Introduction to the Intellitool Matrix
The Elsyca Intellitool Matrix is an innovative plating technology that enables high-precision control over the electroplating process. Developed by Elsyca, a leading provider of electrochemical solutions, the Intellitool Matrix combines advanced hardware and software to deliver superior plating results across a wide range of applications.
Key Features of the Intellitool Matrix
The Intellitool Matrix offers several key features that set it apart from traditional plating systems:
-
High-resolution current distribution control: The system utilizes a matrix of individually controllable anodes, allowing for precise control over the current distribution across the substrate surface. This enables the creation of complex plating patterns and the compensation of substrate geometries.
-
Real-time monitoring and feedback: Integrated sensors continuously monitor the plating process, providing real-time data on key parameters such as current density, temperature, and electrolyte composition. This data is used to dynamically adjust the plating conditions, ensuring optimal results.
-
Advanced simulation and optimization tools: The Intellitool Matrix includes powerful simulation software that predicts the plating outcome based on the input parameters. This allows for the optimization of the plating process before the actual deposition takes place, saving time and resources.
-
Flexible and scalable architecture: The modular design of the Intellitool Matrix enables easy scaling and customization to meet specific application requirements. The system can be configured for a wide range of substrate sizes, geometries, and materials.
Applications of the Intellitool Matrix
The Elsyca Intellitool Matrix finds applications in various industries where precise and uniform plating is critical. Some of the key application areas include:
Semiconductor and Electronics Industry
In the semiconductor and electronics industry, the Intellitool Matrix is used for the deposition of thin films and the creation of interconnects. The high-resolution current control enables the formation of fine features and the compensation of substrate topography, resulting in improved device performance and reliability.
Application | Benefits of Intellitool Matrix |
---|---|
Through-silicon vias (TSVs) | Uniform deposition, reduced voids and defects |
Redistribution layers (RDLs) | Precise control over line width and spacing |
Bumping and pillars | Uniform height and shape, improved bonding strength |
Copper filling | Void-free filling, reduced overburden |
Automotive and Aerospace Industries
The Intellitool Matrix is employed in the automotive and aerospace industries for the plating of functional and decorative coatings. The system’s ability to control the plating thickness and distribution enables the creation of coatings with improved mechanical properties, corrosion resistance, and aesthetic appeal.
Application | Benefits of Intellitool Matrix |
---|---|
Hard chrome plating | Uniform thickness, improved wear resistance |
Electroless nickel plating | Precise control over phosphorus content, enhanced corrosion resistance |
Anodizing | Uniform color and thickness, improved surface hardness |
Decorative plating | High-quality finishes, reduced rejects |
Medical Device Industry
In the medical device industry, the Intellitool Matrix is used for the deposition of biocompatible coatings and the creation of micro-scale features. The precise control over the plating process ensures the production of high-quality devices that meet stringent regulatory requirements.
Application | Benefits of Intellitool Matrix |
---|---|
Stent coating | Uniform drug loading, controlled release kinetics |
Implantable electrodes | Precise control over surface area, improved signal-to-noise ratio |
Microfluidic devices | High-resolution features, uniform channel dimensions |
Orthopaedic implants | Uniform hydroxyapatite coating, enhanced osseointegration |
Case Studies
To demonstrate the capabilities of the Elsyca Intellitool Matrix, let’s examine a few case studies from different industries.
Case Study 1: Semiconductor TSV Plating
A semiconductor manufacturer sought to improve the yield and reliability of their through-silicon via (TSV) plating process. The challenge was to achieve uniform copper deposition inside the high aspect ratio vias while minimizing voids and defects.
The Elsyca Intellitool Matrix was employed to optimize the plating process. The system’s high-resolution current control enabled the precise modulation of the current density inside the vias, resulting in uniform copper growth. The real-time monitoring and feedback ensured that the plating conditions were maintained within the optimal range throughout the process.
As a result, the manufacturer achieved a significant improvement in TSV yield, with a 95% reduction in voids and defects. The optimized process also led to a 20% increase in throughput, translating to substantial cost savings.
Case Study 2: Automotive Hard Chrome Plating
An automotive supplier needed to improve the quality and consistency of their hard chrome plating process for engine components. The main challenges were to achieve uniform coating thickness across complex geometries and to minimize the occurrence of defects such as cracks and nodules.
The Elsyca Intellitool Matrix was implemented to address these challenges. The system’s simulation tools were used to predict the current distribution and optimize the anode configuration for the specific component geometry. The real-time monitoring and control ensured that the plating parameters were maintained within the specified limits.
The optimized process resulted in a significant improvement in coating uniformity, with a thickness variation of less than 5% across the component surface. The occurrence of defects was reduced by 80%, leading to a higher yield and reduced rework costs.
Case Study 3: Medical Device Stent Coating
A medical device manufacturer required a precise and reproducible process for the deposition of a drug-eluting coating on coronary stents. The challenge was to achieve uniform drug loading across the stent surface while maintaining the desired release kinetics.
