What is Pad hole ring copper?
Pad hole ring copper refers to the copper plating that surrounds the holes drilled in a PCB. These holes, also called vias or through-holes, allow electrical connections between different layers of the PCB. The pad hole ring copper provides a conductive surface for soldering components and ensures a reliable electrical connection.
The primary functions of pad hole ring copper include:
- Providing a conductive path for electrical signals
- Enhancing the mechanical strength of the hole
- Facilitating the soldering process
- Improving the overall reliability of the PCB
Importance of Pad hole ring copper Specification
Proper specification of pad hole ring copper is crucial for several reasons:
-
Electrical conductivity: The thickness and uniformity of the copper plating directly affect the electrical conductivity of the via. Insufficient or non-uniform plating can lead to high resistance, signal loss, or even open circuits.
-
Mechanical strength: The copper plating adds structural support to the hole, preventing damage during the assembly process and ensuring the long-term reliability of the PCB.
-
Solderability: A well-specified pad hole ring copper enables proper wetting and adhesion of solder, resulting in strong and reliable solder joints.
-
Manufacturing yield: Adhering to the correct specifications minimizes defects and improves the overall manufacturing yield, reducing costs and lead times.
Manufacturing Process
The manufacturing process for pad hole ring copper involves several steps:
-
Drilling: Holes are drilled into the PCB substrate according to the design specifications.
-
Desmear: A chemical or plasma process is used to remove any debris or resin smear from the hole walls, ensuring a clean surface for copper deposition.
-
Electroless copper plating: A thin layer of copper is deposited onto the hole walls through an electroless chemical process. This layer acts as a conductive seed for the subsequent electrolytic plating.
-
Electrolytic copper plating: The PCB is immersed in an electrolytic bath, where an electric current is applied to deposit a thicker layer of copper onto the hole walls. The thickness of this layer is determined by the plating time and current density.
-
Inspection: The plated holes are inspected for thickness, uniformity, and adherence to specifications using various methods such as cross-sectioning, microscopy, or electrical testing.
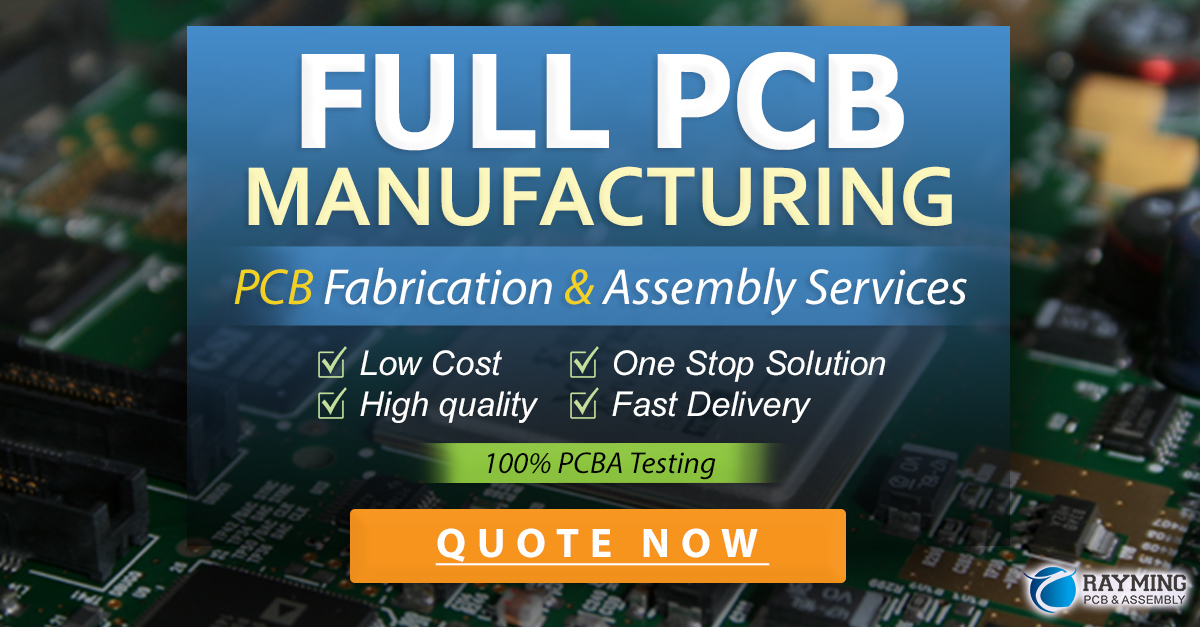
Key Specifications
Several key specifications define the quality and performance of pad hole ring copper:
Copper Thickness
The copper thickness is a critical parameter that affects the electrical and mechanical properties of the via. The minimum copper thickness is typically specified in micrometers (µm) or mils (thousandths of an inch). Common specifications include:
Standard | Minimum Copper Thickness |
---|---|
IPC-6012 | 20 µm (0.79 mil) |
IPC-6013 | 25 µm (0.98 mil) |
IPC-6018 | 35 µm (1.38 mil) |
The required copper thickness may vary depending on the specific application, hole size, and aspect ratio (ratio of hole depth to diameter).
