What is PCB Conformal Coating?
PCB conformal coating is a thin layer of protective material applied onto printed circuit boards (PCBs) to shield them from environmental factors such as moisture, dust, chemicals, and extreme temperatures. This coating acts as a barrier, preventing contaminants from reaching the sensitive electronic components and conductive traces on the PCB. Conformal coatings are essential for ensuring the long-term reliability and performance of electronic devices, especially those operating in harsh environments.
Types of PCB Conformal Coatings
There are several types of conformal coatings available, each with its own unique properties and advantages:
Coating Type | Characteristics | Typical Thickness Range |
---|---|---|
Acrylic | Easy to apply and remove, good moisture resistance | 25-75 μm |
Silicone | Excellent flexibility and temperature resistance | 50-200 μm |
Polyurethane | Abrasion-resistant, good chemical resistance | 25-130 μm |
Epoxy | High dielectric strength, excellent chemical resistance | 25-150 μm |
Parylene | Uniform coverage, superior barrier properties | 12-50 μm |
Importance of PCB Conformal Coating Thickness
The thickness of the conformal coating applied to a PCB is a critical factor in determining its effectiveness in protecting the board from environmental hazards. An ideal coating thickness ensures optimal coverage and protection without compromising the functionality or performance of the PCB.
Adequate Protection
A conformal coating that is too thin may not provide sufficient protection against moisture, chemicals, or other contaminants. This can lead to corrosion, short circuits, and premature failure of the electronic components. On the other hand, an excessively thick coating can cause issues such as reduced heat dissipation, altered electrical properties, and mechanical stress on components.
Maintaining PCB Functionality
The ideal conformal coating thickness should be carefully chosen to maintain the intended functionality of the PCB. Thick coatings may interfere with the operation of certain components, such as switches, connectors, or heat sinks. Additionally, excessive coating thickness can cause problems during the assembly process, such as difficulty in soldering or component placement.
Factors Affecting PCB Conformal Coating Ideal Thickness
Several factors must be considered when determining the ideal thickness of a conformal coating for a specific PCB application:
1. Environmental Conditions
The environmental conditions to which the PCB will be exposed play a significant role in determining the ideal coating thickness. Harsh environments, such as those with high humidity, corrosive chemicals, or extreme temperatures, may require thicker coatings for adequate protection. On the other hand, PCBs operating in mild environments may only need a thin layer of coating.
2. PCB Design and Components
The design of the PCB and the types of components used can also influence the ideal coating thickness. High-density PCBs with closely spaced components may require thinner coatings to avoid bridging or excessive buildup between components. Boards with tall components or those requiring specific clearances may need special consideration when applying the coating.
3. Coating Material Properties
Each type of conformal coating material has its own unique properties that affect the ideal thickness. For example, parylene coatings are typically applied in very thin layers due to their excellent barrier properties, while silicone coatings may require thicker applications to achieve the desired level of protection.
4. Application Method
The method used to apply the conformal coating can impact the ideal thickness. Common application methods include spray coating, brush coating, and dip coating. Each method has its own advantages and limitations in terms of coating uniformity, thickness control, and coverage of complex board geometries.
5. Curing and Drying Time
The curing and drying time of the conformal coating can also influence the ideal thickness. Thicker coatings may require longer curing times, which can impact production throughput. Additionally, some coating materials may shrink or change dimensions during the curing process, affecting the final thickness.
6. Cost Considerations
The cost of the conformal coating material and the application process should also be taken into account when determining the ideal thickness. Thicker coatings may require more material and longer application times, increasing overall costs. A balance must be struck between adequate protection and cost-effectiveness.
7. Industry Standards and Regulations
Certain industries, such as automotive, aerospace, and military, have specific standards and regulations governing the use of conformal coatings. These standards may dictate minimum or maximum coating thicknesses for different applications. It is essential to ensure compliance with relevant standards when selecting the ideal coating thickness.
