What is PCB Conformal Coating?
PCB conformal coating is a protective layer applied to printed circuit boards (PCBs) to shield them from environmental factors such as moisture, dust, chemicals, and extreme temperatures. This coating acts as a barrier, preventing damage to the delicate electronic components and ensuring the long-term reliability of the PCB.
Types of PCB Conformal Coatings
There are several types of conformal coatings used in the electronics industry, each with its own unique properties and benefits:
-
Acrylic Resin: Acrylic coatings offer excellent moisture and fungal resistance, as well as good electrical insulation properties. They are easy to apply and remove, making them a popular choice for many applications.
-
Silicone Resin: Silicone coatings provide superior protection against extreme temperatures and UV exposure. They are highly flexible and have excellent dielectric properties, making them ideal for high-voltage applications.
-
Polyurethane Resin: Polyurethane coatings offer excellent abrasion and chemical resistance, as well as good moisture protection. They are also known for their durability and long-term reliability.
-
Epoxy Resin: Epoxy coatings are known for their exceptional chemical and abrasion resistance, as well as their strong adhesion to various surfaces. They provide excellent moisture and insulation properties, making them suitable for harsh environments.
-
Parylene: Parylene is a unique conformal coating that is applied through a vapor deposition process. It offers uniform coverage, excellent dielectric properties, and superior protection against moisture and chemicals.
Coating Type | Moisture Resistance | Temperature Resistance | Chemical Resistance | Dielectric Strength |
---|---|---|---|---|
Acrylic | Good | Moderate | Moderate | Good |
Silicone | Excellent | Excellent | Good | Excellent |
Polyurethane | Very Good | Good | Very Good | Good |
Epoxy | Excellent | Good | Excellent | Very Good |
Parylene | Excellent | Very Good | Excellent | Excellent |
Why is PCB Conformal Coating Important?
PCB conformal coating plays a crucial role in ensuring the reliability and longevity of electronic devices. Here are some key reasons why conformal coating is essential:
-
Protection from Moisture: Conformal coatings prevent moisture from penetrating the PCB and causing corrosion, short circuits, and other moisture-related failures.
-
Insulation and Dielectric Properties: Coatings provide electrical insulation between components, preventing short circuits and improving the overall dielectric strength of the PCB.
-
Chemical Resistance: Conformal coatings protect PCBs from exposure to harsh chemicals, such as cleaning agents, fuels, and other corrosive substances.
-
Temperature Resistance: Some coatings, like silicone and parylene, offer excellent protection against extreme temperatures, allowing PCBs to function reliably in harsh environments.
-
Mechanical Protection: Conformal coatings provide a barrier against physical damage, such as abrasion, vibration, and impact, extending the life of the PCB.
Industries that Benefit from PCB Conformal Coating
PCB conformal coating is used across a wide range of industries, including:
-
Automotive: Electronic components in vehicles are exposed to harsh conditions, such as moisture, temperature fluctuations, and vibrations. Conformal coating ensures the reliability of these components.
-
Aerospace: Aerospace applications require high reliability and protection against extreme temperatures, pressure variations, and moisture. Conformal coating is essential for ensuring the performance of electronic systems in aircraft and spacecraft.
-
Medical Devices: Medical electronics must function reliably in the presence of moisture, chemicals, and sterilization processes. Conformal coating protects these devices, ensuring patient safety and equipment longevity.
-
Industrial Electronics: Industrial environments often expose PCBs to harsh chemicals, dust, and extreme temperatures. Conformal coating is crucial for maintaining the reliability of industrial control systems, sensors, and automation equipment.
-
Consumer Electronics: While not all consumer electronics require conformal coating, devices exposed to moisture, such as smartwatches, fitness trackers, and outdoor equipment, benefit from the added protection.
Conformal Coating Application Methods
There are several methods for applying conformal coatings to PCBs, each with its own advantages and considerations:
1. Spray Coating
Spray coating is one of the most common methods for applying conformal coatings. It involves using a spray gun to atomize the coating material and apply it evenly across the PCB surface. This method is suitable for large-volume production and can accommodate a wide range of coating materials.
Advantages:
– Fast application process
– Suitable for large-volume production
– Accommodates various coating materials
– Allows for selective coating with masking
Considerations:
– Requires operator skill for consistent results
– Overspray can lead to material waste
– Masking is required for selective coating
2. Brush Coating
Brush coating involves manually applying the conformal coating using a brush. This method is simple and cost-effective, making it suitable for low-volume production, prototyping, and repair work.
Advantages:
– Low-cost and simple process
– Ideal for low-volume production and repairs
– Allows for precise application in specific areas
Considerations:
– Time-consuming for large-volume production
– Consistency depends on operator skill
– Difficult to achieve uniform thickness
3. Dip Coating
Dip coating involves immersing the PCB in a tank of conformal coating material and then slowly withdrawing it, allowing the excess coating to drip off. This method provides excellent coverage and is suitable for high-volume production.
Advantages:
– Provides complete and uniform coverage
– High-volume production capability
– Relatively simple process
Considerations:
– Requires masking for selective coating
– Excess material can accumulate in holes and crevices
– Drying time can be lengthy
4. Selective Coating
Selective coating involves applying the conformal coating only to specific areas of the PCB. This method is useful when certain components or connectors must remain uncoated. Selective coating can be achieved through various techniques, such as robotic dispensing, jet printing, or masking.
