1. Optimize PCB Design for Manufacturing (DFM)
One of the most effective ways to cut PCB Assembly Costs is to optimize your PCB design for manufacturing (DFM). By following DFM guidelines, you can ensure that your PCB design is compatible with the manufacturing process, minimizing the risk of errors, delays, and additional costs. Some key DFM considerations include:
- Choosing appropriate component sizes and packages
- Ensuring adequate spacing between components
- Avoiding unnecessary complexity in the PCB layout
- Using standard drill sizes and pad dimensions
- Minimizing the number of layers in the PCB stack-up
By incorporating DFM principles into your PCB design process, you can streamline manufacturing, reduce the likelihood of defects, and ultimately lower your assembly costs.
2. Leverage Economies of Scale
Another effective strategy for cutting PCB assembly costs is to leverage economies of scale. By placing larger orders or consolidating multiple smaller orders into a single production run, you can often secure more favorable pricing from your PCB assembly provider. This is because larger orders allow for more efficient use of materials, equipment, and labor, resulting in lower per-unit costs.
Consider the following table, which illustrates the potential cost savings associated with placing larger orders:
Order Quantity | Price per PCB |
---|---|
100 | $10.00 |
500 | $8.50 |
1,000 | $7.00 |
5,000 | $5.50 |
As you can see, the price per PCB decreases significantly as the order quantity increases. By carefully planning your production needs and placing larger orders when possible, you can take advantage of these economies of scale and reduce your overall PCB assembly costs.
3. Choose Cost-Effective Components
The selection of components for your PCB assembly can have a significant impact on overall costs. To minimize expenses without sacrificing quality, consider the following strategies:
3.1. Use Standard Components
Whenever possible, opt for standard, readily available components rather than custom or specialized parts. Standard components are typically less expensive due to their higher production volumes and wider availability. They also tend to have shorter lead times, which can help streamline your assembly process and reduce the risk of delays.
3.2. Consider Alternative Suppliers
Don’t be afraid to explore alternative component suppliers to find the best combination of price and quality. While it may be tempting to stick with familiar vendors, conducting thorough research and comparing prices from multiple sources can help you identify cost-saving opportunities without compromising on component performance.
3.3. Optimize Component Selection for Functionality
When designing your PCB, carefully evaluate each component’s role and specifications to ensure that you are not overengineering or using unnecessarily expensive parts. By selecting components that meet your functional requirements without exceeding them, you can often find cost-effective alternatives that still deliver the desired performance.
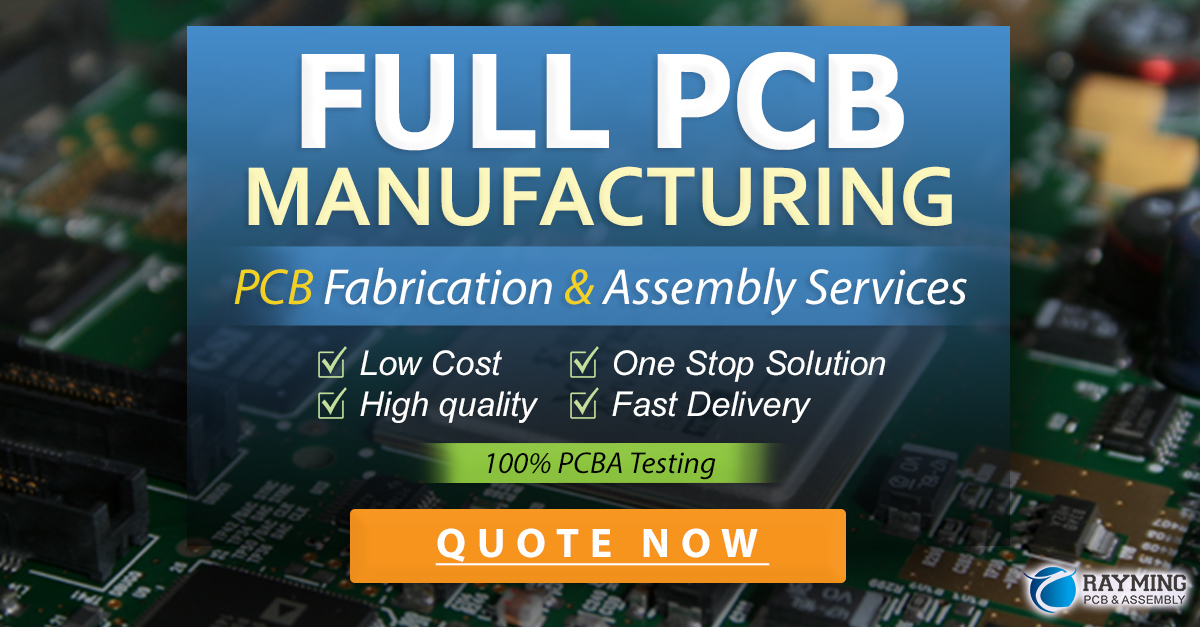
4. Minimize PCB Complexity
The complexity of your PCB design can have a direct impact on assembly costs. More complex designs generally require more time, resources, and specialized equipment to manufacture, leading to higher expenses. To minimize PCB complexity and reduce costs, consider the following tips:
- Reduce the number of layers in your PCB stack-up
- Minimize the use of blind and buried vias
- Avoid unnecessary routing complexity
- Use larger component packages when possible
- Optimize component placement for ease of assembly
By simplifying your PCB design, you can reduce manufacturing challenges, improve yields, and ultimately lower your assembly costs.
