What is a Stepper Motor?
A stepper motor is a brushless DC electric motor that divides a full rotation into a number of equal steps. It moves in discrete increments, or steps, rather than rotating continuously like a conventional DC motor. The motor’s position can be precisely controlled without any feedback mechanism, as long as the motor is carefully sized to the application in respect to torque and speed.
Working Principle of Stepper Motors
Stepper motors operate on the principle of electromagnetism. They consist of a rotor (the rotating part) and a stator (the stationary part). The stator has multiple windings that can be energized in a specific sequence to create a rotating magnetic field. The rotor, which is a permanent magnet or a ferromagnetic core with salient poles, aligns itself with the magnetic field generated by the stator windings. By energizing the stator windings in a particular order, the motor can be made to rotate in precise increments.
There are three main types of stepper motors:
-
Variable Reluctance (VR) Stepper Motors: These motors have a plain iron rotor with salient poles and a wound stator. They operate based on the principle of variable reluctance, where the rotor moves to minimize the reluctance between the rotor teeth and the energized stator poles.
-
Permanent Magnet (PM) Stepper Motors: PM stepper motors have a permanent magnet rotor and a wound stator. The rotor aligns itself with the magnetic field generated by the energized stator windings, causing the motor to rotate in steps.
-
Hybrid Stepper Motors: Hybrid stepper motors combine the features of both VR and PM stepper motors. They have a rotor with multiple teeth and a permanent magnet, along with a toothed stator. Hybrid stepper motors offer higher torque and resolution compared to VR and PM stepper motors.
Advantages of Stepper Motors
-
Precise Positioning: Stepper motors provide excellent positional accuracy and repeatability. They can achieve precise movements without the need for an external feedback mechanism.
-
High Torque at Low Speeds: Stepper motors offer high holding torque at low speeds, making them suitable for applications that require precise positioning and high load-carrying capacity.
-
Open-Loop Control: Stepper motors can be controlled in an open-loop system, eliminating the need for expensive feedback devices like encoders or resolvers.
-
Low Speed Operation: Stepper motors can operate at very low speeds without the need for gears or speed reducers.
-
Full Torque at Standstill: Stepper motors provide full torque even when stationary, making them ideal for holding positions.
Disadvantages of Stepper Motors
-
Limited Speed Range: Stepper motors have a limited speed range compared to DC motors. They tend to lose torque at higher speeds.
-
Resonance and Vibration: Stepper motors can exhibit resonance and vibration at certain step rates, which can affect the motor’s performance and cause positioning errors.
-
Power Consumption: Stepper motors consume power even when holding a position, which can lead to increased power consumption compared to DC motors.
-
Complex Drive Circuitry: Stepper motors require complex drive circuitry to control the sequence and timing of the stator windings’ energization.
Applications of Stepper Motors
Stepper motors find applications in various fields where precise positioning and control are required, such as:
- 3D printers and CNC machines
- Robotics and automation systems
- Positioning systems in cameras and telescopes
- Medical equipment like insulin pumps and drug delivery systems
- Automotive applications like gauges, meters, and valve control
Characteristic | Stepper Motor |
---|---|
Working Principle | Electromagnetism, discrete steps |
Rotor Types | Variable reluctance, permanent magnet, hybrid |
Positional Accuracy | High |
Torque at Low Speeds | High |
Control Method | Open-loop |
Speed Range | Limited |
Resonance and Vibration | Can occur at certain step rates |
Power Consumption | Consumes power even when holding position |
Drive Circuitry | Complex |
What is a DC Motor?
A DC motor, short for direct current motor, is an electric motor that converts electrical energy into mechanical energy through the interaction of magnetic fields and current-carrying conductors. DC motors are one of the most widely used types of motors due to their simplicity, reliability, and cost-effectiveness.
Working Principle of DC Motors
DC motors operate on the principle of Lorentz force, which states that a current-carrying conductor placed in a magnetic field experiences a force perpendicular to both the current and the magnetic field. In a DC motor, the stator generates a stationary magnetic field, while the rotor (armature) carries the current. The interaction between the magnetic field and the current-carrying rotor windings creates a torque that causes the rotor to rotate.
The basic components of a DC motor include:
-
Stator: The stationary part of the motor that generates the magnetic field. It consists of permanent magnets or electromagnets.
-
Rotor (Armature): The rotating part of the motor that carries the current. It consists of windings wound around a ferromagnetic core.
-
Commutator: A mechanical switch that reverses the current direction in the rotor windings as the rotor rotates, ensuring continuous rotation.
-
Brushes: Conductive components that press against the commutator, providing electrical contact between the external circuit and the rotor windings.
Types of DC Motors
There are several types of DC motors, each with its own characteristics and applications:
-
Brushed DC Motors: These motors have a mechanical commutator and brushes to control the current flow in the rotor windings. They are simple, low-cost, and easy to control.
-
Brushless DC (BLDC) Motors: BLDC motors use electronic commutation instead of brushes and a mechanical commutator. They offer higher efficiency, longer lifespan, and reduced maintenance compared to brushed DC motors.
