What is PCA Electronics?
PCA (Printed Circuit Assembly) Electronics refers to the process of assembling various electronic components onto a printed circuit board (PCB) to create a functional electronic device. The PCB is a flat board made of insulating material, such as fiberglass or plastic, with conductive pathways etched or printed onto its surface. These pathways connect the electronic components, allowing them to communicate and function together as a complete system.
PCA Electronics has revolutionized the electronics industry by enabling the mass production of complex electronic devices in a compact and efficient manner. This technology is used in a wide range of applications, from consumer electronics like smartphones and laptops to industrial equipment, medical devices, and aerospace systems.
The PCA Electronics Assembly Process
The PCA Electronics assembly process involves several key steps, each of which plays a crucial role in ensuring the quality and functionality of the final product. These steps include:
- PCB Design and Fabrication
- Component Selection and Procurement
- Solder Paste Application
- Component Placement
- Reflow Soldering
- Inspection and Testing
- Conformal Coating and Potting (optional)
PCB Design and Fabrication
The first step in the PCA Electronics process is designing the PCB layout using specialized software. The design must take into account factors such as component placement, signal integrity, power distribution, and thermal management. Once the design is finalized, the PCB is fabricated using a variety of methods, such as etching, drilling, and plating.
Component Selection and Procurement
The next step is to select and procure the electronic components that will be assembled onto the PCB. This involves sourcing components from various suppliers, ensuring they meet the required specifications, and managing inventory to ensure a steady supply for production.
Solder Paste Application
Before the components are placed on the PCB, a thin layer of solder paste is applied to the pads where the components will be soldered. This is typically done using a stencil printing process, which ensures a precise and uniform application of the solder paste.
Component Placement
Once the solder paste is applied, the electronic components are placed onto the PCB using automated pick-and-place machines. These machines use computer vision and robotic arms to quickly and accurately place components onto the board.
Reflow Soldering
After the components are placed, the PCB undergoes a reflow soldering process. The board is heated in a reflow oven, causing the solder paste to melt and form a strong electrical and mechanical bond between the components and the PCB.
Inspection and Testing
Once the soldering process is complete, the PCB undergoes various inspection and testing procedures to ensure its quality and functionality. This may include automated optical inspection (AOI), X-ray inspection, in-circuit testing (ICT), and functional testing.
Conformal Coating and Potting (optional)
In some cases, additional protection may be required for the PCB and its components. Conformal coating involves applying a thin layer of a protective material over the PCB to protect it from moisture, dust, and other environmental factors. Potting involves encapsulating the PCB and components in a solid material, such as epoxy or silicone, to provide additional mechanical protection and thermal insulation.
Advantages of PCA Electronics
PCA Electronics offers several key advantages over traditional through-hole assembly methods:
-
Miniaturization: PCA allows for the use of smaller components and tighter spacing between them, enabling the creation of more compact and lightweight electronic devices.
-
Increased Reliability: The automated assembly process and use of surface mount components results in fewer assembly errors and higher reliability compared to manual through-hole assembly.
-
Faster Production: Automated pick-and-place machines and reflow soldering processes enable much faster assembly times, allowing for higher production volumes and shorter lead times.
-
Lower Costs: The increased efficiency and automation of the PCA process results in lower labor costs and reduced material waste, ultimately leading to lower overall production costs.
-
Improved Signal Integrity: The shorter lead lengths and closer component spacing in PCA designs help to minimize signal distortion and interference, resulting in better overall performance.
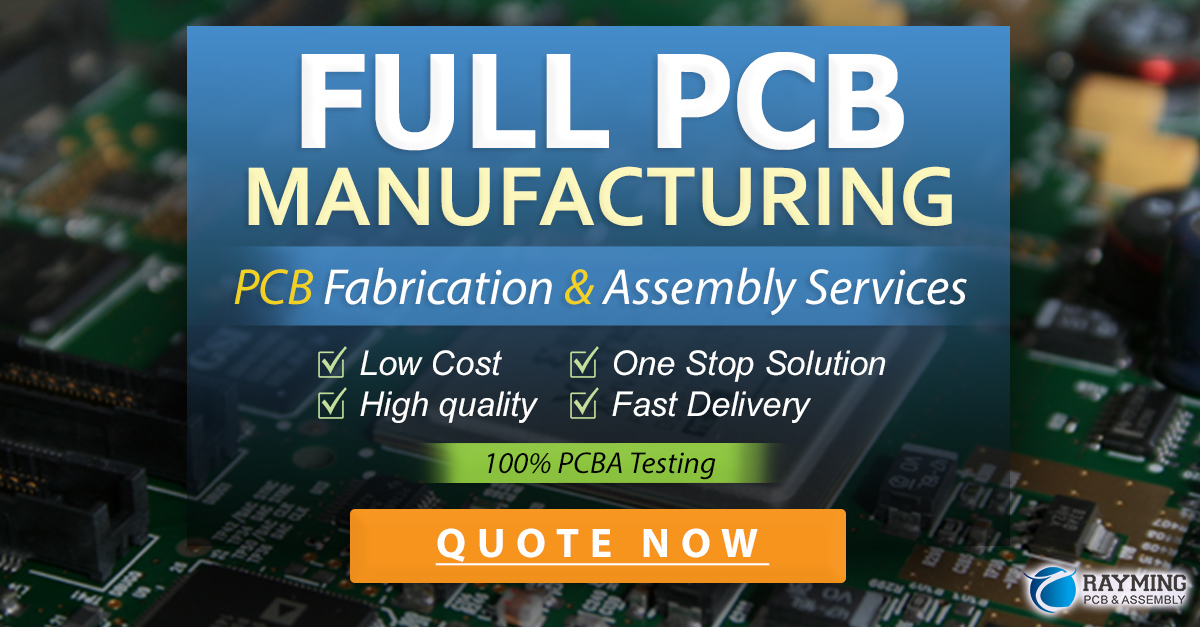
PCA Electronics Applications
PCA Electronics is used in a wide range of industries and applications, including:
-
Consumer Electronics: Smartphones, tablets, laptops, wearables, and home appliances.
