Understanding the Causes of Components Shortages
Several factors have contributed to the current components shortages, including:
-
Increased demand: The COVID-19 pandemic has accelerated the adoption of digital technologies, leading to a surge in demand for electronic devices and the components that power them.
-
Supply chain disruptions: Lockdowns, travel restrictions, and other measures implemented to curb the spread of the virus have disrupted global supply chains, making it difficult for manufacturers to obtain the components they need.
-
Natural disasters: Events such as earthquakes, floods, and fires have damaged production facilities and infrastructure, further exacerbating supply chain issues.
-
Geopolitical tensions: Trade disputes and tariffs have created additional challenges for businesses that rely on international supply chains.
Assessing the Impact on Industries
The components shortages have affected various industries in different ways. Here’s an overview of how some key sectors have been impacted:
Industry | Impact |
---|---|
Automotive | Production delays, reduced output, increased costs |
Consumer Electronics | Product shortages, higher prices, longer lead times |
Medical Devices | Difficulty sourcing components, potential delays in patient care |
Telecommunications | Slower rollout of 5G networks, increased equipment costs |
Strategies for Mitigating the Effects of Shortages
To navigate the components shortages, businesses can adopt several strategies:
1. Diversifying Supplier Networks
By working with multiple suppliers across different regions, companies can reduce their reliance on a single source and minimize the risk of disruption. This approach also allows businesses to compare prices and lead times, ensuring they get the best possible deal.
2. Redesigning Products
In some cases, it may be necessary to redesign products to use more readily available components. This can involve collaborating with suppliers to identify suitable alternatives or working with engineering teams to develop new designs that are less dependent on scarce parts.
3. Improving Inventory Management
Effective inventory management is crucial during times of shortage. By closely monitoring stock levels, forecasting demand, and communicating with suppliers, businesses can ensure they have the components they need when they need them. This may involve increasing safety stock levels or implementing just-in-time delivery systems.
4. Collaborating with Industry Partners
Collaboration is key to surviving components shortages. By working with industry partners, such as suppliers, customers, and even competitors, businesses can share information, pool resources, and develop joint solutions. For example, companies could form purchasing consortia to negotiate better terms with suppliers or establish shared inventory pools to ensure a steady supply of components.
5. Investing in Technology
Technology can play a vital role in helping businesses manage components shortages. For instance, supply chain management software can provide real-time visibility into inventory levels, supplier performance, and potential risks. Additionally, advanced analytics and artificial intelligence can help companies predict demand, optimize production schedules, and identify alternative sourcing options.
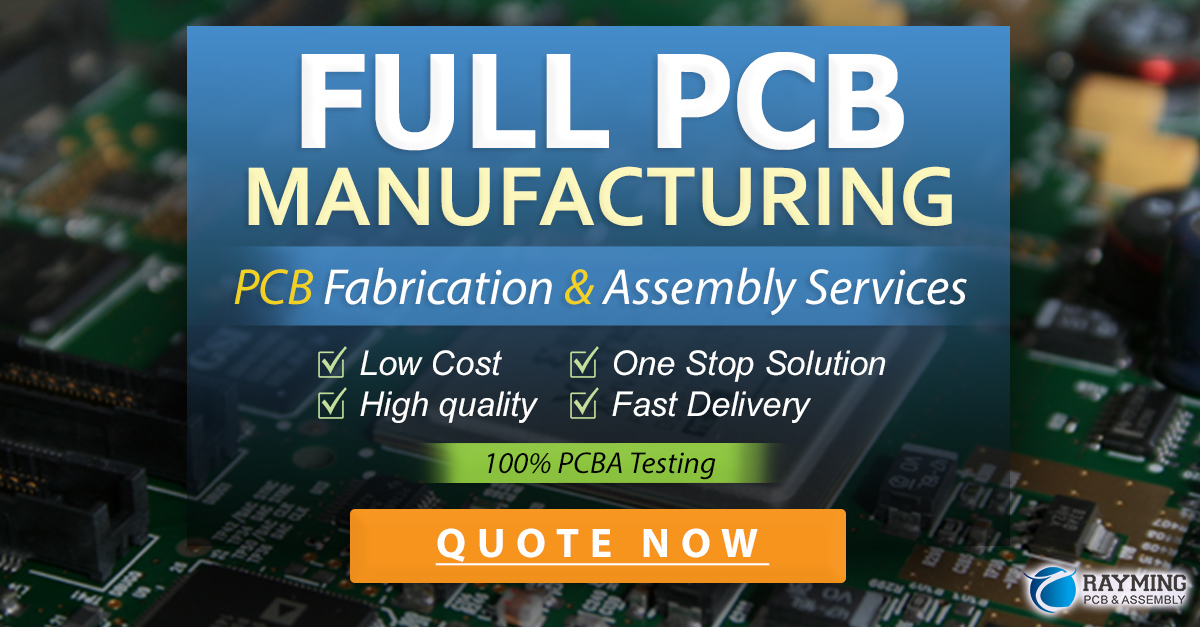
Case Studies: Successful Strategies in Action
Several companies have successfully navigated components shortages by implementing the strategies outlined above. Here are a few examples:
1. Tesla’s Vertical Integration
Tesla, the electric vehicle manufacturer, has mitigated the impact of components shortages by vertically integrating its supply chain. By producing many of its own components, such as batteries and semiconductors, Tesla has reduced its reliance on external suppliers and ensured a steady supply of critical parts.
2. Apple’s Supplier Diversification
