What is Thermal Adhesive?
Thermal adhesive is a specialized bonding material designed to provide both adhesion and thermal conductivity between electronic components and heat sinks or other heat dissipation devices. These adhesives are formulated to offer excellent thermal conductivity, allowing heat to be efficiently transferred from the heat-generating component to the heat sink, where it can be dissipated into the surrounding environment.
Composition of Thermal Adhesives
Thermal adhesives are typically composed of a polymer matrix filled with thermally conductive particles or fillers. The polymer matrix provides the adhesive properties, while the fillers enhance the thermal conductivity. Common fillers used in thermal adhesives include:
- Aluminum oxide
- Boron nitride
- Aluminum nitride
- Silver
- Graphite
- Diamond
The choice of filler material depends on the specific requirements of the application, such as the desired thermal conductivity, electrical conductivity, and cost considerations.
Properties of Thermal Adhesives
Thermal adhesives exhibit several key properties that make them suitable for use in electronic assemblies:
-
Thermal Conductivity: The primary function of thermal adhesives is to efficiently transfer heat. The thermal conductivity of these adhesives can range from a few watts per meter-kelvin (W/mK) to over 10 W/mK, depending on the filler material and loading.
-
Adhesion Strength: Thermal adhesives must provide a strong and reliable bond between the electronic component and the heat sink. The adhesion strength is influenced by factors such as surface preparation, curing conditions, and the compatibility of the adhesive with the substrate materials.
-
Electrical Insulation: In many applications, thermal adhesives need to provide electrical insulation to prevent short circuits or interference. Some thermal adhesives are formulated with electrically insulating fillers to achieve this property.
-
Cure Mechanism: Thermal adhesives can be classified based on their cure mechanism, which can be room temperature vulcanizing (RTV), heat-cured, or UV-cured. The choice of cure mechanism depends on the application requirements and manufacturing process.
-
Operating Temperature Range: Thermal adhesives must maintain their properties over the expected operating temperature range of the electronic device. Some adhesives are designed for high-temperature applications, while others are suitable for cryogenic environments.
Applications of Thermal Adhesive in Electronics
Thermal adhesives find use in a wide range of electronic applications, from consumer devices to industrial equipment. Some common applications include:
Power Electronics
In power electronic devices, such as switched-mode power supplies, motor drives, and inverters, thermal adhesives are used to attach power semiconductor devices (e.g., MOSFETs, IGBTs) to heat sinks. The adhesive provides a low thermal resistance path for heat dissipation, ensuring the devices operate within their safe temperature limits.
LED Lighting
High-power LED packages generate significant amounts of heat that must be effectively dissipated to maintain light output and reliability. Thermal adhesives are used to bond LED packages to metal core printed circuit boards (MCPCBs) or heat sinks, facilitating efficient heat transfer and extending the lifespan of the LEDs.
Automotive Electronics
The harsh operating environment in automotive applications, characterized by high temperatures, vibrations, and exposure to moisture and chemicals, demands robust thermal management solutions. Thermal adhesives are employed to bond electronic control units (ECUs), sensors, and power modules to heat sinks or chassis, ensuring reliable operation under these challenging conditions.
Telecommunications Equipment
In telecommunications equipment, such as base stations and routers, thermal adhesives are used to attach high-power radio frequency (RF) components, like power amplifiers, to heat sinks. The adhesive helps maintain stable operating temperatures, preventing performance degradation and ensuring signal integrity.
Applying Thermal Adhesive
Proper application of thermal adhesive is critical for achieving optimal performance and reliability. The following steps outline the general process for applying thermal adhesive:
-
Surface Preparation: Clean and degrease the surfaces of the electronic component and heat sink to remove any contaminants that may interfere with adhesion. If necessary, roughen the surfaces to improve adhesion.
-
Adhesive Dispensing: Apply the thermal adhesive to the mating surfaces using a dispensing system, such as a syringe, automated dispenser, or screen printing. Ensure an even and controlled application to achieve the desired bond line thickness.
-
Component Placement: Carefully place the electronic component onto the heat sink, ensuring proper alignment and avoiding air entrapment. Apply pressure to achieve good contact between the surfaces.
