Introduction to SMT-BGA Assembly
Surface Mount Technology (SMT) has revolutionized the electronics manufacturing industry by enabling the production of smaller, faster, and more reliable electronic devices. One of the most critical components in SMT assembly is the Ball Grid Array (BGA) package. BGA components are widely used in various applications, including smartphones, laptops, gaming consoles, and medical devices, due to their high density and superior performance.
In this article, we will discuss the key points of the SMT assembly process for BGA components, including the challenges, best practices, and quality control measures.
What is SMT-BGA?
SMT-BGA refers to the process of assembling Ball Grid Array components using Surface Mount Technology. BGA packages have a grid of solder balls on the bottom side, which are used to connect the component to the printed circuit board (PCB). The solder balls are arranged in a matrix pattern, allowing for a high density of interconnects in a small area.
Advantages of SMT-BGA Assembly
- Higher density of interconnects compared to other package types
- Better thermal and electrical performance
- Reduced signal noise and improved signal integrity
- Smaller footprint and lower profile
- Suitable for high-speed and high-frequency applications
Challenges in SMT-BGA Assembly
Thermal Management
One of the primary challenges in SMT-BGA assembly is thermal management. BGA components generate a significant amount of heat during operation, which can lead to thermal stress and damage to the package and PCB. Proper thermal management is essential to ensure the reliability and longevity of the assembled device.
Warpage and Coplanarity
BGA packages are susceptible to warpage and coplanarity issues due to their large size and high pin count. Warpage occurs when the package deforms due to thermal stress, while coplanarity refers to the flatness of the solder balls. These issues can lead to poor solder joints and reduced reliability.
Solder Joint Reliability
Ensuring the reliability of solder joints is crucial in SMT-BGA assembly. Solder joint failures can occur due to various factors, such as thermal cycling, mechanical stress, and contamination. Proper process control and quality inspection are necessary to minimize the risk of solder joint failures.
SMT-BGA Assembly Process
PCB Design Considerations
The PCB design plays a critical role in the success of SMT-BGA assembly. Some key considerations include:
- Proper Land Pattern Design to ensure good solder joint formation
- Adequate clearance between components to facilitate inspection and rework
- Thermal management features, such as thermal vias and heat spreaders
- Controlled impedance routing for high-speed signals
Solder Paste Printing
Solder paste printing is the first step in the SMT-BGA assembly process. The solder paste, which consists of tiny solder spheres suspended in a flux matrix, is deposited onto the PCB using a stencil. The stencil has openings that match the land pattern of the BGA component, allowing for precise control of the solder paste volume.
Parameter | Typical Value |
---|---|
Solder Paste Type | Type 3 or Type 4 |
Stencil Thickness | 0.1 mm to 0.15 mm |
Aperture Size | 80% to 90% of pad size |
Print Speed | 25 mm/s to 50 mm/s |
Print Pressure | 0.2 kg to 0.4 kg per cm of blade length |
Component Placement
After solder paste printing, the BGA component is placed onto the PCB using a pick-and-place machine. The machine uses vision systems to align the component with the land pattern and places it with high accuracy. Proper placement is critical to ensure good solder joint formation and prevent component shifting during reflow.
Reflow Soldering
Reflow soldering is the process of melting the solder paste and forming solder joints between the BGA component and the PCB. The assembled PCB is passed through a reflow oven, which follows a specific temperature profile to melt the solder and form reliable joints. The reflow profile must be carefully controlled to ensure proper solder joint formation and prevent thermal damage to the components.
A typical reflow profile for lead-free solder consists of the following stages:
- Preheat: The assembled PCB is gradually heated to activate the flux and remove moisture.
- Soak: The temperature is maintained to ensure even heating and flux activation.
- Reflow: The temperature is raised above the melting point of the solder to form solder joints.
- Cooling: The PCB is cooled down to solidify the solder joints.
Stage | Temperature Range | Time |
---|---|---|
Preheat | 150°C to 180°C | 60 to 120 seconds |
Soak | 180°C to 200°C | 60 to 120 seconds |
Reflow | 235°C to 250°C | 30 to 90 seconds |
Cooling | Below 100°C | 30 to 60 seconds |
Inspection and Testing
After reflow soldering, the assembled PCB undergoes inspection and testing to ensure the quality and reliability of the solder joints. Common inspection methods include:
- Visual inspection: Manual or automated visual inspection to check for solder joint defects, such as bridging, insufficient solder, or voids.
- X-ray inspection: Non-destructive inspection using X-rays to detect internal solder joint defects, such as voids or cracks.
- Boundary scan testing: Functional testing of the assembled PCB using built-in test features of the components.
- Electrical testing: Verification of the electrical performance and functionality of the assembled PCB.
