Introduction to Flex Board Manufacturing
Flexible printed circuit boards, also known as flex PCBs or simply flex boards, are revolutionizing electronic product design. Unlike traditional rigid PCBs, flex boards are made from thin, flexible materials that can bend and fold to fit into compact spaces and conform to three-dimensional shapes. This makes them ideal for applications requiring small, lightweight, or uniquely shaped circuit boards.
Flex board manufacturing is a complex process that involves specialized materials, equipment, and techniques to produce high-quality, reliable flexible circuits. In this comprehensive guide, we’ll delve into the details of flex board manufacturing, covering everything from the basic concepts and materials to the latest advancements and best practices in the industry.
The Advantages of Flex Boards
Flex boards offer numerous advantages over traditional rigid PCBs, making them increasingly popular in a wide range of industries and applications. Some of the key benefits of using flex boards include:
-
Space Savings: Flex boards can be bent, folded, and shaped to fit into tight spaces, allowing for more compact and streamlined product designs.
-
Weight Reduction: The thin, lightweight materials used in flex boards help reduce the overall weight of electronic devices, which is crucial for portable and mobile applications.
-
Increased Reliability: Flex boards eliminate the need for connectors and wires between separate rigid PCBs, reducing the number of potential failure points and improving overall system reliability.
-
Enhanced Durability: The flexible materials used in flex boards can withstand repeated bending and flexing without cracking or breaking, making them more durable than rigid PCBs in applications with frequent motion or vibration.
-
Improved Signal Integrity: Flex boards can be designed with shorter signal paths and controlled impedance, minimizing signal loss and interference for better overall performance.
These advantages make flex boards an attractive choice for applications such as wearable devices, medical implants, aerospace systems, automotive electronics, and more.
Flex Board Materials and Construction
The unique properties of flex boards are achieved through the use of specialized materials and construction techniques. The most common materials used in flex board manufacturing include:
-
Polyimide (PI): A high-performance polymer with excellent thermal stability, chemical resistance, and mechanical strength. PI is the most widely used substrate material for flex boards.
-
Polyester (PET): A low-cost alternative to PI, PET offers good flexibility and electrical properties but has lower temperature resistance and durability.
-
Copper: Thin copper foils are used for the conductive traces and pads on flex boards. The copper is typically electrodeposited (ED) or rolled annealed (RA) and comes in various thicknesses (typically 9-70 µm).
-
Adhesives: Specialized adhesives are used to bond the copper foil to the substrate material and to laminate multiple layers together. Common adhesives include acrylic, epoxy, and polyimide.
-
Coverlay: A thin, insulating layer that is laminated over the copper traces to protect them from damage and provide electrical insulation. Coverlay materials include polyimide, polyester, and solder mask.
The construction of a flex board typically involves the following layers:
Layer | Description |
---|---|
Coverlay | Insulating and protective layer |
Copper | Conductive traces and pads |
Adhesive | Bonding layer between copper and substrate |
Substrate | Flexible base material (PI or PET) |
Adhesive | Bonding layer for double-sided or multilayer designs |
Copper | Conductive traces and pads (for double-sided or multilayer designs) |
Coverlay | Insulating and protective layer (for double-sided designs) |
Flex boards can be single-sided (one copper layer), double-sided (two copper layers), or multilayer (three or more copper layers) depending on the complexity and density of the circuit design.
