Introduction
Flex rigid PCBs combine rigid and flexible circuitry into a single board, providing solutions for complex electronics and packaging requirements. Choosing the right flex rigid PCB manufacturer is crucial to get high-quality boards that meet design specifications. This guide covers key considerations when selecting a flex rigid PCB manufacturer, including capabilities, quality, services, and cost.
Capabilities
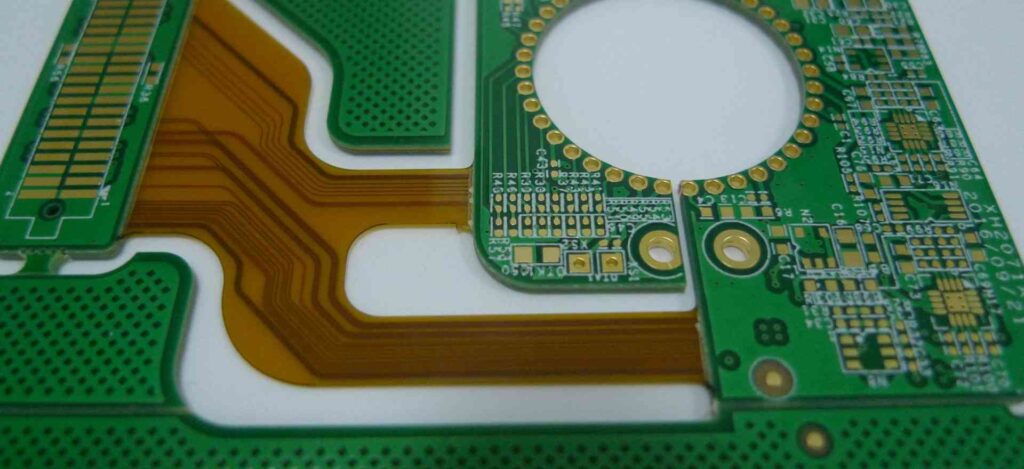
Circuit Density
- HDI (High-Density Interconnect) – More than 6 layers, microvias, tight trace/space
- Standard density – 4-6 layers with larger features
HDI boards enable miniaturization and higher component density. Ensure the manufacturer can produce the required number of layers and features sizes.
Board Thickness
- Thin cores (25-50μm) allow flexible sections to bend tighter
- Thick cores (0.8-1.6mm) provide rigidity in rigid sections
Choose a manufacturer capable of working with required material thicknesses.
Board Size
- Some manufacturers specialize in larger boards (over 460 x 610mm)
- Others focus on smaller, high mix boards
Match board dimensions to manufacturer size capabilities and production focus.
Special Materials
- RF/microwave substrates (PTFE, ceramic-filled)
- Flexible materials (PI, LCP)
- Metal core boards, carbon fiber
If specialized materials are needed, verify the manufacturer has expertise with those materials.
Technology Mix
- Embedded components
- Controlled impedance
- Flex-rigid transitions
- Coverlays, coatings
Evaluate expertise with any special technologies that will be used in the design.
Certifications
- AS9100 – Aerospace
- ISO 13485 – Medical
- IPC 6013 – Flex/rigid standards
- IPC Class 3 fabrication
Choose a manufacturer with certifications applicable to your industry and technology requirements.
Quality
First Pass Yield
- Percentage of boards passing electrical test requirements
- Industry average around 85%
- Look for first pass yields over 90%
Higher first pass yield indicates robust processes and quality control.
Solderability
- Test coupons to verify high quality solder pads
- IPC solderability standards testing
Ensure the manufacturer qualifies solder pad finishes like ENIG, Immersion Silver.
Inspection Accuracy
- Automated optical inspection (AOI)
- 3D inspection for solder joints
- High magnification inspection of plated features
Precision inspection tools like AOI reduce defects and improve quality consistency.
Process Capabilities
- Cpk/Ppk process capability indices
- Real-time WIP monitoring
- Statistical process control
Mature statistical process control shows the manufacturer’s processes are optimized and stable.
Services
Design For Manufacturing (DFM)
- DFM analysis to ensure manufacturability
- Feedback on stackup, tolerances, etc.
- Identify design improvements early
Look for detailed DFM analysis to avoid issues during manufacturing.
Prototyping
- Rapid prototyping services
- Small batches
- Quick turnaround
Rapid prototyping with similar processes to production improves design validation.
Assembly
- In-house assembly capabilities
- Component procurement
- Functional testing
Assembly services enable fully tested and working boards to be delivered.
Logistics
- Local warehouses for quick delivery
- Supply chain management
- Customs expertise for international orders
Choose a manufacturer with logistics resources to meet delivery requirements.
