Introduction to PCB Design Flow
Printed Circuit Board (PCB) design is a complex process that involves multiple steps and considerations. To ensure a successful PCB design, it is essential to follow an optimized design flow that encompasses all the necessary stages from concept to manufacturing. In this article, we will explore the optimum PCB design flow, discussing each step in detail and providing insights into best practices and common challenges.
Understanding the PCB Design Process
Key Steps in the PCB Design Flow
- Concept and Requirements Gathering
- Schematic Design
- Component Selection
- PCB Layout
- Design Rule Check (DRC) and verification
- Gerber File Generation
- Manufacturing and Assembly
Importance of Following an Optimized Design Flow
Following an optimized PCB design flow is crucial for several reasons:
- Ensures the design meets all functional and performance requirements
- Reduces the risk of design errors and costly revisions
- Improves the overall quality and reliability of the PCB
- Facilitates smoother communication between design team members
- Streamlines the manufacturing and assembly process
Step 1: Concept and Requirements Gathering
Defining Project Goals and Objectives
The first step in the PCB design flow is to clearly define the project goals and objectives. This involves understanding the intended application, target market, and any specific requirements or constraints. Some key considerations include:
- Functionality and features of the PCB
- Performance requirements (speed, power, signal integrity)
- Environmental factors (temperature, humidity, vibration)
- Size and form factor constraints
- Budget and timeline
Creating a Design Specification Document
Once the project goals and objectives are established, it is essential to create a comprehensive design specification document. This document serves as a blueprint for the entire design process and should include:
- Detailed functional and performance requirements
- Bill of Materials (BOM) with component specifications
- Interface and connectivity requirements
- Power supply and distribution specifications
- Mechanical and environmental constraints
- Testing and validation criteria
Having a well-defined design specification document helps ensure that all stakeholders are aligned and reduces the risk of miscommunication or scope creep.
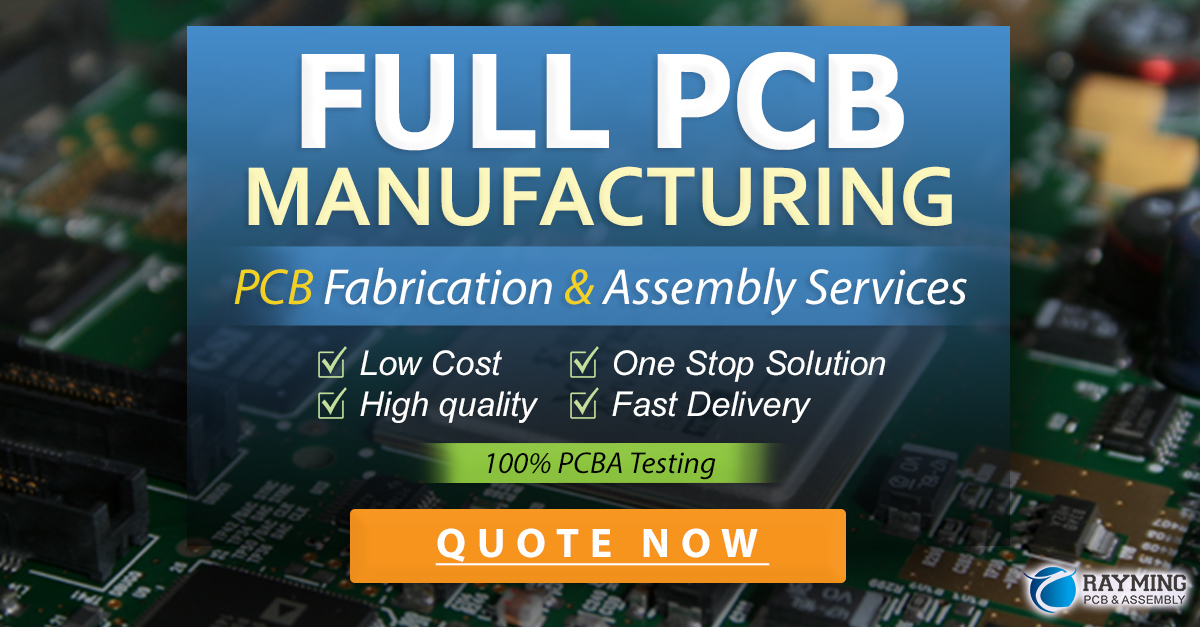
Step 2: Schematic Design
Capturing the Circuit Diagram
The schematic design stage involves capturing the circuit diagram using Electronic Design Automation (EDA) tools such as Altium Designer, OrCAD, or KiCad. The schematic should accurately represent the electrical connections and components of the PCB. Some best practices for schematic design include:
- Using clear and consistent naming conventions for components and nets
- Organizing the schematic into logical hierarchical blocks
- Providing comprehensive component annotations and notes
- Following industry-standard symbols and designators
Verifying the Schematic
Once the schematic is complete, it is crucial to thoroughly verify its accuracy and integrity. This involves:
- Checking for proper component connections and polarities
- Verifying power supply and ground connections
- Ensuring proper signal integrity and impedance matching
- Performing a design rule check (DRC) to identify any errors or violations
Catching and correcting schematic errors early in the design process can save significant time and resources later on.
