Understanding PCB component clearance
PCB component clearance refers to the minimum distance between components, pads, and traces on a PCB. Maintaining appropriate clearance is essential to prevent short circuits, signal interference, and manufacturing issues. Insufficient clearance can lead to problems such as solder bridging, reduced insulation resistance, and difficulties in assembly and inspection.
Types of PCB Component Clearance
There are several types of component clearance to consider in PCB design:
- Pad-to-Pad Clearance: The distance between two adjacent component pads.
- Pad-to-Trace Clearance: The distance between a component pad and a nearby trace.
- Trace-to-Trace Clearance: The distance between two adjacent traces.
- Component-to-Component Clearance: The distance between two adjacent components.
- Component-to-Board Edge Clearance: The distance between a component and the edge of the PCB.
IPC Standards for PCB Component Clearance
The IPC provides several standards that address PCB design and manufacturing, including guidelines for component clearance. The most relevant standards for component clearance are:
- IPC-2221: Generic Standard on Printed Board Design
- IPC-7351: Generic Requirements for Surface Mount Design and Land Pattern Standard
- IPC-A-610: Acceptability of Electronic Assemblies
IPC-2221: Generic Standard on Printed Board Design
IPC-2221 provides general guidelines for PCB design, including recommendations for minimum component clearance. According to IPC-2221, the minimum clearance between components depends on several factors, such as the component package type, voltage requirements, and environmental conditions.
The standard provides a table with recommended minimum clearances for various scenarios:
Clearance Type | Voltage (V) | Minimum Clearance (mm) |
---|---|---|
Pad-to-Pad | 0-100 | 0.1 |
101-300 | 0.2 | |
301-500 | 0.5 | |
Pad-to-Trace | 0-100 | 0.1 |
101-300 | 0.2 | |
301-500 | 0.5 | |
Trace-to-Trace | 0-100 | 0.1 |
101-300 | 0.2 | |
301-500 | 0.5 |
These values serve as a starting point for PCB design, but designers should also consider other factors such as the manufacturing process, assembly requirements, and end-use environment when determining the appropriate clearance.
IPC-7351: Generic Requirements for Surface Mount Design and Land Pattern Standard
IPC-7351 focuses on surface mount technology (SMT) and provides guidelines for Land Pattern Design and component placement. The standard includes recommendations for minimum component clearance based on the package type and size.
For example, consider a 0402 (1005 metric) chip resistor. According to IPC-7351, the recommended minimum pad-to-pad clearance is 0.2 mm, and the minimum pad-to-trace clearance is 0.1 mm.
IPC-A-610: Acceptability of Electronic Assemblies
IPC-A-610 is a widely-used standard for electronic assembly acceptance criteria. While it does not provide specific recommendations for minimum component clearance, it does emphasize the importance of maintaining sufficient clearance to ensure proper assembly and reliability.
The standard defines three classes of electronic assemblies based on their intended end-use:
- Class 1: General Electronic Products
- Class 2: Dedicated Service Electronic Products
- Class 3: High Performance Electronic Products
Each class has different acceptance criteria for various aspects of PCB Assembly, including component placement and soldering. Designers should consider the target assembly class when determining the appropriate component clearance.
Factors Affecting PCB Component Clearance
Several factors influence the minimum component clearance required for a PCB design:
- Voltage and Current: Higher voltage and current applications require greater clearance to prevent arcing and maintain insulation resistance.
- Operating Environment: PCBs exposed to harsh environments, such as high humidity or vibration, may require increased clearance to ensure reliability.
- Manufacturing Process: Different PCB manufacturing processes have varying capabilities and limitations. Designers should consider the minimum feature sizes and tolerances achievable by the chosen fabrication and assembly processes.
- Component Package: The size and shape of component packages affect the required clearance. Smaller packages, such as chip components, generally require less clearance than larger packages, such as through-hole components.
- Signal Integrity: High-speed or sensitive signals may require increased clearance to minimize crosstalk and electromagnetic interference (EMI).
