The Importance of Round-Edge Plating
Round-edge plating plays a crucial role in improving the overall quality and performance of metal parts. Some of the key benefits of this process include:
-
Enhanced durability: Round-edge plating helps to protect metal parts from wear and tear, extending their lifespan and reducing the need for frequent replacements.
-
Improved corrosion resistance: By applying a protective coating to the edges of metal parts, round-edge plating helps to prevent corrosion and oxidation, even in harsh environmental conditions.
-
Increased safety: Sharp edges on metal parts can pose a safety hazard, especially in applications where human contact is involved. Round-edge plating helps to create a smooth, safe surface that minimizes the risk of injury.
-
Better aesthetic appeal: Round-edge plating can be used to apply decorative finishes, such as chrome, gold, or nickel, to metal parts, enhancing their visual appeal and making them more attractive to consumers.
The Round-Edge Plating Process
The round-edge plating process typically involves several steps, which may vary depending on the specific application and the type of metal being plated. Here is a general overview of the process:
1. Surface Preparation
Before the plating process can begin, the metal surface must be thoroughly cleaned and prepared. This step involves removing any dirt, grease, or other contaminants that could interfere with the adhesion of the plating material. Common surface preparation methods include:
- Degreasing: Using solvents or alkaline cleaners to remove oils and grease
- Pickling: Immersing the metal in an acidic solution to remove oxides and scale
- Mechanical cleaning: Using abrasive methods, such as sanding or grinding, to remove surface imperfections
2. Edge Rounding
Once the surface is clean, the edges of the metal part are rounded to create a smooth, uniform surface. This can be done using various methods, such as:
- Vibratory finishing: Using a tumbling machine filled with abrasive media to gradually wear down the edges
- Belt sanding: Using an abrasive belt to manually sand the edges
- CNC Machining: Using computer-controlled machines to precisely shape the edges
3. Masking
In some cases, it may be necessary to mask off certain areas of the metal part to prevent them from being plated. This is typically done using a temporary adhesive or tape that can withstand the plating process.
4. Plating
The actual plating process involves immersing the metal part in a bath containing the desired plating material, such as nickel, chrome, gold, or copper. An electric current is then applied, causing the plating material to adhere to the surface of the metal. The thickness of the plating can be controlled by adjusting the current and the duration of the process.
5. Post-Treatment
After the plating is complete, the metal part may undergo additional treatments to enhance the performance or appearance of the coating. These may include:
- Heat treatment: Heating the plated part to improve the hardness and durability of the coating
- Passivation: Applying a protective film to the surface to enhance corrosion resistance
- Polishing: Buffing or polishing the surface to create a high-gloss finish
Common Round-Edge Plating Materials
There are several materials commonly used in round-edge plating, each with its own unique properties and advantages. Some of the most popular plating materials include:
1. Nickel
Nickel plating is widely used for its excellent corrosion resistance, hardness, and wear resistance. It is often used as an undercoat for other plating materials, such as chrome or gold.
2. Chrome
Chrome plating is known for its bright, shiny appearance and excellent wear resistance. It is commonly used in automotive and decorative applications.
3. Gold
Gold plating is often used in electronic and high-end decorative applications for its excellent conductivity and corrosion resistance. It is also used for its attractive, lustrous appearance.
4. Copper
Copper plating is commonly used as an undercoat for other plating materials, such as nickel or chrome. It is also used in electronic applications for its excellent conductivity.
5. Zinc
Zinc plating is known for its excellent corrosion resistance and is often used in outdoor applications or as a sacrificial coating to protect steel parts.
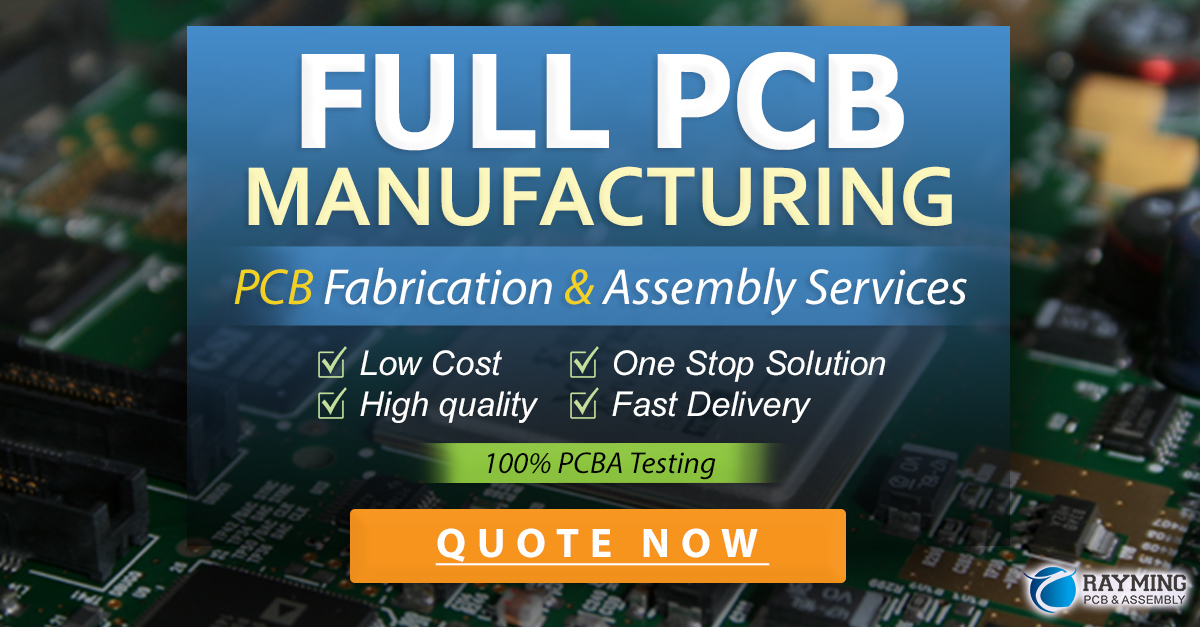
Applications of Round-Edge Plating
Round-edge plating is used in a wide range of industries and applications, including:
1. Automotive
In the automotive industry, round-edge plating is used to enhance the durability and appearance of various components, such as:
- Wheels
- Trim pieces
- Bumpers
- Grilles
2. Aerospace
Round-edge plating is used in the aerospace industry to improve the corrosion resistance and wear resistance of critical components, such as:
- Fasteners
- Hydraulic fittings
- Landing gear components
- Engine parts
3. Electronics
In the electronics industry, round-edge plating is used to enhance the conductivity and corrosion resistance of various components, such as:
- Connectors
- Printed circuit boards
- Switches
- Terminals
4. Manufacturing
Round-edge plating is used in various manufacturing applications to improve the durability and performance of metal parts, such as:
- Cutting tools
- Molds and dies
- Bearings
- Gears
Advantages of Round-Edge Plating
Round-edge plating offers several advantages over other metal finishing processes, including:
-
Versatility: Round-edge plating can be applied to a wide range of metal parts and components, regardless of their size, shape, or complexity.
-
Cost-effectiveness: Round-edge plating is a relatively inexpensive way to enhance the performance and appearance of metal parts, especially compared to other processes, such as machining or casting.
-
Customization: Round-edge plating allows for a high degree of customization, with various plating materials, thicknesses, and finishes available to meet specific application requirements.
-
Environmentally friendly: Many modern round-edge plating processes use eco-friendly chemicals and techniques, making them a more sustainable choice compared to other metal finishing methods.
Challenges and Considerations
While round-edge plating offers many benefits, there are also some challenges and considerations to keep in mind:
-
Substrate compatibility: Not all metals are suitable for round-edge plating, and some may require special surface preparation or pretreatment to ensure proper adhesion of the plating material.
-
Plating thickness: Achieving a consistent and uniform plating thickness can be challenging, especially on parts with complex geometries or hard-to-reach areas.
-
Stress management: The plating process can introduce residual stresses into the metal part, which can lead to warping or cracking if not properly managed.
-
Environmental regulations: Round-edge plating processes often involve the use of chemicals and materials that are subject to environmental regulations, which can vary by region and industry.
FAQ
-
What is the difference between round-edge plating and other metal finishing processes?
Round-edge plating is specifically designed to apply a protective or decorative coating to the edges of metal parts, while other metal finishing processes, such as anodizing or powder coating, may focus on the entire surface of the part. -
How long does the round-edge plating process take?
The duration of the round-edge plating process can vary depending on the size and complexity of the metal part, as well as the specific plating material and desired thickness. In general, the process can take anywhere from a few minutes to several hours. -
Can round-edge plating be applied to any metal?
While round-edge plating can be applied to a wide range of metals, some materials may require special surface preparation or pretreatment to ensure proper adhesion of the plating material. It is important to consult with a qualified metal finishing provider to determine the best approach for your specific application. -
How durable is round-edge plating?
The durability of round-edge plating depends on several factors, including the specific plating material, the thickness of the coating, and the environmental conditions to which the part will be exposed. In general, round-edge plating can significantly enhance the durability and corrosion resistance of metal parts, extending their lifespan and reducing the need for frequent replacements. -
Is round-edge plating environmentally friendly?
Many modern round-edge plating processes use eco-friendly chemicals and techniques, making them a more sustainable choice compared to other metal finishing methods. However, it is important to work with a reputable metal finishing provider that adheres to all relevant environmental regulations and best practices to ensure the most environmentally responsible approach.
Conclusion
Round-edge plating is a versatile and cost-effective metal finishing process that offers numerous benefits for a wide range of industries and applications. By applying a protective or decorative coating to the edges of metal parts, round-edge plating can enhance durability, corrosion resistance, safety, and aesthetic appeal.
While there are some challenges and considerations to keep in mind, such as substrate compatibility and environmental regulations, the advantages of round-edge plating make it a valuable tool for improving the performance and longevity of metal products.
As technology continues to advance and new plating materials and techniques are developed, the potential applications for round-edge plating will only continue to grow, making it an increasingly important process in the world of metal finishing.
Industry | Applications |
---|---|
Automotive | Wheels, trim pieces, bumpers, grilles |
Aerospace | Fasteners, hydraulic fittings, landing gear components, engine parts |
Electronics | Connectors, printed circuit boards, switches, terminals |
Manufacturing | Cutting tools, molds and dies, bearings, gears |
Leave a Reply