Introduction to PCB Data Upload
Uploading PCB (printed circuit board) data is an essential step in the PCB design and manufacturing process. PCB data contains all the necessary information required to fabricate the physical circuit board, including the copper layers, drill holes, component footprints, and more.
Properly preparing and uploading your PCB data ensures that the manufacturer can accurately produce your board to your exact specifications. It helps avoid errors, delays, and additional costs.
In this comprehensive guide, we’ll walk through the process of uploading PCB data step-by-step. We’ll cover:
- Preparing your PCB design files
- Generating manufacturing output files
- Selecting a PCB manufacturer
- Uploading your data to the manufacturer
- Reviewing and approving your design for production
By following best practices for PCB data upload, you can streamline the handoff to manufacturing and get your boards fabricated correctly the first time. Let’s dive in!
Preparing Your PCB Design Files
Finalize Your PCB Layout
Before generating any manufacturing files, it’s crucial to finalize and thoroughly review your PCB layout. This includes:
- Running a design rule check (DRC) to verify your layout meets manufacturing constraints
- Reviewing copper pour, trace routing, via placement, etc.
- Updating your silkscreen, solder mask, and drill layers
- Confirming component footprints match your bill of materials (BOM)
- Getting signoff from all stakeholders on the final design
Taking the time upfront to perfect your PCB layout prevents late-stage design changes that can be costly and time-consuming to fix. Once you’re confident your design is ready for production, you can proceed to generating manufacturing files.
Generate Gerber Files
Gerber files are the industry standard format for conveying PCB design data to manufacturers. A complete Gerber package includes all the data required to image and produce the various layers of the physical PCB.
Most PCB design tools can export Gerber files. The exact steps vary by software, but generally involve:
- Open your PCB layout
- Select File > Fabrication Outputs (or similar)
- Choose Gerber RS-274X format
- Select all copper, solder mask, silkscreen, and drill layers
- Set the output directory
- Adjust any other export settings (e.g. apertures, line widths, etc.)
- Click OK to generate the Gerber files
This process will output a set of Gerber files, usually with file extensions like:
- .GTO – Top Overlay (silkscreen)
- .GTS – Top Solder Mask
- .GTL – Top Copper
- .GBL – Bottom Copper
- .GBS – Bottom Solder Mask
- .GBO – Bottom Overlay
- .GKO – Board Outline
- .DRL – Drill File
Carefully review the generated Gerber files in a Gerber viewer to ensure all layers look correct before sending them to your manufacturer. Most PCB design tools include a built-in Gerber viewer.
Export Drill Files
In addition to the Gerber files, you’ll need to provide your manufacturer with a drill file that specifies the location, size, and type of drill hits required for your PCB. This data is used to program the CNC drill machines.
Drill files are usually generated in Excellon format with file extensions like .DRL, .TXT or .XLN. They can be exported from your PCB design software similarly to Gerbers:
- Open the Fabrication Outputs menu
- Select Excellon format
- Choose which drill holes to include (plated, non-plated, slots, etc.)
- Set drill file options like units, precision, etc.
- Generate the output drill file(s)
Review the drill files to confirm hole sizes, locations, and quantities match your design intent. Your manufacturer may be able to catch major drill file errors, but it’s best to verify the data yourself before submitting it.
Provide Pick & Place Files
If your PCB design contains surface mount (SMT) components, you’ll likely need to supply a pick & place file to your manufacturer. Also known as a centroid file or XY file, this data tells the pick & place machine where to place each SMT part on the board during assembly.
Pick & place file formats vary, but the most common is a comma-separated value (CSV) file containing:
- Reference designator for each SMT component
- X-Y coordinates for component placement
- Component rotation
- Part number or comment
Here’s an example pick & place CSV file:
Designator | Footprint | Mid X | Mid Y | Rotation | Comment |
---|---|---|---|---|---|
C1 | 0805 | 135.890 | 80.264 | 90 | 10uF |
C2 | 0603 | 128.524 | 115.570 | 180 | 0.1uF |
U1 | TQFP-100 | 85.090 | 100.330 | 45 | MCU_chip |
Most PCB design tools can export a pick & place file:
- Open the Assembly Outputs menu
- Select the pick & place format (usually CSV or text)
- Map the columns to the required data
- Adjust units, origin, and other settings
- Preview and generate the pick & place file
Carefully review the generated pick & place data to ensure component locations and orientations are correct. Sending an inaccurate pick & place file can lead to costly and time-consuming assembly errors.
Include a Bill of Materials
Finally, compile a bill of materials (BOM) for your PCB. The BOM is a complete list of components required to assemble the board. It helps your manufacturer procure the correct parts in the right quantities.
