The Importance of Outer layer etching in PCB Manufacturing
Outer layer etching plays a vital role in the production of high-quality PCBs. The process allows for the creation of intricate patterns and designs on the copper surfaces of the PCB, which are essential for establishing electrical connections between components. Some of the key reasons why outer layer etching is crucial include:
-
Creating Conductive Paths: By selectively removing copper from the outer layers, outer layer etching creates the necessary conductive paths that allow electrical signals to travel between components on the PCB.
-
Ensuring Signal Integrity: Properly etched outer layers help maintain signal integrity by providing a clean and clear path for electrical signals to follow, minimizing interference and cross-talk between adjacent traces.
-
Facilitating Component Placement: Outer layer etching creates the required pad sizes and shapes for surface-mounted components, ensuring proper component placement and soldering.
-
Enabling High-Density Designs: As electronic devices become smaller and more complex, outer layer etching allows for the creation of high-density PCB designs with fine pitch traces and small component footprints.
The Outer Layer Etching Process
The outer layer etching process typically involves several steps, each of which is critical for achieving the desired results. The main steps in the process include:
1. Cleaning and Surface Preparation
Before the etching process can begin, the PCB’s outer layers must be thoroughly cleaned to remove any contaminants, such as dirt, grease, or oxidation. This step is crucial for ensuring proper adhesion of the photoresist and achieving optimal etching results. Common cleaning methods include chemical cleaning, mechanical cleaning, and plasma cleaning.
2. Photoresist Application
Once the surface is clean, a layer of photoresist is applied to the copper surface. Photoresist is a light-sensitive material that, when exposed to UV light through a patterned mask, changes its solubility in a developer solution. The photoresist can be applied using various methods, such as spin coating, spray coating, or dry film lamination.
3. Exposure and Development
The photoresist-coated PCB is then exposed to UV light through a patterned mask, which selectively hardens or softens the photoresist depending on the type of resist used (positive or negative). After exposure, the PCB is placed in a developer solution, which removes the soluble portions of the photoresist, leaving behind a patterned resist layer that will protect the desired copper areas during etching.
4. Etching
The exposed copper areas are then etched away using a chemical etchant, typically an acidic solution containing cupric chloride or ferric chloride. The etching process can be performed using various methods, such as immersion etching, spray etching, or bubble etching. The choice of etching method depends on factors such as the desired etch rate, the complexity of the design, and the available equipment.
5. Resist Stripping and Cleaning
After etching, the remaining photoresist is stripped away using a chemical stripper or a combination of mechanical and chemical methods. The PCB is then thoroughly cleaned to remove any residual etchant or contaminants, leaving behind the desired copper pattern on the outer layers.
Etching Methods
There are several methods used for outer layer etching, each with its own advantages and disadvantages. The choice of etching method depends on various factors, such as the desired etch rate, the complexity of the design, the available equipment, and the production volume. Some of the most common etching methods include:
1. Immersion Etching
Immersion etching involves submerging the PCB in a tank containing the etching solution. This method is relatively simple and cost-effective, making it suitable for low-volume production or prototyping. However, immersion etching has limited control over the etch rate and can result in undercut, where the etchant removes copper underneath the photoresist, leading to wider traces than desired.
2. Spray Etching
Spray etching uses a pressurized spray of etchant to remove the exposed copper. This method provides better control over the etch rate and reduces undercut compared to immersion etching. Spray etching is suitable for medium to high-volume production and can handle more complex designs. However, it requires specialized equipment and may have higher operating costs.
3. Bubble Etching
Bubble etching, also known as foam etching, uses a foam of etchant generated by air or nitrogen bubbles. The foam is applied to the PCB surface, and the bubbles help to agitate the etchant, improving the etch rate and reducing undercut. Bubble etching is suitable for high-volume production and can handle very fine pitch designs. However, it requires specialized equipment and precise control over the foam generation and application.
4. Laser-Enhanced Etching
Laser-enhanced etching uses a laser to selectively heat the copper surface, increasing the etch rate in the exposed areas. This method provides excellent control over the etch rate and can produce very fine features with minimal undercut. Laser-enhanced etching is suitable for high-precision applications and can handle complex designs. However, it requires specialized and expensive equipment, making it more suitable for high-value, low-volume production.
