What is a Copper PCB?
A copper PCB is a printed circuit board that uses copper as the primary conductive material for its traces, pads, and planes. Copper is laminated onto a non-conductive substrate, typically made of fiberglass or epoxy resin, to create the PCB. The copper layer is then etched to form the desired circuit pattern, connecting the various electronic components mounted on the board.
Advantages of Using Copper in PCB Manufacturing
Copper offers several advantages that make it the preferred choice for PCB manufacturing:
-
Excellent Electrical Conductivity: Copper has a high electrical conductivity, second only to silver among metals. This property allows for efficient and reliable transmission of electrical signals throughout the PCB.
-
Cost-Effectiveness: Compared to other highly conductive metals like gold or silver, copper is relatively inexpensive. This makes it an economical choice for large-scale PCB manufacturing.
-
Durability: Copper is a sturdy metal that can withstand the stresses of the PCB manufacturing process and the operating conditions of the final product.
-
Ease of Processing: Copper is malleable and ductile, making it easy to laminate onto the substrate and etch into the desired circuit pattern.
The PCB Manufacturing Process with Copper
The PCB manufacturing process involving copper consists of several key steps:
-
Substrate Preparation: The non-conductive substrate, usually fiberglass or epoxy resin, is cut to the desired size and shape.
-
Copper Lamination: A thin layer of copper foil is laminated onto the substrate using heat and pressure. The thickness of the copper layer can vary depending on the specific requirements of the PCB.
-
Photoresist Application: A photosensitive resist is applied to the copper layer and then exposed to UV light through a photomask containing the circuit pattern.
-
Etching: The exposed copper is etched away using a chemical solution, leaving behind the desired circuit pattern.
-
Drilling: Holes are drilled through the PCB to accommodate through-hole components and provide interconnections between layers in multi-layer boards.
-
Plating: The holes are plated with copper to ensure electrical connectivity between layers.
-
Solder Mask Application: A solder mask is applied to the PCB to protect the copper traces from oxidation and prevent solder bridges during the assembly process.
-
Silkscreen Printing: Text and symbols are printed onto the PCB using silkscreen printing for identification and assembly purposes.
-
Surface Finishing: The exposed copper areas, such as pads and contacts, are coated with a protective finish like HASL (Hot Air Solder Leveling), ENIG (Electroless Nickel Immersion Gold), or OSP (Organic Solderability Preservative) to prevent oxidation and enhance solderability.
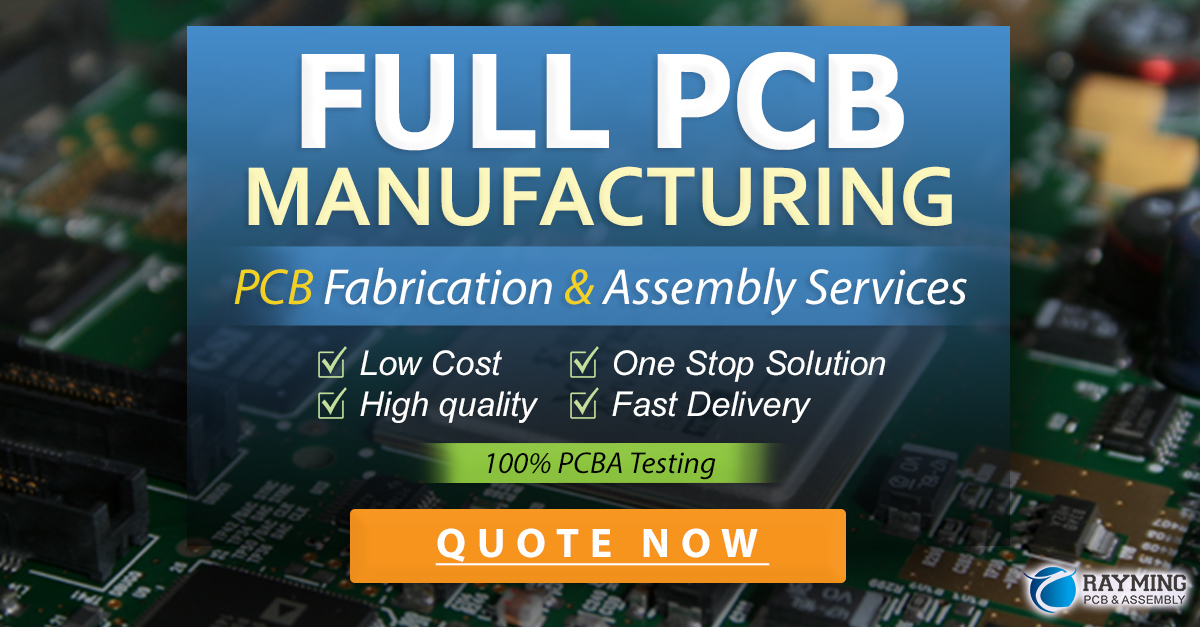
Factors Affecting Copper PCB Manufacturing
Several factors can impact the quality and performance of copper PCBs during manufacturing:
-
Copper Thickness: The thickness of the copper layer can affect the current carrying capacity, signal integrity, and heat dissipation of the PCB. Thicker copper layers are used for high-power applications, while thinner layers are suitable for high-density designs.
