Factors Affecting Finished Hole Size
Several factors can influence the finished hole size, leading to deviations from the intended diameter. These factors include:
Drill Bit Size and Tolerance
The drill bit size is the primary factor that determines the finished hole size. However, drill bits are manufactured with certain tolerances, meaning that their actual diameter may vary slightly from the nominal size. These variations can affect the finished hole size, especially when working with tight tolerances or when drilling multiple holes that need to be consistent.
Material Properties
The properties of the material being drilled can also impact the finished hole size. Different materials respond differently to the drilling process, depending on their hardness, elasticity, and thermal properties. For example:
- Soft materials, such as wood or plastic, may experience more deformation during drilling, leading to slightly larger finished hole sizes.
- Hard materials, like metals or ceramics, may cause drill bit wear, resulting in smaller finished hole sizes over time.
- Materials with high elasticity, such as some plastics or rubbers, may recover partially after drilling, resulting in smaller finished hole sizes.
Drilling Techniques
The drilling technique employed can also affect the finished hole size. Factors such as feed rate, spindle speed, and drilling depth can influence the hole size and quality. For instance:
- High feed rates may cause the drill bit to deflect or wander, leading to larger or irregular finished hole sizes.
- Incorrect spindle speeds can cause excessive heat generation or vibration, affecting the hole size and surface finish.
- Drilling too deep without proper chip evacuation can cause chips to pack in the flutes, leading to larger finished hole sizes.
Measuring Finished Hole Size
To ensure that the finished hole size meets the required specifications, accurate measurement is crucial. There are several methods and tools available for measuring hole sizes, depending on the size range and the required precision.
Hole Gauges
Hole gauges are simple and quick tools for measuring hole sizes. They consist of a set of precisely machined pins or blades with incremental diameters. To measure a hole, the user selects the gauge that fits snugly into the hole without forcing it. The size of the gauge corresponds to the finished hole size. Hole gauges are suitable for quick inspections and for holes with larger tolerances.
Calipers
Calipers are versatile measuring tools that can be used to measure both internal and external dimensions, including hole sizes. There are two main types of calipers:
-
Vernier Calipers: These calipers have a main scale and a sliding vernier scale that allows for precise measurements. To measure a hole size, the inside jaws of the caliper are placed inside the hole, and the reading is taken from the scales.
-
Digital Calipers: These calipers have a digital display that shows the measurement directly. They work on the same principle as vernier calipers but offer easier readability and data transfer capabilities.
Calipers are suitable for measuring hole sizes with higher precision than hole gauges and can handle a wide range of sizes.
Bore Gauges
Bore gauges are specialized tools designed for accurate internal measurements, including hole sizes. They consist of a handle, a measuring head with a dial indicator or digital display, and interchangeable tips or anvils. To measure a hole size, the appropriate anvil is selected based on the hole diameter, and the gauge is inserted into the hole. The dial indicator or digital display shows the deviation from the nominal size, allowing for precise measurements.
Bore gauges are ideal for measuring hole sizes with tight tolerances and for applications that require high accuracy and repeatability.
Coordinate Measuring Machines (CMMs)
Coordinate Measuring Machines (CMMs) are advanced metrology tools that can measure hole sizes along with other dimensional characteristics of a part. CMMs use a probe to touch various points on the surface of the part and record their coordinates in 3D space. By measuring multiple points along the circumference of a hole, the CMM can calculate the average diameter and provide a detailed analysis of the hole size and form.
CMMs are suitable for measuring complex parts with multiple features and for applications that require extremely high precision and traceable measurements.
Controlling Finished Hole Size
To achieve the desired finished hole size consistently, it is essential to control the factors that influence the drilling process. Some strategies for controlling finished hole size include:
Drill Bit Selection
Choosing the right drill bit is crucial for achieving the desired finished hole size. Consider the following factors when selecting a drill bit:
- Material: Select a drill bit that is suitable for the material being drilled. Different materials require different drill bit geometries and coatings to optimize performance and hole quality.
- Size: Choose a drill bit size that is slightly smaller than the desired finished hole size to account for material deformation and drill bit wear.
- Tolerance: Use drill bits with tighter tolerances for applications that require high precision and consistency.
Drilling Parameters Optimization
Optimizing the drilling parameters can help control the finished hole size and improve hole quality. Consider the following factors:
- Feed Rate: Use the appropriate feed rate for the material being drilled and the drill bit size. Too high a feed rate can cause drill bit deflection and oversized holes, while too low a feed rate can cause heat buildup and undersized holes.