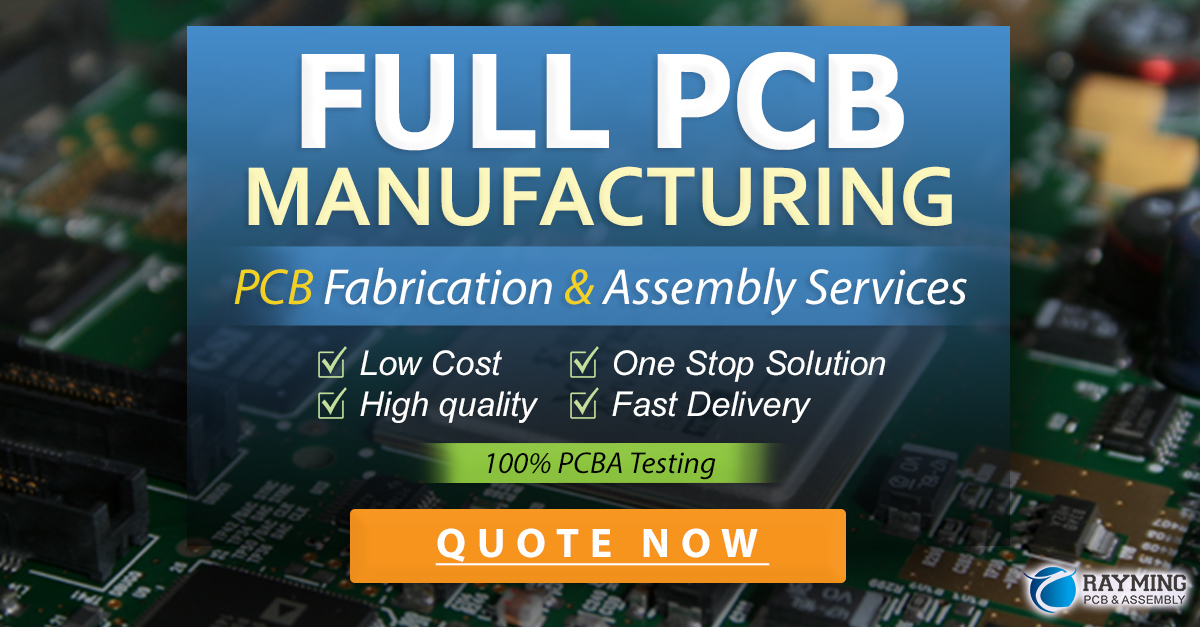
Challenges in Outer Layer Etching
While outer layer etching is a well-established process in PCB manufacturing, there are still several challenges that engineers and manufacturers face. Some of these challenges include:
1. Undercut
Undercut refers to the undesired removal of copper underneath the photoresist, resulting in wider traces than intended. This can lead to reduced signal integrity, increased cross-talk, and potential short circuits. Minimizing undercut requires precise control over the etching process, including the choice of etchant, the etch rate, and the etching method.
2. Over-etching
Over-etching occurs when the etchant removes too much copper, resulting in traces that are narrower than desired. This can lead to increased resistance, reduced current-carrying capacity, and potential open circuits. Preventing over-etching requires careful monitoring of the etching process and precise timing of the etching duration.
3. Surface Roughness
Etching can result in increased surface roughness of the copper traces, which can affect signal integrity and lead to higher insertion losses, especially at high frequencies. Minimizing surface roughness requires optimizing the etching process, including the choice of etchant, the etch rate, and the post-etching cleaning processes.
4. Etchant Compatibility
The choice of etchant must be compatible with the photoresist and the copper surface to ensure optimal etching results. Incompatible etchants can lead to poor adhesion of the photoresist, uneven etching, or excessive undercut. Careful selection of the etchant and thorough testing are necessary to ensure compatibility and optimal performance.
5. Environmental Concerns
Many traditional etching processes use hazardous chemicals, such as strong acids, which can pose environmental and health risks if not handled properly. Disposing of spent etchant and managing the waste generated during the etching process can be challenging and costly. Developing and adopting more environmentally friendly etching processes, such as those using less hazardous etchants or recycling spent etchant, is an ongoing challenge in the industry.
Advancements in Outer Layer Etching Technology
As the demand for higher-density, higher-performance PCBs continues to grow, researchers and manufacturers are continually developing new technologies and methods to improve outer layer etching. Some of the recent advancements include:
-
Direct Imager (DI) Technology: DI technology uses a high-precision, high-speed laser to directly expose the photoresist, eliminating the need for a patterned mask. This allows for faster setup times, improved registration accuracy, and the ability to handle more complex designs with finer features.