The Elsyca Intellitool Matrix was utilized to develop and optimize the coating process. The system’s high-resolution current control enabled the precise modulation of the coating thickness and composition. The real-time monitoring and feedback ensured that the coating parameters were maintained within the tight tolerances required for medical devices.
The optimized process resulted in stents with uniform drug loading and precisely controlled release profiles. The batch-to-batch variability was reduced by 90%, ensuring consistent product quality and patient outcomes.
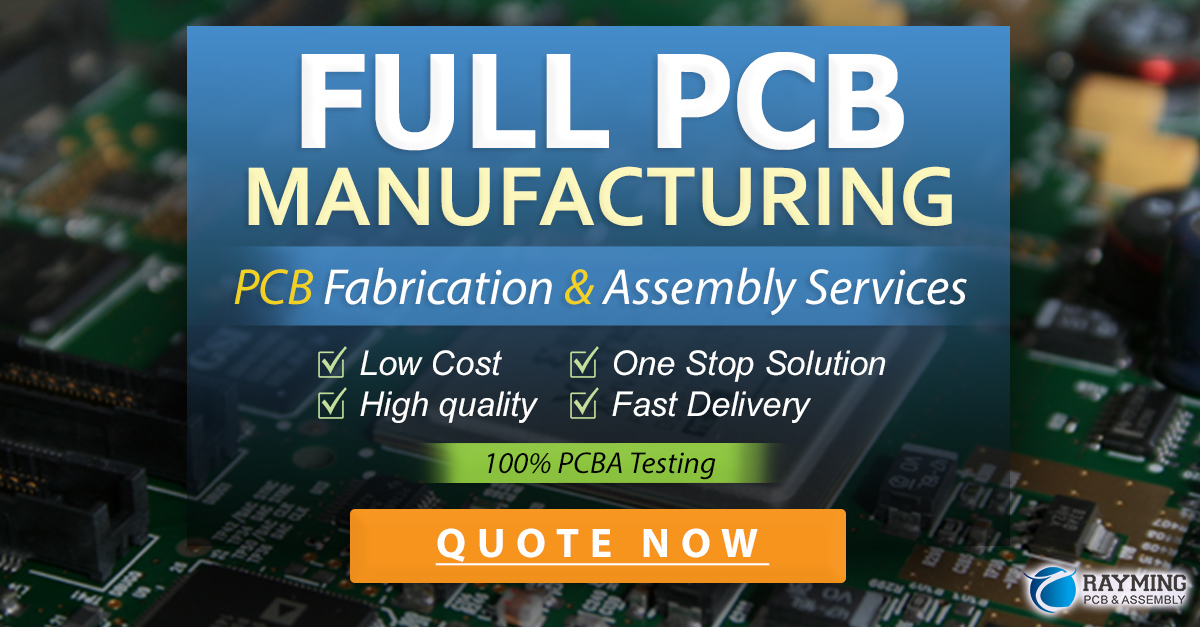
Frequently Asked Questions (FAQ)
-
Q: What is the Elsyca Intellitool Matrix?
A: The Elsyca Intellitool Matrix is an advanced electroplating system that combines high-resolution current control, real-time monitoring, and simulation tools to enable precise and uniform plating across a wide range of applications. -
Q: How does the Intellitool Matrix differ from traditional plating systems?
A: The Intellitool Matrix offers several advantages over traditional plating systems, including high-resolution current distribution control, real-time monitoring and feedback, advanced simulation and optimization tools, and a flexible and scalable architecture. -
Q: What industries can benefit from the Intellitool Matrix?
A: The Intellitool Matrix finds applications in various industries, including the semiconductor and electronics industry, automotive and aerospace industries, and the medical device industry, where precise and uniform plating is critical. -
Q: Can the Intellitool Matrix be customized for specific applications?
A: Yes, the modular design of the Intellitool Matrix enables easy customization and scaling to meet specific application requirements. The system can be configured for a wide range of substrate sizes, geometries, and materials. -
Q: How does the Intellitool Matrix ensure optimal plating results?
A: The Intellitool Matrix ensures optimal plating results through a combination of high-resolution current control, real-time monitoring and feedback, and advanced simulation and optimization tools. These features enable the creation of complex plating patterns, the compensation of substrate geometries, and the maintenance of optimal plating conditions throughout the process.
Conclusion
The Elsyca Intellitool Matrix represents a significant advancement in electroplating technology, offering unprecedented control and precision over the plating process. With its high-resolution current distribution control, real-time monitoring and feedback, and advanced simulation and optimization tools, the Intellitool Matrix enables the creation of high-quality plated products across a wide range of industries.
As demonstrated by the case studies, the Intellitool Matrix has proven its ability to improve product quality, increase yield, and reduce costs in various applications, from semiconductor TSV plating to automotive hard chrome plating and medical device stent coating.
As the demand for precise and uniform plating continues to grow, the Elsyca Intellitool Matrix is well-positioned to meet the evolving needs of industries worldwide, driving innovation and setting new standards in electroplating excellence.
Leave a Reply