Introduction to Digital Twin Technology
A digital twin is a virtual representation of a physical object, process, or system that spans its lifecycle, is updated from real-time data, and uses simulation, machine learning, and reasoning to help decision-making. It is a powerful tool that enables manufacturers to optimize their processes, predict failures, and improve overall efficiency.
Key Components of a Digital Twin
- Physical Entity: The physical object, process, or system that the digital twin represents.
- Virtual Model: A digital replica of the physical entity that includes its properties, behavior, and performance.
- Data: Real-time data collected from sensors, IoT devices, and other sources that update the virtual model.
- Analytics: Algorithms and machine learning models that analyze the data and provide insights and predictions.
Benefits of Digital Twin Technology
- Improved Efficiency: Digital twins enable manufacturers to optimize their processes, reduce downtime, and improve overall efficiency.
- Predictive Maintenance: By analyzing real-time data, digital twins can predict when equipment is likely to fail, enabling proactive maintenance.
- Better Decision Making: Digital twins provide insights and predictions that enable better decision making, from product design to production planning.
- Reduced Costs: By optimizing processes and reducing downtime, digital twins can help manufacturers reduce costs and improve profitability.
Applications of Digital Twin Technology in Manufacturing
Product Design and Development
Digital twins can be used to simulate and optimize product designs before they are physically built. This enables manufacturers to:
- Test and validate designs virtually, reducing the need for physical prototypes.
- Optimize designs for performance, durability, and manufacturability.
- Collaborate with suppliers and customers to ensure that designs meet their requirements.
Benefits of Digital Twins in Product Design | Description |
---|---|
Reduced Time to Market | Virtual testing and validation accelerates the design process. |
Improved Product Quality | Designs can be optimized for performance and durability. |
Lower Development Costs | Fewer physical prototypes are required, reducing costs. |
Production Planning and Optimization
Digital twins can be used to simulate and optimize production processes, enabling manufacturers to:
- Identify bottlenecks and inefficiencies in the production process.
- Test and validate production schedules and resource allocation.
- Optimize production parameters such as speed, temperature, and pressure.
Benefits of Digital Twins in Production Planning | Description |
---|---|
Increased Throughput | Bottlenecks and inefficiencies can be identified and eliminated. |
Improved Resource Utilization | Production schedules and resource allocation can be optimized. |
Reduced Waste and Scrap | Production parameters can be optimized to reduce waste and scrap. |
Predictive Maintenance
Digital twins can be used to predict when equipment is likely to fail, enabling proactive maintenance. This involves:
- Collecting real-time data from sensors and IoT devices on the equipment.
- Analyzing the data using machine learning algorithms to predict when failures are likely to occur.
- Scheduling maintenance activities based on the predictions to prevent unplanned downtime.
Benefits of Digital Twins in Predictive Maintenance | Description |
---|---|
Reduced Unplanned Downtime | Equipment failures can be predicted and prevented. |
Lower Maintenance Costs | Maintenance activities can be scheduled based on actual need rather than fixed intervals. |
Improved Equipment Reliability | Proactive maintenance improves overall equipment reliability. |
Supply Chain Optimization
Digital twins can be used to simulate and optimize supply chain operations, enabling manufacturers to:
- Monitor and track the flow of materials and products throughout the supply chain.
- Identify potential disruptions and bottlenecks in the supply chain.
- Optimize inventory levels and logistics to reduce costs and improve responsiveness.
Benefits of Digital Twins in Supply Chain Optimization | Description |
---|---|
Improved Visibility | The flow of materials and products can be monitored and tracked in real-time. |
Reduced Disruptions | Potential disruptions and bottlenecks can be identified and mitigated. |
Lower Inventory Costs | Inventory levels can be optimized based on real-time demand and supply data. |
Challenges and Considerations
Data Quality and Integration
One of the key challenges in implementing digital twin technology is ensuring the quality and integration of data from multiple sources. This involves:
- Establishing data standards and protocols to ensure consistency and accuracy.
- Integrating data from various systems and devices, including legacy systems.
- Ensuring data security and privacy, especially for sensitive or proprietary information.
Skill and Talent Gap
Implementing digital twin technology requires a range of skills and expertise, including:
- Data science and analytics
- IoT and sensor technology
- Simulation and modeling
- Domain expertise in manufacturing processes
Many organizations may face a skill and talent gap in these areas, requiring investment in training and recruitment.
ROI and Business Case
Implementing digital twin technology can be a significant investment, requiring a clear business case and ROI. Factors to consider include:
- The potential benefits in terms of efficiency, quality, and cost savings.
- The costs of implementation, including hardware, software, and talent.
- The timeline for realizing the benefits and achieving ROI.
