What is Custom Shielding?
Custom shielding refers to the process of designing and manufacturing shielding solutions tailored to specific applications or devices. Unlike off-the-shelf shielding products, custom shielding is created to meet unique requirements in terms of size, shape, material, and performance. This approach allows for optimal protection against electromagnetic interference (EMI), radio frequency interference (RFI), and other unwanted signals.
Types of Custom Shielding
There are several types of custom shielding, each with its own advantages and applications:
-
Custom EMI Shielding: Designed to protect electronic devices from electromagnetic interference, custom EMI shielding can be made from various materials, such as metal foils, conductive fabrics, and coated plastics.
-
Custom RFI Shielding: Similar to EMI shielding, custom RFI shielding focuses on protecting devices from radio frequency interference. This type of shielding is often used in wireless communication devices and military equipment.
-
Custom Magnetic Shielding: Custom magnetic shielding is designed to protect sensitive equipment from magnetic fields. It is commonly used in medical devices, scientific instruments, and high-precision manufacturing equipment.
-
Custom Thermal Shielding: Designed to protect devices from extreme temperatures, custom thermal shielding can be made from materials such as ceramics, composites, and specialized alloys.
Benefits of Custom Shielding
Custom shielding offers several advantages over off-the-shelf solutions:
-
Improved Performance: By tailoring the shielding design to the specific requirements of the application, custom shielding can provide superior protection against EMI, RFI, and other unwanted signals.
-
Cost-Effectiveness: While custom shielding may have higher upfront costs, it can be more cost-effective in the long run by reducing the need for additional shielding components or modifications.
-
Space Optimization: Custom shielding can be designed to fit the exact dimensions of the device or application, minimizing the overall footprint and optimizing space utilization.
-
Aesthetics: Custom shielding can be designed to match the aesthetic requirements of the device, ensuring a seamless integration without compromising on protection.
Designing Custom Shielding
Designing custom shielding involves several key steps:
1. Understanding the Application
The first step in designing custom shielding is to understand the specific requirements of the application. This includes:
- The type and frequency of the interference to be shielded against
- The operating environment of the device (e.g., temperature, humidity, vibration)
- The size and shape constraints of the device
- The required level of shielding effectiveness
2. Material Selection
Once the application requirements are understood, the next step is to select the appropriate shielding material. Factors to consider include:
- Conductivity and permeability of the material
- Corrosion resistance
- Mechanical properties (e.g., strength, flexibility)
- Cost and availability
Some common materials used in custom shielding include:
Material | Conductivity | Permeability | Corrosion Resistance | Flexibility |
---|---|---|---|---|
Copper | High | Low | Moderate | Moderate |
Aluminum | High | Low | High | High |
Stainless Steel | Moderate | High | High | Low |
Nickel-Copper Alloy | High | High | High | Moderate |
Conductive Plastics | Low to High | Low | High | High |
3. Design Optimization
With the material selected, the next step is to optimize the shielding design for the specific application. This involves:
- Determining the optimal thickness and shape of the shielding
- Identifying potential weak points or gaps in the shielding
- Incorporating features such as gaskets, filters, and grounding points
- Conducting simulations or testing to validate the design
4. Manufacturing and Assembly
Once the design is finalized, the custom shielding can be manufactured using various techniques, such as:
- Stamping
- Cutting
- Forming
- Welding
- Plating
The manufactured shielding components are then assembled onto the device, ensuring proper fit and functionality.
