Introduction to DRC in CAD
Design Rule Checking (DRC) is an essential step in the electronic design automation (EDA) process that helps ensure the manufacturability and reliability of integrated circuits (ICs) and printed circuit boards (PCBs). DRC involves verifying that a design complies with a set of predefined rules and constraints specified by the fabrication process and design requirements. These rules cover various aspects of the design, such as minimum feature sizes, spacing between elements, and layer-specific constraints.
Most modern CAD packages, such as Cadence Virtuoso, Synopsys IC Compiler, and Mentor Graphics Calibre, have built-in DRC tools that allow designers to perform rule checks at different stages of the design process. By running DRC regularly, designers can identify and fix potential issues early in the design cycle, reducing the risk of costly redesigns and fabrication failures.
Importance of DRC in the Design Flow
DRC plays a critical role in the overall design flow, ensuring that designs are correct, manufacturable, and meet the required specifications. Some of the key reasons why DRC is essential include:
-
Manufacturability: DRC ensures that the design can be successfully fabricated using the intended manufacturing process. By checking the design against the process-specific design rules, DRC helps avoid potential manufacturing issues, such as shorts, opens, and insufficient spacing between elements.
-
Reliability: DRC helps identify potential reliability issues, such as electromigration, antenna effects, and latch-up, which can impact the long-term performance and reliability of the manufactured device.
-
Design optimization: DRC can help designers optimize their designs by identifying areas where the design rules are not being fully utilized, allowing for potential improvements in performance, power consumption, or area.
-
Time and cost savings: By catching design issues early in the design process, DRC can help reduce the time and cost associated with redesigns and fabrication re-spins.
Common DRC Rules and Constraints
DRC rules and constraints vary depending on the specific fabrication process and design requirements. However, there are several common categories of rules that are typically checked in most DRC runs:
Geometric Rules
Geometric rules define the minimum feature sizes and spacing requirements for different layers and elements in the design. Some common geometric rules include:
- Minimum width: The smallest allowed width for a feature on a given layer.
- Minimum spacing: The smallest allowed distance between two features on the same layer.
- Minimum area: The smallest allowed area for a feature on a given layer.
- Minimum enclosure: The minimum amount of overlap required between features on different layers.
Connectivity Rules
Connectivity rules ensure that the design has the proper connections between different elements and layers. Some common connectivity rules include:
- Antenna rules: Limit the maximum allowed ratio between the metal area and the gate area connected to it, to prevent antenna effects during fabrication.
- Via rules: Define the minimum size, spacing, and overlap requirements for vias connecting different metal layers.
- Short and open checks: Verify that there are no unintended shorts or opens in the design.
Electrical Rules
Electrical rules check for potential electrical issues in the design, such as electromigration and latch-up. Some common electrical rules include:
- Current density rules: Limit the maximum allowed current density in metal lines to prevent electromigration.
- Latch-up rules: Ensure that the spacing between NMOS and PMOS transistors is sufficient to prevent latch-up.
- ESD rules: Verify that the design has proper electrostatic discharge (ESD) protection measures in place.
Setting Up DRC in CAD Packages
Most modern CAD packages provide a built-in DRC tool that allows designers to perform rule checks on their designs. The specific steps for setting up and running DRC may vary depending on the CAD package being used, but the general process typically involves the following steps:
-
Importing design rules: The first step is to import the design rules specific to the fabrication process being used. These rules are usually provided by the foundry or the fabrication facility in a standard format, such as the Standard Verification Rule Format (SVRF) or the Design Rule Exchange Format (DREF).
-
Configuring rule decks: Once the design rules are imported, the next step is to configure the rule decks for the specific design. This involves selecting the relevant rules and constraints for each layer and element in the design, and setting the appropriate parameters and thresholds.
-
Running DRC: With the rule decks configured, designers can run DRC on their designs. The DRC tool will analyze the design and report any violations of the specified rules and constraints. The results are typically displayed in a graphical format, with markers indicating the location and type of each violation.
-
Reviewing and fixing violations: After running DRC, designers need to review the reported violations and determine how to fix them. This may involve modifying the design, adjusting the rule parameters, or waiving certain violations if they are deemed acceptable based on the design requirements.
Example DRC Setup in Cadence Virtuoso
Here’s an example of how to set up and run DRC in the Cadence Virtuoso CAD package:
-
Import the foundry-provided design rule files (e.g., in SVRF format) into the Virtuoso DRC tool.
-
Create a new DRC rule deck or modify an existing one to include the relevant rules for your design. This can be done using the Rule Deck Editor in Virtuoso.
-
Specify the layers and elements to be checked, and set the appropriate rule parameters and thresholds. For example:
Layer | Rule | Value |
---|---|---|
METAL1 | Minimum width | 0.1 µm |
METAL1 | Minimum spacing | 0.1 µm |
VIA1 | Minimum size | 0.2 µm |
VIA1 | Minimum enclosure METAL1 | 0.05 µm |
-
Run DRC on your design by selecting the appropriate rule deck and clicking the “Run DRC” button in the Virtuoso DRC tool.
-
Review the DRC results using the Virtuoso DRC Results Viewer, which displays the violations graphically and provides options for navigating and filtering the results.
-
Fix the reported violations by modifying your design or waiving acceptable violations using the Virtuoso DRC Results Viewer.
