Understanding the Basics of PCB Design
Before we delve into the specific guidelines, let’s review some fundamental concepts of PCB design.
What is a PCB?
A PCB is a laminated board that mechanically supports and electrically connects electronic components using conductive tracks, pads, and other features etched from copper sheets laminated onto a non-conductive substrate.
Layers of a PCB
PCBs can have various numbers of layers, depending on the complexity of the design:
Layers | Description |
---|---|
Single Layer | One conductive layer, usually used for simple designs |
Double Layer | Two conductive layers, one on each side of the substrate |
Multi-Layer | Three or more conductive layers, alternating with insulating layers |
PCB Material Selection
Choosing the right PCB material is essential for ensuring the board’s performance and reliability. Common PCB materials include:
- FR-4: A glass-reinforced epoxy laminate, widely used for its good mechanical and electrical properties
- Rogers: High-frequency laminates with low dielectric loss, used for RF and microwave applications
- Polyimide: Flexible and heat-resistant material, used for flex and Rigid-Flex PCBs
PCB Design Guidelines
Now that we’ve covered the basics, let’s explore the key guidelines for designing PCBs.
Schematic Design
Use a hierarchical design approach
Break down your schematic into functional blocks, making it easier to understand and maintain. Use hierarchical sheets to organize complex designs.
Follow consistent naming conventions
Establish and follow a consistent naming convention for components, nets, and labels. This improves readability and helps with troubleshooting.
Use appropriate component packages
Select component packages that are suitable for your manufacturing process and assembly requirements. Consider factors such as size, pitch, and thermal characteristics.
Component Placement
Group related components together
Place components that belong to the same functional block close to each other. This minimizes the length of traces and improves signal integrity.
Consider component orientation
Orient components in a way that facilitates easy routing and minimizes the number of vias required. Align components to the PCB grid for better manufacturability.
Provide adequate clearance
Ensure sufficient clearance between components to allow for proper soldering and inspection. Follow the manufacturer’s recommendations for component spacing.
Routing and Trace Design
Use appropriate trace widths
Select trace widths based on the current carrying requirements and the desired impedance. Wider traces have lower resistance and can carry more current.
Minimize trace lengths
Keep traces as short as possible to reduce signal delays and minimize electromagnetic interference (EMI). Avoid unnecessary meandering of traces.
Route sensitive signals first
Prioritize the routing of critical signals, such as high-speed lines, clock signals, and power traces. This helps minimize crosstalk and signal integrity issues.
Use ground planes
Incorporate ground planes in your PCB design to provide a low-impedance return path for signals and reduce EMI. Solid ground planes are preferred over gridded planes.
Power Distribution
Use appropriate power planes
Dedicate separate layers for power distribution, especially for multi-layer PCBs. This helps minimize voltage drops and provides a stable reference for signals.
Decouple power supplies
Place decoupling capacitors close to the power pins of ICs to suppress high-frequency noise and provide a stable power supply. Use the appropriate capacitor values and types based on the frequency range and current requirements.
Use proper grounding techniques
Implement a solid grounding strategy to minimize ground loops and reduce noise. Use star grounding or a ground plane, depending on the design requirements.
Signal Integrity
Match trace impedances
Ensure that the impedance of traces matches the characteristic impedance of the connected components and transmission lines. This minimizes reflections and signal distortion.
Terminate transmission lines
Use proper termination techniques, such as series termination or parallel termination, to minimize reflections and maintain signal integrity.
Minimize crosstalk
Reduce crosstalk by increasing the spacing between adjacent traces, using guard traces, or routing sensitive signals on different layers.
Electromagnetic Compatibility (EMC)
Follow EMC design guidelines
Adhere to EMC design guidelines to minimize electromagnetic interference (EMI) and ensure compliance with regulatory standards. Use shielding, filtering, and proper grounding techniques.
Minimize loop areas
Reduce the loop area of current paths to minimize radiated EMI. Keep high-frequency signals and their return paths close together.
Use EMI filters
Implement EMI filters, such as ferrite beads or capacitors, to suppress high-frequency noise and prevent interference.
Manufacturing Considerations
Adhere to design for manufacturability (DFM) rules
Follow the DFM guidelines provided by your PCB manufacturer to ensure that your design can be reliably manufactured. Consider factors such as minimum trace widths, spacing, and hole sizes.
Use standard sizes and shapes
Stick to standard PCB sizes and shapes whenever possible to reduce manufacturing costs and lead times. Avoid irregular shapes or cutouts unless necessary.