-
Plasma Etching: Plasma etching uses a plasma of reactive gases to etch the copper surface. This method provides excellent control over the etch rate and can produce very fine features with minimal undercut. Plasma etching is particularly suitable for high-density designs and can be used in combination with traditional chemical etching processes.
-
Inkjet Resist Printing: Inkjet resist printing uses a high-resolution inkjet printer to directly deposit the photoresist onto the copper surface. This method allows for precise control over the resist pattern and can handle complex designs with fine features. Inkjet resist printing can reduce material waste and improve the efficiency of the etching process.
-
Electrochemical Etching: Electrochemical etching uses an electrical current to selectively remove copper from the PCB surface. This method provides excellent control over the etch rate and can produce very fine features with minimal undercut. Electrochemical etching is particularly suitable for high-density designs and can be used in combination with traditional chemical etching processes.
FAQs
-
Q: What is the difference between outer layer etching and inner layer etching?
A: Outer layer etching involves the selective removal of copper from the top and bottom layers of a PCB, while inner layer etching involves the removal of copper from the internal layers of a multi-layer PCB. Inner layer etching is typically performed before the layers are laminated together, while outer layer etching is performed after lamination. -
Q: What are the most common etchants used in outer layer etching?
A: The most common etchants used in outer layer etching are acidic solutions containing cupric chloride (CuCl2) or ferric chloride (FeCl3). These etchants selectively remove copper from the exposed areas of the PCB while leaving the protected areas intact. -
Q: How does the choice of photoresist affect the outer layer etching process?
A: The choice of photoresist affects the resolution and accuracy of the etching process. Positive photoresists, which become soluble in the developer solution when exposed to UV light, are more common in outer layer etching due to their higher resolution and better compatibility with fine-pitch designs. Negative photoresists, which become insoluble when exposed to UV light, are less common but may be used in some applications. -
Q: What are the environmental concerns associated with outer layer etching?
A: Traditional outer layer etching processes use hazardous chemicals, such as strong acids, which can pose environmental and health risks if not handled properly. Disposing of spent etchant and managing the waste generated during the etching process can be challenging and costly. Developing and adopting more environmentally friendly etching processes, such as those using less hazardous etchants or recycling spent etchant, is an ongoing challenge in the industry. -
Q: How can undercut be minimized in outer layer etching?
A: Undercut can be minimized by optimizing the etching process, including the choice of etchant, the etch rate, and the etching method. Using a more controlled etching method, such as spray etching or bubble etching, can help reduce undercut compared to immersion etching. Additionally, using a higher-resolution photoresist and precisely controlling the etching duration can help minimize undercut and improve the accuracy of the etched features.
Conclusion
Outer layer etching is a critical process in the manufacturing of PCBs, enabling the creation of the intricate copper patterns that form the electrical connections between components. The process involves several steps, including cleaning, photoresist application, exposure, development, etching, and stripping. Various etching methods, such as immersion etching, spray etching, bubble etching, and laser-enhanced etching, are used depending on the specific requirements of the PCB design and the available equipment.
Despite being a well-established process, outer layer etching still faces challenges, such as undercut, over-etching, surface roughness, etchant compatibility, and environmental concerns. To address these challenges, researchers and manufacturers are continually developing new technologies and methods, such as direct imaging, plasma etching, inkjet resist printing, and electrochemical etching.
As the demand for high-density, high-performance PCBs continues to grow, the importance of outer layer etching in the manufacturing process will only increase. By understanding the fundamentals of the process, its challenges, and the latest advancements in technology, PCB designers and manufacturers can optimize their etching processes to produce higher-quality, more reliable PCBs that meet the ever-increasing demands of the electronics industry.
Etching Method | Advantages | Disadvantages |
---|---|---|
Immersion Etching | Simple, cost-effective, suitable for low-volume production or prototyping | Limited control over etch rate, can result in undercut |
Spray Etching | Better control over etch rate, reduces undercut, suitable for medium to high-volume production | Requires specialized equipment, higher operating costs |
Bubble Etching | Suitable for high-volume production, can handle very fine pitch designs | Requires specialized equipment, precise control over foam generation and application |
Laser-Enhanced Etching | Excellent control over etch rate, produces very fine features with minimal undercut, suitable for high-precision applications | Requires specialized and expensive equipment, more suitable for high-value, low-volume production |
Leave a Reply