5. Implement Effective Quality Control Measures
While it may seem counterintuitive, investing in robust quality control measures can actually help you cut PCB assembly costs in the long run. By catching defects and issues early in the manufacturing process, you can avoid the expense of rework, scrap, and potential product recalls. Some effective quality control strategies include:
- Implementing automated optical inspection (AOI) to detect component placement and soldering defects
- Utilizing in-circuit testing (ICT) to verify the functionality of assembled PCBs
- Conducting thorough visual inspections at various stages of the assembly process
- Establishing clear quality standards and communicating them to your assembly provider
- Regularly auditing your assembly provider to ensure compliance with your quality requirements
By prioritizing quality control, you can minimize the risk of costly defects and ensure that your PCBs meet the highest standards of reliability and performance.
6. Optimize Inventory Management
Effective inventory management is another key strategy for cutting PCB assembly costs. By carefully monitoring and controlling your inventory levels, you can minimize the risk of obsolescence, reduce storage costs, and improve cash flow. Consider the following tips for optimizing your inventory management:
- Implement just-in-time (JIT) inventory practices to minimize excess stock
- Regularly review and adjust your safety stock levels based on demand forecasts
- Use automated inventory tracking systems to monitor stock levels and trigger reorders
- Negotiate favorable terms with suppliers, such as consignment stock or vendor-managed inventory
- Regularly assess your inventory for obsolete or slow-moving components and take appropriate action
By streamlining your inventory management practices, you can reduce the costs associated with excess stock and ensure that you have the right components on hand when you need them.
7. Leverage Automation and Technology
Investing in automation and advanced technology can help you cut PCB assembly costs by improving efficiency, reducing labor requirements, and minimizing the risk of human error. Some examples of automation and technology that can benefit your PCB assembly process include:
- Surface mount technology (SMT) placement machines
- Automated soldering equipment, such as wave soldering or selective soldering machines
- Automated optical inspection (AOI) systems
- Manufacturing execution systems (MES) for real-time production monitoring and control
- 3D printing for rapid prototyping and low-volume production
While these investments may require an initial capital outlay, they can often deliver significant cost savings over time through increased productivity, reduced defects, and improved quality control.
8. Foster Strong Supplier Relationships
Developing strong, long-term relationships with your PCB assembly suppliers can also help you cut costs and improve quality. By establishing a partnership based on trust, communication, and mutual benefit, you can often secure more favorable pricing, priority service, and access to value-added support. Some tips for fostering strong supplier relationships include:
- Communicate openly and transparently about your needs, expectations, and challenges
- Provide regular feedback on supplier performance and work collaboratively to address any issues
- Share long-term production forecasts to help suppliers plan for your needs
- Explore opportunities for joint cost-saving initiatives, such as process improvements or material substitutions
- Treat your suppliers as valued partners in your success, rather than simply transactional vendors
By nurturing strong supplier relationships, you can create a win-win scenario that helps you cut costs, improve quality, and ensure a reliable supply chain for your PCB assembly needs.
9. Outsource to Low-Cost Regions
Outsourcing your PCB assembly to low-cost regions, such as China, India, or Southeast Asia, can be an effective way to cut costs without sacrificing quality. These regions often have lower labor costs, more lenient regulations, and well-established electronics manufacturing ecosystems that can help you achieve significant cost savings.
