Introduction to Solder profiles
Solder profiles are critical parameters that define the temperature curve followed during the reflow soldering process. Proper solder profiles ensure reliable solder joints, minimize thermal stress on components, and prevent defects such as bridging, tombstoning, and delamination. When using the eC-reflow-mate, understanding and optimizing solder profiles is essential for achieving high-quality soldering results.
What is a Solder Profile?
A solder profile is a graphical representation of the temperature changes a printed circuit board (PCB) and its components experience during the reflow soldering process. It consists of several stages, including:
- Preheat: The PCB is gradually heated to activate the flux and evaporate solvents.
- Soak: The temperature is maintained to ensure even heat distribution and minimize thermal gradients.
- Reflow: The temperature is increased above the melting point of the solder, allowing it to melt and form solder joints.
- Cooling: The PCB is cooled down to solidify the solder joints and stabilize the assembly.
Importance of Solder Profiles
Proper solder profiles are crucial for several reasons:
- Ensuring reliable solder joints
- Minimizing thermal stress on components
- Preventing defects such as bridging, tombstoning, and delamination
- Achieving optimal wetting and intermetallic compound formation
- Complying with component manufacturers’ specifications
Factors Influencing Solder Profiles
Several factors influence the choice and optimization of solder profiles:
Solder Paste Characteristics
The solder paste used in the reflow process has a significant impact on the solder profile. Different solder alloys have varying melting temperatures and require specific temperature profiles. The flux in the solder paste also affects the profile, as it requires sufficient time and temperature to activate and remove oxides from the surfaces to be soldered.
Component Thermal Limitations
Electronic components have specific thermal limitations that must be considered when designing solder profiles. Exceeding these limits can cause damage or degradation to the components. Manufacturers provide guidelines for maximum temperatures and durations that components can withstand during reflow soldering.
PCB Design and Thermal Mass
The design and thermal mass of the PCB influence the solder profile. Larger PCBs with higher thermal mass require longer preheat and soak times to ensure even heat distribution. The presence of thermal planes, such as ground or power planes, also affects the heat transfer and temperature distribution across the board.
Oven Characteristics
The characteristics of the reflow oven, such as heating zones, convection air flow, and temperature control, play a crucial role in shaping the solder profile. The eC-reflow-mate offers adjustable parameters to customize the solder profile according to the specific requirements of the PCB Assembly.
Oven Parameters for the eC-reflow-mate
The eC-reflow-mate provides several adjustable parameters to optimize the solder profile for different PCB assemblies. These parameters include:
Temperature Settings
The eC-reflow-mate allows users to set the temperatures for each stage of the reflow process:
Stage | Temperature Range (°C) |
---|---|
Preheat | 100-150 |
Soak | 150-180 |
Reflow | 200-250 |
Cooling | Ambient |
Time Settings
The duration of each stage can be adjusted to achieve the desired solder profile:
Stage | Time Range (seconds) |
---|---|
Preheat | 60-120 |
Soak | 60-120 |
Reflow | 30-90 |
Cooling | 60-120 |
Conveyor Speed
The conveyor speed determines the total time the PCB spends in the reflow oven. Adjusting the conveyor speed allows fine-tuning of the solder profile to match the specific requirements of the PCB assembly. The eC-reflow-mate offers conveyor speeds ranging from 10 to 100 cm/min.
Airflow
The eC-reflow-mate provides adjustable airflow settings to control the convection heat transfer within the oven. Higher airflow rates promote faster heating and cooling, while lower airflow rates allow for gentler temperature changes. The airflow can be adjusted from 20% to 100% of the maximum capacity.
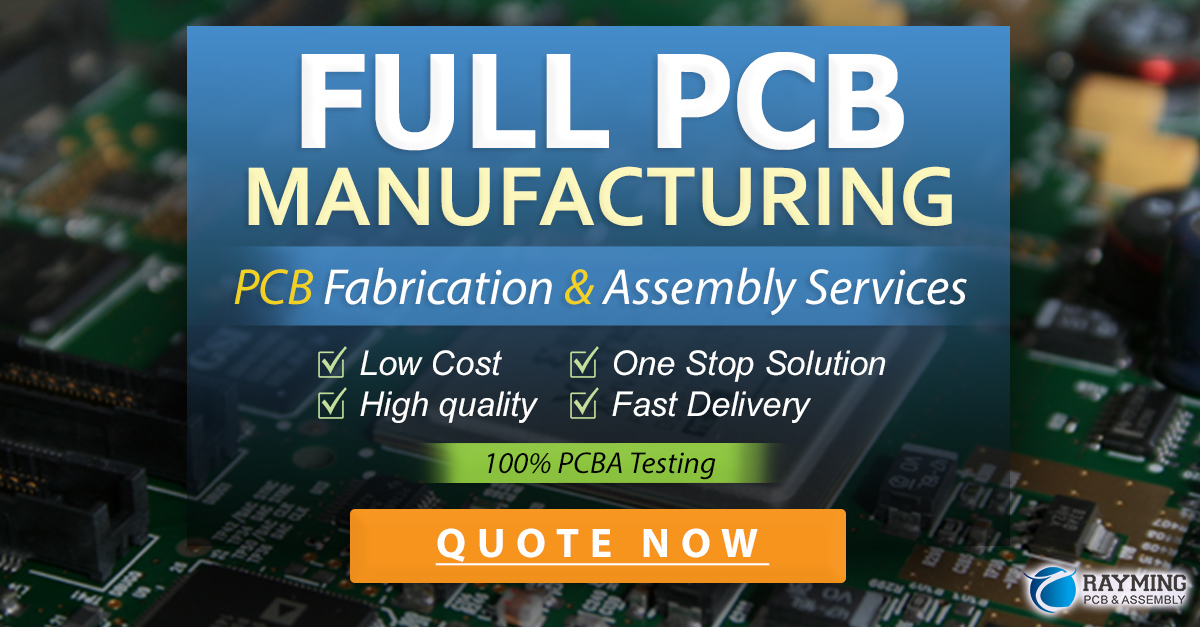
Optimizing Solder Profiles
Optimizing solder profiles involves iterative adjustments and monitoring to achieve the desired temperature curve and ensure reliable soldering results. The following steps can be followed to optimize solder profiles using the eC-reflow-mate:
-
Start with a baseline profile: Begin with a standard solder profile recommended by the solder paste manufacturer or based on the type of PCB and components being soldered.
