Introduction to Capacitor Film
Capacitor film is a essential component in the manufacturing of capacitors, which are widely used in various electronic devices and systems. This article will delve into the properties, construction, and application of capacitor film to provide a comprehensive understanding of this crucial material.
What is Capacitor Film?
Capacitor film is a thin, flexible dielectric material used in the construction of capacitors. It serves as an insulating layer between the conductive plates of a capacitor, allowing the device to store electrical energy in an electric field. The properties of the capacitor film significantly influence the performance and characteristics of the resulting capacitor.
Properties of Capacitor Film
The following are the key properties of capacitor film that make it suitable for use in capacitors:
Dielectric Constant
The dielectric constant, also known as relative permittivity, is a measure of a material’s ability to store electrical energy in an electric field. Capacitor films with high dielectric constants allow for the construction of capacitors with higher capacitance values in a smaller physical size.
Material | Dielectric Constant |
---|---|
Polyester (PET) | 3.0 – 3.2 |
Polypropylene (PP) | 2.2 – 2.4 |
Polyphenylene Sulfide (PPS) | 3.0 – 3.5 |
Polyethylene Naphthalate (PEN) | 3.0 – 3.2 |
Dielectric Strength
Dielectric strength is the maximum electric field that a material can withstand before electrical breakdown occurs. Capacitor films with high dielectric strength can support higher voltage ratings, making them suitable for high-voltage applications.
Material | Dielectric Strength (kV/mm) |
---|---|
Polyester (PET) | 200 – 300 |
Polypropylene (PP) | 500 – 700 |
Polyphenylene Sulfide (PPS) | 400 – 500 |
Polyethylene Naphthalate (PEN) | 300 – 400 |
Dissipation Factor
The dissipation factor, or loss tangent, is a measure of the energy lost in a capacitor due to the dielectric material’s inherent resistance. Capacitor films with low dissipation factors are desirable for applications requiring high efficiency and low energy loss.
Material | Dissipation Factor |
---|---|
Polyester (PET) | 0.005 – 0.01 |
Polypropylene (PP) | 0.0002 – 0.0005 |
Polyphenylene Sulfide (PPS) | 0.003 – 0.005 |
Polyethylene Naphthalate (PEN) | 0.003 – 0.005 |
Temperature Stability
Temperature stability refers to a material’s ability to maintain its properties over a wide temperature range. Capacitor films with good temperature stability ensure that the capacitor’s performance remains consistent across various operating temperatures.
Material | Temperature Range (°C) |
---|---|
Polyester (PET) | -55 to +125 |
Polypropylene (PP) | -55 to +105 |
Polyphenylene Sulfide (PPS) | -55 to +150 |
Polyethylene Naphthalate (PEN) | -55 to +150 |
Construction of Capacitor Film
The construction of capacitor film involves several key steps:
Raw Material Selection
The first step in constructing capacitor film is selecting the appropriate raw material based on the desired properties and application requirements. Common materials used for capacitor films include polyester (PET), polypropylene (PP), polyphenylene sulfide (PPS), and polyethylene naphthalate (PEN).
Film Extrusion
The selected raw material is melted and extruded through a die to form a thin, continuous film. The extrusion process is carefully controlled to ensure uniform thickness and width of the resulting film.
Stretching and Orientation
After extrusion, the film undergoes a stretching process to improve its mechanical and electrical properties. The film is stretched in one or both directions (uniaxial or biaxial orientation) to align the polymer chains, resulting in enhanced strength and dielectric properties.
Heat Treatment
Following the stretching process, the film is subjected to a heat treatment to stabilize its structure and remove any residual stresses. This step ensures the film maintains its properties over its intended service life.
Metallization
In some cases, the capacitor film is metallized to create a conductive layer on one or both sides. This is typically done by vacuum deposition of a thin aluminum or zinc layer onto the film surface. Metallization allows for the construction of self-healing capacitors, where the metal layer can evaporate around a fault site, isolating the defect and preventing capacitor failure.
Slitting and Winding
The final step in capacitor film construction is slitting the film to the desired width and winding it onto cores or bobbins. The wound film is then ready for use in the assembly of various types of capacitors.