However, it’s essential to carefully evaluate potential outsourcing partners to ensure that they meet your quality standards and can deliver reliable, timely service. Some factors to consider when outsourcing your PCB assembly include:
- The supplier’s experience and reputation in the industry
- Their quality control processes and certifications (e.g., ISO 9001, IPC-A-610)
- Their ability to meet your production volume and lead time requirements
- The level of communication and support they provide
- The total cost of ownership, including shipping, duties, and potential tariffs
By carefully selecting an outsourcing partner that aligns with your needs and expectations, you can often achieve significant cost savings without compromising on quality or service.
10. Implement Lean Manufacturing Principles
Lean manufacturing is a systematic approach to identifying and eliminating waste in production processes, with the goal of improving efficiency, reducing costs, and enhancing customer value. By implementing lean principles in your PCB assembly operations, you can streamline your processes, minimize defects, and ultimately cut costs. Some key lean manufacturing principles include:
- Identifying and eliminating non-value-added activities (waste)
- Implementing continuous flow production to minimize work-in-process inventory
- Using pull systems to produce only what is needed, when it is needed
- Empowering workers to identify and solve problems at the source
- Striving for continuous improvement through kaizen events and other initiatives
By embracing lean manufacturing principles, you can create a culture of efficiency and cost-consciousness that permeates your entire PCB assembly operation.
11. Regularly Review and Optimize Processes
Finally, cutting PCB assembly costs is an ongoing process that requires regular review and optimization. By continuously monitoring your processes, analyzing performance data, and identifying areas for improvement, you can ensure that you are always operating at peak efficiency and minimizing unnecessary expenses. Some strategies for regular process review and optimization include:
- Conducting regular cost audits to identify areas of high spend and potential savings
- Implementing a formal continuous improvement program, such as Six Sigma or Lean Six Sigma
- Encouraging employee suggestions and feedback for process improvements
- Benchmarking your performance against industry standards and best practices
- Investing in training and development to ensure that your team has the skills and knowledge to drive cost savings
By making process review and optimization a regular part of your PCB assembly operations, you can create a culture of continuous improvement that helps you cut costs, improve quality, and stay competitive in an ever-evolving market.
Frequently Asked Questions (FAQ)
1. What is Design for Manufacturing (DFM), and why is it important for cutting PCB assembly costs?
Design for Manufacturing (DFM) is the practice of designing products in a way that optimizes their manufacturability. In the context of PCB assembly, DFM involves designing PCBs that are easy to assemble, test, and repair, while minimizing the risk of defects and errors. By following DFM guidelines, you can reduce the complexity of your PCB design, improve yields, and ultimately lower your assembly costs.
2. How can outsourcing PCB assembly to low-cost regions help reduce costs?
Outsourcing your PCB assembly to low-cost regions, such as China or India, can help you take advantage of lower labor costs, more lenient regulations, and well-established electronics manufacturing ecosystems. By carefully selecting an outsourcing partner that meets your quality standards and can deliver reliable, timely service, you can often achieve significant cost savings without compromising on quality or performance.
3. What role does inventory management play in cutting PCB assembly costs?
Effective inventory management is crucial for cutting PCB assembly costs, as it helps you minimize the risk of obsolescence, reduce storage costs, and improve cash flow. By implementing strategies such as just-in-time (JIT) inventory practices, automated inventory tracking, and regular obsolescence reviews, you can ensure that you have the right components on hand when you need them, without tying up excessive capital in excess stock.
4. How can investing in automation and technology help reduce PCB assembly costs?
Investing in automation and advanced technology, such as SMT placement machines, automated soldering equipment, and AOI systems, can help you improve efficiency, reduce labor requirements, and minimize the risk of human error in your PCB assembly process. While these investments may require an initial capital outlay, they can often deliver significant cost savings over time through increased productivity, reduced defects, and improved quality control.
5. Why is regular process review and optimization important for cutting PCB assembly costs?
Cutting PCB assembly costs is an ongoing process that requires regular review and optimization. By continuously monitoring your processes, analyzing performance data, and identifying areas for improvement, you can ensure that you are always operating at peak efficiency and minimizing unnecessary expenses. This ongoing focus on continuous improvement helps you stay competitive in an ever-evolving market and drives long-term cost savings in your PCB assembly operations.
In conclusion, cutting PCB assembly costs without sacrificing quality requires a multi-faceted approach that encompasses design optimization, strategic sourcing, process improvement, and continuous monitoring. By implementing the 11 strategies outlined in this article, you can streamline your PCB assembly operations, reduce unnecessary expenses, and maintain the highest standards of quality and reliability. Remember, cost-cutting is an ongoing process, and by fostering a culture of continuous improvement and collaboration, you can drive long-term success in the competitive world of electronics manufacturing.
Leave a Reply