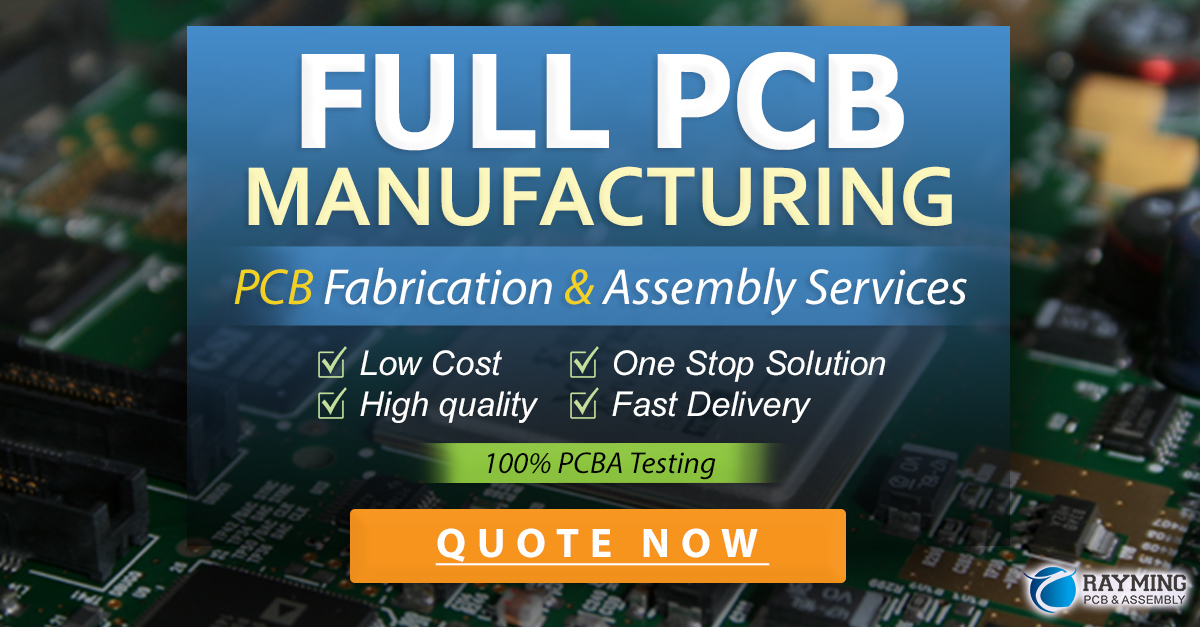
Best Practices for PCB Component Clearance
To ensure optimal PCB design and manufacturability, consider the following best practices for component clearance:
- Follow IPC Standards: Use the recommendations provided in IPC-2221, IPC-7351, and other relevant standards as a starting point for determining component clearance.
- Consult with Manufacturers: Discuss your design requirements with your PCB fabrication and assembly partners to ensure that your clearance specifications are achievable and cost-effective.
- Consider the End-Use Environment: Evaluate the expected operating conditions and adjust clearance accordingly to maintain reliability and performance.
- Use CAD Tools: Utilize PCB design software with built-in design rule checks (DRC) to verify that your component clearance meets the specified requirements.
- Plan for Manufacturing Tolerances: Incorporate appropriate tolerances in your clearance specifications to account for variations in the manufacturing process.
FAQ
Q1. What is the minimum pad-to-pad clearance for a 0603 chip component according to IPC-7351?
A1. According to IPC-7351, the recommended minimum pad-to-pad clearance for a 0603 (1608 metric) chip component is 0.2 mm.
Q2. How does voltage affect the required component clearance?
A2. Higher voltage applications require greater clearance to prevent arcing and maintain insulation resistance. IPC-2221 provides recommended minimum clearances based on voltage ranges.
Q3. What factors should be considered when determining the appropriate component clearance for a PCB design?
A3. Factors to consider include voltage and current requirements, operating environment, manufacturing process capabilities, component package size and shape, and signal integrity requirements.
Q4. Can PCB design software help ensure proper component clearance?
A4. Yes, modern PCB design software often includes design rule checks (DRC) that can verify component clearance based on user-defined specifications, helping to ensure that the design meets the required clearance guidelines.
Q5. What should designers do if they are unsure about the appropriate component clearance for their PCB?
A5. Designers should consult relevant IPC standards, discuss their requirements with PCB fabrication and assembly partners, and consider the end-use environment and manufacturing tolerances when determining the appropriate component clearance for their specific design.
Conclusion
Maintaining proper component clearance is essential for ensuring the functionality, manufacturability, and reliability of PCBs. The IPC standards, particularly IPC-2221 and IPC-7351, provide valuable guidelines for determining the minimum clearance requirements based on factors such as voltage, component package, and manufacturing process.
By following these guidelines, consulting with manufacturing partners, and considering the end-use environment, PCB designers can create designs that meet the necessary clearance requirements while optimizing performance and cost-effectiveness. Utilizing PCB design software with built-in design rule checks can further help ensure that component clearance specifications are met throughout the design process.
Ultimately, a well-designed PCB with appropriate component clearance will contribute to a more reliable and manufacturable product, reducing the risk of issues such as short circuits, signal interference, and assembly defects.
Leave a Reply