-
Automotive: Engine control units, infotainment systems, sensors, and driver assistance systems.
-
Industrial: Process control systems, automation equipment, and power electronics.
-
Medical: Diagnostic equipment, monitoring devices, and implantable devices.
-
Aerospace and Defense: Avionics, communication systems, and military equipment.
-
IoT and Embedded Systems: Smart home devices, wireless sensors, and low-power embedded controllers.
PCA Electronics Design Considerations
When designing a PCB for PCA Electronics, there are several key factors to consider:
-
Component Selection: Choose components that are compatible with the PCA process and meet the necessary performance, reliability, and cost requirements.
-
PCB Layout: Design the PCB layout to optimize signal integrity, power distribution, and thermal management, while minimizing the board size and complexity.
-
Manufacturing Constraints: Consider the capabilities and limitations of the manufacturing process, such as minimum feature sizes, aspect ratios, and tolerances.
-
Assembly Process: Design the PCB and select components to facilitate the automated assembly process, such as using standard component packages and providing adequate clearance for pick-and-place machines.
-
Testing and Inspection: Incorporate design features that enable effective testing and inspection, such as test points, fiducial markers, and clear labeling.
-
Environmental Factors: Consider the operating environment of the final product and design the PCB and select components accordingly, such as using conformal coating or potting for protection against moisture and vibration.
Troubleshooting PCA Electronics
Despite the high reliability of PCA Electronics, issues can sometimes arise during the assembly process or in the final product. Common problems and their potential causes include:
-
Solder Bridges: Caused by excessive solder paste application, improper component placement, or incorrect reflow profile.
-
Tombstoning: When a component stands up on one end due to uneven heating or solder paste application.
-
Component Shift: Caused by insufficient solder paste, improper placement, or vibration during the reflow process.
-
Poor Solder Joints: Resulting from insufficient solder paste, incorrect reflow profile, or contamination of the PCB or components.
-
Electrostatic Discharge (ESD) Damage: Caused by improper handling of sensitive components during assembly or testing.
When troubleshooting PCA Electronics issues, it is important to systematically analyze the problem, identify the root cause, and implement appropriate corrective actions. This may involve adjusting the assembly process parameters, improving ESD protection measures, or modifying the PCB design or component selection.
Future Trends in PCA Electronics
As technology continues to advance, PCA Electronics is evolving to keep pace with new demands and opportunities. Some of the key trends shaping the future of PCA include:
-
Miniaturization: The ongoing trend towards smaller, more compact electronic devices is driving the development of advanced packaging technologies, such as 3D integrated circuits and wafer-level packaging.
-
High-Speed Interfaces: The increasing demand for faster data transfer rates is leading to the adoption of high-speed interfaces, such as USB 4, PCI Express 5.0, and Thunderbolt 4, which require careful PCB design and signal integrity management.
-
Flexible and Stretchable Electronics: The development of flexible and stretchable PCBs and components is enabling new applications in wearable devices, medical implants, and soft robotics.
-
Additive Manufacturing: 3D printing technologies are being adapted for PCB fabrication and assembly, potentially enabling faster prototyping, customization, and on-demand production.
-
Sustainable Electronics: There is a growing emphasis on developing environmentally friendly and sustainable PCA practices, such as using recycled materials, reducing waste, and designing for ease of disassembly and recycling.
As PCA Electronics continues to evolve, designers and manufacturers must stay informed about the latest technologies, best practices, and industry standards to ensure the creation of high-quality, reliable, and innovative electronic products.
FAQ
1. What is the difference between PCA and PCBA?
PCA (Printed Circuit Assembly) and PCBA (Printed Circuit Board Assembly) are often used interchangeably, as they both refer to the process of assembling electronic components onto a printed circuit board. However, some professionals make a distinction between the two terms:
- PCA refers specifically to the assembled board, including the PCB and the components mounted on it.