Apple, the technology giant, has diversified its supplier network to minimize the risk of disruption. By working with multiple suppliers across different regions, Apple has been able to secure the components it needs to produce its popular devices, even during times of shortage.
3. Medtronic’s Collaborative Approach
Medtronic, a leading medical device manufacturer, has collaborated with industry partners to address components shortages. By working closely with suppliers and customers, Medtronic has been able to identify alternative sourcing options and develop joint solutions to ensure the continuity of its operations.
FAQ
1. How long are the components shortages expected to last?
It’s difficult to predict exactly how long the components shortages will last, as the situation is complex and constantly evolving. However, many experts believe that the shortages could persist well into 2022 and possibly beyond, depending on factors such as the pace of economic recovery, the availability of raw materials, and the resolution of geopolitical tensions.
2. Which components are in particularly short supply?
Some of the components that are currently in short supply include semiconductors, capacitors, resistors, and connectors. The shortage of semiconductors, in particular, has had a significant impact on industries such as automotive and consumer electronics, as these components are essential for the production of a wide range of products, from cars and smartphones to gaming consoles and home appliances.
3. How can businesses ensure they have the components they need?
To ensure they have the components they need, businesses can adopt several strategies, such as diversifying their supplier networks, redesigning products to use more readily available components, improving inventory management, collaborating with industry partners, and investing in technology. By implementing these strategies, companies can reduce their reliance on scarce parts and minimize the risk of disruption.
4. What role can governments play in addressing components shortages?
Governments can play a vital role in addressing components shortages by implementing policies that support domestic production, encourage investment in research and development, and facilitate international trade. For example, governments could provide incentives for companies to build new production facilities, fund research into alternative materials and technologies, and work to reduce trade barriers and tariffs.
5. How can businesses prepare for future supply chain disruptions?
To prepare for future supply chain disruptions, businesses can take several steps, such as conducting regular risk assessments, developing contingency plans, and investing in resilient supply chain infrastructure. By proactively identifying potential risks and developing strategies to mitigate them, companies can reduce their vulnerability to disruptions and ensure the continuity of their operations in the face of unexpected challenges.
Conclusion
The components shortages have presented significant challenges for businesses across various industries, but by working together and implementing creative solutions, companies can mitigate the effects of these shortages and ensure the continuity of their operations. By diversifying supplier networks, redesigning products, improving inventory management, collaborating with industry partners, and investing in technology, businesses can navigate these challenging times and emerge stronger and more resilient.
As the world continues to grapple with the impacts of the COVID-19 pandemic, natural disasters, and geopolitical tensions, it’s clear that supply chain disruptions will remain a reality for the foreseeable future. However, by embracing the strategies outlined in this article and learning from the successes of companies like Tesla, Apple, and Medtronic, businesses can not only survive components shortages but thrive in the face of adversity.
Leave a Reply