What is PCB Insulation?
PCB insulation refers to the materials and techniques used to isolate the conductive traces and components on a printed circuit board from each other and the environment. The primary purpose of insulation is to prevent short circuits, signal interference, and damage to the PCB and its components. Effective insulation is essential for maintaining the integrity and reliability of the electronic device.
Types of PCB Insulation Materials
There are several materials commonly used for PCB insulation, each with its own unique properties and advantages. The choice of insulation material depends on factors such as the intended application, operating environment, and cost considerations. Some of the most widely used PCB insulation materials include:
-
FR-4: FR-4 is a glass-reinforced epoxy laminate that is the most common base material for PCBs. It offers excellent electrical insulation properties, mechanical strength, and thermal stability. FR-4 is suitable for a wide range of applications and is cost-effective.
-
Polyimide: Polyimide is a high-performance polymer that offers exceptional thermal and chemical resistance. It is often used in applications that require operation at high temperatures or exposure to harsh environments. Polyimide has excellent electrical insulation properties and is known for its durability.
-
PTFE (Polytetrafluoroethylene): PTFE, also known as Teflon, is a fluoropolymer with outstanding electrical insulation properties. It has a low dielectric constant and dissipation factor, making it ideal for high-frequency applications. PTFE is resistant to chemicals and can withstand high temperatures.
-
Ceramic: Ceramic materials, such as alumina and beryllia, offer excellent electrical insulation and thermal conductivity. They are often used in high-power and high-temperature applications. Ceramic substrates provide a stable and reliable base for mounting electronic components.
-
Conformal Coatings: Conformal coatings are thin layers of insulating material applied to the surface of a PCB. They provide additional protection against moisture, dust, and other environmental factors. Common conformal coating materials include acrylic, silicone, and polyurethane.
Material | Dielectric Constant | Dissipation Factor | Temperature Range (°C) |
---|---|---|---|
FR-4 | 4.5 | 0.02 | -55 to 125 |
Polyimide | 3.5 | 0.002 | -269 to 400 |
PTFE | 2.1 | 0.0002 | -200 to 260 |
Ceramic (Alumina) | 9.8 | 0.0001 | -200 to 1600 |
PCB Insulation Techniques
In addition to selecting the appropriate insulation materials, various techniques are employed to ensure effective insulation on a PCB. These techniques help to maintain the desired spacing between conductive traces, prevent short circuits, and enhance the overall reliability of the PCB.
-
Solder Mask: Solder mask is a thin layer of polymer applied to the surface of a PCB, covering the copper traces while leaving the pads exposed. It serves as an insulating barrier, preventing accidental short circuits during soldering and protecting the traces from environmental factors.
-
Conformal Coating: As mentioned earlier, conformal coatings are applied to the surface of a PCB to provide additional insulation and protection. They form a thin, conforming layer over the components and traces, shielding them from moisture, dust, and other contaminants.
-
Potting and Encapsulation: Potting and encapsulation involve the use of a resin or compound to completely encase the PCB or specific components. This technique provides enhanced insulation, mechanical protection, and environmental sealing. It is commonly used in applications that require high reliability and protection against vibration, shock, and extreme conditions.
-
Clearance and Creepage: Clearance refers to the shortest distance through air between two conductive parts, while creepage is the shortest distance along the surface of the insulating material between two conductive parts. Maintaining appropriate clearance and creepage distances is crucial for preventing electrical breakdown and ensuring proper insulation.
-
Via Tenting: Via tenting is a technique where the solder mask is applied over the vias (holes) on a PCB, creating an insulating barrier. This helps to prevent solder from flowing into the vias during the soldering process and provides additional insulation between layers.
Importance of PCB Insulation
Proper PCB insulation is essential for several reasons:
-
Signal Integrity: Effective insulation prevents signal interference and crosstalk between adjacent traces. It ensures that the electrical signals remain clean and undistorted, maintaining the integrity of the data being transmitted.
-
Reliability: Insulation protects the PCB and its components from short circuits, which can cause permanent damage and lead to device failure. By preventing short circuits and minimizing the risk of electrical breakdown, insulation enhances the overall reliability of the electronic device.
-
Environmental Protection: PCB insulation materials and techniques provide a barrier against environmental factors such as moisture, dust, and chemicals. This protection helps to prevent corrosion, degradation, and premature failure of the PCB and its components.
-
High-Voltage Applications: In applications involving high voltages, proper insulation is critical to prevent electrical arcing and ensure the safety of the device and its users. Insulation materials with high dielectric strength are used to withstand the high voltages and prevent breakdown.
-
Thermal Management: Some insulation materials, such as ceramic substrates, offer excellent thermal conductivity. This property helps to dissipate heat generated by electronic components, preventing overheating and ensuring the stable operation of the device.
Challenges in PCB Insulation
While PCB insulation is crucial, it also presents certain challenges that must be addressed during the design and manufacturing process:
-
Material Selection: Choosing the right insulation material requires careful consideration of the specific application requirements, such as operating temperature, environmental conditions, and electrical properties. Balancing performance, cost, and manufacturability is essential.
-
Manufacturing Complexity: Applying insulation materials and techniques can add complexity to the PCB manufacturing process. Ensuring proper coverage, thickness, and adhesion of insulation layers requires precise control and specialized equipment.