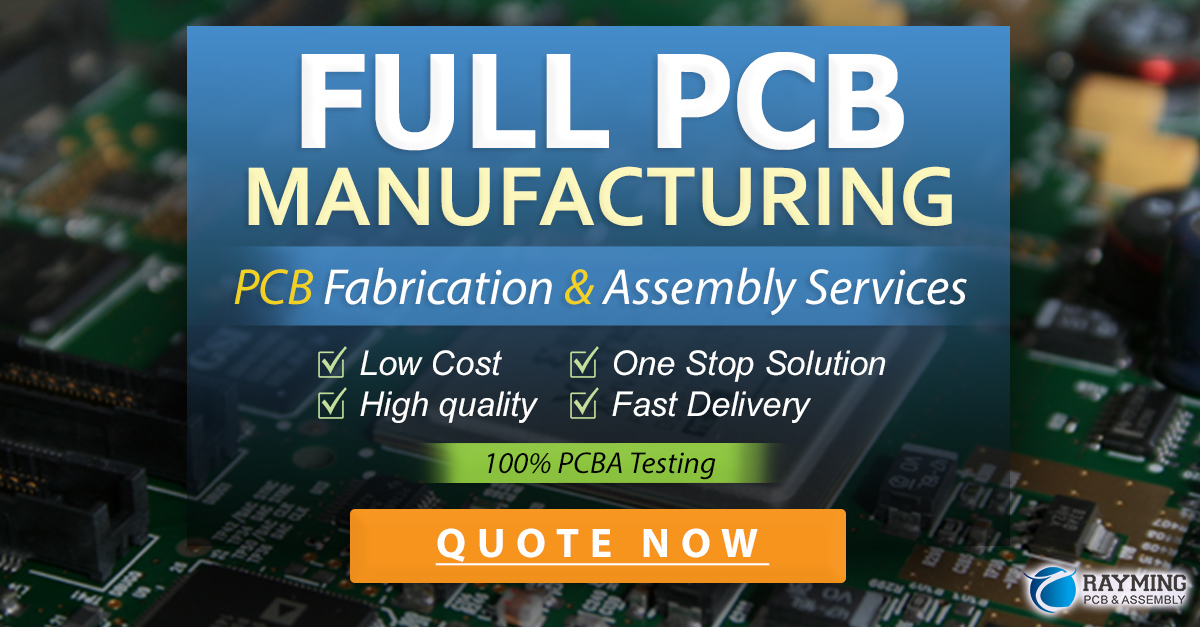
Flex Board Manufacturing Process
The flex board manufacturing process involves several key steps to convert the raw materials into a finished flexible circuit. While the exact process may vary depending on the specific design and requirements, the general steps include:
-
Circuit Design: The flex board design is created using specialized CAD software, taking into account the unique mechanical and electrical requirements of the application.
-
Artwork Generation: The CAD design is converted into a set of photomasks or artwork files that will be used to pattern the copper layers.
-
Material Selection and Preparation: The appropriate substrate, copper foil, adhesives, and coverlay materials are selected based on the design requirements. The materials are cut to size and cleaned to ensure optimal bonding and adhesion.
-
Lamination: The copper foil is laminated to the substrate material using heat and pressure to activate the adhesive and create a strong bond. For double-sided or multilayer designs, multiple layers are laminated together in a single step.
-
Drilling: If the design requires through-holes or vias, they are drilled through the laminated panel using mechanical or laser drilling methods.
-
Patterning: The copper layers are patterned using photolithography and etching processes. A photoresist is applied to the copper, exposed through the photomasks, and developed to create a protective pattern. The exposed copper is then etched away using chemical or plasma etching methods, leaving the desired circuit pattern.
-
Coverlay Application: The coverlay material is laminated over the patterned copper layers to provide insulation and protection. Openings in the coverlay are aligned with the pads and vias to allow for soldering and interconnections.
-
Surface Finishing: If required, additional surface finishes such as ENIG (electroless nickel immersion gold), HASL (hot air solder leveling), or OSP (organic solderability preservative) are applied to the exposed pads and vias to improve solderability and protect against oxidation.
-
Cutting and Forming: The flex board panel is cut into individual circuits using mechanical or laser cutting methods. If required, the circuits are then formed into their final 3D shapes using specialized forming tools and fixtures.
-
Testing and Inspection: The finished flex boards undergo a series of electrical and mechanical tests to ensure they meet the required specifications and performance standards. Visual and automated optical inspection (AOI) methods are used to check for defects and ensure the quality of the final product.
Throughout the manufacturing process, strict quality control measures are implemented to ensure the consistency, reliability, and performance of the flex boards. This includes regular equipment maintenance, material testing, in-process inspections, and final testing to catch any defects or issues before the boards are shipped to the customer.
Advanced Flex Board Technologies
As the demand for smaller, lighter, and more complex electronic devices continues to grow, flex board manufacturers are continuously innovating and developing new technologies to push the boundaries of what is possible with flexible circuits. Some of the latest advancements in flex board manufacturing include:
-
High Density Interconnect (HDI): HDI flex boards feature finer trace widths and spaces, smaller vias, and higher layer counts to achieve greater circuit density and functionality in a smaller footprint. HDI designs often incorporate microvias, blind vias, and buried vias to maximize the use of available space.
-
Rigid-Flex: Rigid-flex circuits combine the benefits of both rigid and flexible PCBs by incorporating rigid sections for component mounting and flexible sections for interconnections and bending. This allows for even greater design flexibility and eliminates the need for connectors between rigid boards.
-
Stretchable Electronics: Stretchable flex boards use specialized materials and design techniques to allow the circuits to stretch and conform to complex 3D shapes without losing functionality. This technology is particularly useful for wearable devices, soft robotics, and biomedical applications.
-
Printed Electronics: Printed electronics technology uses additive manufacturing methods such as screen printing, inkjet printing, and aerosol jet printing to deposit conductive inks directly onto flexible substrates. This allows for the creation of low-cost, customizable, and environmentally friendly flex boards for applications such as RFID tags, sensors, and displays.
