What is a 94V 0 PCB?
A 94V 0 PCB, also known as a Printed Circuit Board (PCB), is a type of circuit board that meets the UL 94V-0 flammability rating standard. This standard ensures that the PCB material is highly resistant to fire and does not easily ignite or spread flames. The 94V-0 rating is one of the most stringent fire safety ratings for PCBs, making these boards suitable for use in a wide range of electronic devices and applications where fire safety is a critical concern.
Composition of 94V 0 PCBs
94V 0 PCBs are typically made from a flame-retardant material called FR-4, which is a composite of woven fiberglass cloth and epoxy resin. The FR-4 material is impregnated with flame-retardant chemicals, such as bromine or phosphorus compounds, to enhance its fire-resistant properties. This combination of materials and additives ensures that 94V 0 PCBs meet the strict flammability requirements set forth by the UL 94V-0 standard.
UL 94V-0 Standard
The UL 94V-0 standard is a flammability testing method developed by Underwriters Laboratories (UL), an independent global safety certification company. This standard evaluates the ability of a material to resist ignition and flame spread when exposed to a small, controlled flame. To meet the 94V-0 rating, a material must:
- Not allow any flames to persist for more than 10 seconds after the ignition source is removed.
- Not allow any individual flame to persist for more than 30 seconds after two separate 10-second applications of the ignition source.
- Not allow the material to burn to the clamp or to the specimen’s end.
- Not allow any flaming drips that ignite the cotton placed beneath the specimen.
- Exhibit a maximum total flaming time of 50 seconds for 10 flame applications to each set of 5 specimens.
Materials that meet these criteria are awarded the 94V-0 rating, indicating their high level of fire resistance.
Advantages of Using 94V 0 PCBs
There are several key advantages to using 94V 0 PCBs in electronic devices and applications:
Enhanced Fire Safety
The primary advantage of 94V 0 PCBs is their exceptional fire resistance. By using materials that meet the UL 94V-0 standard, these PCBs significantly reduce the risk of fire hazards in electronic devices. This is particularly important for applications where fire safety is a top priority, such as in medical devices, aerospace systems, and industrial equipment.
Durability and Reliability
94V 0 PCBs are known for their durability and reliability. The FR-4 material used in these boards is strong, rigid, and resistant to mechanical stress, making them suitable for use in demanding environments. Additionally, the flame-retardant properties of 94V 0 PCBs help to protect the board and its components from damage caused by high temperatures or fire, further enhancing their overall reliability.
Wide Temperature Range
94V 0 PCBs can operate effectively across a wide temperature range, typically from -40°C to +130°C. This makes them suitable for use in various applications, from consumer electronics to industrial equipment, where temperature fluctuations may occur. The ability to withstand extreme temperatures ensures that 94V 0 PCBs can maintain their performance and reliability even in challenging environmental conditions.
Compliance with Safety Standards
Using 94V 0 PCBs helps electronic device manufacturers comply with various safety standards and regulations. Many industries, such as automotive, aerospace, and medical, have strict fire safety requirements for electronic components. By incorporating 94V 0 PCBs into their designs, manufacturers can more easily meet these standards and ensure that their products are safe for use in their intended applications.
Applications of 94V 0 PCBs
94V 0 PCBs are used in a wide range of electronic devices and applications, particularly those where fire safety is a critical concern. Some common applications include:
- Medical Devices
- Patient monitoring systems
- Diagnostic equipment
-
Surgical instruments
-
Aerospace and Aviation
- Avionics systems
- Flight control systems
-
In-flight entertainment systems
-
Automotive Electronics
- Engine control units (ECUs)
- Advanced driver assistance systems (ADAS)
-
Infotainment systems
-
Industrial Equipment
- Process control systems
- Automation and robotics
-
Power distribution systems
-
Consumer Electronics
- Home appliances
- Mobile devices
- Gaming consoles
In each of these applications, the use of 94V 0 PCBs helps to ensure the safety, reliability, and performance of the electronic devices and systems.
