Choose the Right PCB Manufacturer
Factors to Consider When Selecting a PCB Manufacturer
Factor | Description |
---|---|
Reputation | Look for a manufacturer with a proven track record of delivering high-quality PCBs on time. |
Capabilities | Ensure the manufacturer has the necessary equipment and expertise to handle your specific PCB requirements. |
Certifications | Check if the manufacturer holds relevant certifications, such as ISO 9001, UL, or IPC. |
Customer Support | Choose a manufacturer that offers reliable customer support and clear communication throughout the process. |
Pricing | Consider the manufacturer’s pricing structure and ensure it aligns with your budget without compromising quality. |
Selecting the right PCB manufacturer is the foundation of a successful custom PCB Printing project. Take the time to research and compare different manufacturers based on the factors mentioned above to find the one that best suits your needs.
Understand Your PCB Requirements
Before embarking on your custom PCB printing project, it is essential to have a clear understanding of your specific PCB requirements. Consider the following aspects:
PCB Requirements Checklist
- Board size and shape
- Number of layers
- Material selection (e.g., FR-4, high-frequency materials)
- Copper weight and trace width
- Via type and size
- Surface finish (e.g., HASL, ENIG, OSP)
- Solder mask color
- Silkscreen color and labeling
- Impedance control
- Special requirements (e.g., high-density interconnect, flex or rigid-flex)
By clearly defining your PCB requirements, you can ensure that the manufacturer understands your needs and can deliver a board that meets your expectations.
Design for Manufacturability (DFM)
Designing your PCB with manufacturability in mind is crucial for ensuring a smooth and cost-effective production process. Here are some key DFM guidelines to follow:
DFM Guidelines
- Adhere to the manufacturer’s design rules and specifications
- Use standard component sizes and footprints
- Maintain proper spacing between components and traces
- Avoid sharp angles and use rounded corners for traces
- Use appropriate via sizes and spacing
- Minimize the use of blind and buried vias
- Ensure adequate clearance for assembly and testing
- Consider the limitations of the manufacturing process (e.g., minimum hole size, trace width)
By following DFM guidelines, you can minimize the risk of manufacturing issues, reduce costs, and improve the overall quality of your custom PCB.
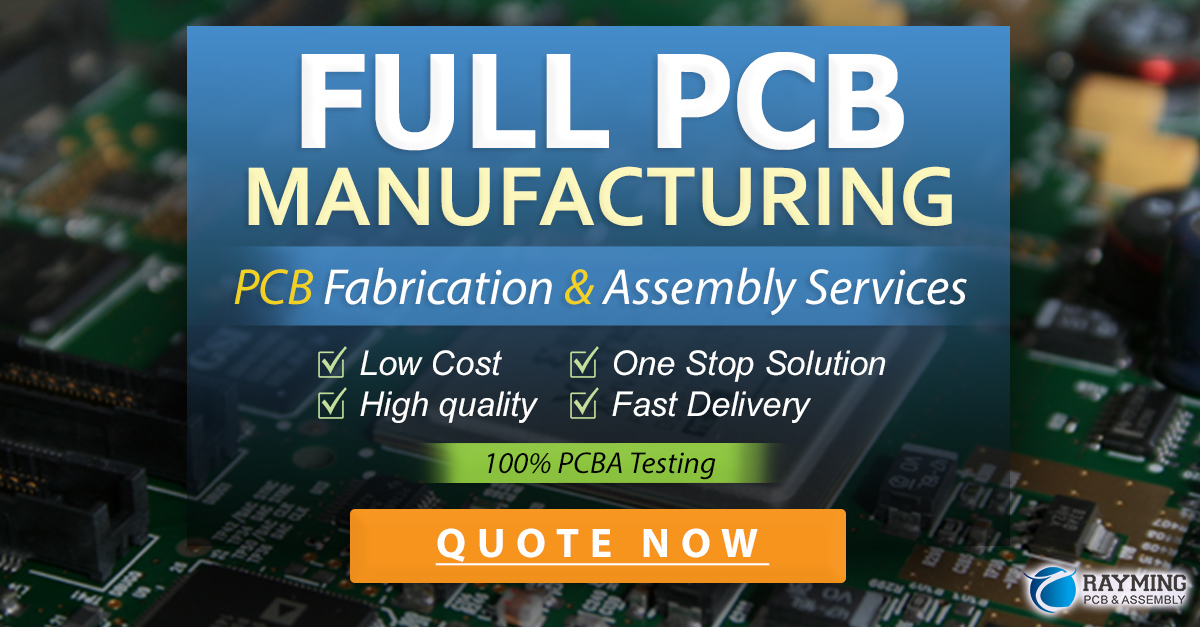
Choose the Right PCB Printing Technology
There are several PCB printing technologies available, each with its own advantages and limitations. The most common technologies are:
Comparison of PCB Printing Technologies
Technology | Advantages | Limitations |
---|---|---|
Through-hole | – Strong mechanical connections – Suitable for high-power applications |
– Larger board size – Higher manufacturing costs – Limited routing density |
Surface Mount (SMT) | – Smaller board size – Higher component density – Lower manufacturing costs |
– More complex assembly process – Requires specialized equipment |
Mixed Technology | – Combines the benefits of through-hole and SMT – Provides flexibility in design |
– Higher complexity – May increase manufacturing costs |
Consider your specific requirements and consult with your PCB manufacturer to determine the most suitable printing technology for your project.
