Introduction
Rigid circuit boards, also known as printed circuit boards (PCBs), are essential components in nearly all modern electronic devices. A rigid circuit board provides a flat surface onto which integrated circuits and other electronic components can be mounted and connected together with conductive traces. The rigidity of the board provides mechanical support and protection for the components. In this article, we will explore the key features and manufacturing processes of rigid circuit boards, examine their critical role in electronics, and highlight some of the latest innovations in PCB technology.
What are Rigid Circuit Boards?
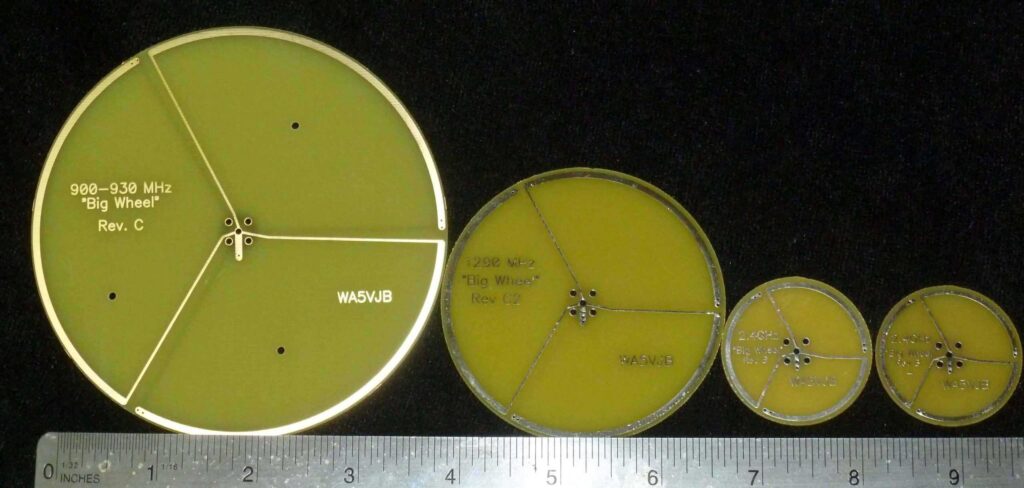
A rigid circuit board is typically made from layers of fiberglass and copper foil laminated together. The fiberglass provides the structural rigidity and mechanical support, while the copper foil is etched into conductive traces that connect the various mounted components. Here are some key features of rigid PCBs:
- Flat surface – Creates a sturdy, flat foundation for mounting components
- Conductive traces – Etched copper tracks that transmit signals between components
- Plated holes – Via holesallow connections between layers
- Solder mask – Prevent solder bridges between traces
- Silkscreen – Component markings and labels printed on the board
Rigid boards can have from 1 to over 30 conductive layers laminated together depending on the complexity of the circuit design. Multilayer boards allow for greater circuit density.
Manufacturing Processes
There are several steps involved in manufacturing a rigid PCB:
1. Design
The board layout is designed in CAD software indicating trace routes, hole locations, layer stackup, and more.
2. Etching
The conductive copper layers are etched to form the traces that connect components.
3. Drilling
Holes are drilled for component leads and vias. The holes are then plated with copper.
4. Lamination
The etched, drilled layers are laminated together under heat and pressure.
5. Solder mask
A layer of epoxy solder mask is applied to prevent solder bridges.
6. Silkscreen
Component outlines and identifiers are silkscreen printed onto the board.
7. Testing
Each completed board is electrically tested.
8. Population
Components are soldered onto the finished board.
Importance in Modern Electronics
Rigid circuit boards are vital components found in practically every modern electronic device including:
- Computers
- Smartphones
- Home appliances
- Automobiles
- Medical equipment
- Industrial machinery
Without rigid boards, electronic devices would be far larger as all connections would need to be made via individual wires. Rigid boards allow for the dense, compact packaging of components that enables the miniaturization of modern electronics.
