Introduction
When it comes to designing and manufacturing medical devices, the quality of the printed circuit board (PCB) is of utmost importance. Medical grade PCBs are held to a higher standard than regular PCBs due to the critical nature of their applications. These PCBs are used in devices that directly impact patient health and safety, such as pacemakers, defibrillators, and medical imaging equipment. As such, it is crucial to ensure that the PCBs used in these devices are of the highest quality and reliability.
In this article, we will discuss seven tips for getting a high-quality medical grade PCB. By following these tips, you can ensure that your medical devices are built with the best possible components and are able to withstand the rigors of their intended use.
Tip 1: Choose the Right Materials
Importance of Choosing the Right Materials
One of the most important factors in getting a high-quality medical grade PCB is choosing the right materials. Medical grade PCBs are exposed to a wide range of environmental conditions, including temperature fluctuations, humidity, and chemical exposure. As such, the materials used in these PCBs must be able to withstand these conditions without degrading or failing.
Common Materials Used in Medical Grade PCBs
Some of the most common materials used in medical grade PCBs include:
- FR-4: This is a glass-reinforced epoxy laminate that is commonly used in PCBs. It has good mechanical and electrical properties and is resistant to moisture and chemicals.
- Polyimide: This is a high-performance polymer that is often used in medical grade PCBs due to its excellent thermal and chemical resistance.
- Ceramic: Ceramic substrates are sometimes used in medical grade PCBs due to their high thermal conductivity and low dielectric constant.
Factors to Consider When Choosing Materials
When choosing materials for your medical grade PCB, there are several factors to consider:
- The specific application of the PCB and the environmental conditions it will be exposed to
- The required electrical and mechanical properties of the PCB
- The cost and availability of the materials
- Any regulatory requirements or standards that must be met
Tip 2: Use Appropriate Design Techniques
Importance of Proper PCB Design
Proper PCB design is critical for ensuring the reliability and performance of medical grade PCBs. Poor design can lead to signal integrity issues, electromagnetic interference (EMI), and other problems that can compromise the functioning of the device.
Key Design Considerations for Medical Grade PCBs
Some of the key design considerations for medical grade PCBs include:
- Signal integrity: Ensuring that signals are transmitted accurately and reliably without distortion or interference
- EMI: Minimizing electromagnetic interference to prevent interference with other devices and ensure compliance with regulatory standards
- Thermal management: Ensuring that the PCB can dissipate heat effectively to prevent overheating and ensure reliable operation
- Manufacturability: Designing the PCB in a way that is easy to manufacture and assemble to reduce costs and improve reliability
Best Practices for Medical Grade PCB Design
To ensure proper PCB design for medical applications, follow these best practices:
- Use appropriate layout techniques, such as proper grounding and shielding, to minimize EMI and ensure signal integrity
- Use thermal management techniques, such as heat sinks and thermal vias, to dissipate heat effectively
- Follow design for manufacturability (DFM) guidelines to ensure that the PCB can be easily and reliably manufactured
- Use simulation tools to verify the performance of the PCB before manufacturing
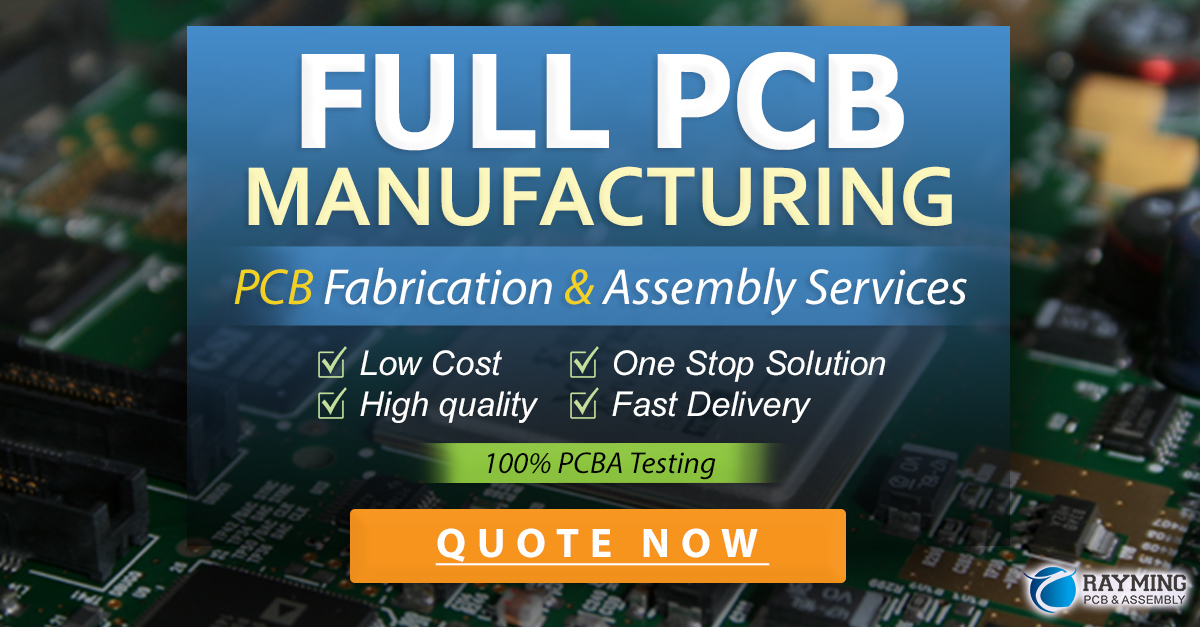
Tip 3: Choose the Right Manufacturing Partner
Importance of Choosing the Right Manufacturing Partner
Choosing the right manufacturing partner is critical for ensuring the quality and reliability of your medical grade PCBs. Not all PCB manufacturers have the expertise and capabilities needed to produce high-quality medical grade PCBs.