Cost
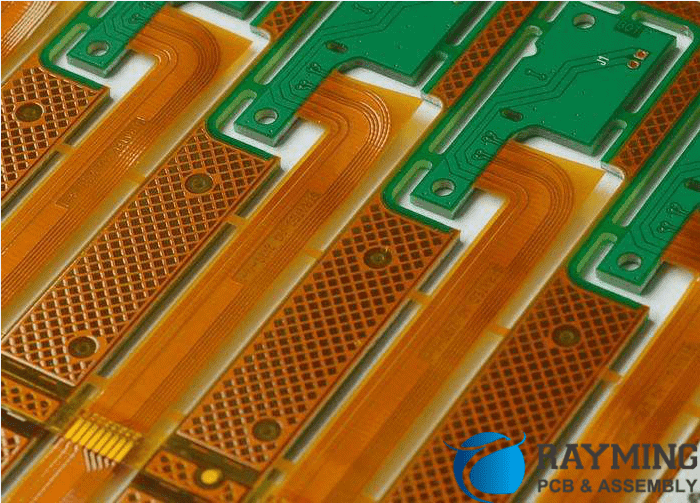
Low Volume Pricing
- Small order fees
- Non-recurring engineering (NRE) charges
- Plate costs for small batches
Understand all cost components, especially for low volume orders.
Volume Discounts
- Negotiate pricing based on annual volume
- Incentives for longer term commitments
Leverage volume production to negotiate better pricing.
Location
- Domestic manufacturers provide quicker turns and communication
- Offshore facilities offer very low cost at high volumes
- Balance cost vs. responsiveness
Factor in location tradeoffs between cost and delivery schedule.
Flex Rigid PCB Manufacturer Examples
To illustrate the selection criteria, here are examples of leading flex rigid PCB manufacturers:
Cirtech (UK)
Cirtech is an expert flex and flex-rigid PCB manufacturer located in the UK. Key strengths:
- High density interconnect (HDI) and microvia capabilities
- Prototyping services and small batch production
- Design support from quote to delivery
Compass Circuits (USA)
Compass Circuits specializes in quick-turn flex and rigid-flex boards made in the USA. Key features:
- Small quantities and fast delivery (24-48 hours)
- Flex-on-rigid constructions with tight tolerances
- Focus on small board sizes
RayMing (China)
RayMing offers cost-effective offshore production of rigid-flex PCBs. Ideal for:
- Medium to high volume production
- Customers comfortable managing extended supply chains
- Tight cost targets with flexible delivery timelines
Flex Rigid PCB Manufacturer Checklist
Here is a summary checklist when evaluating flex rigid PCB manufacturers:
- Capabilities match design requirements (layers, density, size, materials)
- Quality control data demonstrates excellent process maturity
- Available services fit product lifecycle needs (prototyping, DFM, assembly)
- Pricing fits budget constraints for volumes, location, and services needed
- Company is trusted, responsive partner for design and manufacturing
Following these guidelines will help identify the best flex rigid partner for your specific product needs. With the right PCB manufacturer, your next flex-rigid project can be executed smoothly from design through delivery.
Frequently Asked Questions
What are the main benefits of using flex rigid PCBs?
Flex rigid PCBs provide several advantages over rigid PCBs:
- Dynamic flexing and bending in certain areas
- Excellent mechanical shock and vibration resistance
- Lighter weight and thinner profiles
- Reduction in connectors and cables
- Complex 3D shapes and structures
- Integration of discrete electronic modules
What are some examples of products that use flex rigid PCBs?
Flex rigid PCBs enable many innovative electronic products including:
- Wearable devices (smart watches, fitness bands, VR headsets)
- Mobile phones
- Laptops and tablets
- Automotive electronics
- Advanced driver assistance systems (ADAS)
- Internet of things (IoT) products
- Medical devices
What types of materials are used in flex rigid PCB construction?
Common materials include:
- Rigid laminates like FR-4 and polyimide
- Flexible laminates such as polyimide and polyester films
- Adhesives for bonding layers
- Copper foils and trace finishes
- Coverlayers and solder masks
How are the rigid and flexible sections interconnected?
Rigid-flex transition zones use various techniques:
- Plated half-etched ribs for structural stability
- Corner locking features to increase strength
- Tapered edges to reduce stress points
- Bonded layers extending across transition with slots
Careful design of these features ensures durability and reliability.
How should I prepare design files for flex rigid PCB fabrication?
Guidelines include:
- Use a consistent datum in CAD layers for alignment
- Define board outlines, cutouts, slots and routing
- Include rigid-flex transition zones in layout
- Add special notes for materials, finishes and processing
- Consult manufacturer early for design recommendations
Proper design preparation will avoid problems during manufacturing.
Leave a Reply