Table of Contents
- Introduction to SMT Tombstoning
- Causes of SMT Tombstoning
- Preventing SMT Tombstoning
- Troubleshooting and Solving SMT Tombstoning
- Frequently Asked Questions (FAQ)
- Conclusion
Introduction to SMT Tombstoning
What is Surface Mount Technology (SMT)?
Surface Mount Technology (SMT) is a method of assembling electronic components directly onto the surface of a printed circuit board (PCB). Unlike through-hole technology, where component leads are inserted into holes drilled in the PCB, SMT components are placed on top of the PCB and soldered to pads on the board’s surface. This technology allows for smaller component sizes, higher component density, and automated assembly processes.
Understanding SMT Tombstoning
SMT tombstoning, also known as “Manhattan effect,” “Tombstone effect,” “Drawbridging,” or “Chickenheading,” is a defect that occurs when one end of a surface-mounted component lifts off the PCB pad during the reflow soldering process. The lifted end of the component stands upright, resembling a tombstone, while the other end remains attached to the PCB. This defect can cause open circuits, intermittent connections, and reduced reliability of the assembled PCB.
Tombstoning primarily affects small, lightweight, two-terminal components such as chip resistors and capacitors. These components are more susceptible to the forces that cause tombstoning due to their size and mass.
Causes of SMT Tombstoning
Several factors can contribute to the occurrence of SMT tombstoning. Understanding these causes is essential for preventing and minimizing this defect in the SMT assembly process.
Uneven Heating During Reflow Soldering
One of the primary causes of tombstoning is uneven heating during the reflow soldering process. When one end of a component heats up and melts the solder faster than the other end, the surface tension of the molten solder can pull the component upright. This imbalance in heating can be caused by:
- Uneven thermal mass distribution on the PCB
- Inadequate or excessive solder paste
- Incorrect reflow oven temperature profile
- Improper placement of components near larger, heat-absorbing components
Component and PCB Pad Design
The design of both the component and the PCB pads can influence the likelihood of tombstoning. Some design-related factors include:
- Unequal pad sizes or shapes
- Incorrect pad spacing
- Inadequate or excessive solder mask clearance
- Inconsistent component placement or orientation
Solder Paste and Stencil Design
The solder paste and stencil design can also contribute to tombstoning:
- Insufficient or excessive solder paste volume
- Uneven solder paste deposition
- Incorrect stencil aperture size or shape
- Poor solder paste quality or incorrect composition
Manufacturing Variables
In addition to the aforementioned causes, various manufacturing variables can influence tombstoning:
- PCB Warpage or uneven placement in the reflow oven
- Vibrations or disturbances during the reflow process
- Incorrect component storage or handling
- Humidity and environmental factors
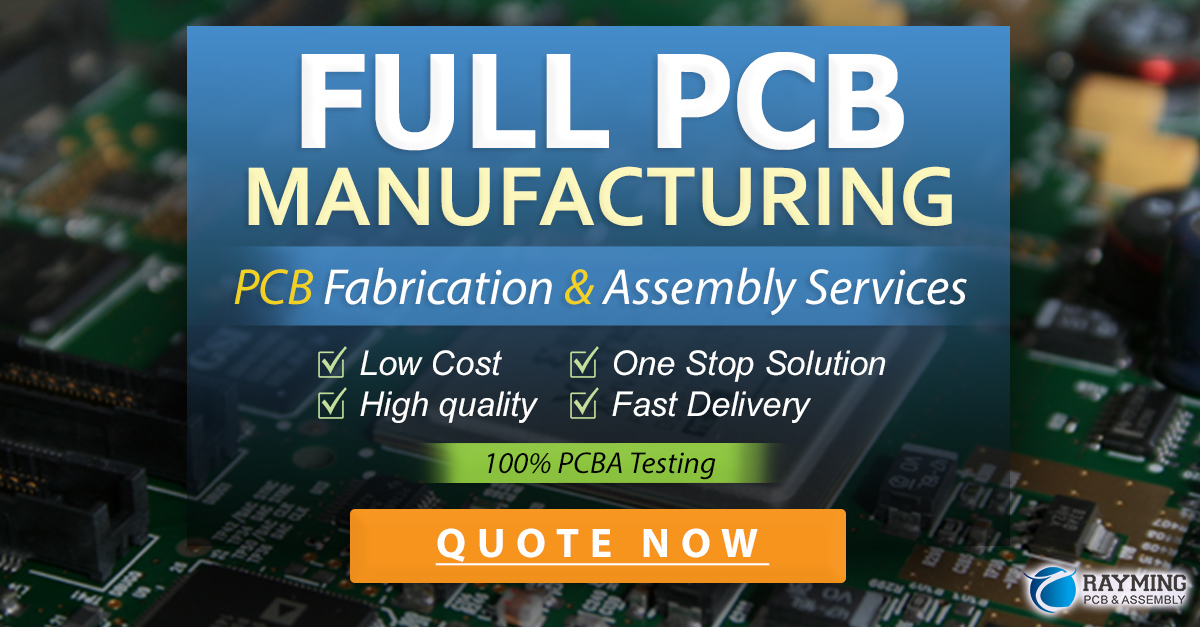
Preventing SMT Tombstoning
Preventing SMT tombstoning requires a multi-faceted approach that addresses the various causes of this defect. By implementing the following best practices, manufacturers can significantly reduce the occurrence of tombstoning in their SMT assembly process.