Factors to Consider When Choosing a Manufacturing Partner
When choosing a manufacturing partner for your medical grade PCBs, consider the following factors:
- Experience and expertise in manufacturing medical grade PCBs
- Quality control processes and certifications (e.g. ISO 13485)
- Ability to meet regulatory requirements and standards
- Manufacturing capabilities and capacity
- Cost and lead time
Questions to Ask Potential Manufacturing Partners
To help you choose the right manufacturing partner, ask potential partners the following questions:
- What experience do you have in manufacturing medical grade PCBs?
- What quality control processes and certifications do you have in place?
- How do you ensure compliance with regulatory requirements and standards?
- What are your manufacturing capabilities and capacity?
- What are your typical lead times and costs for medical grade PCBs?
Tip 4: Implement Stringent Quality Control Measures
Importance of Quality Control in Medical Grade PCBs
Quality control is critical for ensuring the reliability and safety of medical grade PCBs. Even small defects or variations can have serious consequences in medical applications.
Key Quality Control Measures for Medical Grade PCBs
Some of the key quality control measures for medical grade PCBs include:
- Incoming inspection of materials and components
- In-process inspections and testing
- Final inspection and testing of finished PCBs
- Traceability and documentation of all materials, processes, and tests
- Use of statistical process control (SPC) to monitor and control processes
Best Practices for Implementing Quality Control Measures
To effectively implement quality control measures for medical grade PCBs, follow these best practices:
- Establish clear quality standards and specifications for materials, processes, and finished PCBs
- Use automated inspection and testing equipment where possible to reduce human error and improve accuracy
- Implement a robust documentation and traceability system to ensure that all materials, processes, and tests are properly recorded and can be traced back if needed
- Regularly review and analyze quality data to identify trends and opportunities for improvement
- Provide training and resources to ensure that all personnel involved in the manufacturing process understand and follow quality control procedures
Tip 5: Conduct Thorough Testing and Validation
Importance of Testing and Validation in Medical Grade PCBs
Thorough testing and validation are essential for ensuring the safety and reliability of medical grade PCBs. Testing helps to identify any defects or issues with the PCB before it is used in a medical device, while validation ensures that the PCB meets all necessary regulatory requirements and standards.
Types of Testing and Validation for Medical Grade PCBs
Some of the common types of testing and validation for medical grade PCBs include:
- Electrical testing: Testing the electrical performance and functionality of the PCB, including continuity, resistance, and insulation testing
- Environmental testing: Testing the PCB’s ability to withstand environmental conditions such as temperature, humidity, and vibration
- EMC testing: Testing the PCB’s electromagnetic compatibility and ability to operate without causing or being affected by electromagnetic interference
- Functional testing: Testing the PCB’s ability to perform its intended function within the medical device
- Regulatory testing: Testing the PCB’s compliance with relevant regulatory standards and requirements, such as IEC 60601-1 for medical electrical equipment
Best Practices for Conducting Testing and Validation
To ensure thorough and effective testing and validation of medical grade PCBs, follow these best practices:
- Develop a comprehensive test plan that covers all necessary types of testing and validation
- Use qualified and calibrated test equipment and facilities
- Follow established test procedures and protocols
- Document all test results and any issues or defects identified
- Address any issues or defects promptly and retest as necessary
- Maintain detailed records of all testing and validation activities for regulatory compliance and traceability
Tip 6: Ensure Traceability and Documentation
Importance of Traceability and Documentation in Medical Grade PCBs
Traceability and documentation are critical for ensuring the quality and regulatory compliance of medical grade PCBs. Traceability allows manufacturers to track the materials, processes, and tests used in the production of each PCB, while documentation provides evidence of compliance with regulatory requirements and standards.