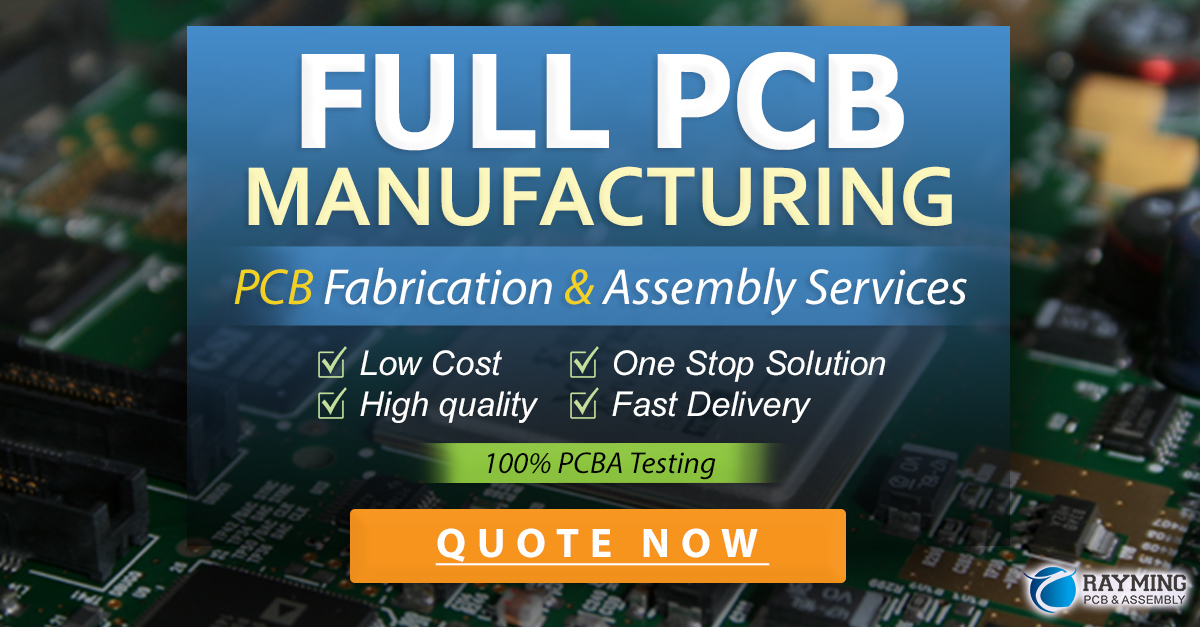
Best Practices for DRC
To ensure the effectiveness of DRC and minimize the risk of design issues, designers should follow some best practices when setting up and running DRC:
-
Run DRC regularly: Run DRC checks at regular intervals during the design process, such as after completing each major design stage or before submitting the design for fabrication. This helps catch potential issues early and reduces the risk of costly redesigns.
-
Use up-to-date rule decks: Ensure that you are using the most up-to-date design rule files provided by the foundry or fabrication facility. Process technologies and design rules can change over time, so it’s important to use the latest available information.
-
Customize rule decks for your design: While foundry-provided rule decks are a good starting point, designers should customize the rules and constraints based on their specific design requirements. This may involve adjusting rule parameters, waiving certain rules, or adding custom checks.
-
Collaborate with the fabrication team: Work closely with the fabrication team to ensure that your DRC setup aligns with their expectations and requirements. They can provide guidance on interpreting design rules, handling complex design structures, and resolving any ambiguities in the rule definitions.
-
Document and track violations: Maintain a clear record of DRC violations and how they were resolved. This can help identify recurring issues, improve the design process, and serve as a reference for future designs.
-
Use automated tools for violation fixing: Many CAD packages offer automated tools for fixing common DRC violations, such as spacing or width violations. Utilizing these tools can save time and effort in the design process.
-
Perform thorough design reviews: In addition to running DRC, conduct thorough design reviews to catch potential issues that may not be covered by the automated checks. This can include examining the design for performance, power, and reliability concerns.
FAQ
1. What is the difference between DRC and LVS (Layout vs. Schematic)?
DRC focuses on verifying that the physical layout of a design complies with the manufacturing process rules and constraints, while LVS checks that the layout matches the intended circuit schematic. DRC ensures manufacturability and reliability, while LVS ensures functional correctness.
2. How often should I run DRC during the design process?
It is recommended to run DRC checks at regular intervals, such as after completing each major design stage or before submitting the design for fabrication. Running DRC regularly helps catch potential issues early and reduces the risk of costly redesigns.
3. What should I do if I encounter a DRC violation that I believe is acceptable for my design?
If you believe a DRC violation is acceptable based on your design requirements, you can choose to waive the violation. However, it’s important to document the waiver and the rationale behind it, and to consult with the fabrication team to ensure that the waiver is indeed acceptable.
4. Can DRC catch all potential design issues?
While DRC is an essential tool for verifying design manufacturability and reliability, it cannot catch all potential issues. Some problems, such as performance or power concerns, may require additional simulation and analysis. It’s important to use DRC in conjunction with other verification methods and thorough design reviews.
5. What are the consequences of not running DRC or ignoring DRC violations?
Not running DRC or ignoring DRC violations can lead to various problems, such as:
- Manufacturing failures: The design may not be manufacturable, resulting in low yields or complete fabrication failures.
- Reliability issues: The manufactured device may suffer from reliability problems, such as electromigration or latch-up, which can impact its long-term performance.
- Redesign costs: If design issues are caught late in the process, it may require costly and time-consuming redesigns and re-fabrication.
To avoid these consequences, it is crucial to prioritize DRC and address any violations promptly.
Conclusion
DRC is a critical step in the electronic design process, ensuring that designs are manufacturable, reliable, and compliant with the specified design rules and constraints. By setting up and running DRC regularly in CAD packages, designers can catch potential issues early, optimize their designs, and minimize the risk of costly fabrication failures.
To make the most of DRC, designers should follow best practices such as using up-to-date rule decks, customizing rules for their specific designs, collaborating with the fabrication team, and documenting violations and waivers. By incorporating DRC into their design flow and addressing violations promptly, designers can improve the quality and reliability of their electronic products.
Leave a Reply