Introduction to PCB Manufacturing
Printed Circuit Boards (PCBs) are essential components in modern electronics. They provide the foundation for connecting and supporting various electronic components in a compact and efficient manner. The manufacturing of PCBs involves several critical steps, each requiring specialized equipment to ensure high quality and reliability.
In this article, we will explore the various types of PCB manufacturing equipment, their functions, and their significance in the overall PCB production process. Understanding the capabilities and limitations of these machines is crucial for anyone involved in electronics design, manufacturing, or procurement.
Types of PCB Manufacturing Equipment
The PCB manufacturing process can be divided into several key stages, each requiring specific equipment. Here are the main categories of PCB manufacturing equipment:
1. PCB Design and Layout Software
Before any physical manufacturing takes place, PCBs are designed using specialized software. These tools allow engineers to create schematic diagrams, component layouts, and generate the necessary files for manufacturing. Some popular PCB design software include:
Software | Vendor | Key Features |
---|---|---|
Altium Designer | Altium | 3D design, real-time collaboration, advanced routing |
Eagle | Autodesk | User-friendly interface, extensive component libraries |
KiCad | Open Source | Free, cross-platform, active community support |
2. Imaging Equipment
Once the PCB design is finalized, the next step is to transfer the circuit pattern onto the copper-clad board. This is done using imaging equipment, which can be categorized into two main types:
a. Photo Plotters
Photo plotters use light exposure to create a photographic negative of the PCB design on a film. This film is then used to expose the photoresist layer on the copper-clad board. Key specifications to consider when selecting a photo plotter include:
- Maximum plot size
- Resolution (dots per inch or DPI)
- Plotting speed
- Film compatibility
b. Direct Imaging (DI) Systems
DI systems skip the film generation step and directly expose the photoresist layer on the copper-clad board using a laser or LED light source. This method offers higher precision and eliminates potential errors introduced by film handling. Important factors to consider when choosing a DI system include:
- Exposure area
- Resolution
- Throughput (panels per hour)
- Light source type (laser or LED)
3. Etching Equipment
After the circuit pattern is transferred to the photoresist layer, the unwanted copper is removed through an etching process. There are two primary types of etching equipment:
a. Wet Etching
Wet etching involves immersing the PCB in a chemical solution (typically ferric chloride or ammonium persulfate) that dissolves the exposed copper. Factors to consider when selecting wet etching equipment include:
- Tank capacity
- Etchant compatibility
- Temperature control
- Filtration and regeneration systems
b. Dry Etching
Dry etching uses a plasma to remove the unwanted copper. This method offers higher precision and generates less waste compared to wet etching. However, it is more expensive and complex. Key considerations for dry etching equipment include:
- Chamber size
- Plasma source type
- Gas compatibility
- Etch rate and selectivity
4. Drilling and Routing Equipment
After etching, holes need to be drilled through the PCB to accommodate through-hole components and provide interconnections between layers. Routing equipment is used to cut out the individual PCBs from the larger panel. The two main types of drilling and routing equipment are:
a. CNC Drills
Computer Numerical Control (CNC) drills use high-speed spindles and precision X-Y tables to drill holes at programmed locations. Important specifications for CNC drills include:
- Spindle speed
- Number of spindles
- Drill bit size range
- Positional accuracy
b. CNC Routers