Step 3: Component Selection
Choosing the Right Components
Selecting the appropriate components is a critical step in the PCB design flow. Factors to consider when choosing components include:
- Functionality and performance requirements
- Availability and lead times
- Cost and budget constraints
- Footprint and packaging compatibility
- Reliability and quality ratings
It is essential to work closely with component suppliers and distributors to ensure the selected components meet all the necessary specifications and are readily available.
Creating the Bill of Materials (BOM)
The Bill of Materials (BOM) is a comprehensive list of all the components required for the PCB Assembly. A well-organized BOM should include:
- Component reference designators
- Manufacturer part numbers
- Descriptions and specifications
- Quantities and units of measure
- Supplier information and pricing
Maintaining an accurate and up-to-date BOM throughout the design process helps streamline purchasing and assembly, reducing the risk of delays or errors.
Step 4: PCB Layout
Placing Components and Routing Traces
The PCB layout stage involves physically placing components on the board and routing the electrical connections between them. Some key considerations for component placement include:
- Optimizing for signal integrity and power distribution
- Minimizing the overall board size and layer count
- Ensuring proper thermal management and heat dissipation
- Facilitating easy assembly and manufacturing
When routing traces, it is essential to follow best practices such as:
- Using appropriate trace widths and spacings for the required current and voltage
- Minimizing the trace lengths and avoiding sharp angles
- Providing proper grounding and shielding for sensitive signals
- Adhering to the specified design rules and constraints
Conducting Signal Integrity Analysis
Signal integrity analysis is a critical step in the PCB layout process, particularly for high-speed or analog designs. This involves simulating and analyzing the behavior of signals on the PCB to ensure proper timing, impedance matching, and noise reduction. Some common techniques for signal integrity analysis include:
- Time-domain reflectometry (TDR) analysis
- Impedance matching and termination
- Crosstalk and electromagnetic interference (EMI) simulation
- Power and ground plane analysis
Conducting thorough signal integrity analysis helps identify and mitigate potential issues before the PCB is manufactured, reducing the risk of costly redesigns or performance problems.
Step 5: Design Rule Check (DRC) and Verification
Running DRC and Addressing Violations
Design Rule Check (DRC) is an automated process that verifies the PCB layout against a set of predefined design rules and constraints. These rules typically cover aspects such as:
- Minimum trace widths and spacings
- Clearance between components and traces
- Via and pad sizes and drilling requirements
- Silk screen and solder mask guidelines
Running a comprehensive DRC helps identify any design rule violations or potential manufacturability issues. It is essential to carefully review and address all DRC violations before proceeding to the next stage of the design flow.
Performing a Final Design Review
Once the DRC is complete and all violations have been addressed, it is important to conduct a final design review. This involves a thorough visual inspection of the PCB layout, checking for any errors or inconsistencies that may have been missed by the automated checks. Some key aspects to review include:
- Component placement and orientation
- Trace routing and connectivity
- Power and ground distribution
- Mechanical dimensions and mounting holes
- Silkscreen and assembly markings
A comprehensive final design review helps catch any remaining issues and ensures the PCB is ready for manufacturing.
Step 6: Gerber File Generation
Creating Manufacturing Files
Once the PCB design is finalized and verified, the next step is to generate the necessary manufacturing files. The most common format for PCB manufacturing files is Gerber, which is a standard used by PCB fabrication houses worldwide. Gerber files contain all the information needed to manufacture the PCB, including:
- Copper layer layouts (top, bottom, and inner layers)
- Solder mask and silkscreen layers
- Drill files and aperture lists
- Fabrication notes and instructions
It is essential to carefully review the generated Gerber files to ensure they accurately represent the intended PCB design.
Communicating with the PCB Manufacturer
Before sending the Gerber files to the PCB manufacturer, it is important to establish clear communication and provide all the necessary information. This includes:
- Specifying the PCB material, thickness, and copper weight
- Defining the surface finish and solder mask requirements
- Providing the BOM and assembly instructions
- Clarifying any special requirements or constraints
Maintaining open and effective communication with the PCB manufacturer helps ensure a smooth and successful production process.
Step 7: Manufacturing and Assembly
PCB Fabrication Process
The PCB fabrication process involves several key steps:
- Preparing the PCB material (typically FR-4) and applying the copper foil
- Printing and developing the photoresist pattern for each layer
- Etching away the unwanted copper to form the traces and pads
- Drilling the via and mounting holes
- Applying the solder mask and silkscreen layers
- Performing electrical testing and inspection
Understanding the PCB fabrication process helps designers make informed decisions and communicate effectively with manufacturers.