- Spindle Speed: Select the appropriate spindle speed based on the drill bit diameter and the material being drilled. The correct spindle speed helps to minimize vibration, heat generation, and drill bit wear.
- Pecking Cycle: Use a pecking cycle when drilling deep holes or materials prone to chip packing. Pecking involves periodically retracting the drill bit to clear chips and prevent heat buildup, which can affect the finished hole size.
Coolant and Lubrication
Proper coolant and lubrication are essential for controlling finished hole size and improving hole quality. Coolant helps to dissipate heat, reduce friction, and flush away chips, while lubrication reduces tool wear and improves surface finish. Consider the following:
- Coolant Type: Select the appropriate coolant for the material being drilled and the drilling operation. Water-soluble coolants are suitable for most materials, while oil-based coolants are better for certain metals and high-speed drilling.
- Coolant Delivery: Ensure that the coolant is delivered effectively to the cutting zone. Use through-tool coolant delivery when possible, as it provides better cooling and chip evacuation than external flooding.
- Minimum Quantity Lubrication (MQL): Consider using MQL for drilling operations that require minimal coolant usage. MQL delivers a fine mist of lubricant to the cutting zone, reducing heat generation and tool wear while minimizing environmental impact.
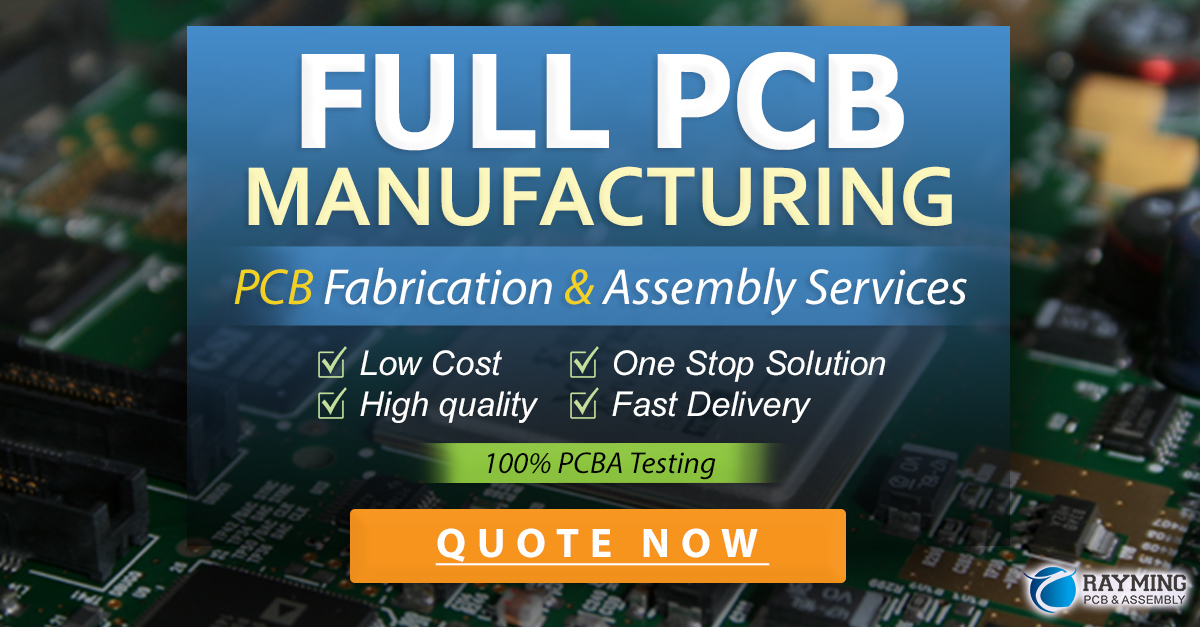
Finished Hole Size Tolerances
Finished hole size tolerances specify the allowable range of variation from the nominal hole size. These tolerances are essential for ensuring proper fit and function of the final product. The required tolerances depend on the application and the mating components and are typically specified in engineering drawings or standards.
Tolerance Classes
Tolerances for finished hole sizes are often specified using tolerance classes, which define the acceptable range of deviation from the nominal size. Some common tolerance classes include:
- H7: A commonly used tolerance class for finished holes that require a close fit with mating parts. The tolerance range for an H7 hole is +0.000 to +0.015 mm for hole sizes up to 10 mm.
- H8: A tolerance class that provides a looser fit than H7, suitable for applications that require some clearance between mating parts. The tolerance range for an H8 hole is +0.000 to +0.027 mm for hole sizes up to 10 mm.
