What is a Transformerless Power Supply?
A transformerless power supply, as the name suggests, is a power supply that does not use a transformer to step down the input AC voltage. Instead, it directly rectifies and filters the high voltage AC input to produce a low voltage DC output suitable for powering electronic devices.
The main advantages of transformerless power supplies are:
- Lower cost due to elimination of the bulky and expensive transformer
- Smaller size and lighter weight
- Higher efficiency, as there are no transformer losses
- Wider input voltage range capability
However, the main disadvantage is the lack of galvanic isolation between the AC input and DC output, which can be a safety hazard if not designed properly. Proper insulation, grounding and protection circuitry is critical in transformerless designs.
Applications of Transformerless Power Supplies
Transformerless power supplies are commonly used in cost-sensitive, space-constrained applications where galvanic isolation is not critical. Some examples are:
- LED lighting
- Battery Chargers
- Home appliances like TVs, set-top boxes, etc.
- Industrial control systems
- Medical devices
- Telecom equipment
Basic Topology of a Transformerless Power Supply
The basic topology of a transformerless power supply consists of the following stages:
-
Input filtering and protection: This stage filters out the high frequency noise from the AC input and provides protection against voltage surges and spikes. It typically consists of a fuse, varistor, X and Y capacitors.
-
Rectification: This stage converts the AC input to pulsating DC using a full-bridge rectifier made up of diodes. The output of this stage is a high voltage DC with a large ripple.
-
High voltage filtering: This stage filters out the ripple from the rectified DC using high voltage capacitors. The output of this stage is a smooth high voltage DC.
-
High frequency switching: This stage converts the high voltage DC to high frequency AC using a switching circuit, typically a MOSFET half-bridge or full-bridge. The switching frequency is usually in the range of 20kHz to 100kHz.
-
Step-down and isolation: This stage steps down the high frequency AC to the desired low voltage level using a small high frequency transformer. This transformer provides the galvanic isolation between the input and output.
-
Output rectification and filtering: This stage rectifies the low voltage AC from the transformer using fast recovery diodes and filters it using low ESR capacitors to produce the final DC output.
-
Output regulation: This stage regulates the output voltage to the desired level using a feedback control loop. The feedback can be voltage mode or current mode. The regulation is done by controlling the switching duty cycle of the high frequency switching stage.
-
Output protection: This stage provides protection against overload, short circuit and over-voltage conditions at the output. It typically consists of a current sensing circuit, over-voltage protection circuit and a crowbar circuit.
Here is a block diagram showing the different stages of a transformerless power supply:
graph LR
A[AC Input] --> B[Input Filtering and Protection]
B --> C[Rectification]
C --> D[High Voltage Filtering]
D --> E[High Frequency Switching]
E --> F[Step-Down and Isolation]
F --> G[Output Rectification and Filtering]
G --> H[Output Regulation]
H --> I[Output Protection]
I --> J[DC Output]
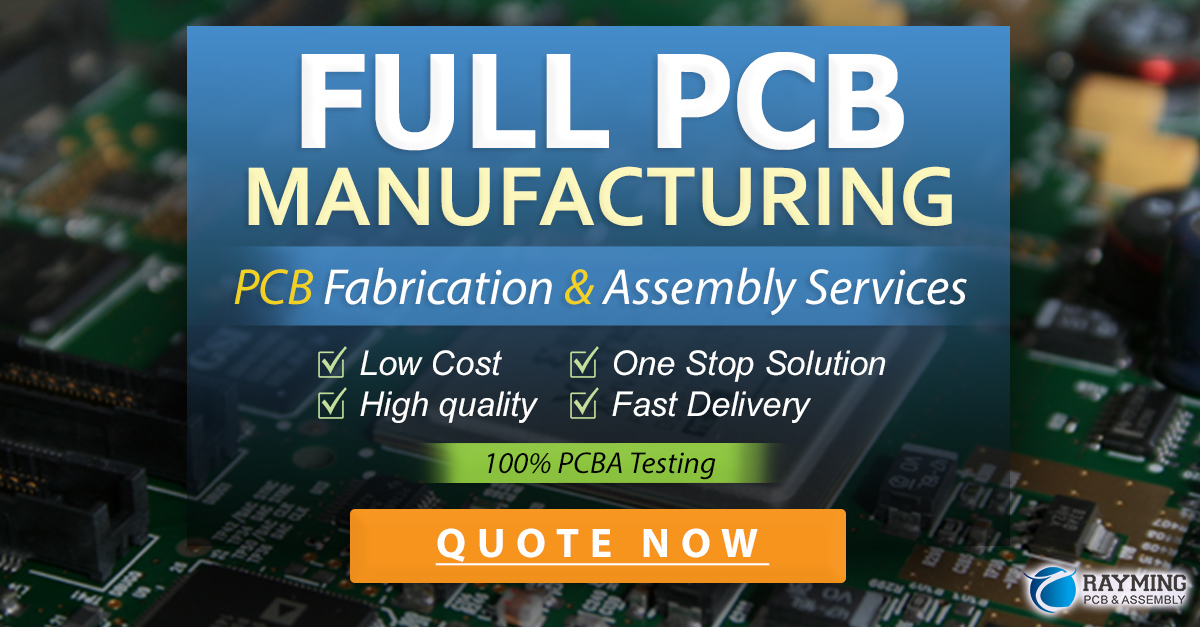
Design Considerations for Transformerless Power Supplies
Designing a transformerless power supply requires careful consideration of several factors to ensure safety, reliability and performance. Some of the key design considerations are:
1. Input Voltage Range
The input voltage range of a transformerless power supply is usually wider than that of a transformer-based power supply. This is because the high frequency transformer used in a transformerless power supply is much smaller and has a higher turns ratio, which allows it to handle a wider range of input voltages.