Key Elements of Traceability and Documentation for Medical Grade PCBs
Some of the key elements of traceability and documentation for medical grade PCBs include:
- Material traceability: Tracking the source and lot number of all materials used in the PCB, including the substrate, copper, solder mask, and silkscreen
- Process traceability: Tracking the processes used in the production of the PCB, including the equipment, parameters, and operators involved
- Test traceability: Tracking the tests performed on the PCB, including the test equipment, procedures, and results
- Certificate of conformance (CoC): A document certifying that the PCB meets all applicable specifications and requirements
- Device history record (DHR): A record of the manufacturing process for each individual PCB, including all materials, processes, and tests used
Best Practices for Ensuring Traceability and Documentation
To ensure effective traceability and documentation for medical grade PCBs, follow these best practices:
- Establish a robust system for tracking and documenting all materials, processes, and tests used in the production of each PCB
- Use unique identification numbers for each PCB and associated documentation
- Maintain detailed records of all production activities, including any deviations or nonconformances
- Regularly review and audit documentation to ensure completeness and accuracy
- Store documentation securely and make it readily available for regulatory inspections or audits
Tip 7: Stay Up-to-Date with Regulatory Requirements and Standards
Importance of Regulatory Compliance in Medical Grade PCBs
Medical grade PCBs are subject to a range of regulatory requirements and standards to ensure their safety and effectiveness. Failure to comply with these requirements can result in costly delays, recalls, or even legal action.
Key Regulatory Requirements and Standards for Medical Grade PCBs
Some of the key regulatory requirements and standards for medical grade PCBs include:
- IEC 60601-1: A standard for the safety and essential performance of medical electrical equipment
- ISO 13485: A quality management system standard for medical devices
- FDA 21 CFR Part 820: Quality system regulations for medical devices in the United States
- EU Medical Device Regulation (MDR): Regulations for medical devices in the European Union
- RoHS: Restriction of Hazardous Substances Directive, which restricts the use of certain hazardous materials in electronic equipment
Best Practices for Staying Up-to-Date with Regulatory Requirements
To ensure ongoing compliance with regulatory requirements and standards for medical grade PCBs, follow these best practices:
- Regularly review and monitor changes to relevant regulatory requirements and standards
- Participate in industry associations and attend conferences and training events to stay informed of regulatory developments
- Conduct internal audits and assessments to identify any gaps or areas for improvement in regulatory compliance
- Work with experienced regulatory consultants or legal counsel to ensure that your PCBs meet all necessary requirements and standards
- Maintain detailed documentation of regulatory compliance activities, including any corrective actions taken to address identified issues
Frequently Asked Questions
What is a medical grade PCB?
A medical grade PCB is a printed circuit board that is designed and manufactured to meet the specific requirements and standards for use in medical devices. These PCBs are subject to more stringent quality control measures and regulatory requirements than standard PCBs.
Why are medical grade PCBs important?
Medical grade PCBs are critical for ensuring the safety and reliability of medical devices. These devices are used in life-critical applications where even small defects or failures can have serious consequences for patient health and safety. By using high-quality medical grade PCBs, manufacturers can reduce the risk of device failures and ensure that their products meet all necessary regulatory requirements.
What are some common materials used in medical grade PCBs?
Some common materials used in medical grade PCBs include FR-4, polyimide, and ceramic substrates. These materials are chosen for their high reliability, thermal stability, and resistance to environmental factors such as moisture and chemicals.
How can I ensure the quality of my medical grade PCBs?
To ensure the quality of your medical grade PCBs, follow the tips outlined in this article, including choosing the right materials, using appropriate design techniques, selecting a qualified manufacturing partner, implementing stringent quality control measures, conducting thorough testing and validation, ensuring traceability and documentation, and staying up-to-date with regulatory requirements and standards.
What are some key regulatory requirements and standards for medical grade PCBs?
Some key regulatory requirements and standards for medical grade PCBs include IEC 60601-1 for medical electrical equipment, ISO 13485 for medical device quality management systems, FDA 21 CFR Part 820 for quality system regulations in the United States, EU Medical Device Regulation (MDR) for medical devices in the European Union, and RoHS for restriction of hazardous substances in electronic equipment.
Conclusion
Designing and manufacturing high-quality medical grade PCBs is a complex and challenging process that requires careful attention to materials, design, manufacturing, quality control, testing, documentation, and regulatory compliance. By following the tips outlined in this article, you can ensure that your medical grade PCBs meet the highest standards of quality and reliability, and are able to support the critical functions of life-saving medical devices. Whether you are a medical device manufacturer or a PCB designer, staying up-to-date with the latest best practices and regulatory requirements is essential for success in this demanding and constantly evolving field.
Leave a Reply