Introduction to PCB Plating Simulation
Printed Circuit Board (PCB) manufacturing involves multiple complex processes, one of which is electroplating. Plating is crucial for ensuring reliable electrical connections, corrosion resistance, and the overall durability of the PCB. However, optimizing the plating process can be challenging due to various factors such as board geometry, material properties, and process parameters. This is where PCB Plating Simulation comes into play.
PCB Plating Simulation is an innovative tool that allows designers to virtually simulate and analyze the plating process before the actual manufacturing begins. By utilizing advanced computational methods and algorithms, this simulation technology predicts the plating thickness distribution, identifies potential issues, and helps optimize the design for improved plating uniformity and quality.
Benefits of PCB Plating Simulation
-
Cost Savings: By identifying and rectifying potential plating issues early in the design stage, PCB Plating Simulation helps avoid costly manufacturing errors and rework.
-
Time Efficiency: Simulation allows for rapid iteration and optimization of the PCB design, reducing the overall development time.
-
Quality Improvement: By predicting and minimizing plating thickness variations, simulation ensures better quality and reliability of the manufactured PCBs.
-
Design Flexibility: Plating Simulation enables designers to experiment with different materials, geometries, and process parameters to find the optimal solution.
How PCB Plating Simulation Works
Computational Methods
PCB Plating Simulation relies on advanced computational methods to model and analyze the electroplating process. Two commonly used approaches are:
-
Finite Element Analysis (FEA): FEA divides the PCB geometry into small elements and solves the governing equations for each element to predict the plating thickness distribution.
-
Boundary Element Method (BEM): BEM focuses on the surfaces of the PCB and uses integral equations to calculate the plating thickness and current density distribution.
Simulation Workflow
The typical workflow for PCB Plating Simulation involves the following steps:
-
CAD Import: The PCB design is imported from CAD software into the simulation environment.
-
Meshing: The imported geometry is discretized into small elements or boundary segments for numerical analysis.
-
Material Properties: The material properties of the PCB substrate, copper traces, and plating solution are defined.
-
Boundary Conditions: The electrical and chemical boundary conditions, such as applied voltage and concentration gradients, are specified.
-
Simulation: The computational solver calculates the plating thickness distribution and other relevant parameters.
-
Post-processing: The simulation results are visualized and analyzed to identify any plating issues or non-uniformities.
-
Optimization: Based on the simulation results, the PCB design or process parameters are modified to improve plating uniformity and quality.
Factors Affecting Plating Uniformity
Several factors can influence the uniformity of the plating thickness distribution on a PCB. These include:
Board Geometry
The shape, size, and layout of the PCB can significantly impact the plating uniformity. Features such as high aspect ratio vias, dense copper patterns, and isolated traces can lead to non-uniform current density distribution and resultant thickness variations.
Anode and Cathode Placement
The positioning of the anodes and cathodes in the plating tank affects the current distribution and, consequently, the plating uniformity. Optimal placement of the electrodes is crucial for achieving uniform plating thickness across the board.
Plating Solution Composition
The composition of the plating solution, including the concentration of metal ions, additives, and other chemicals, plays a vital role in the plating process. Variations in the solution composition can lead to non-uniform plating rates and thickness distribution.
Current Density Distribution
The current density distribution across the PCB surface directly influences the plating rate and thickness uniformity. Areas with higher current density tend to have thicker plating, while areas with lower current density may have thinner or incomplete plating.
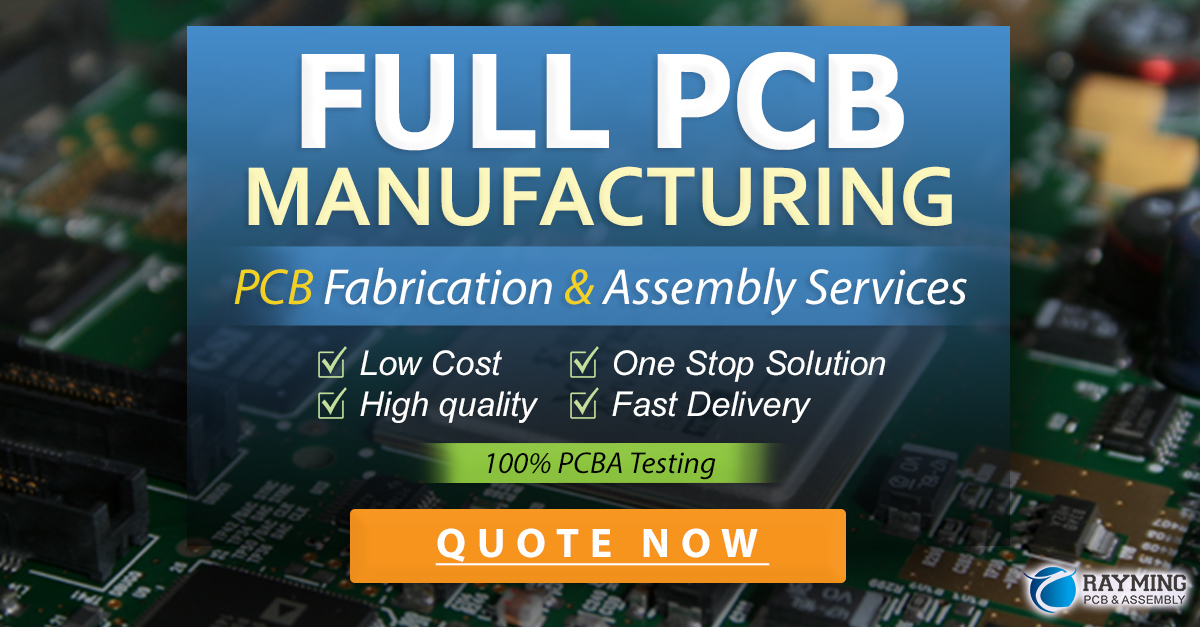
Case Studies
To demonstrate the effectiveness of PCB Plating Simulation, let’s explore a few case studies:
Case Study 1: High Aspect Ratio Vias
Problem: A PCB design contained high aspect ratio vias that were prone to incomplete plating and voids.
