PCB Pricing Factor #1: Board Size
The size of the PCB is one of the most significant factors that affects its price. Larger boards require more material and take longer to manufacture, which increases the cost. PCB sizes are typically measured in square inches, and prices are often quoted based on this measurement.
Here’s a table showing some common PCB sizes and their typical price ranges:
PCB Size (sq in) | Typical Price Range |
---|---|
1-10 | $5-$20 |
11-25 | $15-$40 |
26-50 | $30-$80 |
51-100 | $60-$150 |
101-200 | $120-$300 |
As you can see, the price per square inch generally decreases as the board size increases, but the overall cost still goes up due to the increased material and manufacturing time required.
PCB Pricing Factor #2: Number of Layers
Another important factor that affects PCB pricing is the number of layers in the board. PCBs can have anywhere from one to dozens of layers, depending on the complexity of the design. Each additional layer adds to the cost of the board, as it requires more material and manufacturing steps.
Here’s a table showing typical prices for PCBs with different numbers of layers:
Number of Layers | Typical Price Range (per sq in) |
---|---|
1-2 | $0.50-$1.50 |
4 | $1.00-$3.00 |
6 | $2.00-$5.00 |
8 | $3.00-$8.00 |
10+ | $5.00-$15.00+ |
As you can see, the price per square inch increases significantly as the number of layers goes up. This is why it’s important to carefully consider the number of layers needed for your design, and to only use as many as necessary to keep costs down.
PCB Pricing Factor #3: Quantity
The quantity of PCBs ordered is another key factor that affects pricing. As with most manufacturing processes, there are economies of scale involved in PCB production. This means that the cost per board decreases as the quantity increases.
Here’s a table showing some typical price breaks for different quantities of PCBs:
Quantity | Typical Price per Board |
---|---|
1-10 | $50-$100 |
11-50 | $20-$50 |
51-100 | $10-$30 |
101-500 | $5-$20 |
501-1000 | $3-$10 |
1000+ | $1-$5 |
As you can see, the price per board drops significantly as the quantity increases. This is why it’s often more cost-effective to order larger quantities of PCBs, even if you don’t need them all right away.
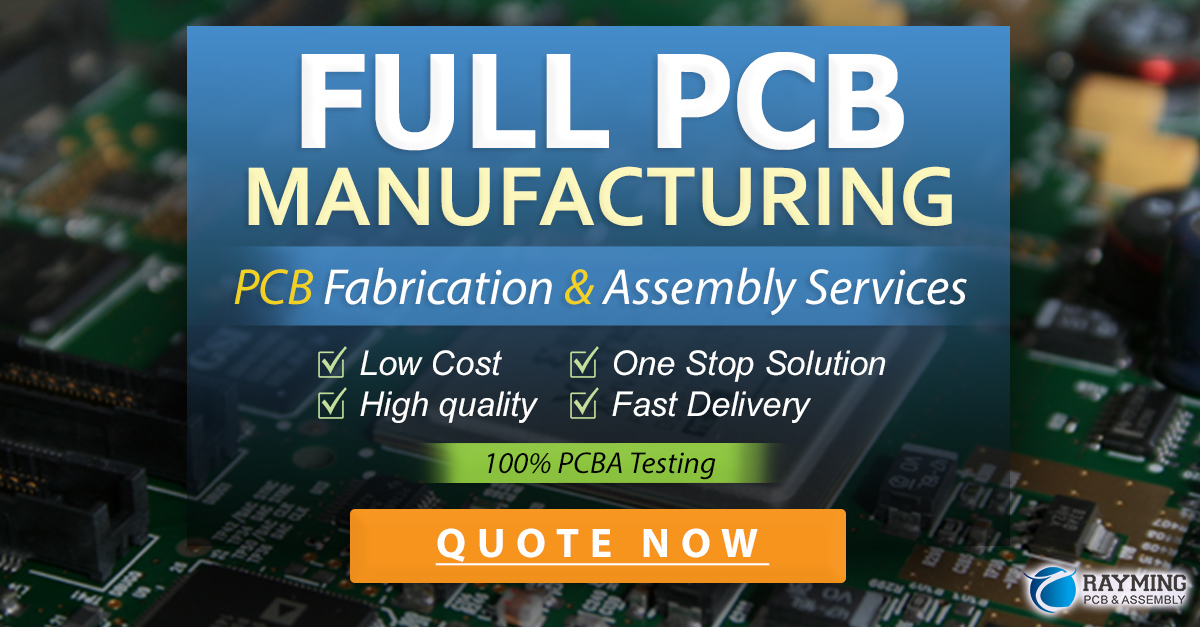
PCB Pricing Factor #4: Material
The material used to manufacture the PCB is another important factor that affects pricing. The most common material used for PCBs is FR-4, which is a type of fiberglass-reinforced epoxy laminate. However, there are other materials available that offer different properties, such as higher temperature resistance or better electrical insulation.
Here’s a table showing some common PCB materials and their typical price ranges:
Material | Typical Price Range (per sq in) |
---|---|
FR-4 | $0.50-$2.00 |
Polyimide | $2.00-$5.00 |
Teflon | $5.00-$10.00 |
Ceramic | $10.00-$20.00 |
Aluminum | $1.00-$3.00 |
As you can see, some materials are significantly more expensive than others. The choice of material will depend on the specific requirements of your PCB design, such as the operating environment and the electrical properties needed.
PCB Pricing Factor #5: Surface Finish
The surface finish of the PCB is another factor that can affect pricing. The surface finish is the coating applied to the copper traces and pads on the board to protect them from corrosion and improve solderability. There are several common surface finishes used for PCBs, each with its own advantages and disadvantages.