A typical BOM is a spreadsheet or CSV file containing:
- Reference designators
- Manufacturer part numbers
- Quantities
- Descriptions
- Any additional component specs
For example:
Designator | Qty | Manufacturer | Mfr Part Number | Description |
---|---|---|---|---|
C1, C2 | 2 | Murata | GRM188R71A105KA61D | CAP CER 1UF 10V X7R 0603 |
R1, R5 | 2 | Yageo | RC0603FR-071KL | RES SMD 1K OHM 1% 1/10W 0603 |
U1 | 1 | Texas Instruments | TMS320F28069PZT | IC MCU 32BIT 90MHZ 100TQFP |
Your PCB design software can usually generate a BOM template that you can populate with part data. Verify that reference designators match between your schematic, PCB layout, and BOM before submitting for manufacturing.
Selecting a PCB Manufacturer
Understand Manufacturing Capabilities
Not all PCB manufacturers have the same capabilities. When selecting a vendor to fabricate your design, it’s important to understand their manufacturing strengths and limitations. Key factors to consider include:
- Board complexity (layer count, HDI, microvias, etc.)
- Minimum trace/space widths
- Smallest drill hole sizes
- Material availability (FR-4, high-Tg, flex, rigid-flex, etc.)
- Surface finishes offered (HASL, ENIG, OSP, etc.)
- Electrical testing (flying probe, boundary scan, etc.)
Look for a manufacturer whose capabilities align well with your PCB’s technical requirements. If your design pushes the boundaries of typical specs (e.g. 8 mil traces, laser microvias, 20+ layers), be sure to discuss it with potential vendors upfront to verify they can fabricate it reliably.
Get Quotations
Once you’ve narrowed down your list of potential PCB manufacturers, reach out to each one for a quotation. Most vendors provide online quote request forms where you can upload your design files and specify things like:
- Number of boards
- Board size
- Layer count
- Surface finish
- Copper weights
- Silkscreen color
- Lead time
The manufacturer will review your design data and respond with a quotation outlining the price, lead time, and any technical questions or concerns they have about your design. Carefully compare quotes to select the vendor that offers the best combination of price, lead time, and technical capabilities for your needs.
Review Manufacturing Guidelines
Each PCB manufacturer publishes a set of design guidelines outlining their capabilities and recommended best practices. These documents contain valuable information to help optimize your design for their manufacturing process, such as:
- Recommended drill hole sizes
- Minimum annular rings
- Copper pour spacing
- Solder mask clearances
- Testpoint requirements
Review your chosen manufacturer’s guidelines and make any necessary adjustments to your design before submitting it for production. This can help avoid manufacturability issues and ensure a smoother overall fabrication process.
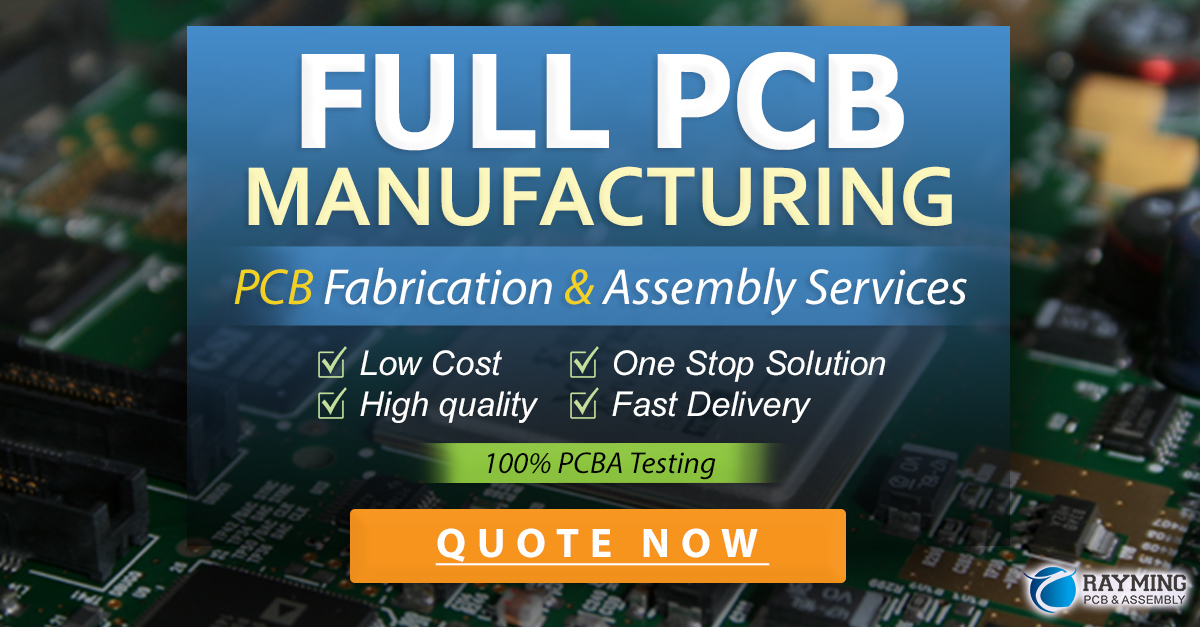
Uploading Your Data
Compress Files for Upload
With your Gerber, drill, pick & place, and BOM files prepared, the next step is to package them for upload to your manufacturer. The best practice is to compress all the files into a single ZIP archive.