However, the input voltage range is limited by the maximum voltage rating of the components used in the input stage, such as the fuse, varistor, rectifier diodes and filter capacitors. These components must be chosen to withstand the maximum input voltage under worst-case conditions, such as voltage surges and spikes.
2. Isolation and Safety
One of the main challenges in designing a transformerless power supply is ensuring galvanic isolation between the AC input and DC output. This is critical for safety, as the AC input can have high voltages of up to 400V or more, which can be lethal if it comes in contact with the user.
The isolation is provided by the high frequency transformer used in the step-down and isolation stage. This transformer must have sufficient insulation between the primary and secondary windings to withstand the maximum input voltage and provide the required isolation.
In addition to the transformer, the power supply must also have proper grounding and protection circuitry to ensure safety. This includes:
- Earth ground connection for the chassis and exposed metal parts
- X and Y capacitors for filtering out common mode noise
- Fuse and varistor for protection against voltage surges and spikes
- Isolation barriers and creepage distances between high voltage and low voltage sections
- Proper insulation and spacing of components and PCB traces
3. Efficiency and Power Density
Transformerless power supplies have higher efficiency and power density compared to transformer-based power supplies due to the elimination of the bulky transformer. However, achieving high efficiency and power density requires careful design and selection of components.
The high frequency switching stage is the most critical stage for efficiency, as it has the highest power losses. The switching frequency, MOSFET selection, gate drive circuit and snubber design all play a key role in minimizing the switching losses and improving efficiency.
The output rectification and filtering stage also has a significant impact on efficiency, as the diode losses and capacitor ESR losses can be substantial. Using fast recovery diodes and low ESR capacitors can help reduce these losses and improve efficiency.
The power density of the power supply can be increased by using high frequency switching, which allows the use of smaller transformers, inductors and capacitors. However, this also increases the challenges in terms of EMI, thermal management and component selection.
4. EMI and EMC
Transformerless power supplies generate high frequency noise due to the switching action of the MOSFETs. This noise can cause electromagnetic interference (EMI) with other electronic devices and must be kept within acceptable limits to meet electromagnetic compatibility (EMC) standards.
The EMI can be reduced by using proper filtering and shielding techniques, such as:
- Input and output EMI filters using X and Y capacitors and common mode chokes
- Proper grounding and shielding of the power supply enclosure
- Use of ferrite beads and snubbers to suppress high frequency ringing
- Careful layout of the PCB to minimize noise coupling and loops
5. Thermal Management
Transformerless power supplies generate heat due to the power losses in the components, especially the MOSFETs, diodes and capacitors. This heat must be effectively dissipated to prevent overheating and ensure reliable operation.
The thermal management can be done using various techniques, such as:
- Using components with low thermal resistance and high power dissipation capability
- Providing adequate heat sinking and air flow for the critical components
- Using thermal interface materials and thermal pads to improve heat transfer
- Implementing over-temperature protection and derating of components based on temperature
Advantages and Disadvantages of Transformerless Power Supplies
Transformerless power supplies have several advantages and disadvantages compared to transformer-based power supplies. Here is a table summarizing the main points:
Advantages | Disadvantages |
---|---|
Lower cost due to elimination of transformer | Lack of galvanic isolation, requiring extra safety measures |
Smaller size and lighter weight | Higher complexity and component count |
Higher efficiency due to no transformer losses | Higher EMI and noise due to high frequency switching |
Wider input voltage range capability | Higher stress on components due to high voltage DC bus |
Higher power density due to smaller size | More challenging thermal management due to higher power density |
As can be seen, transformerless power supplies offer several benefits in terms of cost, size and efficiency, but also have some drawbacks in terms of safety, complexity and noise. The choice between a transformerless and transformer-based power supply depends on the specific application requirements and trade-offs.
FAQs
1. Are transformerless power supplies safe to use?
Yes, transformerless power supplies can be safe to use if designed and built properly with adequate safety measures such as galvanic isolation, grounding, and protection circuitry. However, they do pose a higher safety risk compared to transformer-based power supplies due to the lack of inherent isolation.
2. What are the typical applications for transformerless power supplies?
Transformerless power supplies are commonly used in cost-sensitive, space-constrained applications where galvanic isolation is not critical, such as LED lighting, battery chargers, home appliances, industrial control systems, medical devices, and telecom equipment.
3. What is the main advantage of using a transformerless power supply?
The main advantages of using a transformerless power supply are lower cost, smaller size, lighter weight, higher efficiency, and wider input voltage range capability compared to transformer-based power supplies.
4. What is the main disadvantage of using a transformerless power supply?
The main disadvantage of using a transformerless power supply is the lack of galvanic isolation between the AC input and DC output, which can be a safety hazard if not designed properly. Proper insulation, grounding and protection circuitry is critical in transformerless designs.
5. What are the key design considerations for transformerless power supplies?
The key design considerations for transformerless power supplies are input voltage range, isolation and safety, efficiency and power density, EMI and EMC, and thermal management. Careful design and selection of components is required to ensure reliable and safe operation.
Leave a Reply