What is FR4?
FR4 is a composite material made from woven fiberglass cloth with an epoxy resin binder. The “FR” in FR4 stands for “Flame Retardant,” indicating its ability to resist the spread of flames. The “4” represents the woven glass reinforcement used in the material.
Composition of FR4
FR4 is composed of two main components:
- Woven fiberglass cloth
- Epoxy resin binder
The fiberglass cloth provides strength and stability to the material, while the epoxy resin binds the glass fibers together and gives the material its insulating properties.
Properties of FR4
FR4 has several key properties that make it an ideal choice for various applications in the electronics industry.
Mechanical Properties
FR4 exhibits excellent mechanical properties, including:
- High tensile strength
- Good flexural strength
- Dimensional stability
- Impact resistance
These properties make FR4 suitable for applications that require durability and resistance to mechanical stress.
Electrical Properties
FR4 is an excellent electrical insulator, with the following properties:
- High dielectric strength
- Low dielectric constant
- Low dissipation factor
These properties make FR4 ideal for use in printed circuit boards (PCBs) and other electrical applications.
Thermal Properties
FR4 has good thermal properties, including:
- Flame retardancy
- Heat resistance
- Low thermal expansion
These properties allow FR4 to withstand high temperatures and resist the spread of flames, making it suitable for applications where fire safety is a concern.
Chemical Resistance
FR4 is resistant to a wide range of chemicals, including:
- Acids
- Alkalis
- Solvents
- Oils
This chemical resistance makes FR4 suitable for use in harsh environments and applications where exposure to chemicals is likely.
Manufacturing Process of FR4
The manufacturing process of FR4 involves several steps:
- Impregnation: The woven fiberglass cloth is impregnated with the epoxy resin.
- Layup: The impregnated cloth is layered and stacked to the desired thickness.
- Pressing: The layered material is pressed under high temperature and pressure to cure the epoxy resin and bond the layers together.
- Cutting: The cured FR4 sheet is cut to the desired size and shape.
- Drilling: Holes are drilled in the FR4 sheet as required for the specific application.
- Finishing: The FR4 piece undergoes various finishing processes, such as sanding, plating, or painting, depending on the application requirements.
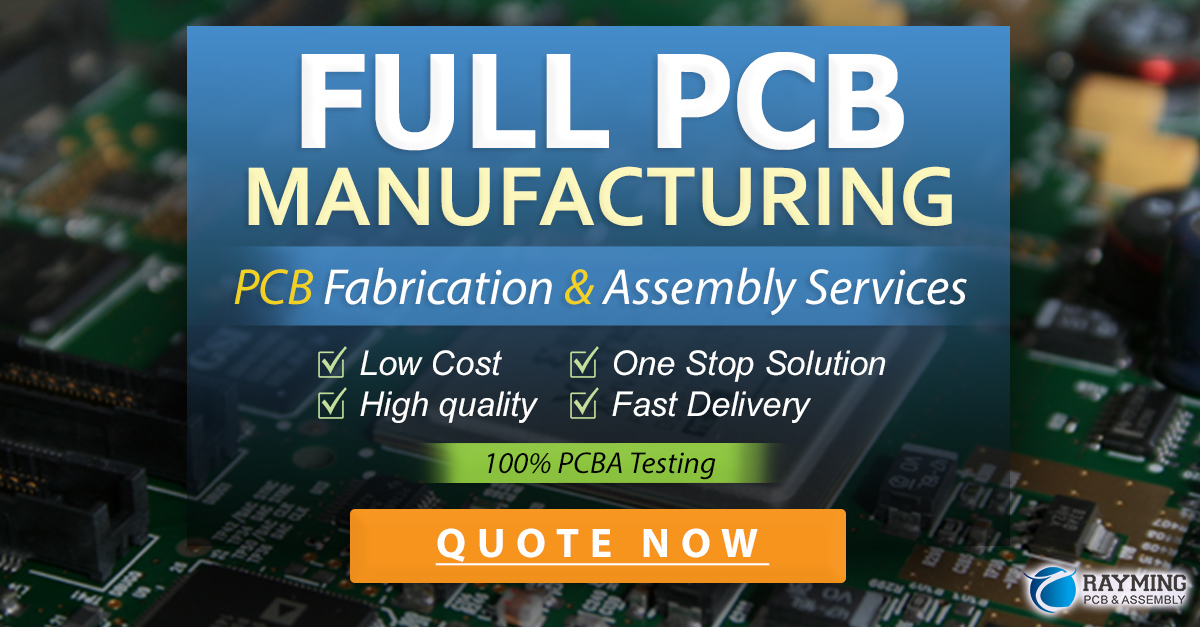
Applications of FR4
FR4 finds use in a wide range of applications, primarily in the electronics industry.