-
Miniaturization: As electronic devices continue to shrink in size, maintaining adequate insulation becomes more challenging. Smaller spacing between traces and components requires advanced insulation techniques and materials to prevent signal interference and short circuits.
-
High-Frequency Applications: In high-frequency applications, insulation materials with low dielectric constant and dissipation factor are crucial to minimize signal loss and maintain signal integrity. Selecting materials that can handle high frequencies while providing effective insulation is a key consideration.
-
Cost Considerations: Implementing advanced insulation materials and techniques can increase the overall cost of PCB production. Balancing the need for high-performance insulation with cost-effectiveness is a challenge that manufacturers must navigate.
Frequently Asked Questions (FAQ)
-
What is the most commonly used PCB insulation material?
FR-4, a glass-reinforced epoxy laminate, is the most widely used PCB insulation material. It offers a good balance of electrical insulation properties, mechanical strength, and cost-effectiveness. -
Can PCB insulation materials withstand high temperatures?
Yes, certain insulation materials, such as polyimide and ceramic, are specifically designed to withstand high temperatures. They are used in applications that require operation in extreme thermal conditions. -
What is the purpose of solder mask on a PCB?
Solder mask serves as an insulating layer applied to the surface of a PCB. It covers the copper traces while leaving the pads exposed, preventing accidental short circuits during soldering and protecting the traces from environmental factors. -
How does conformal coating enhance PCB insulation?
Conformal coating is a thin layer of insulating material applied to the surface of a PCB. It provides additional protection against moisture, dust, and other contaminants, enhancing the overall insulation and reliability of the PCB. -
Why is maintaining appropriate clearance and creepage distances important for PCB insulation?
Maintaining appropriate clearance and creepage distances is crucial for preventing electrical breakdown and ensuring proper insulation. Clearance refers to the shortest distance through air between two conductive parts, while creepage is the shortest distance along the surface of the insulating material between two conductive parts. Adequate spacing helps to prevent short circuits and maintains the integrity of the electrical signals.
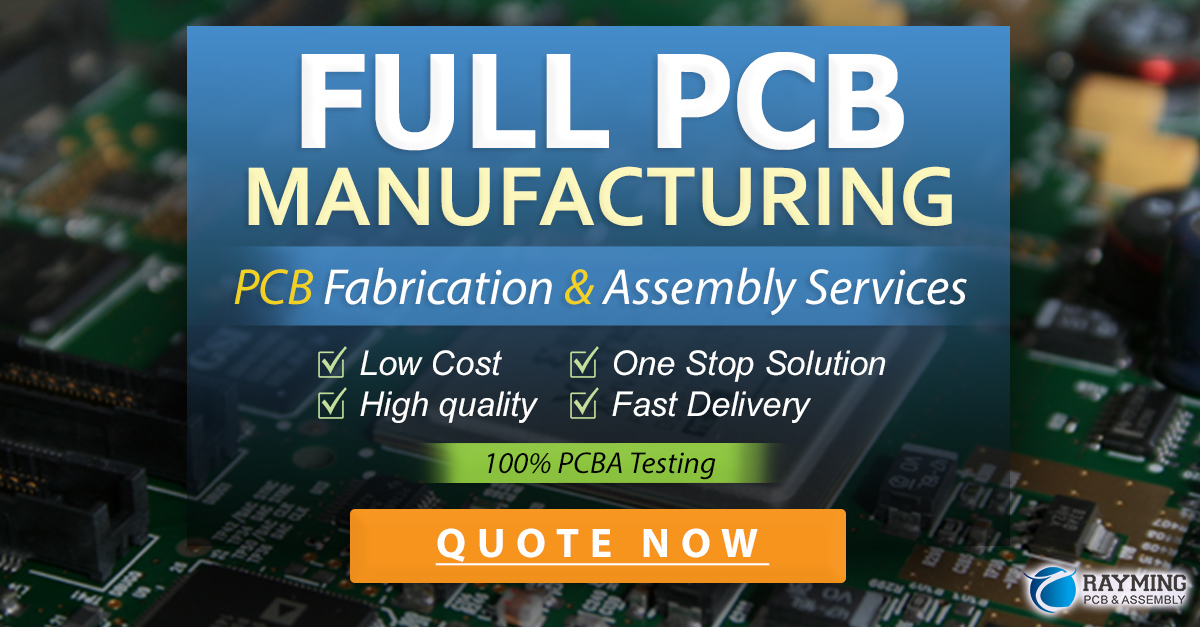
Conclusion
PCB insulation is a vital aspect of PCB production that ensures the proper functioning, reliability, and safety of electronic devices. By selecting appropriate insulation materials and employing effective insulation techniques, manufacturers can mitigate the risks of short circuits, signal interference, and environmental damage.
As technology advances and electronic devices become more complex, the importance of PCB insulation continues to grow. Designers and manufacturers must stay updated with the latest insulation materials and techniques to meet the evolving demands of the industry.
By understanding the principles of PCB insulation, selecting the right materials, and implementing proper insulation techniques, manufacturers can produce high-quality PCBs that deliver optimal performance and reliability. Investing in effective PCB insulation is an essential step towards creating robust and dependable electronic devices that meet the needs of today’s technology-driven world.
Leave a Reply