Introduction to PCB Placement in Reflow Ovens
Printed Circuit Board (PCB) assembly is a crucial process in electronics manufacturing, and reflow soldering is a widely used technique for mounting surface mount components onto PCBs. Proper placement of the PCB in the reflow oven is essential for achieving optimal soldering results and ensuring the reliability of the final product. In this article, we will discuss the key factors to consider when placing PCBs in a reflow oven and provide guidelines for optimal PCB placement.
Factors Affecting PCB Placement in Reflow Ovens
Oven Type and Configuration
The type and configuration of the reflow oven play a significant role in determining the optimal PCB placement. Reflow ovens can be categorized into two main types:
- Convection Reflow Ovens
- Uses forced air circulation to distribute heat evenly
- Suitable for larger PCBs and higher production volumes
-
Requires careful consideration of airflow patterns and PCB orientation
-
Infrared (IR) Reflow Ovens
- Uses IR radiation to heat the PCB and components
- Suitable for smaller PCBs and lower production volumes
- Requires proper alignment of IR emitters and PCB position
PCB Size and Shape
The size and shape of the PCB are critical factors in determining the optimal placement within the reflow oven.
- Smaller PCBs: Easier to position and less affected by temperature variations across the oven
- Larger PCBs: Require more uniform heat distribution and may need specialized fixtures for proper support
The shape of the PCB also influences the placement:
- Rectangular PCBs: Easier to align and position consistently
- Irregular-shaped PCBs: May require custom fixtures or supports to ensure proper alignment
Component Placement and Density
The placement and density of components on the PCB can affect the optimal positioning in the reflow oven.
- High-density PCBs: Require more precise temperature control and uniformity to prevent overheating or underheating of components
- PCBs with tall components: May create shadowing effects, requiring careful placement to ensure even heating
Guidelines for Optimal PCB Placement
Centering the PCB in the Oven
Centering the PCB in the reflow oven helps ensure even heat distribution and minimizes temperature variations across the board. To achieve proper centering:
- Use oven racks or conveyor systems designed for PCB processing
- Align the PCB with the center of the oven cavity
- Maintain equal distances from the PCB edges to the oven walls
Orientation and Alignment
Proper orientation and alignment of the PCB in the reflow oven are crucial for achieving consistent soldering results.
- For convection reflow ovens:
- Orient the PCB parallel to the airflow direction to minimize turbulence
-
Align the PCB with the conveyor system or oven racks to ensure consistent positioning
-
For IR reflow ovens:
- Orient the PCB perpendicular to the IR emitters for optimal heat absorption
- Align the PCB with the IR emitter array to ensure even heating across the board
Spacing and Clearance
Adequate spacing and clearance around the PCB are necessary to allow for proper heat circulation and to prevent interference with oven components.
- Maintain sufficient clearance between the PCB and oven walls, typically at least 25mm (1 inch) on all sides
- For convection reflow ovens, ensure adequate spacing between PCBs to allow for proper airflow
- Consider the height of components when determining the required clearance above and below the PCB
Fixturing and Support
Proper fixturing and support are essential for maintaining the desired PCB position throughout the reflow process.
- Use oven-safe materials for fixtures, such as stainless steel or high-temperature plastics
- Ensure that fixtures provide adequate support without interfering with heat transfer
- Consider the use of pin fixtures or edge supports for larger or heavier PCBs
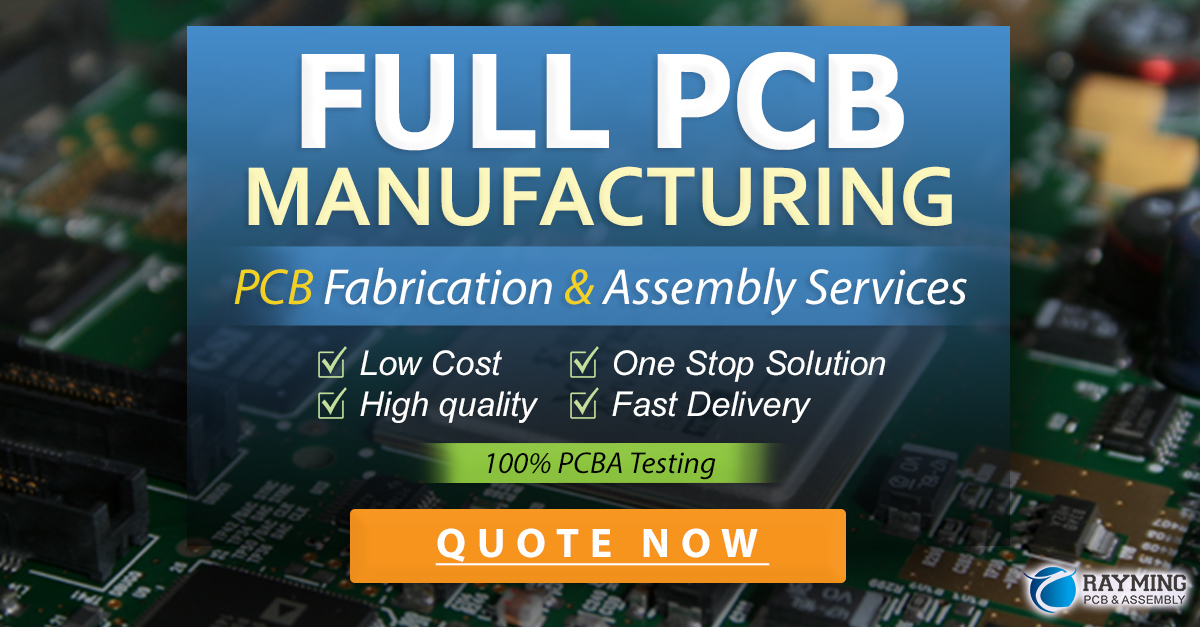
Monitoring and Optimization
Temperature Profiling
Temperature profiling is the process of measuring and analyzing the temperature distribution across the PCB during the reflow process. It helps optimize the PCB placement and ensures that the soldering process meets the required specifications.
