What is FR4?
FR4 is a composite material made from woven fiberglass cloth impregnated with an epoxy resin binder. The “FR” stands for “Flame Retardant,” indicating that the material has been treated to resist catching fire and spreading flames. The “4” in FR4 refers to the specific grade of the material, which is the most common type used in PCB manufacturing.
Composition of FR4
FR4 is composed of two main components:
-
Fiberglass cloth: The fiberglass cloth provides the structural strength and dimensional stability to the material. It is typically woven in a plain or twill pattern, depending on the desired properties.
-
Epoxy resin: The epoxy resin is a thermoset polymer that binds the fiberglass cloth together and provides the insulating properties. It also contributes to the material’s resistance to moisture, chemicals, and heat.
The combination of these two components results in a material with excellent properties for PCB manufacturing.
Factors Affecting FR4 Quality
Several factors can impact the quality of FR4 material, which in turn affects the performance and reliability of the PCBs made from it. These factors include:
1. Material Composition
The quality of the raw materials used in the production of FR4 plays a crucial role in determining the final quality of the material. The fiberglass cloth should be of high quality, with consistent weave patterns and minimal defects. The epoxy resin should also be of a high grade, with the appropriate chemical composition and curing properties.
2. Manufacturing Process
The manufacturing process of FR4 involves several steps, including impregnation, curing, and lamination. Each step must be carefully controlled to ensure consistent quality. For example, the impregnation process should ensure that the epoxy resin is evenly distributed throughout the fiberglass cloth, without any voids or air pockets. The curing process should be carried out at the appropriate temperature and duration to ensure that the epoxy resin is fully cross-linked and achieves its desired properties.
3. Thickness Tolerance
The thickness of the FR4 material is a critical parameter in PCB manufacturing. It affects the electrical properties, such as impedance and signal integrity, as well as the mechanical properties, such as stiffness and strength. The thickness tolerance of FR4 should be tightly controlled to ensure consistency across the entire panel and from batch to batch.
Standard Thickness (mm) | Tolerance (mm) |
---|---|
0.2 | ± 0.02 |
0.4 | ± 0.03 |
0.8 | ± 0.05 |
1.6 | ± 0.10 |
3.2 | ± 0.20 |
4. Copper Foil Quality
The copper foil used in PCB manufacturing is laminated onto the FR4 substrate. The quality of the copper foil, including its thickness, surface roughness, and adhesion to the substrate, can affect the quality of the final PCB. Poor copper foil quality can lead to issues such as delamination, poor signal integrity, and reduced reliability.
5. Environmental Factors
FR4 material is sensitive to environmental factors such as temperature, humidity, and chemical exposure. Exposure to extreme temperatures or high humidity can cause the material to degrade, leading to reduced mechanical and electrical properties. Chemical exposure, such as to strong acids or bases, can also cause damage to the material.
Testing and Certification of FR4 Quality
To ensure that FR4 material meets the required quality standards, various testing and certification procedures are carried out. These include:
1. Material Testing
FR4 material undergoes several tests to evaluate its mechanical, electrical, and thermal properties. These tests include:
- Tensile strength and elongation
- Flexural strength and modulus
- Dielectric constant and loss tangent
- Glass transition temperature (Tg)
- Thermal expansion coefficient (CTE)
- Moisture absorption
The results of these tests are compared against industry standards, such as IPC-4101, to ensure that the material meets the required specifications.
2. Certification
FR4 material can be certified to various industry standards, depending on the intended application. Some common certifications include:
- UL 94 V-0: This certification ensures that the material meets the flammability requirements for vertical burning tests.
- IPC-4101: This standard specifies the requirements for base materials used in rigid and multilayer printed boards.
- MIL-I-24768: This military specification covers the requirements for rigid, flexible, and rigid-flex printed wiring boards.
Certification ensures that the FR4 material has been independently tested and verified to meet the required quality standards.
