1. Choose the Right Materials
Selecting the appropriate materials is crucial for successful FlexPCB-Manufacturing. The most common materials used in Flex PCBs include:
Material | Characteristics | Typical Applications |
---|---|---|
Polyimide (PI) | High heat resistance, good mechanical properties | Aerospace, medical devices, consumer electronics |
Polyester (PET) | Low cost, good electrical properties | Consumer electronics, displays, sensors |
Liquid Crystal Polymer (LCP) | Low moisture absorption, excellent high-frequency performance | High-speed data transmission, RF applications |
When choosing materials, consider factors such as the operating environment, required flexibility, and desired electrical properties.
2. Optimize Circuit Design
Proper circuit design is essential for FlexPCB-Manufacturing success. Keep these tips in mind:
- Use larger trace widths and spacing to accommodate bending and flexing
- Avoid sharp angles in traces; use rounded corners instead
- Place components strategically to minimize stress during flexing
- Consider using stiffeners in areas that require extra support
By optimizing your circuit design, you can reduce the risk of failures and improve the overall reliability of your Flex PCBs.
3. Select the Right Adhesive
Adhesives play a critical role in bonding the layers of a Flex PCB together. The most common adhesives used in FlexPCB-Manufacturing are:
- Acrylic
- Epoxy
- Pressure-sensitive adhesive (PSA)
Choose an adhesive that offers good bonding strength, flexibility, and compatibility with your chosen materials. Additionally, consider the curing process and ensure that it aligns with your manufacturing workflow.
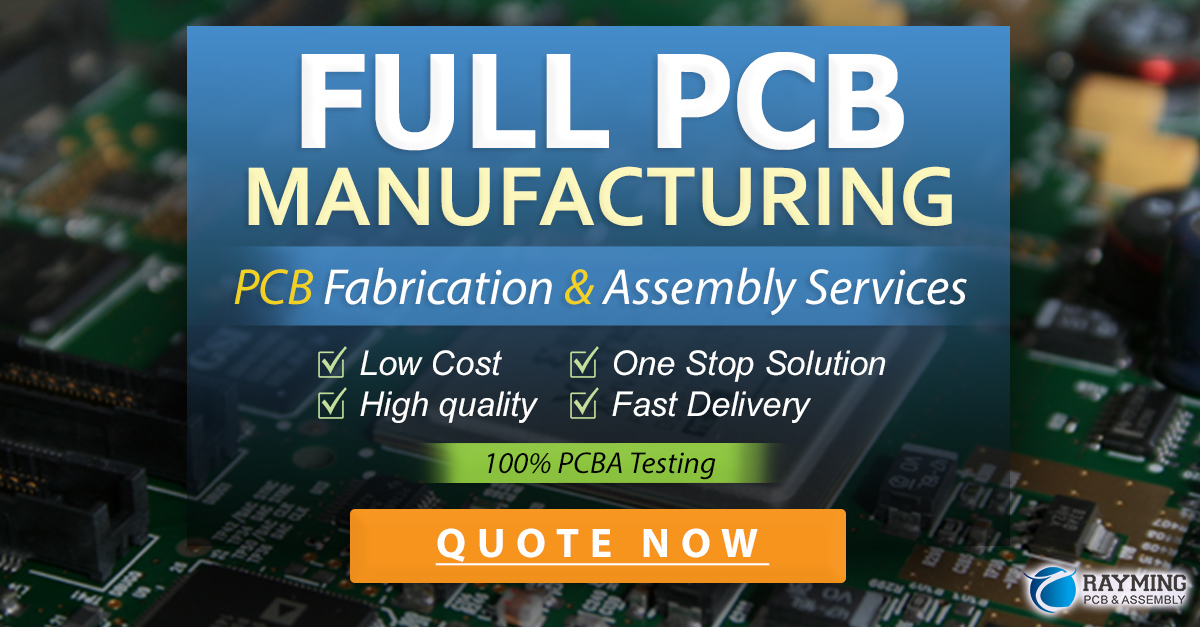
4. Implement Controlled Impedance
For high-speed and RF applications, controlling the impedance of your Flex PCBs is crucial. To achieve controlled impedance:
- Use appropriate dielectric materials with consistent properties
- Maintain consistent trace widths and spacing
- Employ proper grounding techniques
- Utilize simulation tools to predict and optimize impedance
By implementing controlled impedance, you can minimize signal integrity issues and ensure reliable high-frequency performance.
5. Employ Precise Lamination Techniques
Lamination is the process of bonding the layers of a Flex PCB together using heat and pressure. To achieve perfect lamination:
- Use a vacuum press to remove air bubbles and ensure even pressure distribution
- Control the lamination temperature and duration based on your chosen materials and adhesives
- Implement a multi-step lamination process for complex designs
- Monitor and maintain consistent lamination parameters throughout the process
Precise lamination techniques help prevent delamination, improve adhesion, and enhance the overall durability of your Flex PCBs.