- H9: A tolerance class that provides an even looser fit than H8, suitable for applications that require significant clearance between mating parts. The tolerance range for an H9 hole is +0.000 to +0.052 mm for hole sizes up to 10 mm.
The tolerance ranges for these classes vary depending on the nominal hole size, with larger hole sizes having wider tolerance ranges.
Fit Types
Finished hole size tolerances are also related to the desired fit between mating parts. The three main types of fits are:
-
Clearance Fit: A clearance fit allows for some space between the mating parts, enabling free movement or easy assembly. Clearance fits are typically specified using hole tolerance classes such as H7, H8, or H9, depending on the required amount of clearance.
-
Interference Fit: An interference fit involves a hole that is slightly smaller than the mating part, creating a tight and secure connection when the parts are assembled. Interference fits are typically specified using hole tolerance classes such as H6 or H5, depending on the required amount of interference.
-
Transition Fit: A transition fit falls between a clearance fit and an interference fit, where the mating parts have a similar size, and the actual fit can range from a slight clearance to a slight interference. Transition fits are typically specified using hole tolerance classes such as H7 or H8, depending on the desired fit characteristics.
Common Finished Hole Size Applications
Finished hole sizes are critical in various industries and applications, where the proper fit and function of mating parts are essential. Some common applications include:
Bearings and Shafts
Bearings and shafts require precise finished hole sizes to ensure proper fit, smooth rotation, and optimal load distribution. The hole size tolerances for bearings and shafts depend on the type of fit required, such as clearance fit for free rotation or interference fit for secure mounting.
Fasteners and Bolted Connections
Finished hole sizes are crucial for fasteners and bolted connections, as they affect the strength, stability, and ease of assembly of the joint. The hole size tolerances for fasteners depend on the type of fastener, the material being joined, and the desired fit, such as clearance fit for easy assembly or transition fit for a more secure connection.
Hydraulic and Pneumatic Components
Hydraulic and pneumatic components, such as valves, cylinders, and fittings, require precise finished hole sizes to ensure proper sealing, flow control, and pressure management. The hole size tolerances for these components are typically specified by industry standards, such as ISO or SAE, and depend on the operating pressure, fluid compatibility, and sealing method.
Aerospace and Automotive Parts
In the aerospace and automotive industries, finished hole sizes are critical for the proper assembly, performance, and safety of various components, such as engine parts, structural elements, and fluid systems. The hole size tolerances for these applications are often tightly controlled and specified by industry standards or manufacturer specifications, considering factors such as material properties, operating conditions, and safety requirements.
FAQ
- What is the difference between nominal hole size and finished hole size?
-
Nominal hole size refers to the theoretical or designed size of a hole, while finished hole size is the actual size of the hole after the drilling process is complete. The finished hole size may deviate slightly from the nominal size due to factors such as drill bit wear, material properties, and drilling techniques.
-
How do I choose the right drill bit size for a desired finished hole size?
-
When selecting a drill bit size, consider the desired finished hole size, the material being drilled, and the required tolerance. As a general rule, choose a drill bit size that is slightly smaller than the desired finished hole size to account for material deformation and drill bit wear. Consult drill bit size charts or engineering standards for specific recommendations.
-
What are the most common methods for measuring finished hole sizes?
-
The most common methods for measuring finished hole sizes include using hole gauges, calipers (vernier or digital), and bore gauges. Each method has its own advantages and limitations, depending on the size range, required precision, and accessibility of the hole. For high-precision applications, coordinate measuring machines (CMMs) may be used.
-
How can I improve the consistency of finished hole sizes in my drilling operations?
-
To improve the consistency of finished hole sizes, consider the following strategies:
- Select the appropriate drill bit for the material and desired hole size
- Optimize drilling parameters, such as feed rate and spindle speed
- Use proper coolant and lubrication to reduce heat generation and tool wear
- Implement quality control measures, such as regular drill bit inspections and hole size measurements
-
What are the consequences of finished hole sizes being out of tolerance?
- Finished hole sizes that are out of tolerance can lead to various problems, such as:
- Poor fit and alignment of mating parts
- Reduced strength and stability of bolted connections
- Leakage or failure of hydraulic and pneumatic systems
- Compromised performance and safety of critical components
- Increased production costs due to rework or scrap
By understanding the importance of finished hole sizes, selecting the appropriate tools and techniques, and implementing proper quality control measures, engineers, machinists, and DIY enthusiasts can ensure that their drilled holes meet the required specifications and contribute to the overall success of their projects.
Leave a Reply