-
Embedded Components: Flex boards can be designed with embedded passive components such as resistors and capacitors, as well as active components such as ICs and sensors. Embedding components directly into the flex board saves space, reduces assembly costs, and improves reliability by eliminating the need for surface-mounted components.
These advanced technologies are enabling new applications and design possibilities for flex boards in a wide range of industries, from consumer electronics and automotive to healthcare and aerospace.
Flex Board Design Best Practices
Designing a successful flex board requires careful consideration of the unique mechanical and electrical properties of flexible circuits. Some key best practices for flex board design include:
-
Consider the Bend Radius: The minimum bend radius of a flex board depends on the substrate material, copper thickness, and number of layers. Designers should ensure that the bend radius is within the acceptable range to avoid damaging the circuit or compromising its reliability.
-
Use Strain Relief: Incorporate strain relief features such as curves, loops, or accordion folds into the design to minimize stress on the copper traces during bending and flexing.
-
Avoid Tight Tolerances: Flex boards have larger manufacturing tolerances compared to rigid PCBs due to the nature of the flexible materials. Designers should avoid overly tight tolerances and allow for adequate spacing between features to ensure manufacturability and reliability.
-
Consider Panelization: Panelizing multiple flex boards onto a single panel can help optimize material usage, reduce costs, and improve manufacturing efficiency. However, panelization should be carefully planned to ensure adequate spacing and support for each individual circuit.
-
Minimize Layer Count: While multilayer flex boards offer greater circuit density, they also increase the thickness and reduce the flexibility of the circuit. Designers should aim to minimize the number of layers and use creative layout techniques to maximize the use of available space.
-
Plan for Assembly: Consider the assembly process when designing the flex board, including the placement of components, the orientation of the circuit, and the use of stiffeners or reinforcements in areas subjected to high stress or frequent handling.
-
Collaborate with the Manufacturer: Work closely with the flex board manufacturer throughout the design process to ensure that the design is optimized for manufacturability, reliability, and cost-effectiveness. The manufacturer can provide valuable feedback and suggestions based on their experience and expertise.
By following these best practices and leveraging the latest technologies and manufacturing techniques, designers can create high-quality, reliable flex boards that meet the unique requirements of their applications.
FAQ
1. What are the key advantages of using flex boards over traditional rigid PCBs?
Flex boards offer several advantages over rigid PCBs, including space savings, weight reduction, increased reliability, enhanced durability, and improved signal integrity. They can be bent, folded, and shaped to fit into compact spaces and withstand repeated flexing without damage.
2. What materials are commonly used in flex board manufacturing?
The most common materials used in flex board manufacturing include polyimide (PI) and polyester (PET) for the substrate, copper foil for the conductive traces and pads, specialized adhesives for bonding the layers together, and coverlay materials such as polyimide, polyester, or solder mask for insulation and protection.
3. What are the different types of flex boards available?
Flex boards can be single-sided (one copper layer), double-sided (two copper layers), or multilayer (three or more copper layers) depending on the complexity and density of the circuit design. They can also be combined with rigid sections to create rigid-flex circuits for even greater design flexibility.
4. What industries and applications commonly use flex boards?
Flex boards are used in a wide range of industries and applications, including consumer electronics, medical devices, automotive electronics, aerospace systems, industrial equipment, and telecommunications. They are particularly well-suited for applications requiring small, lightweight, or uniquely shaped circuit boards that can withstand repeated bending and flexing.
5. How can I ensure the reliability and manufacturability of my flex board design?
To ensure the reliability and manufacturability of your flex board design, consider key factors such as the bend radius, strain relief, manufacturing tolerances, panelization, layer count, and assembly requirements. Collaborate closely with your flex board manufacturer throughout the design process to optimize your design for cost-effectiveness, reliability, and ease of manufacturing.
Conclusion
Flex board manufacturing is a complex and constantly evolving field that offers unique advantages and challenges compared to traditional rigid PCB manufacturing. By understanding the materials, processes, and best practices involved in flex board manufacturing, designers can create high-quality, reliable flexible circuits that meet the demands of today’s increasingly complex and compact electronic devices.
From the basic concepts and materials to the latest advancements and design techniques, this comprehensive guide has covered the essential aspects of flex board manufacturing. As the industry continues to innovate and push the boundaries of what is possible with flexible electronics, it is crucial for designers and manufacturers to stay up-to-date with the latest technologies and best practices.
By leveraging the advantages of flex boards and collaborating closely with experienced manufacturers, designers can unlock new possibilities for their products and stay ahead of the curve in an ever-changing market. With the right knowledge, tools, and partnerships, the potential applications and benefits of flex boards are virtually limitless.
Leave a Reply