-
Substrate Material: The choice of substrate material can influence the mechanical stability, thermal properties, and dielectric constant of the PCB. Common substrate materials include FR-4, Rogers, and polyimide.
-
Etching Process: The etching process must be carefully controlled to ensure accurate reproduction of the circuit pattern. Over-etching or under-etching can lead to defects like open circuits or short circuits.
-
Drilling Quality: The accuracy and cleanliness of the drilled holes are crucial for ensuring proper electrical connectivity and preventing signal loss.
-
Surface Finish: The choice of surface finish can impact the solderability, durability, and signal integrity of the PCB. Each surface finish has its own advantages and disadvantages, and the selection depends on the specific application requirements.
Copper PCB Applications
Copper PCBs find applications in a wide range of industries and products:
Industry | Applications |
---|---|
Consumer Electronics | Smartphones, tablets, laptops, televisions, gaming consoles |
Automotive | Engine control units, infotainment systems, sensors, ADAS |
Medical Devices | Diagnostic equipment, monitoring systems, implantable devices |
Aerospace and Defense | Avionics, radar systems, communication equipment, satellites |
Industrial Automation | PLCs, motor controllers, HMIs, sensors |
Telecommunications | Routers, switches, base stations, fiber optic equipment |
Frequently Asked Questions (FAQ)
-
Q: What is the difference between single-sided and double-sided copper PCBs?
A: Single-sided copper PCBs have copper traces on only one side of the substrate, while double-sided PCBs have copper traces on both sides. Double-sided PCBs offer higher component density and better signal integrity compared to single-sided PCBs. -
Q: Can copper PCBs be used for high-frequency applications?
A: Yes, copper PCBs can be used for high-frequency applications, but the design must account for factors like impedance control, signal integrity, and EMI/EMC considerations. Special substrate materials like Rogers or PTFE may be used for better high-frequency performance. -
Q: How does the copper thickness affect the current carrying capacity of a PCB?
A: The current carrying capacity of a PCB increases with the thickness of the copper layer. Thicker copper layers have lower resistance and can handle higher currents without overheating or causing voltage drops. -
Q: What is the purpose of the solder mask on a copper PCB?
A: The solder mask is a protective layer applied to the copper traces to prevent oxidation and accidental solder bridges during the assembly process. It also provides electrical insulation and improves the aesthetics of the PCB. -
Q: Can copper PCBs be recycled?
A: Yes, copper PCBs can be recycled to recover the valuable copper and other materials. Recycling helps reduce electronic waste and minimizes the environmental impact of PCB manufacturing.
Conclusion
Copper PCBs play a vital role in the manufacturing of electronic devices across various industries. The excellent electrical conductivity, cost-effectiveness, and ease of processing make copper the preferred choice for PCB manufacturing. By understanding the factors that affect copper PCB manufacturing and the various applications they serve, designers and engineers can make informed decisions when developing their products. As technology continues to advance, copper PCBs will remain an essential component in the ever-evolving landscape of electronics manufacturing.
Leave a Reply