-
Permanent Magnet DC (PMDC) Motors: PMDC motors have permanent magnets in the stator and a wound rotor. They provide high starting torque and good speed regulation.
-
Separately Excited DC Motors: In these motors, the stator and rotor windings are energized by separate power sources, allowing for independent control of the magnetic field and the rotor current.
-
Series DC Motors: In series DC motors, the stator and rotor windings are connected in series. They offer high starting torque but poor speed regulation.
-
Shunt DC Motors: In shunt DC motors, the stator and rotor windings are connected in parallel. They provide good speed regulation but lower starting torque compared to series DC motors.
Advantages of DC Motors
-
Simple Control: DC motors can be easily controlled using simple voltage or current regulation techniques.
-
High Starting Torque: DC motors, especially series DC motors, offer high starting torque, making them suitable for applications that require heavy loads to be started from rest.
-
Wide Speed Range: DC motors can operate over a wide range of speeds by varying the supply voltage or using speed control techniques like pulse-width modulation (PWM).
-
Compact Size: DC motors are available in compact sizes, making them suitable for applications with space constraints.
-
Low Cost: DC motors, particularly brushed DC motors, are relatively inexpensive compared to other types of motors.
Disadvantages of DC Motors
-
Maintenance: Brushed DC motors require regular maintenance due to the wear and tear of brushes and the commutator.
-
Sparking and EMI: The commutation process in brushed DC motors can cause sparking and generate electromagnetic interference (EMI).
-
Limited Lifespan: The lifespan of brushed DC motors is limited by the wear of brushes and the commutator.
-
Lower Efficiency: DC motors, especially brushed DC motors, have lower efficiency compared to AC motors due to the losses associated with the commutation process.
Applications of DC Motors
DC motors find applications in a wide range of industries and products, such as:
- Automotive systems like power windows, seats, and windshield wipers
- Robotics and automation equipment
- Power tools and machinery
- Toys and hobby projects
- Pumps, fans, and blowers
- Aerospace and defense systems
Characteristic | DC Motor |
---|---|
Working Principle | Lorentz force |
Rotor Types | Wound rotor (armature) |
Commutation | Mechanical (brushed) or electronic (brushless) |
Control Method | Simple voltage or current regulation |
Starting Torque | High (especially in series DC motors) |
Speed Range | Wide |
Efficiency | Lower (especially in brushed DC motors) |
Maintenance | Required for brushed DC motors |
Lifespan | Limited by brush and commutator wear (brushed DC motors) |
Key Differences between Stepper Motors and DC Motors
Now that we have explored the characteristics, advantages, and disadvantages of stepper motors and DC motors, let’s summarize the key differences between them:
-
Working Principle: Stepper motors operate on the principle of electromagnetism and move in discrete steps, while DC motors operate on the principle of Lorentz force and provide continuous rotation.
-
Control Method: Stepper motors are typically controlled in an open-loop system, while DC motors can be controlled using simple voltage or current regulation techniques.
-
Positional Accuracy: Stepper motors offer high positional accuracy and repeatability, while DC motors require external feedback mechanisms for precise positioning.
-
Torque Characteristics: Stepper motors provide high holding torque at low speeds, while DC motors offer high starting torque (especially series DC motors).
-
Speed Range: Stepper motors have a limited speed range and tend to lose torque at higher speeds, while DC motors can operate over a wide range of speeds.
-
Power Consumption: Stepper motors consume power even when holding a position, while DC motors consume power only when rotating.
-
Resonance and Vibration: Stepper motors can exhibit resonance and vibration at certain step rates, while DC motors generally do not suffer from these issues.
-
Drive Circuitry: Stepper motors require complex drive circuitry to control the sequence and timing of the stator windings’ energization, while DC motors can be driven using simpler circuitry.
-
Maintenance: Brushed DC motors require regular maintenance due to brush and commutator wear, while stepper motors and brushless DC motors have lower maintenance requirements.
-
Cost: Stepper motors and brushless DC motors are generally more expensive than brushed DC motors.
