What is a Tachometer?
A tachometer is a device that measures the rotational speed of an object, typically expressed in revolutions per minute (RPM). It is commonly used in vehicles to display the engine’s RPM, helping drivers optimize gear changes and avoid exceeding the engine’s safe operating limits. Tachometers also find applications in industrial settings, such as monitoring the speed of motors, turbines, and conveyors.
Types of Tachometers
There are several types of tachometers, each with its own working principle and application:
-
Mechanical Tachometers: These tachometers use a rotating cable connected to the engine’s crankshaft. The cable drives a needle on a dial, indicating the RPM. Mechanical tachometers are simple and reliable but can be less accurate than electronic counterparts.
-
Electrical Tachometers: Electrical tachometers work by measuring the frequency of electrical pulses generated by the engine’s ignition system. They are more accurate than mechanical tachometers and are commonly found in modern vehicles.
-
Optical Tachometers: Optical tachometers use a light source and a sensor to detect the rotation of a shaft or disk. They are non-contact devices, making them suitable for measuring the speed of delicate or inaccessible components.
-
Stroboscopic Tachometers: These tachometers use a strobe light synchronized with the rotation of the object. By adjusting the strobe frequency until the object appears stationary, the RPM can be determined. Stroboscopic tachometers are highly accurate and useful for measuring high rotational speeds.
How a Tachometer Circuit Works
A tachometer circuit typically consists of the following components:
-
Sensor: The sensor detects the rotation of the object and generates electrical pulses. Common sensors include Hall Effect Sensors, optical sensors, and inductive sensors.
-
Signal Conditioning: The sensor output is often a weak or noisy signal that requires conditioning. This stage may include amplification, filtering, and pulse shaping to produce a clean and stable signal.
-
Frequency to Voltage Converter: The conditioned signal is fed into a frequency to voltage converter (FVC) circuit. The FVC converts the frequency of the input pulses into a corresponding voltage level.
-
Display: The output voltage from the FVC is used to drive a display, such as an analog meter or a digital readout. The display is calibrated to show the RPM based on the voltage level.
Here’s a block diagram of a typical tachometer circuit:
graph LR
A[Sensor] --> B[Signal Conditioning]
B --> C[Frequency to Voltage Converter]
C --> D[Display]
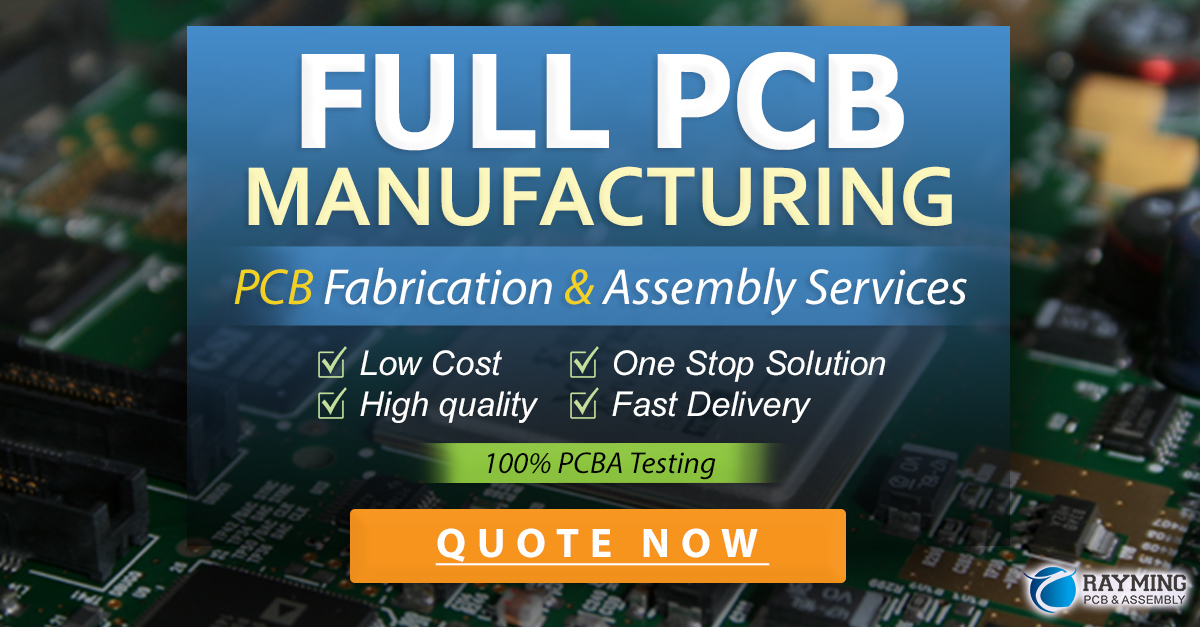
Designing a Tachometer Circuit
Now that we understand the basic components of a tachometer circuit let’s walk through the process of designing one.
Step 1: Sensor Selection
Choose a suitable sensor based on your application. For this example, we’ll use a Hall effect sensor, which detects the magnetic field of a rotating magnet attached to the shaft.
