Understanding PCB Plating Materials
PCB plating involves depositing a thin layer of metal onto the copper traces and pads of a circuit board. This process serves several purposes:
- Enhancing electrical conductivity
- Improving solderability for component assembly
- Protecting the copper from oxidation and corrosion
- Providing a better surface finish for aesthetic purposes
There are several common plating materials used in the PCB industry, each with its own advantages and disadvantages. Some of the most popular options include:
- Tin (Sn)
- Lead (Pb)
- Nickel (Ni)
- Gold (Au)
- Silver (Ag)
- Copper (Cu)
While each material has its merits, the choice ultimately depends on the specific requirements of the PCB, such as the intended application, environmental conditions, and budget constraints.
Tin (Sn) Plating
Tin plating is one of the most widely used and cost-effective options for PCB plating. It offers several advantages:
Advantages of Tin Plating
- Low cost compared to other plating materials
- Good solderability for component assembly
- Adequate protection against oxidation and corrosion
- Relatively easy to apply using electroplating or immersion plating techniques
However, tin plating also has some limitations:
Disadvantages of Tin Plating
- Susceptible to tin whiskers, which can cause short circuits
- Not suitable for high-temperature applications
- May develop a dull appearance over time
Despite these drawbacks, tin plating remains a popular choice for many PCB manufacturers due to its affordability and overall performance.
Lead (Pb) Plating
In the past, lead plating was commonly used in combination with tin to create a tin-lead (Sn-Pb) alloy for PCB plating. This alloy offered excellent solderability and was the standard choice for many years. However, due to environmental and health concerns, the use of lead in electronics has been largely phased out through initiatives like the Restriction of Hazardous Substances (RoHS) directive.
Advantages of Lead Plating
- Excellent solderability when used in tin-lead alloys
- Low cost compared to other plating materials
- Good resistance to tin whiskers when used in tin-lead alloys
Disadvantages of Lead Plating
- Environmental and health hazards associated with lead
- Restricted or banned in many countries due to RoHS regulations
- Limited compatibility with lead-free soldering processes
As a result of these concerns, lead plating has largely been replaced by lead-free alternatives in the PCB industry.
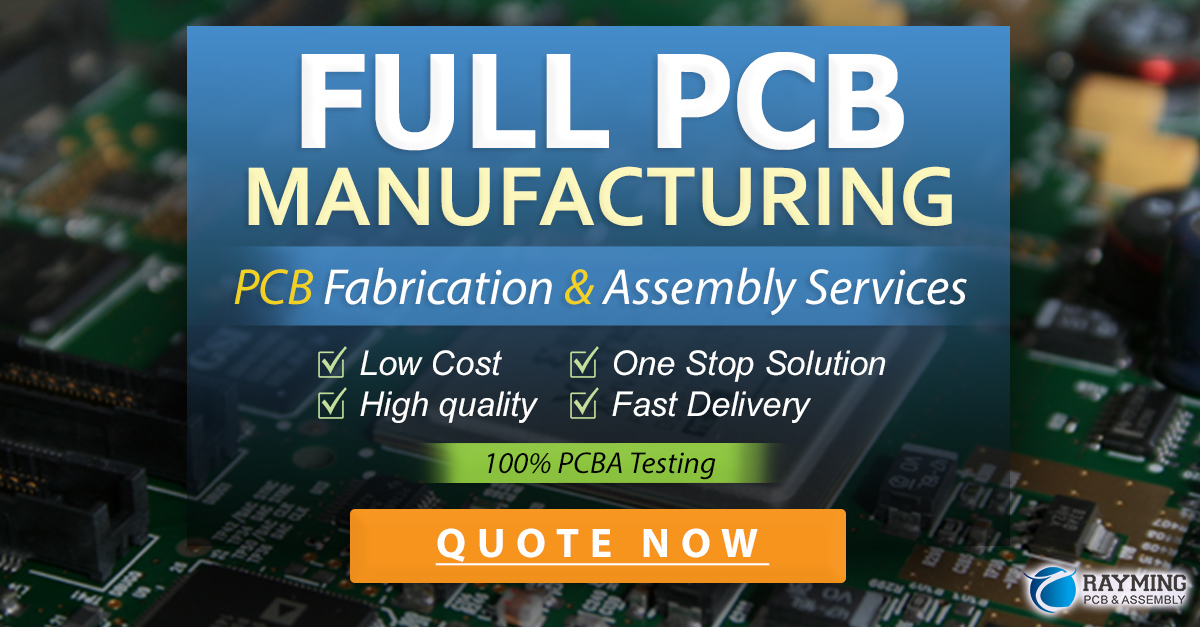
Nickel (Ni) Plating
Nickel plating is often used as an undercoat for other plating materials, such as gold or silver. It provides a barrier layer that improves adhesion and prevents the diffusion of copper into the top plating layer.
Advantages of Nickel Plating
- Excellent corrosion resistance
- Good hardness and wear resistance
- Provides a smooth and uniform surface for subsequent plating layers
- Relatively low cost compared to precious metal plating options
Disadvantages of Nickel Plating
- Not suitable as a standalone plating material due to poor solderability
- May cause allergic reactions in some individuals
- Requires careful process control to achieve consistent results
Nickel plating is rarely used as the final plating layer but plays a crucial role in multi-layer plating systems.