- PCBA refers to the complete process of assembling the board, from the bare PCB to the finished product, including soldering, inspection, and testing.
2. What is the difference between surface mount and through-hole components?
Surface mount components are designed to be mounted directly onto the surface of a PCB, with their leads soldered to pads on the board. Through-hole components, on the other hand, have long leads that are inserted through holes in the PCB and soldered on the opposite side.
Surface mount components are generally smaller, faster to assemble, and more suitable for high-density designs, while through-hole components are often used for larger, higher-power components or in applications where mechanical strength is a priority.
3. What is the purpose of solder paste in the PCA process?
Solder paste is a mixture of tiny solder particles suspended in a flux medium. It is applied to the pads on a PCB prior to component placement, and serves several important functions:
- It holds the components in place during the assembly process.
- It provides a conductive path for the solder to flow and form a strong mechanical and electrical bond between the component leads and the PCB pads.
- The flux in the solder paste helps to remove oxides and other contaminants from the surfaces to be soldered, ensuring a clean and reliable solder joint.
4. What is the difference between reflow soldering and wave soldering?
Reflow soldering and wave soldering are two common methods used to solder components onto a PCB in the PCA process:
-
Reflow soldering is typically used for surface mount components. The solder paste is applied to the PCB pads, the components are placed, and then the entire board is heated in a reflow oven, causing the solder to melt and form a bond between the components and the board.
-
Wave soldering is primarily used for through-hole components. The PCB, with the components already inserted, is passed over a molten solder wave, which selectively solders the component leads to the PCB.
Reflow soldering is generally faster, more precise, and better suited for high-density designs, while wave soldering is often used for larger, heavier components or in mixed-technology assemblies that include both surface mount and through-hole components.
5. What are some common defects that can occur in PCA, and how can they be prevented?
Some common defects that can occur in the PCA process include:
-
Solder bridges: Unintended connections between adjacent solder joints, caused by excessive solder or improper component placement. These can be prevented by optimizing the solder paste application, ensuring proper component placement, and using a well-designed reflow profile.
-
Tombstoning: When a component stands up on one end due to uneven heating or solder paste application. This can be prevented by ensuring even heating during reflow, using a balanced pad design, and optimizing the solder paste volume.
-
Component shift: When components move out of position during the reflow process, caused by insufficient solder paste, improper placement, or vibration. This can be prevented by using appropriate solder paste volume, ensuring accurate component placement, and minimizing vibration during reflow.
-
Poor solder joints: Weak or unreliable solder connections, resulting from insufficient solder, incorrect reflow profile, or contamination. These can be prevented by using the correct solder paste volume, optimizing the reflow profile, and maintaining a clean assembly environment.
To minimize defects, it is important to follow best practices in PCB design, component selection, and assembly process control, as well as to implement robust inspection and testing procedures to identify and correct any issues that may arise.
Summary
PCA Electronics has revolutionized the electronics industry, enabling the mass production of complex, high-density electronic assemblies in a fast, efficient, and cost-effective manner. The PCA process involves several key steps, including PCB design and fabrication, component selection and procurement, solder paste application, component placement, reflow soldering, inspection, and testing.
PCA offers numerous advantages over traditional through-hole assembly, such as miniaturization, increased reliability, faster production, lower costs, and improved signal integrity. As a result, PCA is used in a wide range of industries and applications, from consumer electronics and automotive systems to medical devices and aerospace equipment.
Designing for PCA involves careful consideration of factors such as component selection, PCB layout, manufacturing constraints, assembly process requirements, testing and inspection needs, and environmental factors. When issues arise in PCA, systematic troubleshooting is necessary to identify the root cause and implement appropriate corrective actions.
Looking to the future, PCA Electronics continues to evolve, with trends such as miniaturization, high-speed interfaces, flexible and stretchable electronics, additive manufacturing, and sustainable practices shaping the development of new technologies and processes.
By understanding the principles, advantages, and best practices of PCA Electronics, designers and manufacturers can create high-quality, reliable, and innovative electronic products that meet the ever-increasing demands of the modern world.
PCA Process Step | Key Considerations |
---|---|
PCB Design and Fabrication | – Signal integrity – Power distribution – Thermal management – Manufacturability |
Component Selection and Procurement | – PCA compatibility – Performance – Reliability – Cost |
Solder Paste Application | – Stencil design – Paste volume – Paste properties |
Component Placement | – Pick-and-place machine capabilities – Component orientation – Placement accuracy |
Reflow Soldering | – Reflow profile – Oven settings – Solder joint quality |
Inspection and Testing | – Automated optical inspection (AOI) – X-ray inspection – In-circuit testing (ICT) – Functional testing |
Conformal Coating and Potting (optional) | – Environmental protection – Mechanical protection – Thermal insulation |
Leave a Reply