Step 2: Signal Conditioning
The Hall effect sensor output is a series of pulses whose frequency is proportional to the rotational speed. We need to condition this signal to remove noise and ensure compatibility with the FVC.
-
Amplification: Use an operational amplifier to amplify the sensor output to a suitable level.
-
Filtering: Implement a low-pass filter to remove high-frequency noise.
-
Pulse Shaping: Use a Schmitt trigger to convert the filtered signal into clean, square pulses.
Step 3: Frequency to Voltage Converter
The heart of the tachometer circuit is the FVC. It converts the frequency of the conditioned pulses into a corresponding voltage level. There are several ways to implement an FVC, but we’ll use a simple RC circuit and a diode for this example.
- The input pulses charge a capacitor through a resistor.
- The diode prevents the capacitor from discharging between pulses.
- The voltage across the capacitor increases with the frequency of the input pulses.
Here’s a schematic of a basic FVC circuit:
+-----|>|-----+
| |
Input---+ +---Output
| |
+----/\/\----+
R C
Step 4: Display
The output voltage from the FVC can be used to drive various displays, such as:
-
Analog Meter: Use a moving-coil meter with a suitable scale to display the RPM.
-
Digital Readout: Use an analog-to-digital converter (ADC) and a microcontroller to display the RPM on a digital display, such as an LCD or a 7-Segment Display.
Step 5: Calibration
Calibrate the tachometer circuit by measuring the output voltage at known rotational speeds and adjusting the components accordingly. This step ensures accurate RPM readings.
Building a Tachometer Circuit
Now that we have designed the tachometer circuit let’s build a prototype using readily available components.
Components Required
- Hall effect sensor (e.g., SS441A)
- Operational amplifier (e.g., LM358)
- Resistors and capacitors
- Diode (e.g., 1N4148)
- Analog meter or digital display
- Breadboard and jumper wires
Circuit Diagram
Here’s a simplified circuit diagram of the tachometer:
+5V
|
+-+
| |
| | R1
| |
+-+
|
Sensor ---+--- Amplifier --- Filter --- Schmitt Trigger --- FVC --- Display
|
+-+
| |
| | R2
| |
+-+
|
GND
Assembly Instructions
- Connect the Hall effect sensor to the breadboard, with its output pin connected to the non-inverting input of the operational amplifier.
- Configure the operational amplifier as a non-inverting amplifier using resistors R1 and R2. Choose the resistor values to achieve the desired gain.
- Implement the low-pass filter and Schmitt trigger using additional resistors and capacitors.
- Build the FVC circuit using a resistor, capacitor, and diode.
- Connect the FVC output to the display (analog meter or digital readout).
- Power the circuit with a suitable voltage source (e.g., 5V).
Testing and Calibration
- Attach a magnet to a rotating object (e.g., a motor shaft) and position the Hall effect sensor near it.
- Rotate the object at known speeds and measure the output voltage of the FVC.
- Adjust the FVC components (resistor and capacitor values) to achieve the desired voltage range.
- Calibrate the display to show the correct RPM based on the FVC output voltage.
Applications and Enhancements
The tachometer circuit described in this article serves as a basic foundation for various applications. You can enhance the circuit by:
- Adding a microcontroller for more advanced processing and control.
- Implementing wireless data transmission for remote monitoring.
- Integrating the tachometer with other sensors (e.g., temperature, vibration) for comprehensive machine health monitoring.
Frequently Asked Questions (FAQ)
-
Q: Can I use other types of sensors with this tachometer circuit?
A: Yes, you can use various sensors, such as optical or inductive sensors, with appropriate modifications to the signal conditioning stage. -
Q: How do I choose the right display for my tachometer?
A: The choice of display depends on your application and preferences. Analog meters are simple and intuitive, while digital displays offer more precision and flexibility. -
Q: Can I measure very high rotational speeds with this circuit?
A: The maximum measurable speed depends on the sensor and FVC characteristics. By using high-speed sensors and optimizing the FVC design, you can measure speeds up to several thousand RPM. -
Q: How can I improve the accuracy of the tachometer?
A: Accuracy can be improved by using high-quality sensors, implementing robust signal conditioning, and carefully calibrating the circuit. Additionally, using a microcontroller with advanced algorithms can enhance accuracy. -
Q: Can I power the tachometer circuit from a battery?
A: Yes, you can power the circuit from a battery with a suitable voltage regulator. Ensure that the battery capacity is sufficient for your application’s power requirements and duration.
Conclusion
In this article, we explored the working principles of a tachometer circuit and provided a step-by-step guide on how to design and build one. By understanding the sensor, signal conditioning, frequency to voltage converter, and display stages, you can create a functional tachometer for various applications.
Remember to choose the appropriate components, follow the assembly instructions, and calibrate the circuit for accurate RPM measurements. With the knowledge gained from this article, you can further enhance the tachometer circuit to suit your specific needs and integrate it into more complex systems for monitoring and control purposes.
Happy tinkering!
Leave a Reply