Most operating systems have built-in tools for creating ZIP files:
- On Windows, select the files, right-click, and choose “Send to > Compressed (zipped) folder”
- On Mac, select the files, right-click, and choose “Compress items”
- On Linux, use the zip command in the terminal
Be sure to give your ZIP file a descriptive name that includes the board name, revision, and date. For example: WidgetPro_v1.2_2023-04-15.zip
Upload to Manufacturer’s Website
Most PCB manufacturers provide a web portal for uploading design files. Once you’ve created an account and logged in, look for an “Upload Files” or “Submit Design” button.
Click the button and select your ZIP file to upload. The manufacturer’s website will typically display a progress bar as the file uploads. Once the upload is complete, you should see a confirmation message.
Provide Additional Instructions
After uploading your design files, most manufacturers provide a form or text field where you can enter additional instructions or comments. Use this space to communicate any special requirements, clarifications, or questions you have about the fabrication process.
For example, you might specify:
- “Use lead-free HASL finish on all boards”
- “Please X-out pin 1 on all ICs”
- “Boards will require electrical testing using flying probe”
Be as clear and concise as possible in your instructions to avoid confusion. If you have a lot of detailed requirements, consider attaching a separate document outlining your specifications.
Review and Approve Design
After submitting your design files and instructions, the manufacturer will typically review your data and provide feedback within 1-2 business days. This may come in the form of an email, online chat, or phone call.
The manufacturer’s engineers will analyze your Gerber, drill, and pick & place files to check for any technical issues or violations of their design guidelines. They may request clarification or changes to your design if they spot any red flags.
Carefully review the manufacturer’s feedback and address any concerns promptly. If needed, make changes to your design files and resubmit them for another review.
Once the manufacturer has confirmed that your design is acceptable for production, they will usually provide a final price and lead time quotation. If you approve, reply with your authorization to proceed with fabrication.
The manufacturer will then begin producing your PCBs according to your specifications. Depending on the complexity of your design and the manufacturer’s workload, lead times can range from a few days to several weeks.
Conclusion
Uploading PCB data for manufacturing may seem daunting at first, but by following the steps outlined in this guide, you can ensure a smooth and successful handoff to your chosen vendor.
Remember to:
- Finalize and double-check your PCB design before generating manufacturing files
- Export complete and accurate Gerber, drill, pick & place, and BOM data
- Select a PCB manufacturer whose capabilities match your technical requirements
- Package your design files into a single ZIP archive for upload
- Provide clear instructions and promptly address any feedback from the manufacturer
By taking the time to properly prepare and communicate your design data, you can avoid costly mistakes and delays in the PCB fabrication process. With practice, uploading PCB data will become a natural part of your design workflow.
Frequently Asked Questions
What are the most common issues with PCB data upload?
Some of the most frequent problems with PCB data upload include:
- Incomplete or missing Gerber files
- Incorrect drill file format or units
- Inaccurate pick & place data
- Mismatch between BOM and design files
- Violating the manufacturer’s design guidelines
Double-checking your data before submitting it can help catch and correct these issues early.
How do I know if my design is manufacturable?
The best way to verify your design’s manufacturability is to review your PCB manufacturer’s design guidelines and capabilities. Make sure your trace/space widths, drill holes, layer stack-up, and other specifications fall within their recommended ranges.
Running a design for manufacturing (DFM) check in your PCB design software can also help identify potential manufacturability issues before you generate your output files.
What if I need to make changes to my design after submitting it?
If you discover an error or need to make a change to your design after submitting it for manufacturing, contact your PCB manufacturer as soon as possible. Depending on how far along they are in the fabrication process, they may be able to accommodate your changes without incurring significant delays or additional costs.
However, if fabrication has already begun, changes may be difficult or impossible to implement without scrapping the existing boards and starting over. That’s why it’s crucial to thoroughly review your design before releasing it for production.
How long does PCB fabrication usually take?
PCB fabrication lead times can vary widely depending on the complexity of your design, the manufacturer’s workload, and your specific requirements. Simple 2-layer boards may be turned around in as little as 1-2 days, while complex HDI designs with 10+ layers may take 2-3 weeks or more.
When requesting a quotation from your manufacturer, be sure to specify your desired lead time. Most vendors offer expedited options for an additional fee if you need your boards faster than their standard lead time.
What should I do if I have questions or concerns during the PCB fabrication process?
If you have any questions, concerns, or special requests during the PCB fabrication process, don’t hesitate to reach out to your manufacturer. Most vendors have a dedicated support team available by email, phone, or online chat to assist with customer inquiries.
Be as specific and detailed as possible when describing your issue or request. Provide your order number, design files, and any other relevant information to help the manufacturer understand and address your concerns quickly.
By maintaining open and proactive communication with your PCB manufacturer, you can help ensure a smooth and successful fabrication process from start to finish.
Leave a Reply