History of Assembly Manufacturing
The concept of assembly manufacturing dates back to the Industrial Revolution in the late 18th century. The introduction of interchangeable parts and the division of labor allowed for the mass production of goods, which revolutionized the manufacturing industry. In the early 20th century, the automotive industry pioneered the use of assembly lines, which further streamlined the production process and increased efficiency.
Key Milestones in Assembly Manufacturing
Year | Milestone |
---|---|
1913 | Henry Ford introduces the moving assembly line for automobile production |
1947 | The first fully automated assembly line is developed by General Motors |
1960s | The rise of robotics in assembly manufacturing |
1980s | The introduction of flexible manufacturing systems (FMS) |
1990s | The adoption of lean manufacturing principles |
2000s | The integration of digital technologies, such as IoT and AI, in assembly manufacturing |
Types of Assembly Manufacturing
There are several types of assembly manufacturing, each with its own characteristics and applications.
Manual Assembly
Manual assembly involves human workers performing the assembly tasks using hand tools or simple machinery. This method is suitable for low-volume production or products that require intricate handling and manipulation.
Automated Assembly
Automated assembly utilizes machines, such as robots or dedicated assembly equipment, to perform the assembly tasks. This method is ideal for high-volume production and can achieve higher levels of precision and consistency compared to manual assembly.
Hybrid Assembly
Hybrid assembly combines manual and automated assembly methods, leveraging the strengths of both approaches. This method is suitable for products that require a mix of human dexterity and machine precision.
Advantages of Assembly Manufacturing
Assembly manufacturing offers several advantages over other manufacturing methods:
- Increased efficiency: Assembly lines allow for the streamlining of production processes, reducing lead times and increasing output.
- Improved quality: Automated assembly systems can achieve higher levels of precision and consistency, resulting in fewer defects and improved product quality.
- Cost reduction: The use of assembly lines and automation can reduce labor costs and minimize waste, leading to overall cost savings.
- Scalability: Assembly manufacturing can be easily scaled up or down to meet changing demand, making it suitable for both low-volume and high-volume production.
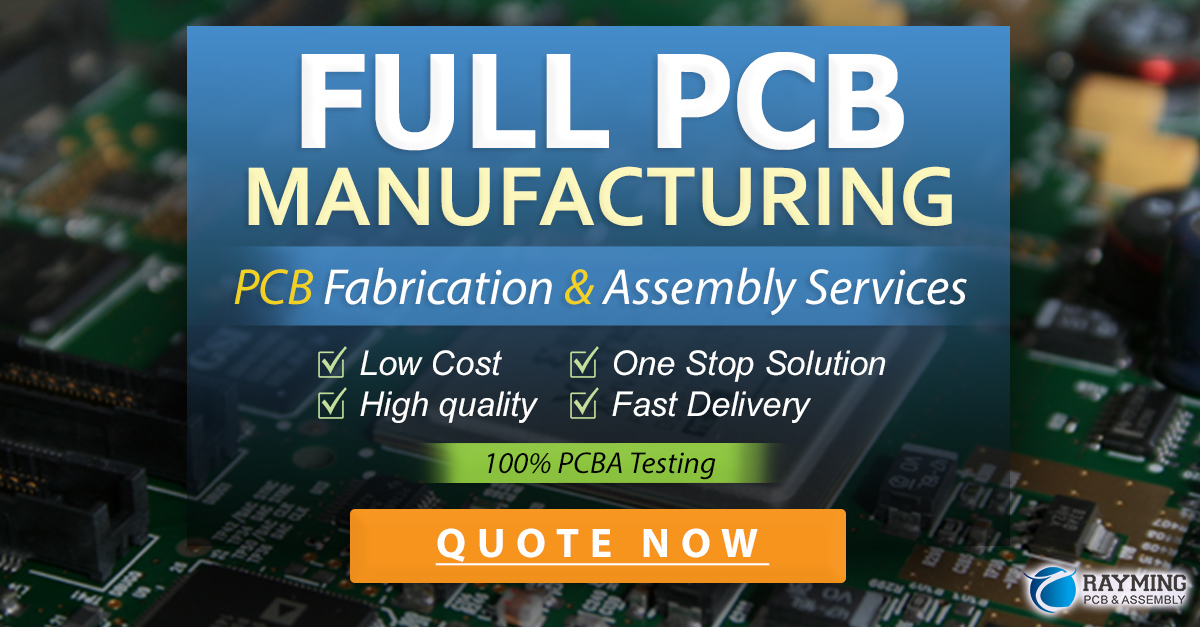
Challenges in Assembly Manufacturing
Despite its advantages, assembly manufacturing also faces several challenges:
- Initial investment: Setting up an assembly line or implementing automation can require significant upfront costs for equipment, training, and infrastructure.
- Complexity: As products become more complex, the assembly process also becomes more intricate, requiring advanced planning and coordination.
- Skilled labor: While automation can reduce the need for manual labor, it also requires skilled technicians and engineers to design, implement, and maintain the systems.
- Supply chain management: Assembly manufacturing relies on a stable and efficient supply chain to ensure the timely delivery of components and materials.
Future Trends in Assembly Manufacturing
As technology continues to advance, assembly manufacturing is poised to undergo significant changes in the coming years. Some of the key trends include:
- Industry 4.0: The integration of digital technologies, such as the Internet of Things (IoT), artificial intelligence (AI), and big data analytics, will enable smarter, more connected, and more efficient assembly processes.
- Collaborative robots: The use of collaborative robots, or cobots, will allow for safer and more flexible human-machine interaction in assembly tasks.
- Additive manufacturing: The incorporation of 3D printing technology in assembly manufacturing will enable the production of complex, customized parts and reduce lead times.
- Sustainable manufacturing: There will be an increased focus on sustainable practices in assembly manufacturing, such as the use of eco-friendly materials, energy-efficient equipment, and closed-loop production systems.
Frequently Asked Questions (FAQ)
-
Q: What is the difference between assembly manufacturing and other manufacturing methods?
A: Assembly manufacturing focuses on the joining of individual components or subassemblies to create a complete product, while other manufacturing methods, such as machining or casting, involve the creation of individual parts from raw materials. -
Q: Is assembly manufacturing suitable for all types of products?
A: Assembly manufacturing is suitable for a wide range of products, from simple consumer goods to complex machinery. However, the specific assembly method (manual, automated, or hybrid) will depend on factors such as production volume, product complexity, and available resources. -
Q: How can companies overcome the challenges associated with assembly manufacturing?
A: Companies can overcome the challenges in assembly manufacturing by carefully planning their investments, partnering with reliable suppliers, investing in employee training and development, and continuously monitoring and optimizing their processes. -
Q: What role does technology play in the future of assembly manufacturing?
A: Technology will play a crucial role in the future of assembly manufacturing, enabling smarter, more connected, and more efficient processes. The integration of digital technologies, collaborative robots, additive manufacturing, and sustainable practices will shape the industry in the coming years. -
Q: How can companies ensure the quality of their products in assembly manufacturing?
A: Companies can ensure product quality in assembly manufacturing by implementing robust quality control measures, such as in-process inspections, statistical process control, and final product testing. The use of automation and digital technologies can also help minimize human error and improve consistency.
Conclusion
Assembly manufacturing technology has come a long way since the Industrial Revolution, and it continues to evolve with the advancement of digital technologies and innovative approaches. By understanding the different types of assembly manufacturing, its advantages, and challenges, companies can make informed decisions and adapt to the changing landscape of the industry. As we move towards a more connected, sustainable, and efficient future, assembly manufacturing will remain a critical component of the global manufacturing ecosystem.
Leave a Reply