PCB Assembly and Testing
Once the PCB is fabricated, the next step is to assemble the components onto the board. This typically involves:
- Applying solder paste to the pads using a stencil
- Placing the components onto the board using pick-and-place machines
- Reflowing the solder in a controlled oven to form the electrical connections
- Inspecting the assembled PCB for any defects or issues
- Performing functional testing to verify the PCB’s operation
Thorough testing and inspection during the assembly process helps identify and correct any issues before the PCB is shipped to the end customer.
Common Challenges and Best Practices
Dealing with High-Speed Design Constraints
Designing PCBs for high-speed applications presents unique challenges, such as managing signal integrity, controlling impedance, and minimizing crosstalk. Some best practices for high-speed PCB design include:
- Using controlled impedance traces and terminations
- Implementing proper grounding and shielding techniques
- Minimizing the use of vias and layer transitions
- Conducting thorough signal integrity simulations and analysis
Managing Thermal Considerations
Thermal management is a critical aspect of PCB design, particularly for high-power or densely populated boards. Some strategies for managing thermal issues include:
- Providing adequate copper pour and heat-sinking for power components
- Using thermal vias to conduct heat away from hot spots
- Implementing proper airflow and cooling mechanisms
- Conducting thermal simulations to identify and mitigate potential issues
Ensuring Manufacturability and Reliability
To ensure the manufacturability and reliability of the PCB, it is essential to follow best practices such as:
- Adhering to the specified design rules and constraints
- Using standard component footprints and packaging
- Providing clear and comprehensive fabrication and assembly instructions
- Conducting thorough testing and inspection at each stage of the process
By focusing on manufacturability and reliability throughout the design flow, designers can minimize the risk of production delays, quality issues, or field failures.
Frequently Asked Questions (FAQ)
- What is the importance of creating a comprehensive design specification document?
-
A comprehensive design specification document serves as a blueprint for the entire PCB design process. It ensures that all stakeholders are aligned on the project goals, requirements, and constraints, reducing the risk of miscommunication or scope creep. The document should include detailed functional and performance requirements, bill of materials, interface and connectivity specifications, power supply and distribution details, mechanical and environmental constraints, and testing and validation criteria.
-
What are some key considerations when selecting components for a PCB design?
-
When selecting components for a PCB design, it is essential to consider factors such as functionality and performance requirements, availability and lead times, cost and budget constraints, footprint and packaging compatibility, and reliability and quality ratings. It is crucial to work closely with component suppliers and distributors to ensure the selected components meet all the necessary specifications and are readily available.
-
What is the purpose of conducting a Design Rule Check (DRC) in the PCB design process?
-
Design Rule Check (DRC) is an automated process that verifies the PCB layout against a set of predefined design rules and constraints. These rules typically cover aspects such as minimum trace widths and spacings, clearance between components and traces, via and pad sizes and drilling requirements, and silk screen and solder mask guidelines. Running a comprehensive DRC helps identify any design rule violations or potential manufacturability issues, allowing designers to address them before proceeding to the manufacturing stage.
-
What are some common challenges in designing high-speed PCBs, and how can they be mitigated?
-
Designing PCBs for high-speed applications presents unique challenges, such as managing signal integrity, controlling impedance, and minimizing crosstalk. To mitigate these challenges, designers can implement best practices such as using controlled impedance traces and terminations, implementing proper grounding and shielding techniques, minimizing the use of vias and layer transitions, and conducting thorough signal integrity simulations and analysis.
-
How can designers ensure the manufacturability and reliability of their PCB designs?
- To ensure the manufacturability and reliability of PCB designs, it is essential to follow best practices such as adhering to the specified design rules and constraints, using standard component footprints and packaging, providing clear and comprehensive fabrication and assembly instructions, and conducting thorough testing and inspection at each stage of the process. By focusing on manufacturability and reliability throughout the design flow, designers can minimize the risk of production delays, quality issues, or field failures.
Conclusion
In conclusion, following an optimum PCB design flow is essential for creating high-quality, reliable, and manufacturable PCBs. By understanding and implementing the key steps in the design process, from concept and requirements gathering to manufacturing and assembly, designers can ensure their PCBs meet all the necessary functional and performance requirements while minimizing the risk of errors or issues.
Some key takeaways from this article include:
- The importance of creating a comprehensive design specification document to guide the entire design process
- The need for careful component selection and BOM management
- The critical role of signal integrity analysis and thermal management in PCB layout
- The significance of conducting thorough DRC and final design reviews before manufacturing
- The value of effective communication and collaboration with PCB manufacturers and assemblers
By following best practices and addressing common challenges throughout the PCB design flow, designers can streamline the development process, reduce costs and time-to-market, and ultimately deliver high-quality PCBs that meet the needs of their end customers.
Leave a Reply