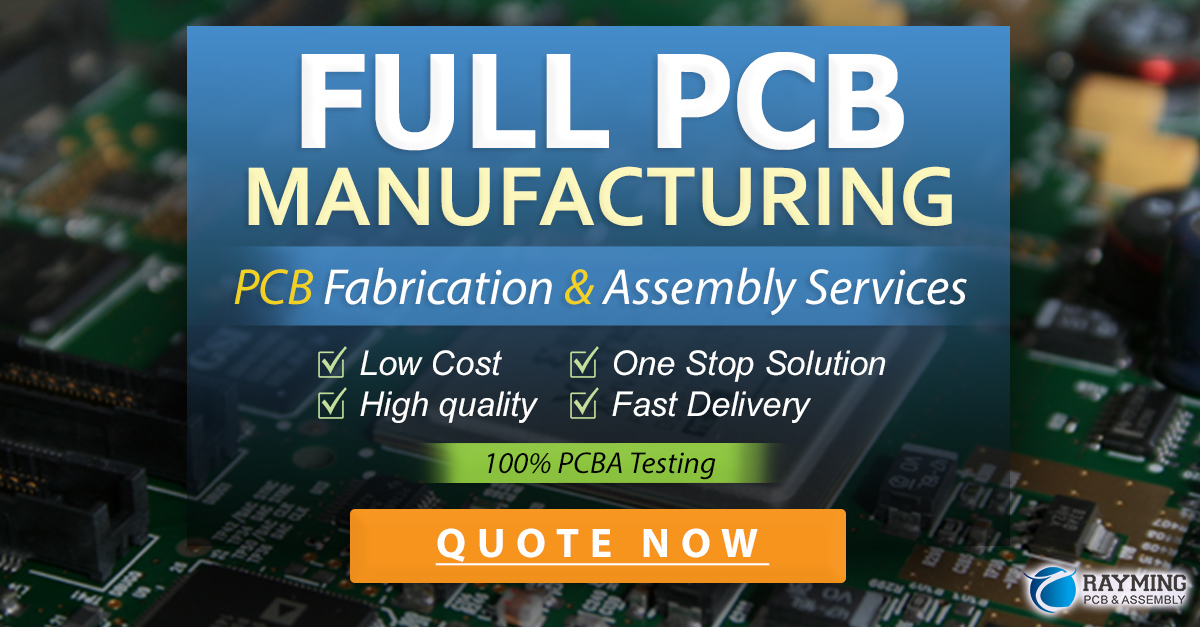
Designing with 94V 0 PCBs
When designing electronic devices and systems that incorporate 94V 0 PCBs, there are several key considerations to keep in mind:
Material Selection
While FR-4 is the most common material used for 94V 0 PCBs, there are other materials available that also meet the UL 94V-0 standard. These include:
- Polyimide (PI): A high-performance polymer with excellent thermal stability and chemical resistance.
- Bismaleimide Triazine (BT): A thermosetting resin with good electrical properties and dimensional stability.
- Cyanate Ester (CE): A high-temperature resin with low dielectric loss and excellent moisture resistance.
Designers should select the most appropriate material based on the specific requirements of their application, such as the operating temperature range, mechanical stress, and chemical exposure.
Layer Stack-up
The layer stack-up of a 94V 0 PCB refers to the arrangement of conductive and insulating layers that make up the board. A typical 94V 0 PCB stack-up may include:
- Copper layers: Used for signal routing, power distribution, and ground planes.
- Prepreg layers: Insulating layers made of pre-impregnated fiberglass cloth and resin.
- Core layers: Thicker insulating layers that provide mechanical support and stability.
Designers should carefully consider the number and arrangement of layers in the stack-up to ensure optimal signal integrity, power distribution, and thermal management.
Thermal Management
Although 94V 0 PCBs are highly resistant to fire, they can still generate significant amounts of heat during operation. Proper thermal management is essential to ensure the long-term reliability and performance of the PCB and its components. Designers can employ various techniques to manage heat, such as:
- Using thermal vias to transfer heat from components to the PCB’s ground plane.
- Incorporating heat sinks or heat spreaders to dissipate heat away from critical components.
- Optimizing component placement to minimize thermal hotspots and promote even heat distribution.