-
Curing: Allow the thermal adhesive to cure according to the manufacturer’s recommendations. This may involve room temperature curing, elevated temperature curing, or UV exposure, depending on the adhesive formulation.
-
Inspection: After curing, visually inspect the assembly for any defects, such as voids, gaps, or excessive adhesive spillage. If necessary, perform thermal or mechanical testing to verify the performance of the bonded assembly.
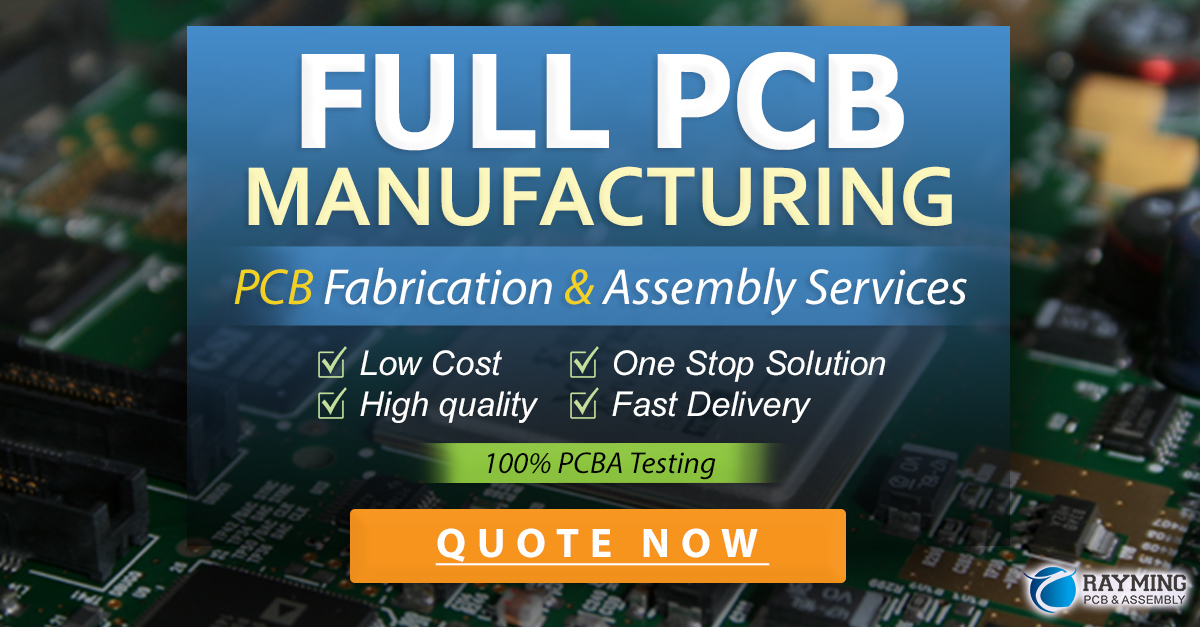
Selecting the Right Thermal Adhesive
Choosing the appropriate thermal adhesive for a specific application involves considering several factors:
-
Thermal Conductivity: Select an adhesive with a thermal conductivity that meets the heat dissipation requirements of the application. Higher thermal conductivity may be necessary for high-power devices or applications with limited heat sink area.
-
Adhesion Strength: Consider the required adhesion strength based on the operating environment and mechanical stresses the assembly will be subjected to. Adhesives with higher bond strength may be needed for applications with high vibration or thermal cycling.
-
Electrical Properties: Determine whether the adhesive needs to provide electrical insulation or conduction. For applications requiring electrical insulation, choose an adhesive with high dielectric strength and low dielectric constant.
-
Cure Mechanism: Select an adhesive with a cure mechanism that is compatible with the manufacturing process and throughput requirements. Room temperature curing adhesives offer simplicity, while heat-cured or UV-cured adhesives may provide faster curing times and higher performance.
-
Operating Temperature Range: Ensure the adhesive can withstand the expected operating temperature range of the electronic device. Consider both the maximum and minimum temperatures the assembly will be exposed to during operation.
-
Substrate Compatibility: Verify that the thermal adhesive is compatible with the substrate materials, such as the electronic component packaging and heat sink surface finish. Some adhesives may have limited adhesion to certain materials or may cause corrosion over time.