- Use thermocouples or thermal profiling systems to measure temperatures at critical points on the PCB
- Analyze the temperature data to identify hot spots, cold spots, or uneven heating
- Adjust the PCB placement or oven settings based on the profiling results to achieve optimal soldering conditions
Process Validation and Quality Control
Regular process validation and quality control measures are essential to maintain consistent PCB placement and soldering results.
- Establish standard operating procedures (SOPs) for PCB placement and reflow soldering
- Conduct periodic inspections and audits to ensure compliance with SOPs
- Implement statistical process control (SPC) techniques to monitor and control the reflow soldering process
- Perform post-reflow inspections, such as visual inspection or X-ray analysis, to verify soldering quality
Frequently Asked Questions (FAQ)
-
Q: What happens if the PCB is not properly centered in the reflow oven?
A: If the PCB is not properly centered, it may experience uneven heating, which can lead to poor soldering results, component damage, or reduced reliability of the final product. -
Q: Can I place multiple PCBs in the reflow oven at the same time?
A: Yes, you can place multiple PCBs in the reflow oven simultaneously, provided that there is sufficient spacing between the boards and the oven has the capacity to handle the increased thermal load. Ensure that the placement of multiple PCBs does not compromise the uniformity of heat distribution. -
Q: How do I determine the optimal orientation of the PCB in the reflow oven?
A: The optimal orientation of the PCB depends on the type of reflow oven being used. For convection reflow ovens, orient the PCB parallel to the airflow direction. For IR reflow ovens, orient the PCB perpendicular to the IR emitters. Always consider the specific oven manufacturer’s recommendations and guidelines. -
Q: What materials should I use for PCB fixturing in the reflow oven?
A: Use oven-safe materials that can withstand the high temperatures of the reflow process. Stainless steel and high-temperature plastics are common choices for PCB fixtures. Avoid materials that may outgas or contaminate the PCB during the reflow process. -
Q: How often should I perform temperature profiling for my reflow soldering process?
A: Temperature profiling should be performed whenever there are significant changes to the PCB design, components, or reflow oven settings. It is also recommended to conduct periodic profiling as part of regular process validation and quality control measures. The frequency of profiling depends on factors such as production volume, product complexity, and quality requirements.
Conclusion
Proper placement of PCBs in the reflow oven is essential for achieving optimal soldering results and ensuring the reliability of the final product. By considering factors such as oven type, PCB size and shape, component placement, and density, manufacturers can develop guidelines for optimal PCB positioning. Centering the PCB, ensuring proper orientation and alignment, maintaining adequate spacing and clearance, and using appropriate fixturing and support are key elements of successful PCB placement.
Temperature profiling, process validation, and quality control measures are essential for monitoring and optimizing the reflow soldering process. By following best practices and continuously improving PCB placement techniques, electronics manufacturers can enhance the quality and reliability of their products while minimizing defects and rework.
References
- Heller, Reflow Soldering Processes and Troubleshooting: SMT, BGA, CSP, and Flip Chip Technologies, 2002.
- IPC-7530, Guidelines for Temperature Profiling for Mass Soldering Processes (Reflow & Wave), Association Connecting Electronics Industries, 2016.
- IPC-7095C, Design and Assembly Process Implementation for BGAs, Association Connecting Electronics Industries, 2013.
- IPC-J-STD-033D, Handling, Packing, Shipping and Use of Moisture/Reflow Sensitive Surface Mount Devices, Association Connecting Electronics Industries, 2018.
Leave a Reply