Gold (Au) Plating
Gold plating is often used in high-reliability applications where excellent corrosion resistance, electrical conductivity, and solderability are required. However, gold is also one of the most expensive plating materials.
Advantages of Gold Plating
- Excellent corrosion resistance
- Superior electrical conductivity
- Good solderability and wire bonding capabilities
- Stable surface finish that does not tarnish or oxidize over time
Disadvantages of Gold Plating
- High cost compared to other plating materials
- Susceptible to gold embrittlement when exposed to high temperatures
- May require additional processes, such as nickel undercoating, for better adhesion
Due to its high cost, gold plating is typically reserved for critical applications or used selectively on specific areas of a PCB.
Silver (Ag) Plating
Silver plating offers excellent electrical conductivity and is sometimes used as a more affordable alternative to gold plating. However, it is less common in PCB manufacturing due to some limitations.
Advantages of Silver Plating
- Excellent electrical conductivity, even better than gold
- Good solderability
- Lower cost compared to gold plating
Disadvantages of Silver Plating
- Prone to tarnishing and oxidation when exposed to air
- May develop silver migration, leading to short circuits
- Not as widely available as other plating options
Silver plating is occasionally used in specialized applications but is not as prevalent as other plating materials in the PCB industry.
Copper (Cu) Plating
Copper plating is an essential part of the PCB manufacturing process, as it is used to create the conductive traces and pads on the circuit board. However, copper is rarely used as the final plating layer due to its susceptibility to oxidation and corrosion.
Advantages of Copper Plating
- Excellent electrical conductivity
- Low cost compared to other plating materials
- Easy to apply using electroplating techniques
Disadvantages of Copper Plating
- Prone to oxidation and corrosion when exposed to air and moisture
- Poor solderability without additional surface finishes
- May develop a dull or tarnished appearance over time
Copper plating is an integral part of PCB fabrication but is typically covered with other plating materials to improve its performance and durability.
Cost Comparison of PCB Plating Materials
To determine the cheapest material for PCB plating, it is essential to compare the costs of the various options. The following table provides a relative cost comparison of the most common plating materials:
Plating Material | Relative Cost |
---|---|
Tin (Sn) | Low |
Lead (Pb) | Low |
Nickel (Ni) | Moderate |
Gold (Au) | High |
Silver (Ag) | Moderate-High |
Copper (Cu) | Low |
As evident from the table, tin and copper are among the most cost-effective plating materials, while gold is the most expensive option. However, it is important to note that the final choice of plating material should not be based solely on cost but also on the specific requirements of the PCB application.
Factors Influencing the Choice of PCB Plating Material
When selecting the appropriate plating material for a PCB, several factors must be considered:
- Intended application and environment
- Electrical and mechanical requirements
- Solderability and component assembly needs
- Compatibility with lead-free soldering processes
- Compliance with environmental regulations (e.g., RoHS)
- Budget constraints
By carefully evaluating these factors, PCB manufacturers can choose the most suitable plating material that balances performance, reliability, and cost-effectiveness.
FAQ
Q1: What is the cheapest material for PCB plating?
A1: Tin (Sn) and copper (Cu) are generally the cheapest materials for PCB plating. However, copper is rarely used as the final plating layer due to its susceptibility to oxidation and corrosion.
Q2: Is lead plating still used in PCB manufacturing?
A2: Due to environmental and health concerns, lead plating has been largely phased out in the PCB industry through initiatives like the Restriction of Hazardous Substances (RoHS) directive. Lead-free alternatives are now more commonly used.
Q3: Why is gold plating used despite its high cost?
A3: Gold plating is used in high-reliability applications where excellent corrosion resistance, electrical conductivity, and solderability are required. Its stable surface finish and resistance to tarnishing make it suitable for critical applications.
Q4: Can nickel be used as a standalone plating material?
A4: Nickel plating is rarely used as a standalone plating material due to its poor solderability. Instead, it is often used as an undercoat for other plating materials, such as gold or silver, to improve adhesion and prevent copper diffusion.
Q5: What factors should be considered when choosing a PCB plating material?
A5: When selecting a PCB plating material, consider factors such as the intended application and environment, electrical and mechanical requirements, solderability and component assembly needs, compatibility with lead-free soldering processes, compliance with environmental regulations, and budget constraints.
Conclusion
Choosing the cheapest material for PCB plating requires a careful consideration of various factors, including performance requirements, environmental regulations, and cost-effectiveness. While tin and copper are among the most affordable options, they may not always be the best choice for every application.
PCB manufacturers must strike a balance between cost and quality, ensuring that the selected plating material meets the specific needs of the intended use case. By understanding the advantages and limitations of each plating material and considering the relevant factors, manufacturers can make informed decisions that optimize the performance and reliability of their PCBs while keeping costs under control.
Ultimately, the cheapest material for PCB plating is one that satisfies the technical requirements of the application while providing the best value for money. As technology continues to advance and new plating materials emerge, PCB manufacturers must stay updated with the latest developments to remain competitive in an ever-evolving industry.
Leave a Reply