Advantages:
– Precise application to specific areas
– Eliminates the need for masking in some cases
– Reduces material waste
Considerations:
– Requires specialized equipment or masking techniques
– May be more time-consuming than full-coverage methods
Application Method | Suitable Production Volume | Masking Required | Equipment Cost |
---|---|---|---|
Spray Coating | High | Yes | Moderate |
Brush Coating | Low | No | Low |
Dip Coating | High | Yes | Moderate |
Selective Coating | Varies | Sometimes | High |
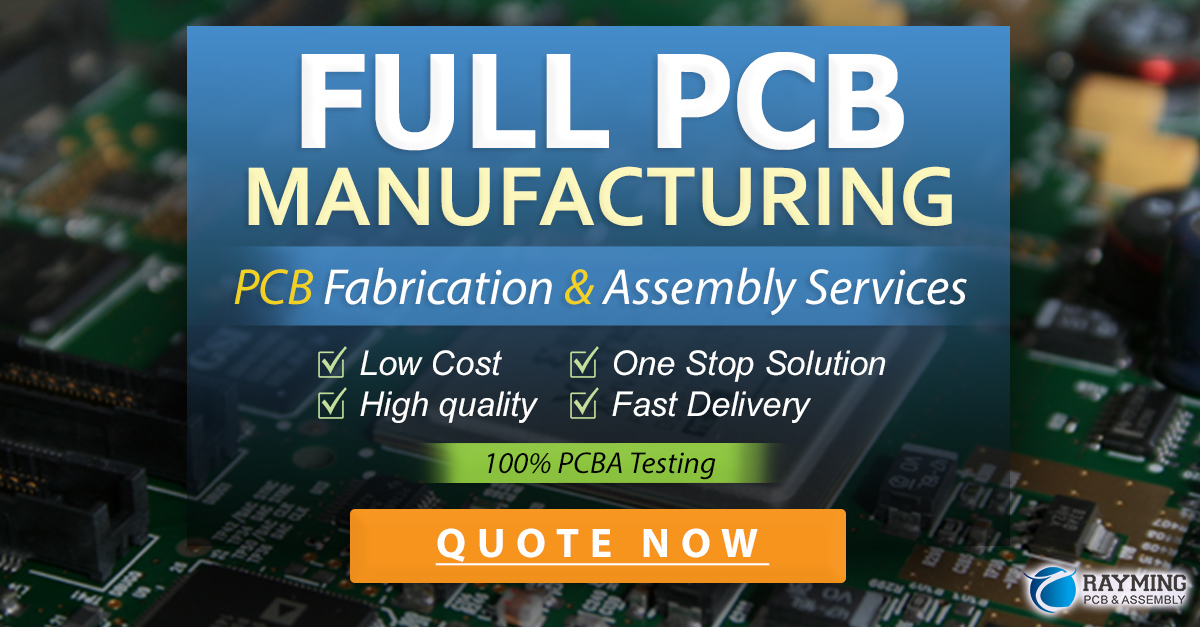
Conformal Coating Inspection and Quality Control
To ensure the effectiveness of conformal coatings, it is essential to perform thorough inspection and quality control. Some common methods for inspecting conformal coatings include:
-
Visual Inspection: A trained operator visually examines the coated PCB for defects such as pinholes, bubbles, or uneven coverage. This method is simple but subjective and may not detect all defects.
-
UV Inspection: Some conformal coatings contain UV-reactive additives that fluoresce under ultraviolet light. This allows for easy identification of coating coverage and defects.
-
Thickness Measurement: Various techniques, such as eddy current testing or ultrasonic thickness gauges, can be used to measure the thickness of the conformal coating. Ensuring consistent thickness is crucial for optimal protection.
-
Adhesion Testing: Adhesion tests, such as the cross-hatch test or the scratch test, evaluate how well the coating adheres to the PCB surface. Good adhesion is essential for long-term reliability.
-
Dielectric Withstand Testing: This test involves applying a high voltage to the coated PCB to ensure that the coating provides adequate insulation and dielectric strength.
Frequently Asked Questions (FAQ)
-
Q: Can conformal coating be removed if needed?
A: Yes, most conformal coatings can be removed using solvents or abrasive methods. However, the removal process may be time-consuming and can potentially damage the PCB if not done carefully. -
Q: How long does conformal coating take to dry?
A: Drying times vary depending on the type of coating and the application method. Some coatings may dry within minutes, while others may take several hours to fully cure. -
Q: Can conformal coating be applied to PCBs with sensitive components?
A: Yes, selective coating methods can be used to apply conformal coating only to specific areas of the PCB, avoiding sensitive components or connectors. -
Q: How does conformal coating affect PCB repair and rework?
A: Conformal coating can make PCB repair and rework more challenging, as the coating must first be removed from the affected area. However, some coatings are designed to be easily removable for such purposes. -
Q: Are there any environmental concerns with conformal coating?
A: Some conformal coating materials may contain volatile organic compounds (VOCs) or other harmful substances. It is important to follow proper safety protocols and dispose of waste materials in accordance with local regulations.
In conclusion, PCB conformal coating is a critical process for ensuring the reliability and longevity of electronic devices. By understanding the different types of coatings, application methods, and inspection techniques, engineers and manufacturers can select the best conformal coating solution for their specific needs. As electronic devices continue to advance and find applications in increasingly harsh environments, the importance of conformal coating will only continue to grow.
Leave a Reply