-
Adjust oven parameters: Use the adjustable parameters of the eC-reflow-mate to fine-tune the solder profile. Modify the temperature settings, time durations, conveyor speed, and airflow to achieve the desired temperature curve.
-
Monitor the actual profile: Use a profiling system or thermocouples to measure the actual temperature profile experienced by the PCB during the reflow process. Compare the measured profile with the target profile to identify any deviations.
-
Analyze and iterate: Analyze the measured profile and make further adjustments to the oven parameters until the desired profile is achieved. Pay attention to key points such as peak temperature, time above liquidus (TAL), and temperature ramp rates.
-
Validate the profile: Once the optimized profile is obtained, run multiple test PCBs to validate the soldering results. Inspect the solder joints for quality and reliability, and make any necessary final adjustments.
Best Practices for Solder Profiles
To ensure optimal soldering results and minimize the risk of defects, consider the following best practices when working with solder profiles and the eC-reflow-mate:
-
Follow component manufacturers’ guidelines: Adhere to the thermal specifications provided by component manufacturers to avoid damage or degradation during the reflow process.
-
Use appropriate solder paste: Select a solder paste that is compatible with the PCB and components being soldered. Consider factors such as alloy composition, particle size, and flux activity.
-
Maintain proper preheat and soak: Ensure sufficient preheat and soak times to activate the flux and evaporate solvents. This helps in achieving better wetting and reduces the risk of defects.
-
Control peak temperature and TAL: Monitor and control the peak temperature and time above liquidus (TAL) to prevent overheating and ensure proper solder joint formation.
-
Optimize cooling rate: Adjust the cooling rate to allow gradual solidification of the solder joints and minimize thermal stress on the components.
-
Regularly maintain the oven: Perform regular maintenance on the eC-reflow-mate, including cleaning the heating elements, conveyor belt, and sensors to ensure consistent performance and accurate temperature control.
Frequently Asked Questions (FAQ)
-
Q: What is the recommended solder profile for lead-free solder paste?
A: Lead-free solder pastes typically require higher reflow temperatures compared to leaded solder pastes. A typical lead-free solder profile includes a peak temperature of 240-250°C and a time above liquidus (TAL) of 60-90 seconds. However, it is essential to refer to the specific recommendations provided by the solder paste manufacturer. -
Q: How do I know if my solder profile is optimal?
A: An optimal solder profile should achieve good wetting, proper solder joint formation, and minimal thermal stress on the components. Visual inspection of the soldered PCB can provide indications of the profile’s effectiveness. Look for smooth and shiny solder joints, absence of bridging or tombstoning, and no signs of component damage or discoloration. Additionally, using a profiling system to measure the actual temperature profile can help in verifying the solder profile’s accuracy. -
Q: Can I use the same solder profile for different PCBs?
A: While it is possible to use the same solder profile for similar PCBs with comparable components and thermal requirements, it is recommended to optimize the solder profile for each specific PCB design. Different PCBs may have varying thermal masses, component densities, and heat distribution patterns, which can affect the optimal solder profile. It is advisable to fine-tune the profile for each PCB to ensure the best soldering results. -
Q: How often should I perform maintenance on the eC-reflow-mate?
A: Regular maintenance of the eC-reflow-mate is crucial for ensuring consistent performance and accurate temperature control. The frequency of maintenance depends on the usage and environmental conditions. As a general guideline, it is recommended to perform basic cleaning and inspection of the heating elements, conveyor belt, and sensors every 100 hours of operation or as specified in the manufacturer’s manual. Additionally, periodic calibration of the temperature sensors may be necessary to maintain accurate temperature readings. -
Q: What should I do if I encounter soldering defects despite using an optimized solder profile?
A: If soldering defects persist even after optimizing the solder profile, consider the following troubleshooting steps: - Verify the accuracy of the temperature measurements using a profiling system or thermocouples.
- Check the condition and placement of the solder paste on the PCB pads.
- Ensure proper alignment and seating of components on the PCB.
- Review the PCB design for any potential issues, such as improper pad sizing or insufficient clearances.
- Investigate the reflow oven’s performance, including heating element functionality and airflow uniformity.
If the defects continue, consult with experienced professionals or the equipment manufacturer for further assistance and guidance.
Conclusion
Solder profiles and oven parameters play a critical role in achieving high-quality and reliable soldering results when using the eC-reflow-mate. By understanding the factors influencing solder profiles, adjusting the oven parameters, and following best practices, users can optimize the reflow soldering process for their specific PCB assemblies. Regular monitoring, analysis, and maintenance of the solder profiles and the reflow oven ensure consistent and defect-free soldering outcomes. With the proper knowledge and application of solder profiles and oven parameters, the eC-reflow-mate can be an effective tool for achieving excellent soldering results in Electronic Manufacturing.
Leave a Reply