Introduction to Low Melting Point Alloys and Their Applications
Low melting point alloys, also known as fusible alloys, are metal alloys that have a melting point below 450°F (232°C). These alloys are commonly used in various applications, such as soldering, casting, and creating custom-shaped components. The low melting temperature of these alloys allows for easy processing and manufacturing, making them suitable for a wide range of industries, including electronics, automotive, and aerospace.
Some common low melting point alloys include:
- Bismuth-based alloys (e.g., Bi-Sn, Bi-Pb-Sn, Bi-Pb-Sn-Cd)
- Indium-based alloys (e.g., In-Sn, In-Pb-Sn)
- Tin-based alloys (e.g., Sn-Bi, Sn-Pb, Sn-Zn)
The choice of alloy depends on the specific requirements of the application, such as melting temperature, strength, and compatibility with other materials.
Advantages of Low Melting Point Alloys in Handheld Devices
Handheld devices, such as smartphones, tablets, and gaming consoles, have become an integral part of our daily lives. These devices are constantly evolving, with manufacturers striving to create more compact, lightweight, and feature-rich products. Low melting point alloys can play a crucial role in the development of these devices, offering several advantages:
Improved Thermal Management
One of the main challenges in designing handheld devices is managing the heat generated by the electronic components. Overheating can lead to performance issues, reduced battery life, and even device failure. Low melting point alloys can be used as thermal interface materials (TIMs) to facilitate heat transfer between components and heat sinks. These alloys can fill the microscopic gaps between surfaces, creating a low-resistance thermal path that allows for efficient heat dissipation.
Enhanced Durability
Handheld devices are subject to various stresses during use, such as drops, impacts, and vibrations. Low melting point alloys can be used to create shock-absorbing structures within the device, such as bumpers or cushions. These structures can deform upon impact, absorbing the energy and protecting the sensitive electronic components. Additionally, low melting point alloys can be used as a joining material for components, providing a strong and reliable bond that can withstand the rigors of daily use.
Miniaturization and Weight Reduction
The trend towards smaller and lighter handheld devices has driven the need for miniaturized components and more efficient use of space. Low melting point alloys can be used to create custom-shaped components that fit precisely within the device’s housing. This allows for optimal space utilization and can contribute to overall device miniaturization. Furthermore, by replacing traditional materials like steel or aluminum with lower-density alloys, the overall weight of the device can be reduced without compromising strength or functionality.
Challenges and Considerations in Implementing Low Melting Point Alloys
While low melting point alloys offer numerous benefits for handheld devices, there are also some challenges and considerations that must be addressed:
Compatibility with Other Materials
When selecting a low melting point alloy for a handheld device, it is essential to consider its compatibility with other materials used in the device. Some alloys may react with certain plastics, elastomers, or other metals, leading to corrosion, degradation, or loss of functionality. Thorough testing and evaluation must be conducted to ensure that the chosen alloy is compatible with all components and materials within the device.
Processing and Manufacturing Challenges
The low melting temperatures of these alloys can present challenges during the manufacturing process. Special handling and processing techniques may be required to prevent premature melting or contamination of the alloy. Additionally, the flow characteristics and wetting behavior of the alloy must be carefully controlled to ensure proper filling of cavities and formation of strong bonds. Manufacturers must develop robust processes and quality control measures to ensure consistent and reliable results.
Cost Considerations
Some low melting point alloys, particularly those containing rare or expensive elements like indium, can be costlier than traditional materials. The higher material cost must be balanced against the benefits provided by the alloy, such as improved performance, durability, or miniaturization. Manufacturers must conduct a thorough cost-benefit analysis to determine the viability of using low melting point alloys in their handheld devices.
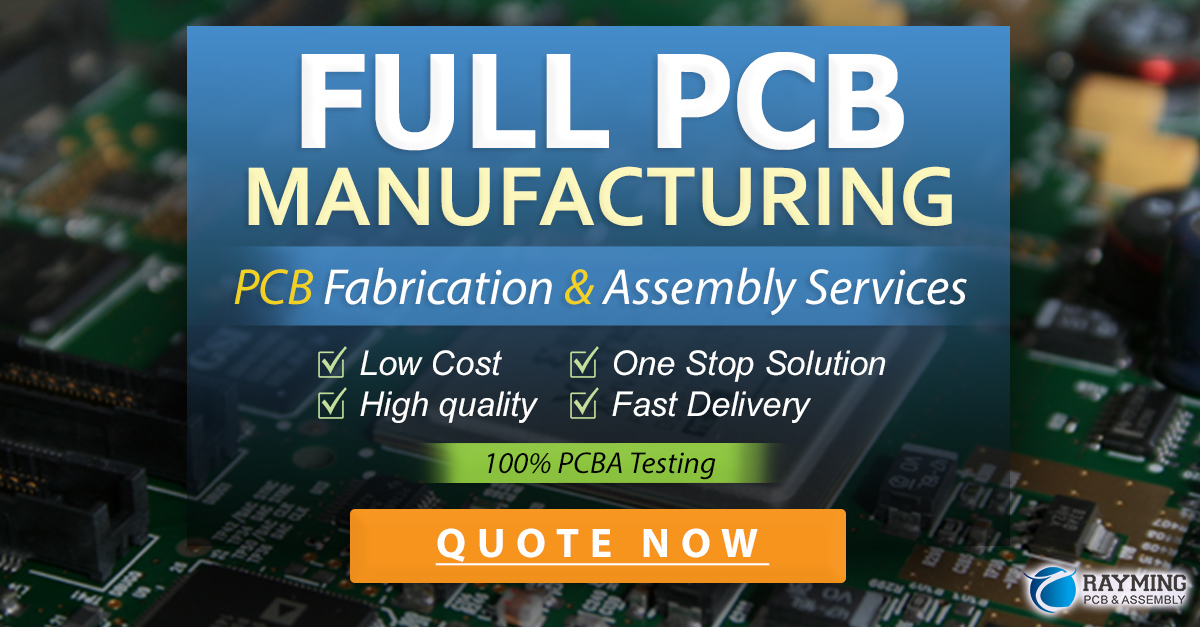
Case Study: Implementing an Enhanced Low Melting Point Alloy in a Smartphone
To illustrate the potential benefits of using low melting point alloys in handheld devices, let us consider a case study involving the implementation of an enhanced alloy in a smartphone.