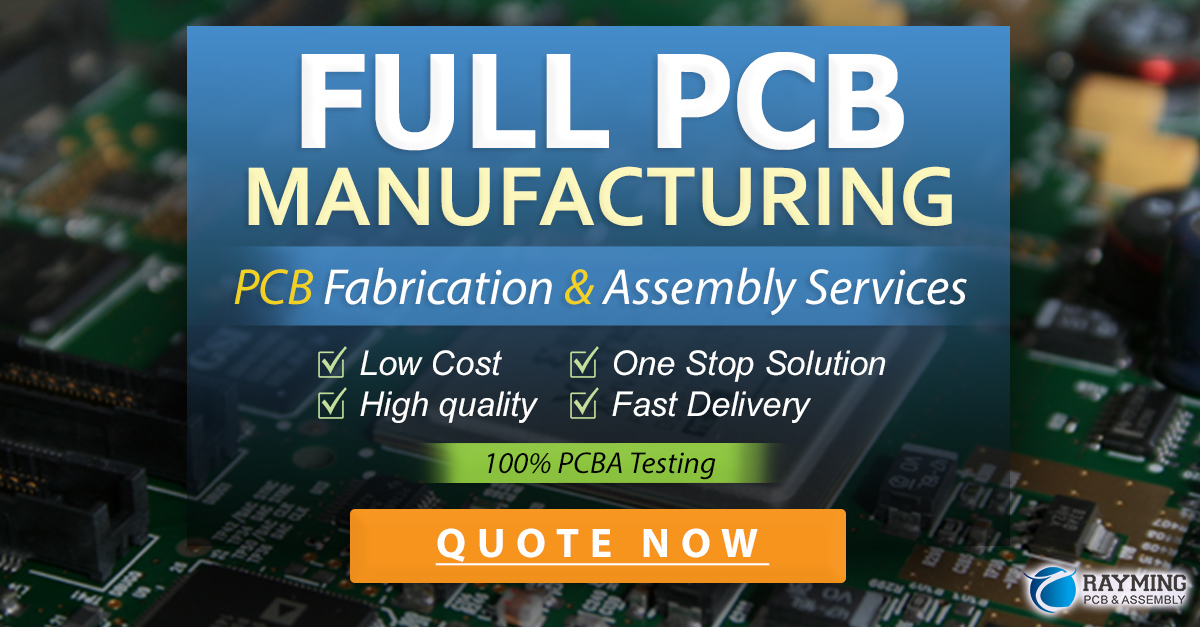
Future Trends and Developments
Integration with Other Technologies
Digital twin technology is likely to be increasingly integrated with other emerging technologies, such as:
- Artificial Intelligence and Machine Learning: Enhancing the analytics and decision-making capabilities of digital twins.
- Augmented and Virtual Reality: Enabling immersive visualization and interaction with digital twins.
- Edge Computing: Enabling real-time processing and analysis of data at the source, reducing latency and bandwidth requirements.
Expansion to Other Industries
While digital twin technology has been pioneered in the manufacturing industry, it is likely to be adopted in other industries, such as:
- Healthcare: Enabling personalized medicine and treatment planning based on patient-specific digital twins.
- Construction: Enabling virtual design, simulation, and optimization of buildings and infrastructure.
- Aerospace: Enabling virtual testing and certification of aircraft and spacecraft designs.
Frequently Asked Questions (FAQ)
- What is the difference between a digital twin and a simulation?
-
A digital twin is a virtual representation of a specific physical asset, while a simulation is a general model of a system or process. Digital twins are updated with real-time data from the physical asset, while simulations are typically based on historical data or assumptions.
-
How much does it cost to implement a digital twin?
-
The cost of implementing a digital twin depends on various factors, such as the complexity of the system being modeled, the amount of data being collected and processed, and the specific hardware and software requirements. In general, implementing a digital twin can be a significant investment, but the potential benefits in terms of efficiency, quality, and cost savings can justify the expense.
-
What are the key skills required for implementing a digital twin?
-
Implementing a digital twin requires a range of skills, including data science and analytics, IoT and sensor technology, simulation and modeling, and domain expertise in the specific industry or process being modeled. Organizations may need to invest in training and recruitment to acquire these skills.
-
How do digital twins handle data privacy and security?
-
Digital twins often involve the collection and processing of sensitive or proprietary data, so data privacy and security are critical considerations. Organizations need to establish data standards and protocols to ensure consistency and accuracy, as well as robust security measures to protect against unauthorized access or breaches.
-
What are some of the industries that are likely to adopt digital twin technology in the future?
- While digital twin technology has been pioneered in the manufacturing industry, it is likely to be adopted in other industries such as healthcare, construction, and aerospace. In healthcare, digital twins could enable personalized medicine and treatment planning based on patient-specific models. In construction, digital twins could enable virtual design, simulation, and optimization of buildings and infrastructure. In aerospace, digital twins could enable virtual testing and certification of aircraft and spacecraft designs.
Conclusion
Digital twin technology is a powerful tool that enables manufacturers to optimize their processes, predict failures, and improve overall efficiency. By creating a virtual representation of a physical object, process, or system, manufacturers can gain real-time insights and make better decisions.
While implementing digital twin technology can be challenging, requiring significant investment and a range of skills and expertise, the potential benefits in terms of efficiency, quality, and cost savings make it a compelling proposition for many organizations.
As digital twin technology continues to evolve and mature, it is likely to be adopted in a wider range of industries and applications, from healthcare to construction to aerospace. By embracing this powerful technology, organizations can gain a competitive edge and drive innovation in their respective fields.
Leave a Reply