Pay Attention to PCB Testing and Inspection
Thorough testing and inspection are essential for ensuring the quality and reliability of your custom PCB. Here are some common testing and inspection methods:
PCB Testing and Inspection Methods
- Visual inspection
- Automated Optical Inspection (AOI)
- X-ray inspection
- Electrical testing (e.g., continuity, insulation resistance)
- Functional testing
- In-circuit testing (ICT)
- Burn-in testing
- Environmental testing (e.g., temperature, humidity, vibration)
Work closely with your PCB manufacturer to develop a comprehensive testing and inspection plan that covers all critical aspects of your custom PCB.
Plan for PCB Assembly and Packaging
Once your custom PCB is manufactured, you need to consider the assembly and packaging process. Here are some key factors to keep in mind:
PCB Assembly and Packaging Considerations
- Component sourcing and procurement
- Assembly method (e.g., manual, automated)
- Soldering techniques (e.g., wave soldering, reflow soldering)
- Conformal coating and potting (if required)
- Labeling and serialization
- Packaging and shipping requirements
- Electrostatic Discharge (ESD) protection
Collaborate with your PCB manufacturer and assembly partner to ensure a smooth and efficient assembly and packaging process that meets your specific needs.
Frequently Asked Questions (FAQ)
1. What is the typical turnaround time for custom PCB printing?
The turnaround time for custom PCB printing varies depending on the complexity of the design, the chosen manufacturer, and the manufacturing technology. Generally, it can range from a few days to several weeks. Discuss your timeline requirements with your chosen manufacturer to ensure they can meet your needs.
2. How much does custom PCB printing cost?
The cost of custom PCB printing depends on several factors, such as the board size, complexity, number of layers, materials, and quantity. As a general rule, larger quantities and simpler designs result in lower per-unit costs. Request quotes from multiple manufacturers and compare prices to find the best option for your budget.
3. What files do I need to provide for custom PCB printing?
To begin the custom PCB printing process, you typically need to provide Gerber files, which include information about the PCB layers, drill files, and component placement. Additionally, you may need to provide a bill of materials (BOM) and assembly instructions. Consult with your chosen manufacturer for their specific file requirements.
4. Can I request samples before placing a large order?
Yes, most PCB manufacturers offer the option to order prototype or sample boards before committing to a large production run. This allows you to test and validate your design, ensuring it meets your requirements before investing in a larger quantity.
5. What certifications should I look for in a PCB manufacturer?
When selecting a PCB manufacturer, look for certifications such as ISO 9001, which demonstrates a commitment to quality management systems, and UL or IPC certifications, which indicate compliance with industry standards for safety and reliability. These certifications provide assurance that the manufacturer adheres to strict quality control processes.
Conclusion
Custom PCB printing is a complex process that requires careful consideration of multiple factors to ensure success. By paying special attention to the six key aspects discussed in this article – choosing the right manufacturer, understanding your PCB requirements, designing for manufacturability, selecting the appropriate printing technology, thorough testing and inspection, and planning for assembly and packaging – you can navigate the custom PCB printing process with confidence and achieve the best possible results for your project.
Remember to communicate clearly with your chosen PCB manufacturer throughout the process, and don’t hesitate to ask questions or seek guidance when needed. With the right approach and attention to detail, custom PCB printing can help bring your electronic projects to life, enabling you to create innovative and reliable products that meet your specific needs.
Leave a Reply