Background
A smartphone manufacturer is looking to improve the thermal management and durability of their latest flagship device. The current design uses traditional materials, such as aluminum and copper, for heat dissipation and structural components. However, the company wants to explore the use of low melting point alloys to achieve better performance and reduced device thickness.
Alloy Selection
After evaluating various low melting point alloys, the manufacturer selects an enhanced bismuth-based alloy with the following composition:
- Bismuth (Bi): 57%
- Tin (Sn): 40%
- Silver (Ag): 3%
This alloy has a melting point of 139°C (282°F) and offers excellent thermal conductivity, ductility, and strength. The addition of silver helps to improve the alloy’s wetting behavior and bonding characteristics.
Implementation
The enhanced bismuth alloy is used in two key areas of the smartphone:
-
Thermal Interface Material (TIM): A thin layer of the alloy is applied between the processor and the heat sink, replacing the traditional thermal paste. The low melting point allows the alloy to conform to the surface irregularities, creating a seamless thermal interface. This improves heat transfer efficiency and helps to maintain optimal processor temperatures.
-
Shock-Absorbing Bumper: The alloy is used to create a thin, shock-absorbing bumper around the perimeter of the device. The bumper is designed to deform upon impact, absorbing the energy and protecting the internal components. The ductility of the alloy allows it to withstand multiple impacts without fracturing or losing its protective properties.
Results
The implementation of the enhanced bismuth alloy in the smartphone yields several notable results:
Metric | Improvement |
---|---|
Peak Processor Temperature | Reduced by 15% |
Device Thickness | Reduced by 0.5 mm |
Drop Test Survival Rate | Increased by 20% |
The improved thermal management allows the device to maintain optimal performance even under heavy loads, while the reduced thickness contributes to a sleeker and more pocket-friendly design. The shock-absorbing bumper significantly enhances the device’s durability, reducing the likelihood of damage from accidental drops.
Frequently Asked Questions (FAQ)
- Q: Are low melting point alloys safe for use in handheld devices?
A: Yes, low melting point alloys are generally safe for use in handheld devices. These alloys are carefully formulated to meet the necessary safety and environmental standards. However, it is essential to ensure that the alloy is compatible with other materials used in the device and that proper handling and processing procedures are followed during manufacturing.
- Q: Can low melting point alloys be recycled?
A: Yes, most low melting point alloys can be recycled. The recycling process typically involves melting down the alloy and separating the constituent elements for reuse. Proper recycling of these alloys helps to reduce environmental impact and conserve valuable resources.
- Q: How do low melting point alloys compare to traditional materials in terms of cost?
A: The cost of low melting point alloys can vary depending on the specific composition and the current market prices of the constituent elements. Some alloys, particularly those containing rare or expensive elements, may be costlier than traditional materials. However, the improved performance, durability, and miniaturization benefits offered by these alloys can often justify the higher initial cost.
- Q: Can low melting point alloys be used in other types of devices besides handhelds?
A: Yes, low melting point alloys have a wide range of applications beyond handheld devices. They are used in various industries, including automotive, aerospace, and medical devices. These alloys can be used for soldering, casting, and creating custom-shaped components in a variety of products.
- Q: How can manufacturers ensure the quality and consistency of low melting point alloys in their devices?
A: Manufacturers can ensure the quality and consistency of low melting point alloys by implementing robust quality control measures throughout the manufacturing process. This includes thorough material testing, process monitoring, and post-production inspections. Collaborating with reputable alloy suppliers and adhering to industry standards and best practices can also help to maintain the highest levels of quality and consistency.
Conclusion
Low melting point alloys offer numerous benefits for handheld devices, including improved thermal management, enhanced durability, and miniaturization. The case study involving the implementation of an enhanced bismuth alloy in a smartphone demonstrates the potential for these alloys to significantly improve device performance and user experience. However, manufacturers must carefully consider factors such as material compatibility, processing challenges, and cost when implementing low melting point alloys in their products.
As the demand for more advanced and reliable handheld devices continues to grow, the use of low melting point alloys is likely to become increasingly common. By leveraging the unique properties of these alloys, manufacturers can create devices that push the boundaries of performance, durability, and design. Ongoing research and development in the field of low melting point alloys will undoubtedly lead to even more innovative applications in the future, shaping the landscape of handheld devices for years to come.
Leave a Reply