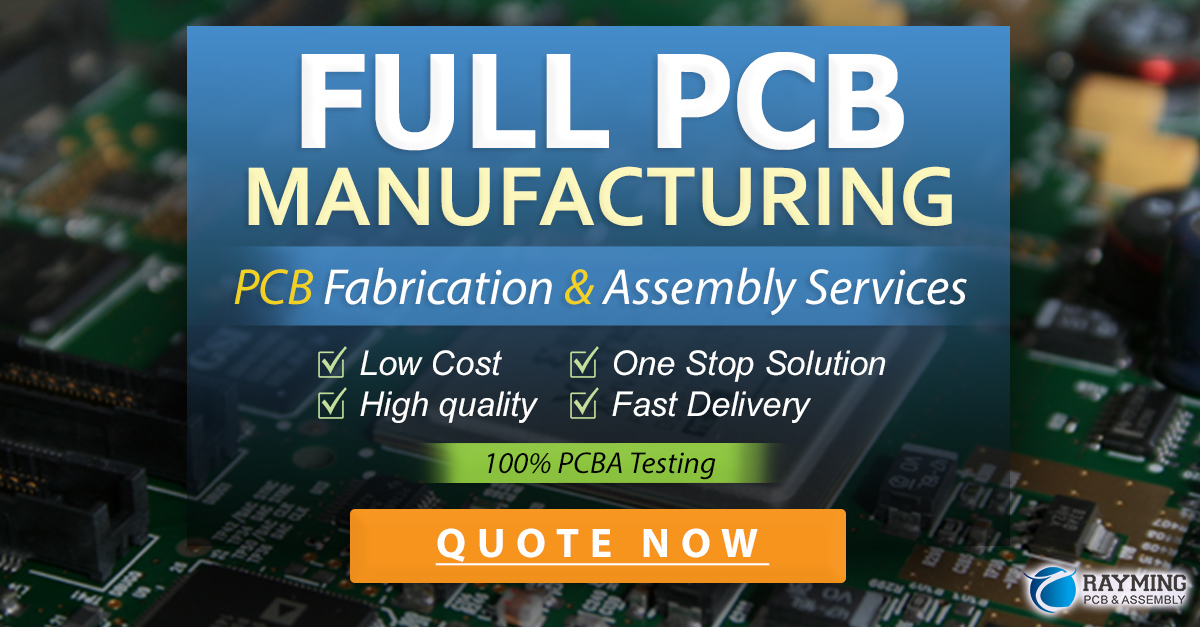
Application of Capacitor Film
Capacitor film finds application in a wide range of capacitor types and end-use industries:
Film Capacitors
Film capacitors are the most common application of capacitor film. These capacitors use a dielectric film, such as polyester or polypropylene, sandwiched between two conductive foils or metallized layers. Film capacitors offer high stability, low losses, and a wide range of capacitance values, making them suitable for various electronic applications.
Power Capacitors
Power capacitors are used in high-voltage and high-current applications, such as power factor correction, motor starting, and voltage stabilization. These capacitors often employ polypropylene or polyphenylene sulfide films due to their high dielectric strength and low dissipation factors.
Automotive Capacitors
Capacitor films are used in the construction of automotive capacitors, which must withstand harsh environmental conditions and temperature extremes. Polyester and polyphenylene sulfide films are commonly used in automotive capacitors due to their excellent temperature stability and mechanical strength.
Renewable Energy
In renewable energy applications, such as wind and solar power systems, capacitor films play a crucial role in power conditioning and energy storage. High-voltage, high-capacity film capacitors are used in DC-link and snubber circuits to ensure smooth and efficient power conversion.
Electronics Industry
Capacitor films are essential components in various electronic devices and systems, including consumer electronics, telecommunications equipment, and industrial control systems. The choice of capacitor film depends on the specific requirements of each application, such as voltage rating, capacitance value, and temperature range.
Frequently Asked Questions (FAQ)
1. What is the difference between a film capacitor and a ceramic capacitor?
Film capacitors use a flexible dielectric film, such as polyester or polypropylene, as the insulating layer between conductive plates. In contrast, ceramic capacitors use a rigid ceramic material as the dielectric. Film capacitors offer higher capacitance values, lower losses, and better temperature stability compared to ceramic capacitors, making them suitable for a wide range of applications.
2. Can capacitor films be recycled?
Yes, capacitor films can be recycled. Many manufacturers have implemented recycling programs to recover and reuse the valuable raw materials from end-of-life capacitors. Recycling capacitor films helps reduce environmental impact and conserve resources.
3. What is the self-healing property of metallized capacitor films?
Metallized capacitor films feature a thin metal layer deposited on one or both sides of the dielectric film. In the event of a localized dielectric breakdown, the metal layer around the fault site will vaporize, isolating the defect and preventing the capacitor from failing completely. This self-healing property enhances the reliability and lifetime of metallized film capacitors.
4. How does the choice of capacitor film affect the performance of a capacitor?
The choice of capacitor film significantly influences the performance and characteristics of the resulting capacitor. Factors such as dielectric constant, dielectric strength, dissipation factor, and temperature stability of the film determine the capacitor’s capacitance value, voltage rating, energy efficiency, and operating temperature range. Selecting the appropriate capacitor film based on the application requirements is crucial for optimal capacitor performance.
5. What are the advantages of using polypropylene film in power capacitors?
Polypropylene (PP) film offers several advantages for use in power capacitors. It has a high dielectric strength, allowing for higher voltage ratings, and a low dissipation factor, resulting in lower energy losses. PP film also exhibits excellent temperature stability, maintaining its properties over a wide temperature range. These characteristics make PP film an ideal choice for high-voltage, high-current applications such as power factor correction and motor starting.
Conclusion
Capacitor film is a crucial component in the construction of capacitors, playing a significant role in determining the performance and characteristics of these essential electronic devices. By understanding the properties, construction, and application of capacitor film, engineers and manufacturers can design and produce capacitors optimized for specific requirements across various industries. As technology continues to advance, the development of new and improved capacitor films will drive innovation in the field of capacitors and the broader electronics industry.
Leave a Reply