CNC routers are used to cut the PCB panels into individual boards. They use high-speed spindles and cutting tools to achieve precise and clean cuts. Key factors to consider when selecting a CNC router include:
- Working area
- Spindle power and speed
- Tool change capabilities
- Vacuum table for material holding
5. Solder Mask and Silkscreen Application Equipment
Solder mask is a protective layer applied to the PCB to prevent solder bridging and provide insulation. Silkscreen is used to print text and symbols on the PCB for component identification and assembly guidance. The equipment used for applying solder mask and silkscreen includes:
a. Screen Printers
Screen printers use a mesh screen and squeegee to apply the solder mask or silkscreen ink to the PCB. Important considerations for screen printers include:
- Maximum print area
- Frame size compatibility
- Registration accuracy
- Print speed
b. Coating Systems
Coating systems apply the solder mask or silkscreen ink using a spraying or curtain coating method. These systems offer higher throughput and more uniform coverage compared to screen printers. Key factors to consider when selecting a coating system include:
- Coating method (spray or curtain)
- Coating thickness control
- Curing method (UV or thermal)
- Masking capabilities
6. Assembly and Inspection Equipment
After the bare PCBs are fabricated, they need to be populated with components and inspected for quality. The equipment used in this stage includes:
a. Pick-and-Place Machines
Pick-and-place machines automatically place surface mount components onto the PCB. They use vacuum nozzles and precision positioning systems to achieve high speed and accuracy. Important specifications for pick-and-place machines include:
- Placement speed (components per hour)
- Component size range
- Feeder capacity and types
- Vision system capabilities
b. Reflow Ovens
Reflow ovens are used to solder surface mount components to the PCB. They heat the board and components according to a precise temperature profile to melt the solder paste and form reliable connections. Key considerations for reflow ovens include:
- Heating zones and control
- Temperature profiling capabilities
- Conveyor type and speed
- Nitrogen atmosphere compatibility
c. Automated Optical Inspection (AOI) Systems
AOI systems use cameras and image processing algorithms to inspect the assembled PCBs for defects such as missing components, incorrect placements, or solder bridging. Important factors to consider when selecting an AOI system include:
- Camera resolution and lighting
- Defect detection algorithms
- Inspection speed
- Integration with other systems (e.g., pick-and-place machines)
Importance of PCB Manufacturing Equipment
Investing in high-quality PCB manufacturing equipment is crucial for several reasons:
-
Quality: Advanced equipment enables the production of high-quality PCBs with tight tolerances, minimal defects, and consistent performance. This is essential for applications where reliability is critical, such as aerospace, medical devices, and automotive systems.
-
Efficiency: Modern PCB manufacturing equipment offers high throughput and automation, reducing the time and labor required to produce PCBs. This translates to lower costs and faster turnaround times for customers.
-
Capability: As PCB designs become more complex, with finer features and higher densities, advanced manufacturing equipment becomes necessary to fabricate these boards. Investing in state-of-the-art equipment allows a manufacturer to stay competitive and meet the evolving needs of their customers.
-
Scalability: High-capacity equipment enables manufacturers to scale their production to meet increasing demand. This is particularly important for companies that expect significant growth or need to accommodate large orders.
-