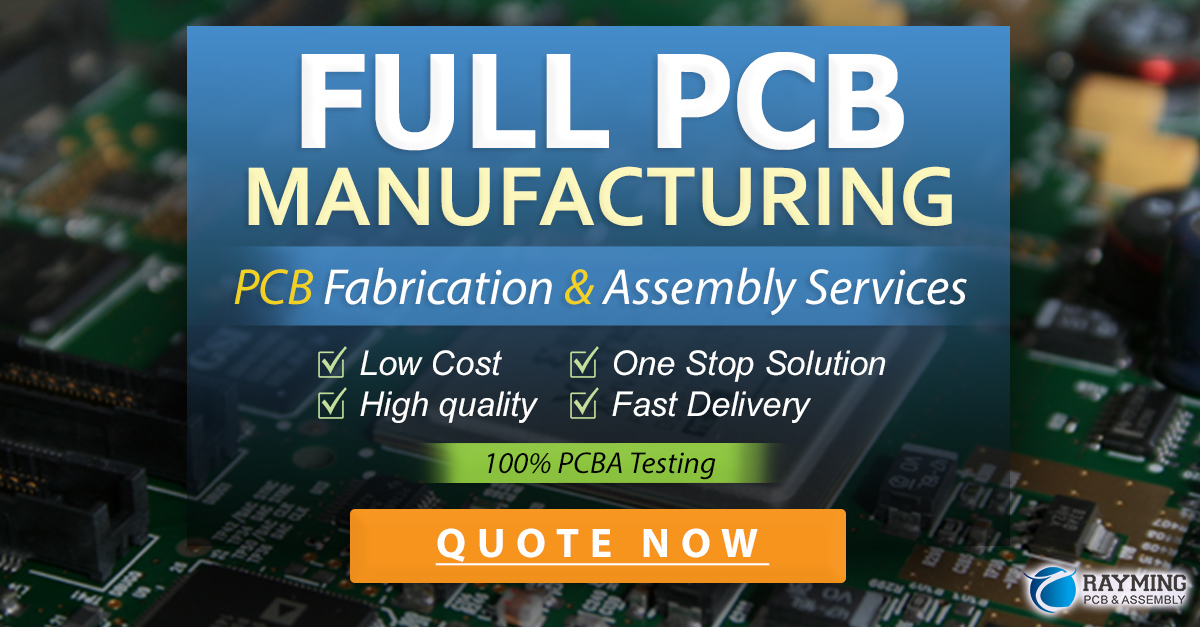
Best Practices for SMT-BGA Assembly
Process Control
Implementing strict process control measures is essential to ensure consistent and reliable SMT-BGA assembly. Some key process control practices include:
- Monitoring and controlling the solder paste printing process to ensure consistent solder paste deposition.
- Regularly calibrating and maintaining the pick-and-place machine to ensure accurate component placement.
- Monitoring and controlling the reflow oven temperature profile to ensure proper solder joint formation.
- Implementing statistical process control (SPC) to monitor and control process parameters.
Moisture Management
BGA components are sensitive to moisture absorption, which can lead to package cracking during reflow soldering. Proper moisture management is essential to prevent moisture-related defects. Some best practices include:
- Storing BGA components in moisture-barrier bags with desiccants.
- Baking BGA components before assembly to remove absorbed moisture.
- Monitoring the humidity levels in the storage and assembly areas.
- Following the component manufacturer’s guidelines for moisture sensitivity level (MSL) and floor life.
Handling and Storage
Proper handling and storage of BGA components and assembled PCBs are critical to preventing damage and contamination. Some best practices include:
- Using ESD-safe handling procedures and equipment to prevent electrostatic discharge damage.
- Storing components and PCBs in a clean, dry, and temperature-controlled environment.
- Avoiding mechanical stress or shock during handling and transportation.
- Using appropriate packaging materials to protect the components and PCBs during storage and shipping.
Quality Control and Inspection
Implementing a robust quality control and inspection program is essential to ensure the reliability and performance of the assembled PCBs. Some key quality control measures include:
- Performing incoming inspection of BGA components and PCBs to ensure conformance to specifications.
- Conducting in-process inspections during solder paste printing, component placement, and reflow soldering to identify and correct defects early in the process.
- Performing post-assembly inspections, such as visual inspection, X-ray inspection, and electrical testing, to verify the quality and functionality of the assembled PCBs.
- Implementing a failure analysis process to identify the root causes of defects and implement corrective actions.
Frequently Asked Questions (FAQ)
- What is the difference between BGA and QFN packages?
- BGA packages have a grid of solder balls on the bottom side, while QFN (Quad Flat No-lead) packages have flat contact pads on the bottom side.
- BGA packages have a higher pin count and density compared to QFN packages.
-
BGA packages are more suitable for high-speed and high-frequency applications, while QFN packages are more suitable for low-cost and low-power applications.
-
Can BGA components be reworked?
- Yes, BGA components can be reworked using specialized equipment and techniques.
- Rework involves removing the defective component, cleaning the PCB pads, and replacing it with a new component.
-
Proper rework procedures and equipment are essential to prevent damage to the PCB and ensure reliable solder joints.
-
What is the purpose of underfill in BGA assembly?
- Underfill is an epoxy material that is applied between the BGA component and the PCB after reflow soldering.
- Underfill provides mechanical support and reduces thermal stress on the solder joints, improving reliability.
-
Underfill is commonly used in applications with high thermal cycling or mechanical stress, such as automotive and aerospace electronics.
-
How can voids in BGA solder joints be minimized?
- Voids in BGA solder joints can be minimized by optimizing the solder paste printing process, including the stencil design, aperture size, and print parameters.
- Using a vacuum reflow oven can help reduce voids by removing trapped air during soldering.
-
Proper control of the reflow profile, including the ramp rate, peak temperature, and cooling rate, can also help minimize voids.
-
What is the role of flux in SMT-BGA assembly?
- Flux is a chemical compound that is added to the solder paste to remove oxides and contaminants from the metal surfaces during soldering.
- Flux promotes wetting and spreading of the solder, enabling the formation of reliable solder joints.
- The type of flux used in SMT-BGA assembly depends on the solder alloy, PCB surface finish, and cleaning requirements.
Conclusion
SMT-BGA assembly is a critical process in the production of high-performance electronic devices. Proper understanding of the challenges, best practices, and quality control measures is essential to ensure reliable and consistent assembly. By following the guidelines discussed in this article, manufacturers can optimize their SMT-BGA assembly process and produce high-quality electronic products.
As the electronics industry continues to evolve, the demand for smaller, faster, and more reliable devices will continue to drive the adoption of advanced packaging technologies like BGA. Staying up-to-date with the latest advancements in SMT-BGA assembly and implementing best practices will be crucial for manufacturers to remain competitive in the market.
Leave a Reply