PCB and Component Design Considerations
Proper PCB and component design is crucial for minimizing tombstoning. Consider the following guidelines:
- Ensure equal pad sizes and shapes for two-terminal components
- Maintain consistent pad spacing and solder mask clearance
- Optimize component placement and orientation
- Use appropriate land patterns for specific component sizes and types
Component Size | Pad Width | Pad Length | Pad Spacing |
---|---|---|---|
0201 | 0.25 mm | 0.35 mm | 0.35 mm |
0402 | 0.50 mm | 0.70 mm | 0.50 mm |
0603 | 0.80 mm | 1.00 mm | 0.80 mm |
0805 | 1.00 mm | 1.25 mm | 1.00 mm |
Table 1: Recommended pad dimensions for common chip component sizes
Solder Paste and Stencil Optimization
Optimizing the solder paste and stencil design can help prevent tombstoning:
- Use solder paste with the appropriate particle size and composition
- Ensure even solder paste deposition through proper stencil design
- Adjust stencil aperture size and shape to control solder paste volume
- Maintain solder paste quality through proper storage and handling
Stencil Thickness | Aperture Size (0402) | Aperture Size (0603) |
---|---|---|
0.100 mm | 0.40 mm x 0.55 mm | 0.70 mm x 0.85 mm |
0.125 mm | 0.45 mm x 0.60 mm | 0.75 mm x 0.90 mm |
0.150 mm | 0.50 mm x 0.65 mm | 0.80 mm x 0.95 mm |
Table 2: Recommended stencil aperture sizes for 0402 and 0603 chip components
Reflow Profile Optimization
Optimizing the reflow profile is essential for achieving even heating and minimizing tombstoning:
- Conduct reflow profile analysis to ensure proper temperature distribution
- Adjust peak temperature, ramp rates, and dwell times to minimize thermal gradients
- Use convection reflow ovens with multi-zone temperature control
- Monitor and maintain consistent oven temperature and conveyor speed
Reflow Stage | Temperature Range | Duration |
---|---|---|
Preheat | 150°C – 180°C | 60-90 s |
Soak | 180°C – 200°C | 60-120 s |
Reflow | 235°C – 250°C | 30-60 s |
Cooling | < 100°C | 30-60 s |
Table 3: Typical reflow profile parameters for lead-free solder
Manufacturing Process Control
Maintaining strict control over the manufacturing process can help prevent tombstoning:
- Ensure proper PCB support and flatness during reflow
- Minimize vibrations and disturbances in the reflow oven
- Implement humidity control and ESD protection measures
- Regularly maintain and calibrate SMT assembly equipment
Troubleshooting and Solving SMT Tombstoning
Despite implementing best practices, tombstoning may still occur occasionally. When encountering tombstoning defects, follow these troubleshooting steps to identify the root cause and implement appropriate solutions:
- Analyze the tombstoned components and identify any patterns or commonalities
- Review the PCB and component design for potential issues (e.g., pad size, spacing, orientation)
- Evaluate the solder paste and stencil design (e.g., aperture size, shape, solder paste volume)
- Examine the reflow profile and temperature distribution across the PCB
- Assess the manufacturing process for potential contributing factors (e.g., PCB support, vibrations, humidity)
Based on the identified root cause, implement targeted solutions:
- Modify PCB or component design
- Adjust solder paste and stencil parameters
- Optimize the reflow profile
- Improve manufacturing process control measures
Continuously monitor and document the results of these changes to ensure the effectiveness of the implemented solutions.
Frequently Asked Questions (FAQ)
-
Q: Can tombstoning be repaired after the reflow process?
A: In most cases, tombstoned components can be manually repaired by reflowing the affected component using a soldering iron or hot air rework station. However, this manual repair process is time-consuming and may not be feasible for high-volume production. -
Q: Are certain types of components more prone to tombstoning?
A: Yes, small, lightweight, two-terminal components such as chip resistors and capacitors are more susceptible to tombstoning due to their size and mass. Larger, heavier components are less likely to be affected by the forces that cause tombstoning. -
Q: How does the solder paste composition affect tombstoning?
A: The solder paste composition, particularly the flux and alloy content, can influence the likelihood of tombstoning. Using a solder paste with a higher tackiness and a more active flux can help hold components in place during reflow, reducing the risk of tombstoning. -
Q: Can tombstoning be detected by automated optical inspection (AOI) systems?
A: Yes, modern AOI systems are capable of detecting tombstoned components by comparing the height and angle of the component to predefined thresholds. However, the effectiveness of AOI detection may depend on the specific component size, type, and the severity of the tombstoning defect. -
Q: How does PCB warpage contribute to tombstoning?
A: PCB warpage can cause uneven heating during the reflow process, leading to tombstoning. When a PCB is warped, certain areas of the board may be closer to or farther from the heat source, resulting in temperature gradients that can cause uneven solder melting and component lifting.
Conclusion
SMT tombstoning is a common defect that can significantly impact the quality and reliability of assembled PCBs. By understanding the causes of tombstoning, implementing best practices in design and manufacturing, and effectively troubleshooting and solving tombstoning issues, electronics manufacturers can minimize the occurrence of this defect and improve their overall production yield.
Preventing tombstoning requires a comprehensive approach that addresses PCB and component design, solder paste and stencil optimization, reflow profile control, and manufacturing process management. By continuously monitoring, documenting, and refining these processes, manufacturers can achieve consistent, high-quality SMT assembly results.
As the electronics industry continues to evolve, with ever-increasing demands for miniaturization and higher component densities, addressing SMT tombstoning will remain a critical challenge. However, by staying informed about the latest best practices and technologies, manufacturers can effectively combat this defect and deliver reliable, high-performance electronic products to their customers.
Leave a Reply