thermal stability and reduced thermal expansion, are ideal for high-power electronic applications.
4. Telecommunications
The telecommunications industry requires PCBs that can handle high-frequency signals with minimal signal loss and distortion. High Tg PCB resins, with their low dielectric constant and low dissipation factor, are well-suited for high-speed, high-frequency applications, such as 5G networks and satellite communications.
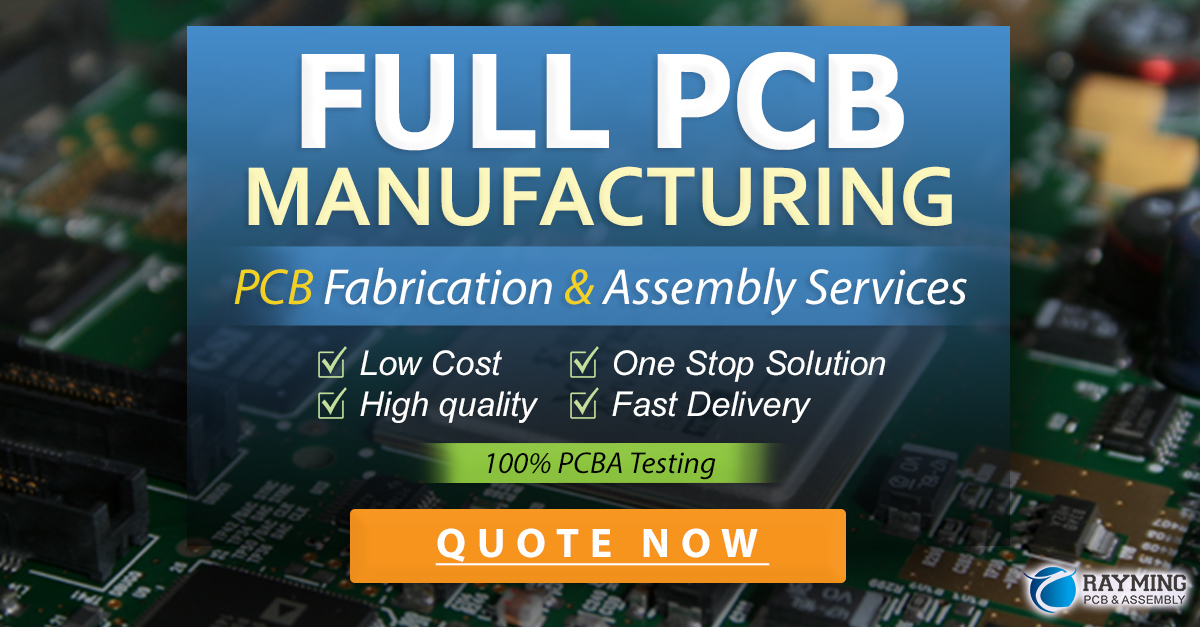
Processing and Manufacturing of High Tg PCB Resins
The processing and manufacturing of high Tg PCB resins require specialized equipment and techniques to ensure optimal performance and reliability. Some key aspects of high Tg PCB resin processing include:
1. Resin Formulation
The formulation of high Tg PCB resins involves the selection and blending of appropriate monomers, hardeners, and additives to achieve the desired properties. The choice of components and their proportions significantly influence the final properties of the cured resin, such as Tg, thermal expansion, and dielectric properties.
2. Lamination
The lamination process involves the consolidation of the PCB layers, including the high Tg resin-impregnated glass fabric (prepreg) and copper foil, under heat and pressure. The lamination parameters, such as temperature, pressure, and time, must be carefully controlled to ensure proper resin flow, void-free lamination, and optimal bond strength between layers.
3. Curing
After lamination, the PCB undergoes a curing process to cross-link the high Tg resin and achieve its final properties. The curing temperature and time depend on the specific resin formulation and the desired properties. Proper curing is essential to maximize the Tg, mechanical strength, and chemical resistance of the PCB.
4. Drilling and Plating
Once the PCB is cured, it undergoes drilling and plating processes to create the necessary interconnections between layers. High Tg PCB resins may require specialized drilling and plating techniques to ensure the integrity of the holes and the adhesion of the plated copper.