Printed Circuit Boards (PCBs)
FR4 is the most common substrate material for PCBs due to its excellent electrical insulation properties and dimensional stability. PCBs made from FR4 are used in:
- Consumer electronics
- Automotive electronics
- Industrial control systems
- Telecommunications equipment
Electrical Insulation
FR4 is used as an electrical insulator in various applications, such as:
- Transformers
- Motors
- Generators
- Switchgear
Structural Components
FR4 is used to make structural components that require high strength and dimensional stability, such as:
- Aerospace components
- Automotive parts
- Machine parts
- Tools and fixtures
Advantages of FR4
FR4 offers several advantages over other materials:
- Excellent electrical insulation properties
- High mechanical strength and dimensional stability
- Good thermal and chemical resistance
- Flame retardancy
- Versatility in applications
- Cost-effectiveness
These advantages make FR4 a popular choice for a wide range of applications in various industries.
Disadvantages of FR4
Despite its many advantages, FR4 has some limitations:
- Limited high-frequency performance due to its relatively high dielectric constant and dissipation factor
- Susceptibility to moisture absorption, which can affect its electrical and mechanical properties
- Lower thermal conductivity compared to metal substrates, which can limit its use in high-power applications
These limitations should be considered when selecting FR4 for a specific application.
FR4 vs. Other Materials
FR4 is often compared to other materials used in similar applications, such as:
- Aluminum: FR4 has better electrical insulation properties but lower thermal conductivity than aluminum.
- Ceramics: FR4 is less brittle and more cost-effective than ceramics but has lower thermal stability.
- High-frequency laminates: FR4 is more cost-effective than high-frequency laminates but has lower performance at high frequencies.
The choice between FR4 and other materials depends on the specific requirements of the application, such as electrical performance, thermal management, and cost.
Future Trends in FR4
As the electronics industry continues to evolve, so do the requirements for materials like FR4. Some of the future trends in FR4 development include:
- Improved high-frequency performance through the use of modified epoxy resins and alternative reinforcement materials
- Enhanced thermal conductivity for better heat dissipation in high-power applications
- Increased use of eco-friendly and halogen-free flame retardants to meet environmental regulations
- Development of thinner and more flexible FR4 Laminates for use in wearable electronics and flexible circuits
These trends are driven by the ever-increasing demands for higher performance, sustainability, and miniaturization in the electronics industry.
Conclusion
FR4 is a versatile and widely used material in the electronics industry, thanks to its excellent properties and cost-effectiveness. Its combination of mechanical strength, electrical insulation, thermal resistance, and flame retardancy makes it suitable for a wide range of applications, from PCBs to structural components.
As the electronics industry continues to evolve, FR4 will likely remain a key material, with ongoing developments to improve its performance and sustainability. Understanding the properties and applications of FR4 is essential for engineers, designers, and manufacturers working in the electronics industry.
FAQ
1. What does FR4 stand for?
FR4 stands for “Flame Retardant 4,” indicating its flame-retardant properties and the use of woven glass reinforcement.
2. What are the main components of FR4?
FR4 is composed of two main components: woven fiberglass cloth and an epoxy resin binder.
3. What are some key properties of FR4?
Some key properties of FR4 include high mechanical strength, excellent electrical insulation, good thermal and chemical resistance, and flame retardancy.
4. What are the primary applications of FR4?
The primary applications of FR4 include printed circuit boards (PCBs), electrical insulation, and structural components in various industries, such as electronics, aerospace, and automotive.
5. What are some limitations of FR4?
Some limitations of FR4 include limited high-frequency performance, susceptibility to moisture absorption, and lower thermal conductivity compared to metal substrates.
Property | Value |
---|---|
Density | 1.85 g/cm³ |
Tensile Strength | 310 MPa |
Flexural Strength | 415 MPa |
Dielectric Constant (at 1 MHz) | 4.7 |
Dielectric Strength | 20 kV/mm |
Thermal Conductivity | 0.3 W/m·K |
Glass Transition Temperature (Tg) | 130-140°C |
Flammability Rating (UL 94) | V-0 |
Table 1: Key properties of FR4
Leave a Reply