Solution: By simulating the plating process, the designers identified the areas with low current density and modified the via geometry to improve the plating uniformity. The optimized design resulted in complete plating coverage and elimination of voids.
Case Study 2: Dense Copper Patterns
Problem: A PCB with dense copper patterns experienced significant plating thickness variations, leading to reliability issues.
Solution: Plating Simulation helped analyze the current density distribution and identify the areas with excessive or insufficient plating. By adjusting the anode placement and modifying the copper pattern layout, the designers achieved uniform plating thickness across the dense areas.
Case Study 3: Isolated Traces
Problem: Isolated traces on a PCB exhibited thin and inconsistent plating, causing signal integrity problems.
Solution: Through simulation, the designers discovered that the isolated traces had lower current density compared to the surrounding areas. By adding dummy copper features and optimizing the anode configuration, they improved the plating uniformity on the isolated traces.
Best Practices for PCB Plating Simulation
To get the most out of PCB Plating Simulation, follow these best practices:
-
Start Early: Incorporate plating simulation early in the design process to identify and address potential issues before finalizing the layout.
-
Use Accurate Models: Ensure that the simulation models accurately represent the PCB geometry, material properties, and process parameters for reliable results.
-
Validate with Experiments: Validate the simulation results with experimental data to build confidence in the simulation accuracy and refine the models if necessary.
-
Collaborate with Manufacturers: Work closely with the PCB manufacturers to understand their plating processes and incorporate their feedback into the simulation setup.
-
Continuously Improve: Use the simulation results to continuously optimize the PCB design and plating process for better quality and efficiency.
Frequently Asked Questions (FAQ)
-
What is PCB Plating Simulation?
PCB Plating Simulation is a virtual tool that allows designers to simulate and analyze the electroplating process of a PCB before actual manufacturing. It predicts the plating thickness distribution, identifies potential issues, and helps optimize the design for improved plating uniformity and quality. -
Why is Plating Simulation important for PCB design?
Plating Simulation is important because it helps identify and rectify potential plating issues early in the design stage, saving costs and time. It enables designers to optimize the PCB layout and process parameters for better plating uniformity, reliability, and overall quality of the manufactured PCBs. -
What factors affect plating uniformity on a PCB?
Several factors can affect plating uniformity, including board geometry, anode and cathode placement, plating solution composition, and current density distribution. PCB features like high aspect ratio vias, dense copper patterns, and isolated traces can also lead to non-uniform plating thickness. -
How does PCB Plating Simulation work?
PCB Plating Simulation uses advanced computational methods, such as Finite Element Analysis (FEA) or Boundary Element Method (BEM), to model and analyze the electroplating process. It involves importing the PCB design, meshing the geometry, defining material properties and boundary conditions, running the simulation solver, and post-processing the results to identify plating issues and optimize the design. -
What are the best practices for using PCB Plating Simulation effectively?
To use PCB Plating Simulation effectively, start early in the design process, use accurate models, validate the simulation results with experimental data, collaborate with PCB manufacturers, and continuously improve the design based on the simulation insights. These practices help ensure reliable simulation results and optimize the PCB design for better plating quality and efficiency.
Conclusion
PCB Plating Simulation is a powerful tool that empowers PCB designers to optimize the plating process virtually, saving time, costs, and improving the overall quality of the manufactured PCBs. By accurately predicting the plating thickness distribution and identifying potential issues, simulation enables designers to make informed decisions and iterate quickly to achieve the best possible plating uniformity.
As the complexity of PCB designs continues to increase, the adoption of Plating Simulation becomes increasingly crucial for staying competitive in the industry. By embracing this innovative technology and following best practices, PCB designers can unlock new levels of efficiency, reliability, and performance in their designs.
At our company, we are committed to providing state-of-the-art PCB Plating Simulation tools and expertise to our customers. Our team of experienced engineers and simulation specialists work closely with designers to optimize their PCB layouts and ensure successful plating outcomes. With our cutting-edge simulation technology and collaborative approach, we help our customers navigate the challenges of PCB plating and deliver high-quality, reliable products to the market faster than ever before.
Leave a Reply