Best Practices for Using Thermal Adhesive
To ensure optimal performance and reliability when using thermal adhesives, consider the following best practices:
-
Follow Manufacturer’s Instructions: Always read and follow the manufacturer’s instructions for storage, handling, application, and curing of the thermal adhesive. Pay attention to recommended bond line thicknesses, cure schedules, and shelf life.
-
Ensure Proper Surface Preparation: Clean and degrease the mating surfaces thoroughly to remove any contaminants that may interfere with adhesion. If necessary, roughen the surfaces to improve adhesion.
-
Control Bond Line Thickness: Maintain a consistent and appropriate bond line thickness to achieve the desired thermal and mechanical properties. Too thin of a bond line may result in insufficient adhesion, while too thick of a bond line may increase thermal resistance.
-
Avoid Air Entrapment: During application and component placement, take care to minimize air entrapment between the mating surfaces. Trapped air can act as a thermal insulator and reduce the effectiveness of the adhesive.
-
Allow Adequate Curing Time: Provide sufficient time for the thermal adhesive to fully cure before subjecting the assembly to mechanical or thermal stresses. Incomplete curing can result in reduced adhesion and thermal conductivity.
-
Consider Rework and Repair: Select a thermal adhesive that allows for rework and repair if necessary. Some adhesives may be more easily removable than others, facilitating component replacement or maintenance.
Frequently Asked Questions (FAQ)
-
Q: Can thermal adhesives be used in high-temperature applications?
A: Yes, there are thermal adhesives specifically formulated for high-temperature applications. These adhesives can withstand temperatures up to 200°C or higher, depending on the specific formulation. It is essential to select an adhesive that is rated for the expected operating temperature range of the application. -
Q: How does the bond line thickness affect the performance of thermal adhesives?
A: The bond line thickness plays a crucial role in the performance of thermal adhesives. A thinner bond line generally results in lower thermal resistance, allowing for better heat transfer. However, if the bond line is too thin, it may compromise the adhesion strength and mechanical integrity of the assembly. Manufacturers typically provide recommendations for the optimal bond line thickness for their adhesives. -
Q: Can thermal adhesives be used for electrically conductive applications?
A: While most thermal adhesives are formulated to be electrically insulating, there are specialized thermally and electrically conductive adhesives available. These adhesives contain fillers that provide both thermal and electrical conductivity, making them suitable for applications where electrical grounding or shielding is required. However, it is important to note that electrically conductive adhesives may have lower thermal conductivity compared to their electrically insulating counterparts. -
Q: How do I select the right thermal adhesive for my application?
A: Selecting the right thermal adhesive involves considering several factors, such as the required thermal conductivity, adhesion strength, electrical properties, cure mechanism, operating temperature range, and substrate compatibility. It is recommended to consult with the adhesive manufacturer or a thermal management expert to discuss your specific application requirements and obtain guidance on the most suitable adhesive for your needs. -
Q: Can thermal adhesives be used in conjunction with other thermal management solutions?
A: Yes, thermal adhesives can be used in combination with other thermal management solutions, such as heat sinks, thermal interface materials (TIMs), and phase change materials (PCMs). In fact, thermal adhesives are often used to attach heat sinks to electronic components, providing a secure mechanical bond and efficient thermal transfer. When using multiple thermal management solutions together, it is important to ensure compatibility and optimize the overall thermal design for the best performance.
Conclusion
Thermal adhesives play a vital role in the thermal management of electronic components, providing a reliable and efficient means of bonding heat-generating devices to heat dissipation surfaces. By understanding the properties, applications, and best practices associated with thermal adhesives, engineers and designers can make informed decisions when selecting and applying these materials in their electronic assemblies.
As electronic devices continue to push the boundaries of performance and power density, the demand for advanced thermal management solutions, including high-performance thermal adhesives, will only continue to grow. Ongoing research and development in the field of thermal adhesives aim to improve thermal conductivity, adhesion strength, and ease of use, enabling the creation of more reliable and efficient electronic systems.
By leveraging the capabilities of thermal adhesives and following best practices for their application, manufacturers can ensure their electronic products operate at optimal temperatures, enhancing performance, reliability, and longevity. As the electronics industry advances, thermal adhesives will undoubtedly remain an essential tool in the thermal management toolkit, supporting the development of cutting-edge technologies across a wide range of applications.
Leave a Reply