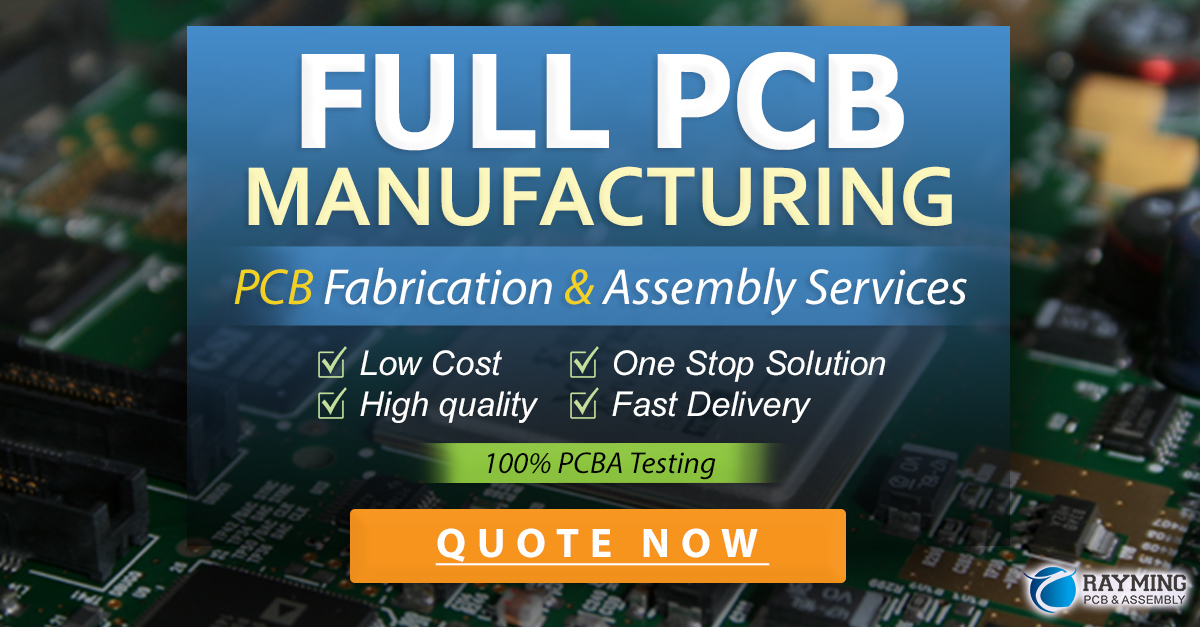
Choosing the Right FR4 Material
When selecting FR4 material for your PCB manufacturing needs, it is essential to consider the specific requirements of your application. Some factors to consider include:
1. Electrical Requirements
Different applications have different electrical requirements, such as signal speed, impedance, and dielectric constant. Choose an FR4 material that meets your specific electrical needs to ensure optimal performance.
2. Mechanical Requirements
Consider the mechanical requirements of your application, such as strength, stiffness, and dimensional stability. Select an FR4 material with the appropriate thickness and glass transition temperature (Tg) to meet these requirements.
3. Environmental Requirements
If your application will be exposed to harsh environmental conditions, such as high temperatures, humidity, or chemical exposure, choose an FR4 material that is designed to withstand these conditions. Look for materials with higher Tg values, lower moisture absorption, and better chemical resistance.
4. Cost Considerations
FR4 materials come in a range of grades and prices. While it may be tempting to choose the lowest-cost option, it is important to balance cost with performance and reliability. Investing in a higher-quality FR4 material can lead to better yields, fewer failures, and lower overall costs in the long run.
FAQ
- What is the difference between standard FR4 and high-Tg FR4?
-
Standard FR4 has a glass transition temperature (Tg) of around 130°C, while high-Tg FR4 has a Tg of 170°C or higher. High-Tg FR4 is more resistant to thermal stress and is suitable for applications that require higher operating temperatures.
-
Can FR4 be used for high-frequency applications?
-
While FR4 is suitable for many general-purpose applications, it may not be the best choice for high-frequency applications due to its relatively high dielectric loss. For high-frequency applications, materials with lower dielectric loss, such as Rogers or PTFE-based laminates, are often used.
-
How does the thickness of FR4 affect its performance?
-
The thickness of FR4 affects its electrical and mechanical properties. Thinner FR4 will have lower dielectric constant and lower stiffness, while thicker FR4 will have higher dielectric constant and higher stiffness. The choice of thickness depends on the specific requirements of the application.
-
What is the shelf life of FR4 material?
-
The shelf life of FR4 material depends on the storage conditions. When stored in a cool, dry place, away from direct sunlight and sources of heat, FR4 can typically last for several years. However, it is always best to consult the manufacturer’s recommendations for specific storage and shelf life guidelines.
-
How can I ensure that I am getting high-quality FR4 material?
- To ensure that you are getting high-quality FR4 material, purchase from a reputable supplier who can provide material certifications and test reports. Look for materials that are certified to industry standards, such as IPC-4101, and that have been independently tested for mechanical, electrical, and thermal properties. Additionally, consider working with a supplier who has a proven track record of providing consistent, reliable materials.
Conclusion
FR4 is a critical material in the manufacturing of printed circuit boards, and its quality can have a significant impact on the performance and reliability of the final product. When selecting FR4 material, it is essential to consider factors such as material composition, manufacturing process, thickness tolerance, copper foil quality, and environmental requirements.
To ensure that you are getting high-quality FR4 material, look for materials that have been tested and certified to industry standards, and purchase from reputable suppliers who can provide consistent, reliable materials. By understanding the factors that affect FR4 quality and making informed choices, you can ensure that your PCBs meet the required standards and perform optimally in their intended applications.
Leave a Reply