Cost Reduction: While the initial investment in advanced PCB manufacturing equipment can be substantial, it often leads to long-term cost savings through increased efficiency, reduced waste, and lower labor costs. Additionally, higher-quality equipment tends to have a longer lifespan, reducing the frequency of costly replacements.
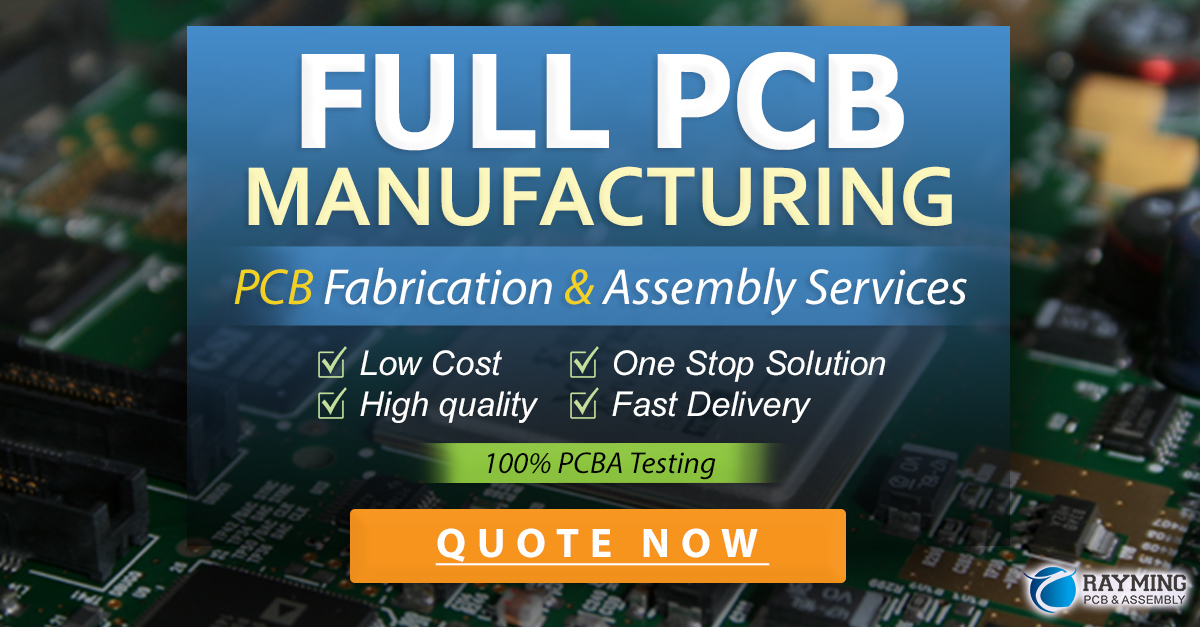
FAQ
1. What is the most critical piece of equipment in PCB manufacturing?
It is difficult to single out one piece of equipment as the most critical, as each stage of the PCB manufacturing process is essential for producing high-quality boards. However, some argue that the imaging equipment (photo plotters or direct imaging systems) is particularly important, as it determines the accuracy and resolution of the circuit patterns.
2. How much does PCB manufacturing equipment cost?
The cost of PCB manufacturing equipment varies widely depending on the type, capacity, and features of the machines. Entry-level equipment for small-scale production can cost tens of thousands of dollars, while high-end, fully automated systems can easily exceed a million dollars. It is important to carefully consider your production needs and budget when investing in PCB manufacturing equipment.
3. Can I manufacture PCBs without specialized equipment?
While it is possible to manually produce simple PCBs using basic tools and chemicals, it is not practical or cost-effective for most applications. Manufacturing high-quality, complex PCBs requires specialized equipment to ensure precision, consistency, and efficiency. Attempting to manufacture PCBs without the proper equipment can lead to subpar results, wasted materials, and potential safety hazards.
4. How do I choose the right PCB manufacturing equipment for my needs?
Choosing the right PCB manufacturing equipment depends on several factors, including:
- Production volume and scalability
- PCB complexity and feature size
- Budget and return on investment
- Facility space and infrastructure
- Technical expertise of your staff
It is advisable to consult with experienced PCB manufacturing professionals or equipment vendors to help assess your needs and recommend suitable solutions.
5. What is the future of PCB manufacturing equipment?
The future of PCB manufacturing equipment is driven by the increasing complexity and miniaturization of electronic devices. Some key trends to watch include:
- Advances in imaging technology to enable finer feature sizes and higher resolutions
- Increased automation and integration of manufacturing processes
- Adoption of Industry 4.0 technologies, such as the Internet of Things (IoT), artificial intelligence (AI), and machine learning (ML) for process optimization and quality control
- Development of new materials and processes to support emerging applications, such as flexible and stretchable electronics
As the demand for more advanced and customized PCBs continues to grow, manufacturers will need to stay up-to-date with the latest equipment and technologies to remain competitive.
Conclusion
PCB manufacturing equipment plays a vital role in the production of high-quality, reliable printed circuit boards. From design and imaging to etching, drilling, and assembly, each stage of the process relies on specialized machines to ensure precision, consistency, and efficiency.
Investing in the right PCB manufacturing equipment is crucial for manufacturers looking to meet the evolving needs of their customers, reduce costs, and stay competitive in an increasingly complex and demanding market. By understanding the capabilities and limitations of different types of equipment, manufacturers can make informed decisions and optimize their production processes.
As the electronics industry continues to advance, PCB manufacturing equipment will undoubtedly evolve to keep pace with new challenges and opportunities. Staying informed about the latest technologies and trends will be essential for those involved in PCB design, manufacturing, and procurement.
Leave a Reply