Some key benefits provided by rigid PCBs:
- Compact – Allows high component density
- Reliable – Provides sturdy mechanical support
- Efficient – Short, optimized trace routing
- Repeatable – Manufacturing can be standardized
- Customizable – Can be designed for specific applications
Rigid boards are a ubiquitous platform at the core of electronics today.
Latest Innovations
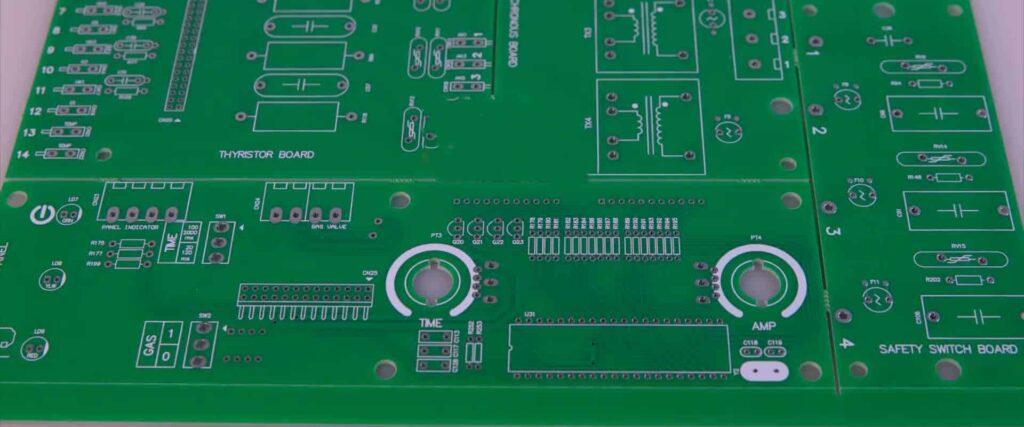
While the fundamental technology of rigid boards has remained relatively unchanged, there have been some notable improvements in PCBs:
- HDI – High density interconnect with tighter trace spacing and via pitches.
- Embedded passives – Passive components like resistors embedded into the circuit board.
- Flex/rigid – Combines rigid boards with flexible circuits.
- Miniaturization – Boards continuously shrinking in size.
- High speed – Innovation in materials to reduce signal loss at high frequencies.
- Thermal management – Improved copper ground planes dissipate heat efficiently.
Here are a few examples of innovative rigid circuit board applications:
Application | Description |
---|---|
Smartphones | Multilayer HDI boards in ultrathin, compact form factors. |
Automotive | High reliability boards in engine control units and infotainment systems. |
IoT devices | Tiny, flexible/rigid boards powering edge nodes. |
High speed data | Low loss materials enable over 50 Gbps data rates. |
The Future of Rigid Boards
Rigid circuit boards will continue improving as electronic devices get faster, smaller, and more complex. Key trends driving PCB advancement include:
- Dimension reduction enabling further miniaturization.
- Higher densities with smaller features and spacing.
- Faster speeds with signal integrity improvements.
- Greater reliability for safety-critical applications.
- Lower costs through optimized, automated manufacturing.
Rigid boards have been a foundational technology over the past 50+ years of electronics, and will continue propelling innovation into the future.
Frequently Asked Questions
What are the standard sizes of rigid circuit boards?
Some common standard sizes are 160mm x 100mm, 220mm x 150mm, and 233mm x 191mm. However, boards can be manufactured in virtually any custom size.
How are components mounted onto a rigid board?
Components are mostly mounted by soldering their leads or termination pads onto the conductive traces on the board surface. Some components are pressed into plated through-holes.
What materials are used to make rigid boards?
The core material is typically fiberglass or other rigid insulating layers. Copper foils form the conductive traces. The layers are bonded with epoxy resin.
Can rigid boards be interconnected together?
Yes, individual rigid boards can be joined together either by high density board-to-board connectors or using flexible circuit board interconnects.
Are rigid circuit boards environmentally friendly?
Rigid PCBs use highly recyclable materials like fiberglass, copper and tin. Many manufacturers follow green initiatives to minimize waste and energy usage.
Leave a Reply