Hole Size and Aspect Ratio
The hole size and aspect ratio influence the ability to achieve the specified copper thickness uniformly throughout the hole. Smaller hole sizes and higher aspect ratios pose challenges for the plating process. Common hole sizes and their corresponding aspect ratios are:
Hole Size (mm) | Typical Aspect Ratio |
---|---|
0.2 – 0.3 | 8:1 – 10:1 |
0.3 – 0.5 | 6:1 – 8:1 |
0.5 – 1.0 | 4:1 – 6:1 |
Designers should consider the manufacturability of the specified hole sizes and aspect ratios to ensure reliable plating results.
Plating Uniformity
The uniformity of the copper plating is essential for maintaining consistent electrical and mechanical properties throughout the via. The plating thickness should be uniform within a specified tolerance, typically expressed as a percentage of the nominal thickness. For example, IPC-6012 specifies a plating uniformity of ±20% for Class 2 and ±10% for Class 3 PCBs.
Non-uniform plating can lead to issues such as:
- Localized high resistance or open circuits
- Weak solder joints
- Reduced mechanical strength
- Increased susceptibility to thermal stress and cracking
Adhesion and Coverage
The copper plating must adhere properly to the hole walls and provide complete coverage without voids or gaps. Poor adhesion or incomplete coverage can result in:
- Delamination of the copper plating
- Intermittent or open electrical connections
- Reduced mechanical strength
- Increased risk of contamination and corrosion
Adhesion and coverage are typically evaluated through visual inspection, cross-sectioning, or peel strength testing.
Design Considerations
When designing PCBs with pad hole ring copper, several factors should be considered to ensure optimal performance and manufacturability:
-
Hole size and aspect ratio: Choose hole sizes and aspect ratios that are compatible with the manufacturing capabilities and ensure reliable plating results.
-
Copper thickness: Specify the appropriate copper thickness based on the electrical and mechanical requirements of the application, taking into account the hole size and aspect ratio.
-
Pad size and shape: Design the pad size and shape to provide sufficient area for soldering and to accommodate any potential misalignment during the assembly process.
-
Thermal management: Consider the thermal expansion mismatch between the copper plating and the PCB substrate, especially for high-aspect-ratio holes. Proper design and material selection can help mitigate thermal stress and prevent cracking.
-
Manufacturing constraints: Consult with the PCB manufacturer to understand their capabilities and limitations, and design within those constraints to ensure the best possible results.
FAQ
1. What is the minimum copper thickness required for pad hole ring copper?
The minimum copper thickness varies depending on the specific standard and application. Common specifications include:
- IPC-6012: 20 µm (0.79 mil)
- IPC-6013: 25 µm (0.98 mil)
- IPC-6018: 35 µm (1.38 mil)
2. How does the hole size and aspect ratio affect the pad hole ring copper plating process?
Smaller hole sizes and higher aspect ratios pose challenges for the plating process, as it becomes more difficult to achieve uniform copper thickness throughout the hole. Designers should consider the manufacturability of the specified hole sizes and aspect ratios to ensure reliable plating results.
3. What are the consequences of non-uniform copper plating in pad hole ring copper?
Non-uniform plating can lead to issues such as localized high resistance or open circuits, weak solder joints, reduced mechanical strength, and increased susceptibility to thermal stress and cracking.
4. How is the adhesion and coverage of pad hole ring copper evaluated?
Adhesion and coverage are typically evaluated through visual inspection, cross-sectioning, or peel strength testing. These methods help identify any issues with delamination, voids, or incomplete coverage.
5. What design considerations should be taken into account when specifying pad hole ring copper?
Designers should consider factors such as hole size and aspect ratio, copper thickness, pad size and shape, thermal management, and manufacturing constraints. Consulting with the PCB manufacturer and designing within their capabilities and limitations can help ensure the best possible results.
Conclusion
Pad hole ring copper is a vital component in the manufacturing of PCBs, ensuring proper electrical conductivity, mechanical strength, and solderability. Understanding the specifications, manufacturing process, and design considerations is essential for creating reliable and high-performance electronic devices.
By adhering to industry standards, selecting appropriate hole sizes and aspect ratios, specifying sufficient copper thickness, and designing with manufacturability in mind, designers and manufacturers can optimize the quality and reliability of their PCBs.
As technology advances and device miniaturization continues, the importance of pad hole ring copper specification will only grow. Staying up-to-date with the latest industry guidelines and best practices will be crucial for success in the ever-evolving world of electronics manufacturing.
Leave a Reply