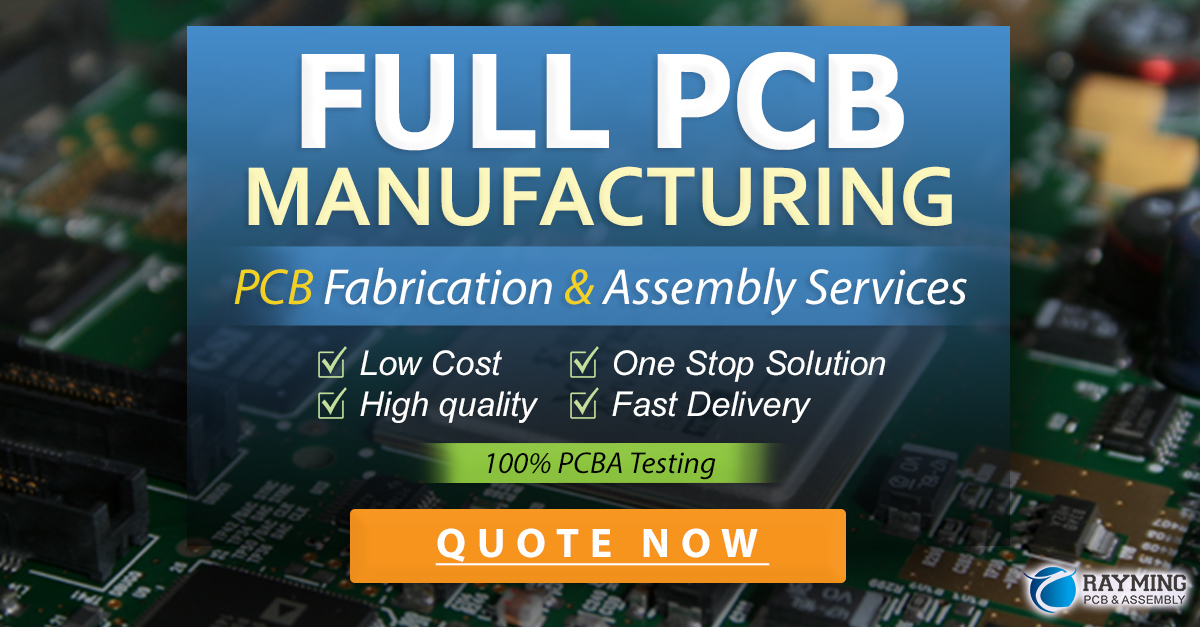
Measuring PCB Conformal Coating Thickness
To ensure that the applied conformal coating meets the desired thickness requirements, accurate measurement techniques must be employed. Several methods are commonly used to measure coating thickness:
Wet Film Thickness Gauge
A wet film thickness gauge is a simple tool that can be used to measure the thickness of the coating immediately after application, while it is still wet. This method involves pressing the gauge into the wet coating and reading the thickness from the graduated scale.
Dry Film Thickness Gauge
Dry film thickness gauges are used to measure the thickness of the coating after it has cured or dried. These gauges use various technologies, such as magnetic induction or eddy current, to non-destructively measure the coating thickness on the PCB.
Cross-Sectional Analysis
For more precise thickness measurements, a cross-sectional analysis can be performed. This involves cutting a small section of the coated PCB and examining it under a microscope. The thickness of the coating can be accurately measured using calibrated software or by comparing it to a known reference scale.
FAQ
1. What is the typical thickness range for PCB conformal coatings?
The typical thickness range for PCB conformal coatings varies depending on the coating material and application requirements. In general, coatings can range from 12 μm to 200 μm, with most applications falling between 25 μm and 75 μm.
2. Can a conformal coating be too thin to provide adequate protection?
Yes, a conformal coating that is too thin may not provide sufficient protection against environmental hazards such as moisture, chemicals, or contaminants. This can lead to corrosion, short circuits, and premature failure of the electronic components.
3. What issues can arise from applying a conformal coating that is too thick?
Applying a conformal coating that is too thick can cause several issues, including reduced heat dissipation, altered electrical properties, and mechanical stress on components. Thick coatings may also interfere with the operation of certain components, such as switches, connectors, or heat sinks.
4. How does the PCB design influence the ideal conformal coating thickness?
The PCB design and component layout can influence the ideal conformal coating thickness. High-density PCBs with closely spaced components may require thinner coatings to avoid bridging or excessive buildup between components. Boards with tall components or those requiring specific clearances may need special consideration when applying the coating.
5. Are there industry standards that dictate conformal coating thickness requirements?
Yes, certain industries, such as automotive, aerospace, and military, have specific standards and regulations governing the use of conformal coatings. These standards may dictate minimum or maximum coating thicknesses for different applications. It is essential to ensure compliance with relevant standards when selecting the ideal coating thickness.
Conclusion
Selecting the ideal thickness for PCB conformal coatings is a critical factor in ensuring the long-term reliability and performance of electronic devices. The thickness of the coating must be carefully chosen to provide adequate protection against environmental hazards while maintaining the functionality and performance of the PCB.
Several factors, including environmental conditions, PCB design, coating material properties, application method, curing time, cost considerations, and industry standards, must be taken into account when determining the ideal coating thickness.
Accurate measurement techniques, such as wet and dry film thickness gauges and cross-sectional analysis, should be employed to ensure that the applied coating meets the desired thickness requirements.
By considering these factors and implementing appropriate measurement and control processes, manufacturers can optimize the performance and reliability of their PCBs through the use of conformal coatings with ideal thicknesses.
Leave a Reply