Characteristic | Stepper Motor | DC Motor |
---|---|---|
Working Principle | Electromagnetism, discrete steps | Lorentz force, continuous rotation |
Control Method | Open-loop | Simple voltage or current regulation |
Positional Accuracy | High | Requires external feedback for precision |
Torque Characteristics | High holding torque at low speeds | High starting torque (series DC) |
Speed Range | Limited | Wide |
Power Consumption | Consumes power when holding position | Consumes power only when rotating |
Resonance and Vibration | Can occur at certain step rates | Generally not an issue |
Drive Circuitry | Complex | Simpler |
Maintenance | Lower (no brushes) | Required for brushed DC motors |
Cost | Higher | Lower (brushed DC) |
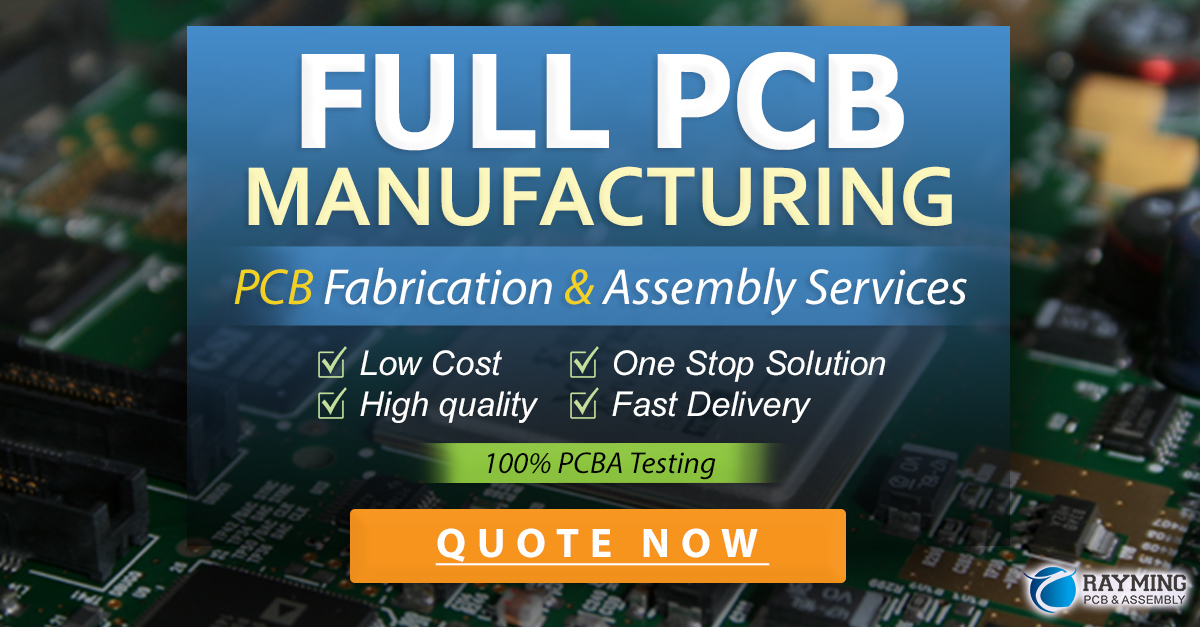
Choosing Between Stepper Motors and DC Motors
When deciding between a stepper motor and a DC motor for a particular application, consider the following factors:
-
Positional Accuracy: If your application requires precise positioning and repeatability, a stepper motor may be the better choice.
-
Torque Requirements: If your application demands high holding torque at low speeds, a stepper motor is suitable. If high starting torque is needed, a series DC motor may be preferred.
-
Speed Range: If your application requires a wide range of operating speeds, a DC motor is generally more suitable than a stepper motor.
-
Power Consumption: If power efficiency is a critical factor, a DC motor may be more appropriate, as it consumes power only when rotating.
-
Vibration and Noise: If smooth operation with minimal vibration and noise is desired, a DC motor or a microstepping stepper motor may be the better choice.
-
Maintenance: If low maintenance is a priority, a stepper motor or a brushless DC motor is preferable over a brushed DC motor.
-
Cost: If cost is a primary concern, a brushed DC motor may be the most economical option.
Ultimately, the choice between a stepper motor and a DC motor depends on the specific requirements of your application. Consider the trade-offs between precision, torque, speed, power consumption, maintenance, and cost to make an informed decision.
Frequently Asked Questions (FAQ)
-
Can stepper motors be used in closed-loop control systems?
Yes, stepper motors can be used in closed-loop control systems by incorporating position feedback devices like encoders or resolvers. This allows for more precise position control and error compensation. -
Are brushless DC motors better than brushed DC motors?
Brushless DC motors offer several advantages over brushed DC motors, including higher efficiency, longer lifespan, reduced maintenance, and better heat dissipation. However, they are generally more expensive and require more complex drive circuitry. -
How do I control the speed of a stepper motor?
The speed of a stepper motor can be controlled by varying the frequency of the step pulses sent to the motor driver. Higher frequencies result in faster rotation, while lower frequencies lead to slower rotation. -
Can DC motors be used for precise positioning applications?
Yes, DC motors can be used for precise positioning applications when combined with position feedback devices like encoders or potentiometers. Closed-loop control techniques can be employed to achieve accurate positioning. -
What is microstepping in stepper motors?
Microstepping is a technique used to increase the resolution and smoothness of stepper motor motion. It involves dividing each full step into smaller increments by precisely controlling the current in the stator windings. Microstepping helps reduce vibration and improve positional accuracy.
In conclusion, stepper motors and DC motors are two distinct types of electric motors with their own unique characteristics, advantages, and disadvantages. Stepper motors excel in applications requiring precise positioning and high holding torque at low speeds, while DC motors are suitable for a wide range of applications that demand high starting torque, wide speed range, and simple control. By understanding the differences between these two motor types and considering the specific requirements of your application, you can make an informed decision when choosing between a stepper motor and a DC motor.
Leave a Reply