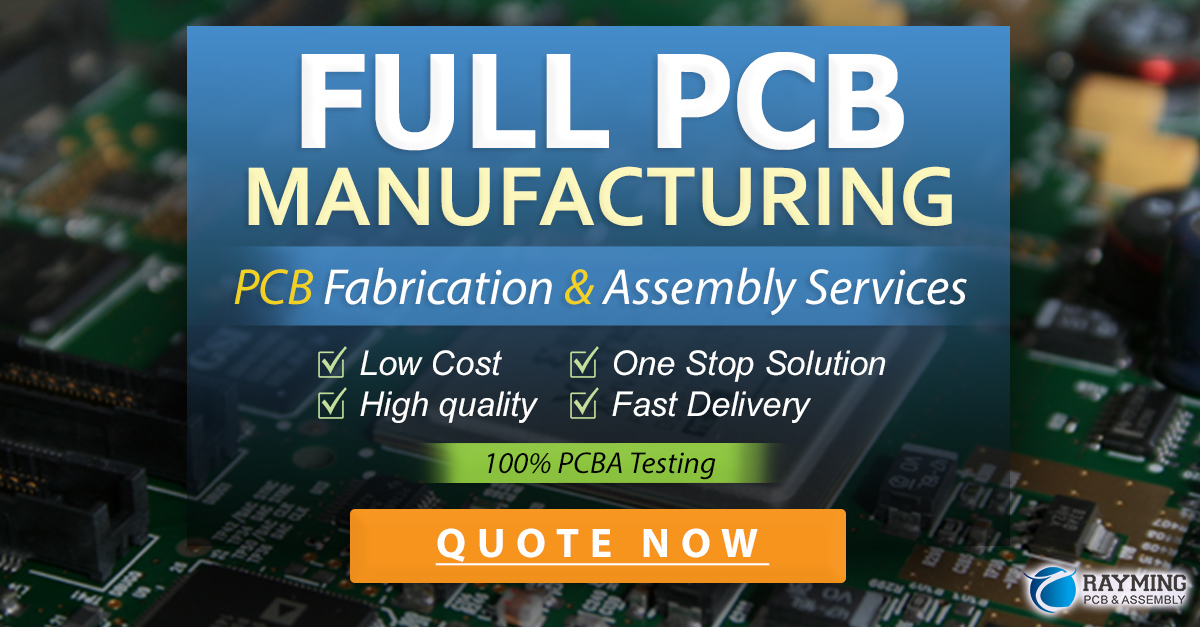
Using Custom Shielding
To maximize the effectiveness of custom shielding, it is important to follow best practices during installation and use:
1. Proper Grounding
Ensuring proper grounding is crucial for the effectiveness of custom shielding. This involves:
- Establishing a low-impedance path to ground for the shielding
- Minimizing the length of grounding connections
- Using multiple grounding points to reduce the risk of ground loops
2. Sealing and Gasketing
Sealing and gasketing are essential for preventing gaps or leaks in the shielding. This can be achieved through:
- Using conductive gaskets or adhesives at the interfaces between shielding components
- Ensuring proper compression of gaskets during assembly
- Regularly inspecting and replacing worn or damaged gaskets
3. Cable Management
Proper cable management is important for maintaining the integrity of custom shielding. This includes:
- Using shielded cables and connectors
- Minimizing the length of exposed cables
- Properly terminating and grounding cable shields
4. Maintenance and Testing
Regular maintenance and testing are essential for ensuring the long-term effectiveness of custom shielding. This involves:
- Visually inspecting the shielding for signs of damage or wear
- Conducting periodic testing to validate shielding performance
- Replacing or repairing damaged shielding components as needed
FAQ
Q1: How much does custom shielding cost compared to off-the-shelf solutions?
A1: The cost of custom shielding can vary depending on factors such as the complexity of the design, the materials used, and the manufacturing processes involved. While custom shielding may have higher upfront costs compared to off-the-shelf solutions, it can be more cost-effective in the long run by providing superior performance and reducing the need for additional shielding components or modifications.
Q2: How long does it take to design and manufacture custom shielding?
A2: The lead time for custom shielding can vary depending on the complexity of the design and the manufacturing processes involved. Typically, the design and prototyping phase can take several weeks, while the manufacturing and assembly phase can take several more weeks. It is important to factor in these lead times when planning for the integration of custom shielding into a device or application.
Q3: Can custom shielding be designed for extreme environments?
A3: Yes, custom shielding can be designed to withstand extreme environments, such as high temperatures, high humidity, or harsh chemicals. This is achieved through the selection of appropriate materials and the incorporation of specialized features, such as thermal insulation or corrosion-resistant coatings.
Q4: How do I know if my device needs custom shielding?
A4: The need for custom shielding is typically determined by the specific requirements of the device or application. If the device is sensitive to EMI, RFI, or other unwanted signals, and off-the-shelf shielding solutions are not sufficient or practical, custom shielding may be necessary. It is important to conduct a thorough analysis of the device’s requirements and operating environment to determine the appropriate shielding solution.
Q5: Can custom shielding be retrofitted to existing devices?
A5: Yes, custom shielding can be retrofitted to existing devices, although it may be more challenging than designing shielding for a new device. Retrofitting involves carefully analyzing the device’s design and identifying potential shielding integration points. In some cases, modifications to the device may be necessary to accommodate the custom shielding. It is important to work closely with a shielding expert to ensure a successful retrofit.
Conclusion
Custom shielding is a powerful tool for protecting electronic devices and sensitive equipment from EMI, RFI, and other unwanted signals. By tailoring the shielding design to the specific requirements of the application, custom shielding can provide superior performance, cost-effectiveness, and space optimization compared to off-the-shelf solutions.
When designing custom shielding, it is important to carefully consider factors such as the application requirements, material selection, and design optimization. Proper installation and use of custom shielding, including grounding, sealing, cable management, and maintenance, are also critical for ensuring long-term effectiveness.
As the complexity of electronic devices continues to increase, the demand for custom shielding solutions is likely to grow. By staying informed about the latest advancements in shielding materials and design techniques, engineers and manufacturers can stay ahead of the curve in protecting their devices from unwanted interference.
Leave a Reply