Provide clear markings and labels
Include clear markings and labels on your PCB to aid in assembly and troubleshooting. Use silkscreen layers to indicate component designators, test points, and other relevant information.
Frequently Asked Questions (FAQ)
1. What is the difference between a schematic and a PCB layout?
A schematic is a graphical representation of the electrical connections and components in a circuit, while a PCB layout is the physical arrangement of those components and connections on a printed circuit board.
2. How do I choose the right PCB material for my design?
The choice of PCB material depends on factors such as the operating frequency, environmental conditions, and cost. FR-4 is a common choice for general-purpose applications, while high-frequency laminates like Rogers are used for RF and microwave designs. Consult with your PCB manufacturer for specific recommendations based on your requirements.
3. What is the purpose of a ground plane in a PCB?
A ground plane serves as a low-impedance return path for signals and helps reduce electromagnetic interference (EMI). It provides a stable reference for signals and minimizes voltage drops across the board.
4. How can I minimize crosstalk between traces on a PCB?
To minimize crosstalk, you can increase the spacing between adjacent traces, use guard traces, or route sensitive signals on different layers. Additionally, ensure proper trace impedance matching and use appropriate termination techniques.
5. What are some common PCB manufacturing considerations?
Common PCB manufacturing considerations include adhering to design for manufacturability (DFM) rules, using standard sizes and shapes, providing clear markings and labels, and selecting appropriate component packages. Consult with your PCB manufacturer for specific guidelines and requirements.
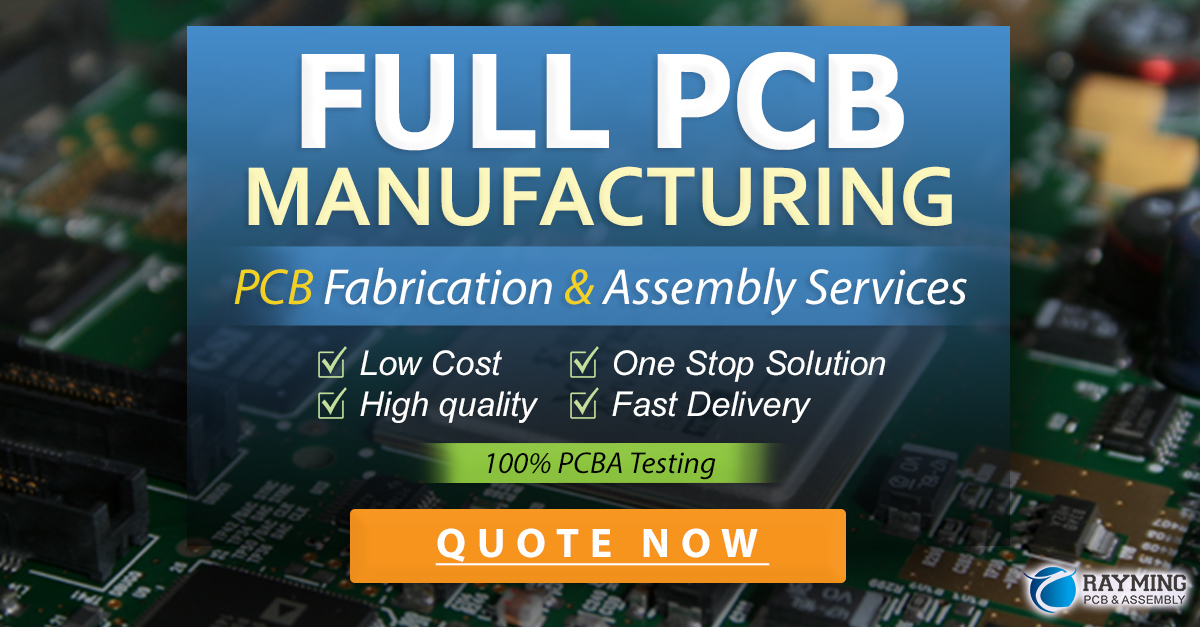
Conclusion
Designing a PCB requires careful consideration of various factors, from schematic design and component placement to routing and signal integrity. By following the guidelines outlined in this article, you can create PCBs that are reliable, perform well, and are cost-effective to manufacture.
Remember to collaborate closely with your PCB manufacturer and assembly partners to ensure that your design meets their requirements and can be efficiently produced. Continuously review and refine your design throughout the development process to catch any issues early and optimize the overall performance of your PCB.
By adhering to these PCB design guidelines and best practices, you’ll be well on your way to creating successful electronic products that meet your customers’ needs and exceed their expectations.
Leave a Reply