6. Incorporate Strain Relief Features
Flex PCBs are subject to repeated bending and flexing, which can lead to mechanical stress and potential failures. To mitigate these issues, incorporate strain relief features such as:
- Bend reliefs: Gradual curves at the transition points between flexible and rigid areas
- Stiffeners: Rigid reinforcements in areas prone to high stress
- Tear stops: Small circular cut-outs that prevent tear propagation
By incorporating these features, you can significantly improve the longevity and reliability of your Flex PCBs.
7. Implement Robust Quality Control Measures
Quality control is essential for ensuring consistent and reliable FlexPCB-Manufacturing. Implement the following measures:
- Automated optical inspection (AOI) to detect surface defects
- Flying probe testing to verify electrical continuity and isolate faults
- Cross-section analysis to examine internal structure and lamination quality
- Functional testing to validate performance under real-world conditions
Robust quality control measures help identify and address issues early in the manufacturing process, reducing waste and improving overall yield.
8. Optimize Cover Lay Application
The cover lay is a protective layer applied to the outer surfaces of a Flex PCB. To optimize cover lay application:
- Use laser-cut or die-cut cover lays for precise fitment
- Ensure proper adhesion between the cover lay and the PCB surface
-
Implement controlled curing processes to achieve optimal bonding
-
Consider using photoimageable cover lays for fine-pitch designs
Proper cover lay application helps protect your Flex PCBs from environmental factors and improves their overall durability.
9. Partner with Experienced Manufacturers
Partnering with experienced FlexPCB-Manufacturing providers is crucial for achieving perfect results. Look for manufacturers that offer:
- State-of-the-art equipment and facilities
- Skilled engineers and technicians
- Proven track record of success in Flex PCB manufacturing
- Comprehensive quality management systems
- Flexibility to accommodate custom designs and requirements
By working with experienced manufacturers, you can leverage their expertise and capabilities to ensure the success of your Flex PCB projects.
FAQ
1. What are the advantages of using Flex PCBs over rigid PCBs?
Flex PCBs offer several advantages over rigid PCBs, including:
– Ability to bend and fold, enabling compact and space-saving designs
– Lighter weight, which is crucial for portable and wearable devices
– Improved reliability due to reduced mechanical stress on components
– Enhanced design flexibility for unique form factors and applications
2. What are the most common challenges faced in FlexPCB-Manufacturing?
Some of the most common challenges in FlexPCB-Manufacturing include:
– Maintaining consistent material properties during the manufacturing process
– Achieving precise alignment and registration of layers
– Controlling the lamination process to prevent delamination and ensure proper adhesion
– Implementing appropriate strain relief features to minimize mechanical stress
– Ensuring compatibility between materials, adhesives, and manufacturing processes
3. How do I choose the right materials for my Flex PCB design?
When choosing materials for your Flex PCB design, consider factors such as:
– Required flexibility and bending characteristics
– Operating environment and temperature range
– Desired electrical properties, such as dielectric constant and loss tangent
– Compatibility with your chosen manufacturing processes and adhesives
– Cost and availability of materials
Consult with experienced Flex PCB manufacturers and material suppliers to select the most suitable materials for your specific application.
4. What are the key considerations for designing Flex PCBs for high-speed applications?
When designing Flex PCBs for high-speed applications, keep these key considerations in mind:
– Implement controlled impedance to maintain signal integrity
– Use appropriate dielectric materials with low loss and consistent properties
– Minimize trace lengths and use proper termination techniques to reduce reflections
– Employ effective shielding and grounding strategies to minimize crosstalk and EMI
– Simulate and optimize your design using advanced tools to predict and address potential issues
5. How can I ensure the longevity and reliability of my Flex PCBs?
To ensure the longevity and reliability of your Flex PCBs:
– Choose high-quality materials that can withstand the intended operating environment
– Incorporate strain relief features to minimize mechanical stress during flexing
– Implement robust quality control measures throughout the manufacturing process
– Use appropriate protective coatings and encapsulation techniques to shield against environmental factors
– Conduct thorough testing and validation to identify and address potential failure modes
By following these best practices and partnering with experienced FlexPCB-Manufacturing providers, you can create Flex PCBs that deliver reliable performance over their intended lifespan.
Conclusion
FlexPCB-Manufacturing requires a combination of precision, expertise, and attention to detail to achieve perfect results. By choosing the right materials, optimizing circuit designs, employing precise manufacturing techniques, and implementing robust quality control measures, you can ensure the success of your Flex PCB projects. Additionally, partnering with experienced manufacturers can provide valuable insights and support throughout the development process.
As the demand for compact, lightweight, and flexible electronics continues to grow, mastering the art of FlexPCB-Manufacturing will become increasingly important. By staying up-to-date with the latest technologies, best practices, and industry trends, you can position yourself at the forefront of this exciting field and create innovative Flex PCB solutions that push the boundaries of modern electronics.
Leave a Reply