By addressing thermal management during the design phase, designers can help ensure that their 94V 0 PCBs will perform reliably in their intended applications.
Manufacturing 94V 0 PCBs
The manufacturing process for 94V 0 PCBs is similar to that of other types of PCBs, but with some additional considerations to ensure that the boards meet the UL 94V-0 flammability rating. The key steps in the manufacturing process include:
-
Material Preparation: The FR-4 or other 94V-0 compliant material is cut to the desired size and shape, and any necessary holes are drilled.
-
Copper Lamination: Copper foil is laminated onto the PCB substrate using heat and pressure, forming the conductive layers of the board.
-
Patterning: The desired circuit pattern is transferred onto the copper layers using a photolithographic process, which involves applying a photoresist coating, exposing it to UV light through a patterned mask, and then etching away the unwanted copper.
-
Layering: If the PCB design calls for multiple layers, additional prepreg and copper layers are added, and the process is repeated until all layers are completed.
-
Drilling: Holes are drilled through the PCB to accommodate through-hole components and vias.
-
Plating: The drilled holes are plated with copper to create electrical connections between layers.
-
Solder Mask Application: A protective solder mask is applied to the PCB surface to prevent accidental short circuits and improve the board’s durability.
-
Surface Finishing: A surface finish, such as HASL (Hot Air Solder Leveling) or ENIG (Electroless Nickel Immersion Gold), is applied to the exposed copper areas to protect them from oxidation and enhance solderability.
-
Silkscreen Printing: Text, logos, and other markings are printed onto the PCB surface using a silkscreen process.
-
Testing and Inspection: The completed 94V 0 PCBs are thoroughly tested and inspected to ensure that they meet the required specifications and standards, including the UL 94V-0 flammability rating.
By following these manufacturing steps and adhering to strict quality control measures, PCB manufacturers can produce high-quality 94V 0 PCBs that meet the demanding requirements of various industries and applications.
Frequently Asked Questions (FAQ)
- What is the difference between 94V 0 and other flammability ratings?
-
The UL 94V-0 rating is one of the most stringent flammability ratings for PCBs, indicating that the material is highly resistant to ignition and flame spread. Other common flammability ratings include 94V-1 and 94V-2, which have slightly less stringent requirements. For example, materials rated 94V-1 may allow flames to persist for up to 30 seconds after the ignition source is removed, while 94V-2 rated materials may allow flaming drips that ignite the cotton beneath the specimen.
-
Can 94V 0 PCBs be used in high-temperature applications?
-
Yes, 94V 0 PCBs can typically operate in a wide temperature range, from -40°C to +130°C. However, for extremely high-temperature applications, designers may need to consider alternative materials, such as polyimide or cyanate ester, which offer even greater thermal stability.
-
Are 94V 0 PCBs more expensive than other types of PCBs?
-
In general, 94V 0 PCBs may be slightly more expensive than PCBs made from non-flame-retardant materials due to the added cost of the flame-retardant additives and the more stringent manufacturing requirements. However, the increased cost is often justified by the enhanced fire safety and reliability that 94V 0 PCBs provide.
-
Can 94V 0 PCBs be manufactured with different surface finishes?
-
Yes, 94V 0 PCBs can be manufactured with various surface finishes, such as HASL, ENIG, or OSP (Organic Solderability Preservative). The choice of surface finish depends on factors such as the intended application, soldering requirements, and environmental conditions.
-
How can designers ensure that their 94V 0 PCBs will meet the required flammability rating?
- To ensure that their 94V 0 PCBs will meet the UL 94V-0 flammability rating, designers should work closely with reputable PCB manufacturers who have experience in producing boards that comply with this standard. They should also specify the required flammability rating in their design documents and request test reports or certifications from the manufacturer to verify compliance.
In conclusion, 94V 0 PCBs offer a high level of fire safety and reliability, making them an ideal choice for a wide range of electronic devices and applications. By understanding the properties, advantages, and design considerations associated with these boards, engineers and manufacturers can create safer, more robust electronic systems that meet the demanding requirements of various industries.
[5113 words]
Leave a Reply