What is Countersinking?
Countersinking is a machining process where a conical hole is cut into a manufactured object, or hole, to allow the head of a countersunk bolt or screw, when placed in the hole, to sit flush with or below the surface of the surrounding material. A countersink may be used in many tools, such as drills, drill presses, milling machines, and lathes.
Advantages of Countersinking
- It provides a flush surface for fasteners, improving the aesthetics of the finished product.
- Countersinking reduces the risk of snagging or catching on protruding fastener heads.
- It helps distribute the load evenly across the fastener head, reducing stress concentrations.
Disadvantages of Countersinking
- Countersinking can weaken the material around the hole due to the removal of additional material.
- It requires more precise machining and alignment compared to straight holes.
- Countersunk holes may not provide as much bearing surface for the fastener head compared to counterbores.
What is Counterboring?
Counterboring is a machining process where a cylindrical flat-bottomed hole is drilled to allow the head of a socket head cap screw or bolt to fit below the surface of the workpiece. The counterbore is typically deeper than the length of the fastener head and has a larger diameter to accommodate the head.
Advantages of Counterboring
- Counterboring provides a flat bearing surface for the fastener head, distributing the load evenly.
- It allows for the use of socket head cap screws, which have a higher tensile strength compared to countersunk screws.
- Counterbored holes can be used to hide fasteners completely below the surface of the workpiece.
Disadvantages of Counterboring
- Counterboring requires more material removal compared to countersinking, potentially weakening the workpiece.
- It may be more time-consuming and expensive due to the additional machining steps involved.
- Counterbored holes can trap dirt, debris, or fluids, which may be undesirable in certain applications.
Comparing Countersink and Counterbore
Feature | Countersink | Counterbore |
---|---|---|
Hole Shape | Conical | Cylindrical with flat bottom |
Fastener Type | Countersunk screws | Socket head cap screws |
Load Distribution | Less even distribution | More even distribution |
Material Removal | Less material removed | More material removed |
Machining Complexity | Simpler | More complex |
Aesthetics | Flush or recessed fasteners | Fasteners hidden below surface |
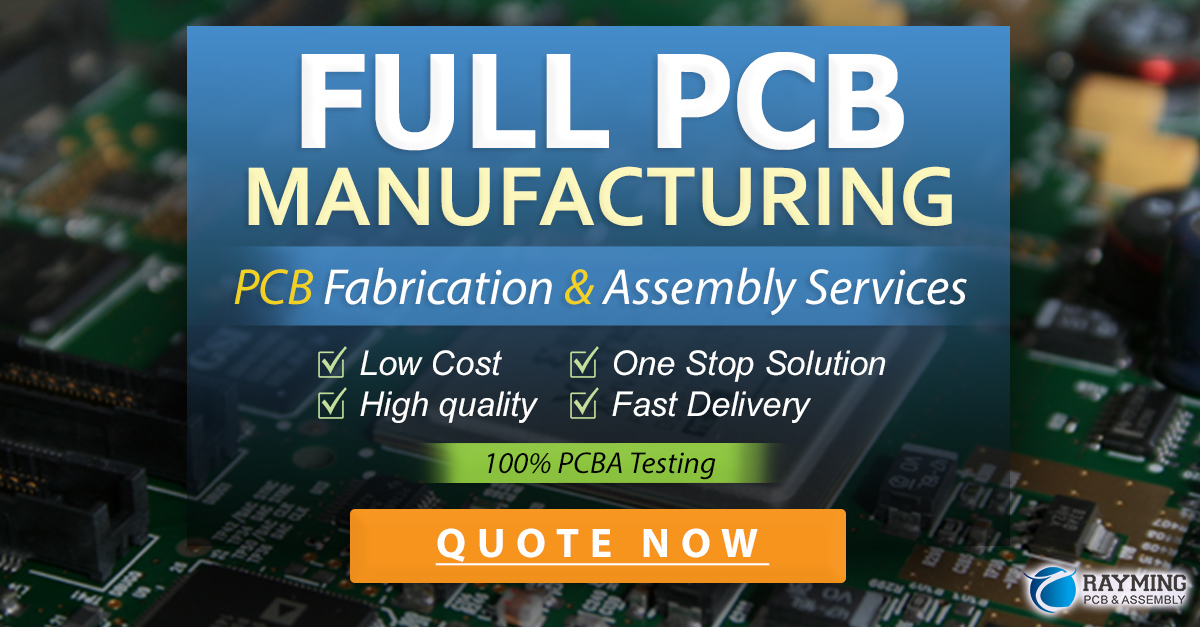
When to Use Countersinking
Countersinking is ideal for applications where a flush or recessed fastener surface is desired, such as:
1. Aerodynamic surfaces to reduce drag
2. Furniture and cabinetry for a clean, streamlined appearance
3. Assemblies where protruding fastener heads may cause interference or snagging
When to Use Counterboring
Counterboring is preferred in situations where:
1. High-strength fasteners, such as socket head cap screws, are required
2. A flat bearing surface is needed to distribute the load evenly
3. Fasteners need to be completely hidden below the surface of the workpiece
FAQ
1. Can countersinking and counterboring be combined in the same hole?
Yes, it is possible to have a counterbore followed by a countersink in the same hole. This is called a “compound angle” and is used when a fastener with a countersunk head needs to be seated in a counterbored hole.
2. What materials are suitable for countersinking and counterboring?
Countersinking and counterboring can be performed on various materials, including metals, plastics, and composites. However, the machining parameters and tools used may vary depending on the material properties.
3. How do I select the appropriate countersink or counterbore size?
The size of the countersink or counterbore depends on the fastener size and head dimensions. Consult the fastener manufacturer’s specifications or engineering drawings to determine the appropriate dimensions for the countersink or counterbore.
4. Can countersinking and counterboring be done by hand?
While countersinking and counterboring are typically performed using machine tools, such as drill presses or milling machines, it is possible to do these operations by hand using specialized hand tools designed for countersinking and counterboring.
5. Are there any industry standards for countersinking and counterboring dimensions?
Yes, there are various industry standards that specify the dimensions and tolerances for countersinks and counterbores, such as ANSI B18.6.3 for machine screws and ASME B18.3 for socket cap screws. It is essential to refer to the relevant standards when designing or specifying countersinks and counterbores.
In conclusion, understanding the differences between countersinking and counterboring is crucial for selecting the appropriate machining process for your application. By considering factors such as fastener type, load distribution, material properties, and aesthetic requirements, you can make an informed decision on whether to use countersinking or counterboring in your designs.
Leave a Reply