Here’s a table showing some common PCB surface finishes and their typical price ranges:
Surface Finish | Typical Price Range (per sq in) |
---|---|
HASL | $0.05-$0.20 |
ENIG | $0.20-$0.50 |
OSP | $0.05-$0.20 |
Immersion Tin | $0.10-$0.30 |
Immersion Gold | $0.20-$0.50 |
As you can see, some surface finishes are more expensive than others. The choice of surface finish will depend on factors such as the solderability requirements, the operating environment, and the shelf life needed for the PCBs.
PCB Pricing Factor #6: Copper Weight
The weight of the copper used in the PCB is another factor that can affect pricing. Copper weight is measured in ounces per square foot (oz/ft²), and refers to the thickness of the copper layer on the board. Thicker copper layers can carry more current and provide better heat dissipation, but they also add to the cost of the board.
Here’s a table showing some common copper weights and their typical price ranges:
Copper Weight (oz/ft²) | Typical Price Range (per sq in) |
---|---|
0.5 | $0.05-$0.20 |
1 | $0.10-$0.30 |
2 | $0.20-$0.50 |
3 | $0.30-$0.80 |
4+ | $0.50-$1.50+ |
As you can see, thicker copper layers are more expensive than thinner ones. The choice of copper weight will depend on the specific requirements of your PCB design, such as the current carrying capacity and heat dissipation needed.
PCB Pricing Factor #7: Minimum Hole Size
The minimum hole size is another factor that can affect PCB pricing. The hole size refers to the diameter of the smallest hole that can be drilled in the board. Smaller hole sizes require more precise drilling equipment and can add to the cost of the board.
Here’s a table showing some common minimum hole sizes and their typical price ranges:
Minimum Hole Size (mm) | Typical Price Range (per sq in) |
---|---|
0.3 | $0.50-$1.50 |
0.25 | $0.75-$2.00 |
0.2 | $1.00-$3.00 |
0.15 | $1.50-$4.00 |
0.1 | $2.00-$5.00+ |
As you can see, smaller hole sizes are more expensive than larger ones. The choice of minimum hole size will depend on the specific requirements of your PCB design, such as the component sizes and the routing density needed.
PCB Pricing Factor #8: Solder Mask Color
The color of the solder mask used on the PCB is another factor that can affect pricing. Solder mask is the coating applied to the board to protect the copper traces and prevent solder from bridging between them. While green is the most common color for solder mask, other colors are available for an additional cost.
Here’s a table showing some common solder mask colors and their typical price ranges:
Solder Mask Color | Typical Price Range (per sq in) |
---|---|
Green | Included |
Red | $0.05-$0.20 |
Blue | $0.05-$0.20 |
Yellow | $0.10-$0.30 |
Black | $0.10-$0.30 |
White | $0.20-$0.50 |
As you can see, non-standard solder mask colors are more expensive than the default green. The choice of solder mask color is largely a cosmetic one, but it can be important for branding or ease of assembly.
PCB Pricing Factor #9: Turnaround Time
Finally, the turnaround time for PCB manufacturing is another factor that can affect pricing. Turnaround time refers to the time between when an order is placed and when the finished PCBs are delivered. Faster turnaround times typically come with a premium price.
Here’s a table showing some common turnaround times and their typical price ranges:
Turnaround Time | Typical Price Increase |
---|---|
Standard (2-3 weeks) | Included |
Rush (1-2 weeks) | 20-50% |
Super Rush (3-5 days) | 50-100% |
Next Day | 100-200% |
As you can see, faster turnaround times come with a significant price increase. The choice of turnaround time will depend on the specific needs of your project and your budget constraints.
Frequently Asked Questions
1. What is the most important factor that affects PCB pricing?
The most important factor that affects PCB pricing is typically the board size, followed closely by the number of layers and the quantity ordered. These three factors together account for the majority of the cost of a PCB.
2. How can I reduce the cost of my PCB order?
There are several ways to reduce the cost of your PCB order, such as:
– Minimizing the board size and number of layers
– Ordering larger quantities to take advantage of volume discounts
– Choosing standard materials and surface finishes
– Using larger minimum hole sizes and standard solder mask colors
– Allowing for longer turnaround times
3. What is the typical price range for a small, simple PCB?
A small (under 10 sq in), simple (1-2 layer) PCB can typically be manufactured for $5-$20 per board, depending on the quantity ordered and other factors.
4. How much does adding additional layers increase the cost of a PCB?
Adding additional layers to a PCB can significantly increase its cost, with each additional layer adding $0.50-$2.00 or more per square inch, depending on the total number of layers and other factors.
5. Are there any other factors that can affect PCB pricing?
Yes, there are several other factors that can affect PCB pricing, such as:
– The complexity of the design and the amount of manual work required
– The quality and consistency requirements of the finished boards
– The location and capabilities of the PCB manufacturer
– The shipping and handling costs for the finished boards
While these factors are less significant than the major ones discussed in this article, they can still have an impact on the final price of a PCB order.
Conclusion
PCB pricing is a complex topic that depends on a wide range of factors, from the board size and number of layers to the materials and surface finishes used. By understanding these factors and how they impact the cost of PCBs, you can make informed decisions about your PCB design and ordering process to get the best value for your money.
Whether you’re a hobbyist building a one-off project or a professional designer working on a large-scale production run, taking the time to optimize your PCB design and ordering process can result in significant cost savings and better overall results. By carefully considering each of the factors discussed in this article and making smart choices based on your specific needs and constraints, you can ensure that you get the highest quality PCBs at the best possible price.
Leave a Reply