5. Surface Finish
The surface finish of the PCB, such as solder mask and surface treatment, must be compatible with the high Tg resin to ensure proper adhesion and protection. The choice of surface finish also depends on the specific application requirements, such as solderability, wire bonding, or high-frequency performance.
Future Trends in High Tg PCB Resin Technology
As the demand for high-performance electronics continues to grow, the development of advanced high Tg PCB resins is expected to accelerate. Some future trends in high Tg PCB resin technology include:
1. Nanocomposite Resins
The incorporation of nanofillers, such as carbon nanotubes, graphene, or ceramic nanoparticles, into high Tg PCB resins can further enhance their thermal, mechanical, and electrical properties. Nanocomposite resins offer the potential for higher Tg values, improved thermal conductivity, and reduced thermal expansion.
2. Bio-Based Resins
The development of bio-based high Tg PCB resins, derived from renewable resources, is gaining interest as a sustainable alternative to petroleum-based resins. Bio-based resins, such as those derived from lignin or vegetable oils, can offer comparable performance to traditional high Tg resins while reducing the environmental impact.
3. Additive Manufacturing
Additive manufacturing techniques, such as 3D printing, are being explored for the fabrication of high Tg PCBs. These methods can enable the creation of complex geometries, embedded components, and customized designs, offering new possibilities for PCB design and manufacturing.
Frequently Asked Questions (FAQ)
1. What is the difference between Tg and Td in PCB resins?
The glass transition temperature (Tg) is the temperature at which the PCB resin transitions from a hard, glassy state to a soft, rubbery state. The decomposition temperature (Td) is the temperature at which the resin begins to decompose and lose its structural integrity. Tg is more relevant for determining the maximum operating temperature of the PCB, while Td is essential for establishing the processing and manufacturing limits.
2. Can high Tg PCB resins be used for flexible PCBs?
Yes, some high Tg PCB resins, such as polyimide resins, are suitable for flexible PCBs. These resins offer excellent flexibility, mechanical strength, and thermal stability, making them ideal for applications that require both high performance and flexibility.
3. How do high Tg PCB resins compare to ceramic substrates in terms of thermal performance?
While ceramic substrates, such as alumina or aluminum nitride, offer excellent thermal conductivity and stability, they are brittle and expensive to manufacture. High Tg PCB resins provide a balance between thermal performance, mechanical properties, and cost-effectiveness. They can be engineered to achieve high thermal conductivity and low thermal expansion, making them a viable alternative to ceramic substrates in many applications.
4. Are high Tg PCB resins compatible with lead-free soldering processes?
Yes, most high Tg PCB resins are compatible with lead-free soldering processes. However, the specific resin formulation and surface finish must be selected to ensure proper wetting and adhesion of the lead-free solder. Some high Tg resins, such as those based on cyanate ester, may require special consideration due to their lower surface energy compared to traditional epoxy resins.
5. What are the key challenges in the adoption of high Tg PCB resins?
The main challenges in the adoption of high Tg PCB resins include higher material costs, more complex processing requirements, and the need for specialized equipment and expertise. Additionally, the long-term reliability and performance of high Tg PCBs in various environmental conditions must be thoroughly evaluated to ensure their suitability for critical applications. As the technology matures and the demand for high-performance electronics grows, these challenges are expected to be addressed through further research and development efforts.
Conclusion
Advanced high Tg PCB resin technology is playing an increasingly important role in enabling the development of high-performance electronics for demanding applications. With their superior thermal stability, mechanical strength, and electrical properties, high Tg PCB resins offer a reliable and cost-effective solution for PCBs exposed to harsh environments and high operating temperatures.
As the electronics industry continues to push the boundaries of performance and functionality, the adoption of high Tg PCB resins is expected to accelerate. Ongoing research and development efforts in areas such as nanocomposite resins, bio-based materials, and additive manufacturing are poised to further advance the capabilities of high Tg PCB technology.
By understanding the properties, advantages, and applications of high Tg PCB resins, electronics manufacturers and designers can make informed decisions when selecting materials for their PCBs. The continued development and adoption of advanced high Tg PCB resin technology will be crucial in enabling the next generation of high-performance electronics across various industries, from automotive and aerospace to telecommunications and power electronics.
Leave a Reply